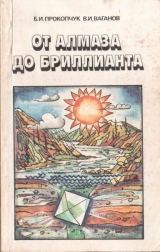
Текст книги "От алмаза до бриллианта"
Автор книги: Валерий Ваганов
Соавторы: Богдан Прокопчук
сообщить о нарушении
Текущая страница: 9 (всего у книги 10 страниц)
В апреле 1983 г. австралийская компания по продаже алмазов «Австрэлиан Рио-Тинто-Цинк» продала две партии камней с россыпных месторождений. Одна партия (200 тыс. карат) была поставлена ЦСО, другая (45 тыс. карат) – на свободный рынок.
С середины 1984 г. компания начала независимую от ЦСО продажу алмазов. Предполагается поставка австралийских алмазов в Индию.
В целом у Австралии есть все, чтобы в ближайшее время стать одной из ведущих алмазодобывающих стран капиталистического мира.
Суммарные запасы алмазов в мире (без СССР) на сегодняшний день могут быть оценены в 1,5–2 млрд. карат.
Алмаз-труженник
Человек еще на заре своей истории оценил исключительную твердость алмаза и стал применять этот камень в качестве инструмента, может быть, даже раньше, чем в качестве украшения. Так, английский египтолог В. Ф. Петри считает, что каменные блоки, из которых сложена пирамида Хеопса, соединялись между собой штырями, а отверстия для них просверливались с помощью алмаза, т. е. по гипотезе Петри, уже 5 тыс. лет тому назад древние египтяне использовали кристаллы алмаза как своеобразный буровой инструмент.
Алмазные инструменты были хорошо известны и в Древней Индии. Индийские мастера по огранке самоцветов прикрепляли кристаллы алмаза к рукояткам ножей и использовали их как инструмент для обработки нефрита и других камней. Такие же инструменты были распространены во многих странах и во все времена. Гай Плиний Старший в своем труде «Естественная история ископаемых тел» писал: «Вырезыватели на камнях стараются приобрести тонкие пластинки алмаза и оправлять их в железо. Посредством их легко продалбливается твердейшее вещество». Алмазом вырезаны арабские надписи на каменных плитах надгробия Тамерлана в мавзолее Гур-Эмир в Самарканде.
В X веке знаменитый ученый средневековья, уроженец Хорезма Абу аль-Бируни указывал в своей книге «О драгоценных минералах»: «Жители Ирака и Хорасана не различают сортов алмазов и их цвета, и все они для них одинаковы, так как они их применяют только для сверления… Алмаз обертывают в кусок свинца и осторожно бьют по нему, пока сила ударов не одолеет его и он, ослабев, перестанет сопротивляться им… Когда алмаз разбивают на мелкие куски или же растирают их, то следует приставить человека, который отгонял бы от него мух, потому что они могут унести крупинки алмаза, втягивая их в свой хоботок, и улетают с ними». Полученный таким способом алмазный порошок смешивался с маслом и наносился на край вращающегося медного диска (этот метод без принципиальных изменений дошел до наших дней).
Конечно, сейчас алмазный порошок используется далеко не на одну лишь обработку других драгоценных камней. Без применения алмазов в той или иной части технологической цепочки промышленного производства просто невозможно представить себе современную обрабатывающую и машиностроительную индустрию. Использование 1 карата алмазов в промышленности дает экономический эффект от 5 до 50 руб., а при обработке особо твердых и хрупких материалов – и до 200 руб. Поэтому неудивительно, что из всех добываемых в мире алмазов почти 80 % так и не попадают в «высший свет» в качестве бриллиантов, а становятся «рабочими», приобретая разнообразные прикладные специальности.
«Рабочими» становятся прежде всего более низкосортные алмазы – кристаллы с неровной окраской, с трещинами и другими дефектами, а также различные осколки, двойники, сростки, которые невозможно огранить в бриллиант, однако для некоторых операций применяются и ювелирные алмазы.
Судьба алмазов, которым предстоит стать «рабочими», неодинакова. Наиболее мелкие кристаллы со значительными дефектами пригодны лишь для измельчения в порошок – это так называемые абразивные алмазы. Другие алмазы применяются в инструментах без какой-либо обработки в своем натуральном виде. Наконец, некоторые кристаллы используются в промышленности после специальной обработки и приобретения соответствующей геометрической формы.
Рассмотрим вкратце, где и как трудятся алмазы всех перечисленных выше типов.
Итак, «рабочие» самой низкой квалификации – абразивные алмазы. Их используют, как это следует из самого названия, на изготовление абразивных материалов. Однако, несмотря на такую, казалось бы, «низкую» квалификацию, роль этих незаметных тружеников переоценить невозможно. Ведь шлифованию подвергаются сотни тысяч самых разнообразных изделий. Объем шлифовальных работ огромен, и поэтому на изготовление абразивов расходуется около 80 % всех технических алмазов.
Поиск наилучших абразивов ведется с незапамятных времен. Сначала в этом качестве использовался природный песчаник, затем появились искусственные абразивы. Индийские гранильщики драгоценных камней смешивали толченый корунд с шеллаком (природным лаком) и формовали из этой смеси круги, которые после обжига превращались в искусственные шлифовальные круги. В конце XIX века англичанин Баркли получил шлифовальный круг путем обжига смеси корундового порошка с огнеупорной глиной, а его соотечественник Батмен предложил использовать в качестве цемента, скрепляющего корундовые зерна (или зерна другого абразива), вулканизированную резину. В настоящее время для связывания зерен абразива применяются еще и керамика, металлы, полимерные материалы.
Широкое использование в современной промышленности твердых и сверхтвердых сплавов потребовало новых, более эффективных абразивных веществ. И здесь алмаз совершил подлинную революцию. Действительно, чтобы сошлифовать, например, 1 г сверхтвердого сплава, необходимо затратить около 50 г. такого абразива, как карбид кремния. Алмаза же на эту цель уйдет в сотни тысяч раз меньше. Высокая твердость и износостойкость алмаза наряду с повышенной теплопроводностью (способствующей быстрому отводу избыточного тепла, образующегося при шлифовании) обеспечивают эффективную обработку деталей из самых твердых материалов при высокой (практически недостижимой другими способами) чистоте обработки поверхности изделий.
Главный вид абразивного инструмента – шлифовальный круг. Он изготовляется из алмазного порошка, сцементированного в монолит каким-либо связующим веществом. Связующее вещество, как более мягкое, постепенно истирается, и тем самым постоянно обнажаются все новые и новые зерна алмаза. Шлифовальный круг как бы сам себя затачивает и работает до полного износа.
Изготовить хороший алмазный шлифовальный круг не такое уж простое дело. В зависимости от предназначения абразива подбирается оптимальный размер его зерен. Более крупнозернистые алмазные порошки используются для предварительной, грубой обработки изделий, когда удаляется большое количество материала, а доводка производится более мелкозернистым порошком. Наиболее распространены порошки со средними размерами зерен (6-10 мкм). Но самое главное, что определяет качество абразива и эффективность его работы, – это одинаковый размер частиц порошка в абразиве одного сорта. А добиться этого непросто: ведь на изготовление одного шлифовального круга идут тысячи маленьких алмазных кусочков.
Помимо шлифовальных кругов, алмазный порошок является основой разнообразных шлифовальных шкурок и лент.
При дроблении алмазов не только получаются порошки требуемой крупности, но и образуется много переизмельченного материала, состоящего из мельчайших крупинок алмаза размером 10 мкм и меньше. Из этих тончайших фракций и алмазной пыли изготовляются алмазные пасты и суспензии. Они используются главным образом на доводочных операциях при необходимости получения зеркально-гладкой поверхности.
Для резания твердых пород, сплавов и других материалов промышленностью выпускаются различные алмазные диски и пилы, где рабочим веществом служат алмазные порошки разной зернистости. Наконец, широкое распространение получили алмазные порошки для изготовления алмазных сверл – трубок, конусов, стержней, рабочая поверхность которых покрыта слоем алмазного абразива. Сверло для обработки часовых камней представляет собой тончайшую стальную иглу, смазанную смесью алмазного микропорошка и оливкового масла. Сверло совершает 15–20 тыс. оборотов в минуту и может просверлить отверстие диаметром 0,01 мм. А с помощью алмазного сверла диаметром 3,2 м (на изготовление которого пошло 125 карат алмазов) в железобетонной стене за два часа было высверлено отверстие указанного диаметра.
Итак, шлифование, резка, сверление … Если бы мы просто попробовали перечислить операции, где незаменимы алмазные порошки и пасты, то один этот перечень составил бы объемистую брошюру. Поэтому ограничимся лишь некоторыми примерами.
Естественно, что с помощью алмазных абразивов проводятся шлифование и зеркальная полировка всех видов изделий. Кроме того, алмазный абразивный инструмент широко используется в металлообрабатывающей промышленности для правки шлифовальных кругов, с применением которых получают точно и чисто обработанные поверхности. Как мы уже упоминали, шлифовальный круг – это множество острых твердых кристалликов абразива, тысячи микрорезцов, сцементированных воедино. В ходе работы эти микрорезцы притупляются и нуждаются в периодической перезаточке – правке. Правка осуществляется специальным алмазным инструментом – алмазометаллическим карандашом (прессованная вставка из алмазного порошка и порошка твердого сплава), алмазным роликом и иглой. Одним алмазометаллическим карандашом можно выправить несколько тысяч шлифовальных кругов.
С приходом в производство алмазных пил неузнаваемо изменились условия труда в карьерах по добыче строительного и облицовочного камня. На камнерезных фабриках с помощью дисковых алмазных пил распиливают самоцветы и поделочные камни. Алмазные пилы используются для резки бетона в строительстве, при прокладке бетонных автострад и взлетно-посадочных полос на аэродромах. Так, в Техасском аэропорту для лучшего сцепления самолетных колес с железобетонным покрытием алмазными пилами было нарезано 20 тыс. канавок длиной 4 км и глубиной 3 см каждая. На это ушло полторы тысячи дисковых алмазных пил.
Применение алмазного резания дает значительный экономический эффект. Например, стоимость распиловки 1 м2 такого труднообрабатываемого материала, как стеклопластик, составляет при использовании инструментов из быстрорежущей стали 40 руб., твердосплавного инструмента – 6 руб., а алмазной пилы – всего 1 руб.
Алмазные сверла широко используются в строительстве. При возведении современных зданий в железобетонных блоках приходится сверлить множество монтажных и коммуникационных отверстий. При использовании сверл из твердых сплавов на одно отверстие уходит около одного часа, а алмазные сверла ускоряют процесс в 4 раза. Кроме того, алмазные сверла позволяют получать отверстия диаметром до 1,5 мм.
Значительный эффект дало использование алмазного инструмента в железнодорожном деле в связи с заменой деревянных шпал железобетонными. У последних после формования концы необходимо обрезать. При резке корундовым кругом одного такого круга едва хватало на обработку пяти шпал, а алмазный отрезной круг обрезает 900 шпал, причем расход алмазов не превышает 1 карата.
Наконец, следует особо подчеркнуть, что алмазные порошки незаменимы при обработке сверхминиатюрных и твердых деталей. Наверное, все обращали внимание на надписи на циферблате наручных часов: 7, 11, 15, 18, 23 камня. В данном случае камни – это трудноистираемые и точно изготовленные опоры, на которых вращаются часовые оси. Они изготовляются из рубина, корунда, сапфира, а в особо точных хронометрах и из алмаза. Чем больше в часах таких камней, тем выше их качество. В некоторых приборах в особо ответственных узлах применяются подшипники из топаза, берилла и сапфира, твердость которых приближается к твердости корунда. Качественно обработать такие детали можно только с помощью алмазных порошков.
Понятно поэтому, какое исключительно важное значение имеют алмазы для развития часовой промышленности, точного приборостроения, электроники.
Теперь рассмотрим, где же используются монокристаллы алмаза на буровых работах. Ведь бурение горных пород – процесс сложный и трудоемкий, да и весьма дорогостоящий. Поэтому повышение эффективности бурения (а оно во многом зависит от производительности бурового инструмента) дает экономический выигрыш в сотни миллионов рублей. Особую важность это представляет для нашей страны, где объем бурения, особенно при поисках, разведке и эксплуатации нефтяных и газовых месторождений, исчисляется многими и многими миллионами метров.
Первым в Европе (да, пожалуй, и в мире) алмазы для бурения твердых горных пород предложил использовать швейцарский часовщик Г. Лешо в 1862 г. Его сын Рудольф Лешо вместе с механиком Пиге усовершенствовал способ отца, изобрел специальный буровой станок и разработал методы крепления алмазов в буровом инструменте. Этот буровой станок был с большим успехом применен при проходке одного из железнодорожных тоннелей в Швейцарских Альпах, а потом и при бурении шпуров на мраморном карьере Вермон в Швейцарии. В России энтузиастом и пионером алмазного бурения скважин явился профессор Горного института в Петербурге С. Г. Войслав, создавший в конце XIX века лучший по тем временам в мире буровой станок.
В наши дни на изготовление бурового алмазного инструмента расходуется около 12 % всех технических алмазов. Это прежде всего буровые коронки – стальные корпуса цилиндрической формы для навинчивания на бурильную трубу. На корпусе закреплена матрица – носитель алмазов.
Для буровых коронок используются алмазы массой 0,01—0,2 карата, непригодные для огранки в бриллианты. Коронки из мелких алмазов имеют большое число режущих граней, поэтому чем тверже горная порода, тем большим числом алмазов должна быть армирована коронка. Так, для бурения сравнительно мягких пород применяют буровые коронки, в которых на 1 карат приходится 5—15 зерен алмаза, для пород средней крепости – 24–40, для крепких – 40-200 и для очень крепких пород – до 400 алмазных зерен на карат. Для бурения нефтяных скважин используются так называемые алмазные долота, причем на каждое долото в зависимости от его типа расходуется от 8 до 26 карат алмазов.
Как мы уже отмечали, главное преимущество бурового алмазного инструмента – заметное повышение скорости бурения, особенно в твердых породах. Кроме того, значительно снижается изнашиваемость оборудования, а скважины приобретают строго цилиндрическую форму, т. е. имеют постоянный диаметр. Все это существенно (в 4 и более раз) снижает стоимость буровых работ.
Другая необъятная область применения монокристаллов алмаза – использование его как режущего инструмента. Режущие свойства инструментальных материалов определяются такими качествами, как твердость, величина модуля упругости, коэффициент трения и теплопроводность. Все эти свойства счастливо объединились в алмазе, который представляет собой непревзойденный резец.
Обычно замена твердосплавных резцов на алмазные производит ошеломляющий эффект на людей, плохо представляющих возможности алмаза. Как вспоминал один из пионеров внедрения алмазов в промышленность Австралии, ему пришлось сначала столкнуться с весьма скептическим отношением к алмазному инструменту, не в последнюю очередь из-за его сравнительно высокой стоимости. Привычное казалось более надежным. Приходилось изыскивать различные способы рекламы. И здесь неожиданную помощь оказала… популярная в Австралии игра в шары.
Дело в том, что шары для этой игры вытачивали из бакелита с помощью резцов с режущей кромкой из карбида вольфрама. А бакелит обладает такой большой абразивностью, что одного резца хватает лишь на грубую обточку шара, для окончательной же обработки требуется либо сменить резец, либо перезаточить его.
Владельцу компании по производству шаров было предложено испытать алмазный резец. Это был австралийский алмаз с одной режущей кромкой, закрепленный в державке. Хозяин фирмы отнесся к предложению с изрядной долей скепсиса, но как же он был потрясен, когда на его глазах алмазный резец до затупления обточил 900 бакелитовых шаров! Немедленно поступил заказ на алмазный инструмент, который вскоре был усовершенствован: на алмазе теперь имелись несколько режущих кромок, и при затуплении одной из них алмаз просто «переводился» в другую позицию. К хорошему привыкают быстро, и через короткий промежуток времени хозяин фирмы уже выражал недовольство, если резец обрабатывал меньше 3500 шаров.
Приведенные выше цифры – 1 шар и 900 шаров – не случайны. Как показала многолетняя практика, производительность алмазных резцов при обработке пластмасс в 900 раз выше производительности резцов, изготовленных из твердых сплавов.
Стойкость резцов принято измерять длиной пути, который они могут пройти по обрабатываемой детали до затупления. Для резца из быстрорежущей стали этот путь составляет 6–8 км, из твердых сплавов – 20–30 км, а алмазный резец может пройти до 3000 км! Кроме того, алмазный резец позволяет заметно повысить скорость резания, а также обеспечивает высокую точность и чистоту обработки деталей, их одинаковость (стандартизацию), – а это ведь и есть основной закон современного массового производства.
Фактически тем же алмазным резцом являются всем известные стеклорезы, на изготовление которых идут бездефектные кристаллы алмазов массой 0,02—0,2 карата. А алмазный резец, заточенный в виде тончайшей иглы, позволяет изготавливать высококачественные дифракционные решетки, используемые в приборах для спектрального анализа. Дифракционная решетка – это стеклянная пластинка, на которую нанесена сверхтончайшая штриховая сетка необычной густоты и плотности (до 3000 штрихов на 1 мм). Сделать такое можно только с помощью алмаза.
Еще одна область, где алмаз просто незаменим, – это производство проволоки, точнее, операция волочения. Для того чтобы получить проволоку нужного диаметра, ее протягивают через ряд волок, или фильер, – твердых пластинок с отверстиями определенной величины. В наборе фильер диаметр отверстий постепенно уменьшается, и проволока, последовательно протягиваясь через них, утоняется, вплоть до получения требуемого сечения. В качестве фильер использовались либо стальные закаленные дощечки, либо пластинки из сапфира. Но они быстро истирались, и проволока теряла свое главное качество, определяющее сортность, – одинаковое по всей длине сечение. Применение алмазов позволило совершить в волочильном деле настоящую революцию.
Интересно, что в России применение алмазных фильер связано с именем прославленного режиссера и актера К. С. Станиславского (Алексеева). Его отец С. В. Алексеев руководил торговым и промышленным товариществом «Владимир Алексеев», которому принадлежала золотоканительная фабрика (ныне московский завод «Электропровод»). На фабрике, где до перехода в театр и работал К. С. Алексеев, инженер по образованию, изготовлялась канитель – тонкая золотая и серебряная проволока. В 1892 г. Константин Сергеевич в Париже увидел станки для алмазного волочения. Алмазные волоки были изготовлены из ювелирных камней массой 0,5 карата, вставленных в массивные стальные оправы. Такой станок был куплен, и в 1894 г. в России был создан первый цех алмазного волочения микропровода.
В скором времени широкое распространение электрических лампочек накаливания резко повысило спрос на проволоку сверхмалых диаметров, а также ужесточило требования к ее качеству. Ведь одинаковость толщины проволочной спиральки на всем ее протяжении – одно из главных условий долгой службы лампочки. А в настоящее время потребность в микропроводе стала огромной в связи с развитием современного приборостроения и электроники. Удовлетворить этот спрос можно, лишь применяя алмазные фильеры. Одна алмазная волока заменяет около 345 волок из твердых сплавов при увеличении скорости волочения в 2–3 раза.
Однако сквозь волоку протягивают не только различные металлы. Алмазная фильера оказалась неоценимой и при изготовлении парашютов. Волокна шелковой ткани, из которой шьют парашют, протягиваются сквозь алмазную фильеру, в результате чего шелковинки становятся настолько гладкими, плотными и скользкими, что ткань не слипается, и парашют раскрывается без помех.
Для изготовления алмазных волок используются обычно ювелирные алмазы массой 0,1–3,5 карата.
Главный потребитель технических алмазов и алмазного инструмента в капиталистическом мире – США, где производством таких инструментов заняты фирмы «Нортон компани» и «Карборундум», выпускающие практически все их разновидности. Эти фирмы имеют предприятия не только в США, но и в Канаде, Великобритании, Франции, ЮАР, Австралии.
Потребление технических алмазов в США постоянно растет. Оно составило в 1955 г. 11 млн. карат; 1960 г. – 13,5, 1965 г. – 15, 1970 г. – 21, 1975 г. – 25–26 млн. карат. Распределение алмазов по различным областям их применения примерно таково: шлифование и заточка инструментов и деталей из твердых сплавов – 60–70 %, правка шлифовальных кругов – 10–12 %, алмазное бурение – 10 %, волочение проволоки – 10 %, резка и шлифование деталей и изделий из стекла, керамики, мрамора, сверление твердосплавных деталей, обработка часовых камней и ювелирных изделий – 10–12 %.
В Западной Европе наиболее крупными потребителями технических алмазов являются Великобритания, Бельгия, ФРГ, Франция, Италия, Швеция и Швейцария.