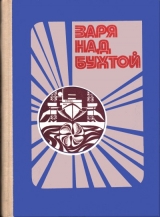
Текст книги "Заря над бухтой"
Автор книги: А. Чернавский
Жанр:
Публицистика
сообщить о нарушении
Текущая страница: 4 (всего у книги 11 страниц)
Внедрение хозяйственного расчета в цехах, организация оперативно-производственного планирования, широкое вовлечение рабочих в управление производством подготовили завод к переходу на работу в новых условиях хозяйствования, когда неизмеримо повысилась самостоятельность предприятия.
1 апреля 1968 года – красная дата в заводском календаре. Судоверфь перешла на пятидневку. Преимущество было очевидным, но в нем обозначились две сложности: во-первых, за пять дней надо было выпустить столько же продукции, сколько раньше за шесть. А потом, два выходных, как их разумно использовать? Вопросы были далеко не праздные. Они требовали тогда не только общего разъяснения, но и конкретной детализации. Ибо с их решением связывались многие важные моменты.
Работа по подготовке к новым условиям велась на заводе объемно, в самых различных направлениях. И если вначале вопросы экономической реформы были предметом заботы небольшого круга людей, в основном экономистов, то потом почти весь коллектив стал работать над практическим применением огромного комплекса мероприятий, связанных с новой системой. Этими мероприятиями были охвачены все стороны экономической и производственной жизни предприятия. Специалисты при активном участии рабочих сумели нащупать, а потом и разработать наиболее удобную для судоремонтников систему планирования, изучить пути внедрения рациональной структуры работ основных и вспомогательных цехов, улучшить организацию труда ведущих подразделений. Например, значительную выгоду принес коллективу новый подход к основным фондам. Еще в период подготовки на заводе освободились от ненужного оборудования. В то же время специалисты выявили в цехах малозагруженные станки и механизмы и разрабатывали меропрития по эффективному их использованию.
Одновременно с этим совершенствовалось планирование производства. Были созданы комплектовочные группы, подчиняющиеся непосредственно отделу подготовки производства. Начали внедрять технологические карты. Они составлялись на каждую деталь и значительно сокращали время и упрощали процесс их обработки. Совсем иным выглядело теперь и материальное стимулирование. Все нормативы по заводу и цехам были пересмотрены. В частности, расход электроэнергии на единицу продукции, расход сжатого воздуха, топлива, смазочных материалов, инструмента. Это создавало заинтересованность в экономии. Наряды стали выписываться комплексно, на весь цикл работ, чтобы ясно было человеку, что делать и сколько он за это получит. Самое серьезное внимание уделили фондам материального поощрения, ибо в новых условиях это был основной рычаг повышения производительности труда. В год реформы премий рабочим и служащим верфи выплатили около 600 тысяч рублей – в четыре раза больше, чем в год предшествующий. И надо сказать, первые месяцы работы по-новому дали обнадеживающие результаты. Из ремонта было выпущено на 13 судов больше, чем устанавливалось заданием. Увеличился объем продукции, завод перекрыл план по ее реализации.
Экономическую эффективность работы судоверфи на период внедрения хозрасчета и в новых условиях невозможно определить простым бухгалтерским учетом. Она выражается не только в миллионах рублей условной экономии, но прежде всего в общем прогрессе предприятия, которое благодаря широкому внедрению в производство передовых методов судоремонта, научных достижений выдвинулось в ряды ведущих в Дальневосточном бассейне.
– Курсом технического прогресса -
Последнее десятилетие (1965–1975) по своему трудовому накалу было, пожалуй, самым напряженным за всю сорокалетнюю историю завода. Старожилы в один голос утверждали, что за долгие годы работы на верфи им не приходилось наблюдать, чтобы судоремонтники с таким энтузиазмом, увлеченностью, с такой ответственностью претворяли в жизнь намеченные планы. Вспомним, чем был насыщен этот отрезок времени. 50-летие Великого Октября, 100-летие со дня рождения В. И. Ленина, XXIV съезд КПСС, 50-летие образования СССР. Священные исторические даты. Вся страна встречала их самоотверженным трудом. И камчатцы тут не были в числе последних. Под руководством областной партийной организации они развернули массовое социалистическое соревнование, в котором добились значительных результатов.
Например, ведущая отрасль хозяйства – рыбная промышленность – сделала такой скачок, о котором раньше могли только мечтать. За одно только пятилетие (1966–1970 гг.) предприятия и колхозы получили в свое распоряжение промысловые и обрабатывающие суда, в числе которых были рефрижераторные плавбазы и большие морозильные траулеры. Их эффективное использование, а также улучшение эксплуатации действовавшего флота позволило резко поднять добычу рыбы.
Такие темпы поставили перед судоремонтниками ряд сложнейших задач, которые потребовали от них не только наращивания производительности труда, применения новейших технических достижений, совершенствования форм организации производства. Весь коллектив старался работать четко, организованно, результативно. За последние годы на заводе заметно повысился уровень механизации труда, стало больше внедряться мероприятий по новой технике, рационализаторских предложений и заимствованных изобретений. Например, в 1974 году они дали два миллиона 200 тысяч рублей условного экономического эффекта. Не так давно на верфи освоены и внедрены в производство универсально-сборные приспособления, представляющие собой наиболее прогрессивный и совершенный вид технологической оснастки. Характерно, что использование самых первых сборок, подготовленных специально созданным участком, позволило на ряде сверловочных и расточных операций повысить производительность труда в 2,5–3 раза. Если сравнить первые планы технического перевооружения судоверфи с настоящими, то обращает на себя внимание прежде всего качественное отличие задач, а также долгосрочность прогноза. Горизонт экономического планирования конкретизируется в годовых производственных планах оргмероприятий по повышению производительности труда, культуры производства и социально-культурному развитию. Восьмая и девятая пятилетки в жизни завода были объединены комплексом долгосрочных проблем, В первую очередь, это осуществление широкой программы социального развития коллектива, углубление хозяйственно-экономической деятельности предприятия и совершенствование системы управления. Это, наконец, единая, стабилизированная производственная программа, основанная на передовых методах судоремонта.
Именно в этой связи и преемственности двух последних пятилеток вырисовывается грандиозная программа развития завода на ближайшие 10 лет.
Для более четкого обеспечения управления постоянно растущим производством и грамотного, научно обоснованного планирования на заводе ведется подготовительная работа по переводу предприятия на автоматизированную систему управления. Кроме того, перспективным планом предусматривается завершение реконструкции корпусного цеха, строительство инженерного корпуса, а также докового комплекса.
Иными словами, задачи перед коллективом стоят большие. На их успешное решение и направляются сейчас усилия судоремонтников, продолжающих свой творческий поиск. Касается он прежде всего углубления специализации и межзаводской кооперации, внедрения поточно-позиционного метода в судоремонте, повышения качества работ.
– Специализация -
В. ДАНИЛОВ, главный инженер
В повышении эффективности судоремонтного производства важную роль играют его специализация и кооперация, иначе говоря, привлечение к процессу ремонта судов элементов, характерных для серийного производства.
Известно, что один процент повышения производительности труда, достигнутый за счет специализации, вдвое «дешевле» процента, получаемого за счет других факторов. На верфи внедряются в основном два вида специализации: подетальная и технологическая. При современном состоянии организации производства они создают наиболее благоприятные условия для внедрения новейшей технологии, комплексной механизации и автоматизации производства.
В корпусном цехе, например, созданы специализированные участки по ремонту гребных винтов, автоматической наплавке валов и ремонту спасательных шлюпок, а в слесарно-монтажном – по ремонту главных и вспомогательных двигателей. Производительность труда здесь на 10–15 процентов выше, чем на неспециализированных участках.
Широко применяется на судоверфи агрегатный метод судоремонта. Это дает возможность специализировать многие трудоемкие операции и использовать специализированную оснастку и приспособления. При большом и малом капитальном ремонте все двигатели демонтируются на судах и доставляются в слесарно-монтажный цех, где производится их разборка, ремонт, сборка и испытание на оборудованных для этой цели участках. Каждый из них оснащен необходимым оборудованием и обслуживается специализированными бригадами.
Внедрение комплексной специализации позволило сократить сроки ремонта судов в среднем на 32 судо-суток. Годовой экономический эффект от организации и проведения ремонта серийных судов с применением агрегатного ремонта механизмов и узлов, например, в 1972 году составил 64823 рубля.
Специализация оказывает большое влияние и на качество ремонта. На многих участках почти вся продукция сдается ОТК с первого предъявления.
Существенному сокращению продолжительности ремонта судов способствует организация в основных цехах бюро комплектации деталей по узлам, механизмам и устройствам. В функции этих бюро входят своевременное обеспечение цеха литьем, поковками, контроль за наличием на складах материалов, необходимых для изготовления деталей.
Опыт работы специализированных участков показывает, что максимально возможная специализация станочников, бригад, мастеров, плановиков, технологов, инженеров, т, е. всех, кто непосредственно принимает участие в производственной деятельности предприятия, целесообразна и крайне необходима. И надо отметить, что внедрение на верфи комплекса мероприятий по специализации производства позволило резко поднять производительность труда, особенно на слесарно-монтажных работах, где этот рост составляет 18–25 процентов.
Мероприятия по специализации, а также по кооперации наряду с концентрацией производства предусматривают и совершенствование самой технологии. Например, трубомедницкий цех предусмотрено освободить от заливки подшипников, полностью передав ее слесарно-монтажному, что позволит на 30–40 процентов снизить брак и увеличить производительность труда.
– БМРТ на… «потоке» -
В. Екимов,
заместитель начальника отдела
Как быстрее? Лучше? Дешевле? Вот те три основных задачи, три проблемы, которые остро стоят сегодня на повестке дня любого судоремонтного предприятия. Поиск резервов идет здесь именно в этом направлении. Рыбацкое судно должно как можно меньше дней простоять у наших пирсов. Но ремонт его следует сделать так, чтобы его оценили высшими баллами. При этом затраты должны быть минимальными. За счет чего же этого можно достичь? Модернизировать суда? Расширить отраслевую и межотраслевую кооперацию? Углубить технологическую и предметную специализацию? Правильно. Все это, кстати, делается на заводе. И работа, проведенная в данном направлении, дает заметный экономический эффект. И все же этого теперь мало. Сегодня необходим такой метод ремонта судов, который в комплексе решал бы три вышеназванных задачи.
Этот метод уже найден и прочно утвердился в судостроении. Называется он так: поточно-позиционный. «Поток» давно уже манил и судоремонтников, однако перенести его на наши заводы было не так-то просто. Во всяком случае, первая попытка внедрить этот метод на Мурманской судоверфи оказалась неудачной. Но зато на Балтийском заводе он прижился. И результаты его внедрения здесь довольно ощутимы. В чем же его преимущества?
При поточно-позиционном методе суда ремонтируются последовательно на специализированных и оборудованных, в соответствии с их назначением, позициях. На каждой из них в строгой технологической последовательности выполняются определенные по номенклатуре ремонтные работы.
А весь цикл их разделяется на ряд этапов с равной продолжительностью. Точнее, на семь этапов, составляющие по времени 108 суток. «Поток» дает немало преимуществ по сравнению со всеми предыдущими методами. Например, на Балтийском заводе в результате его применения значительно сокращены сроки ремонта судов, что позволило в 1973 году увеличить вылов рыбы.
Нашим судоремонтникам этот метод тоже приглянулся. Два года мы уже ведем интенсивную подготовительную работу по его внедрению на заводе. Ею занята большая группа инженеров и техников, экономистов, специалистов различного профиля. Уже выработана организационно-технологическая документация: 140 типовых ремонтных ведомостей; внедрена часть технологических карт и графиков предремонтной дефектации; разработаны временные планово-учетные единицы, которые сейчас корректируются и шлифуются.
В 1974 году мы приступили к эксперименту. Провели опытную обработку планово-технологической документации поточно-позиционного метода на БМРТ «Пахача», «Пауджа» и «Казатин». Полученные результаты подтвердили эффективность «потока». «Пауджа» и «Казатин» вышли из ремонта в расчетные сроки, а БМРТ «Пахача» – на 50 суток раньше! Темпы подготовительных работ во много раз увеличились. Например, график ремонта судов мы составили с учетом постановки и ремонта 22 БМРТ, 3 из которых пройдут опытное внедрение, а 11 – уже промышленное. В феврале 1975 года на заводе был организован демонтажно-разгрузочный участок судов (ДРУ), который обеспечит выполнение комплекса работ по демонтажу и доставке механизмов в цех. Ведь раньше на все это уходило 25–40 суток. А сейчас с организацией данного участка сроки демонтажа значительно сократились. Например, на БМРТ «Зарубино» они составили 19, «И. Рябиков» – 16, «П. Овчинников» – 11 суток.
В последнем году пятилетки ремонт БМРТ в общей программе завода составит 70 процентов. Поэтому быстрейшее освоение поточно-позиционного метода позволит нам применить наиболее прогрессивную технологию. Конечно, трудностей тут целая уйма. Часто нам приходится продвигаться на ощупь, медленно, с осторожностью, рассчитывая, в основном, на собственные силы. Ведь если, скажем, на том же Балтийском заводе внедрение «потока» осуществлялось в течение трех лет с помощью научно-исследовательского института по судоремонту (ЦКТИС), то нашему коллективу все приходится делать самому, причем, в более сжатые сроки.
Поэтому поточно-позиционный метод внедряется на заводе не безболезненно. Ведь по сути дела нам приходится производить полную организационную перестройку предприятия, в процессе которой выявляется масса как текущих, так и перспективных проблем. К первым, например, можно отнести сложность в распределении людских ресурсов. «Поток» тут требует особого подхода. А в условиях крайне напряженной производственной программы найти его не так-то просто. Но более значительным препятствием является, как ни странно, сама организационная новизна, которая требует решительной психологической ломки в сознании работников. Часть из них никак не может «подладиться» под новый метод. Отдельные мастера и даже начальники цехов по-прежнему цепляются за старинку, что нередко создает различные «пробки», неувязки, задержки.
Словом, трудности немалые, но это не значит, что ставится под сомнение новый метод. Мы – за «поток». Нам с ним по пути.
– За честь заводской марки -
Н. Громницкий,
начальник ОТК
Бездефектное изготовление продукции – БИП. В этих трех буквах спрессовано то, чем аттестуется высшее качество работы. В заводской обиход вошли они с десяток лет назад, когда саратовский метод стал с осторожностью пробивать себе дорогу и в судоремонт. Дело это было не простым, ибо трудности обусловливались самой спецификой завода: большая разнотипность судов, отсутствие типовых технологических процессов, устаревшее оборудование, широкий круг профессий ремонтников и многое другое, что стояло на пути этого метода. К тому же на подступах к БИПу требовалось преодолеть и, так сказать, психологический барьер. Ведь в то время качество продукции на заводе не стало еще важным критерием повышения производительности труда. Гнали вал. По нему, собственно, и определяли лучших. За качество ответственность несли службы
ОТК, а исполнитель, как говорится, оставался «с боку припеку». Нередко само цеховое начальство выгораживало бракоделов, ибо работники ОТК находились тогда в штате цехов.
Когда, например, мы взяли под свой контроль закрытие рабочих нарядов, продвижение узлов и механизмов, когда службы ОТК были выведены из-под «опеки» цехов, некоторые авторитеты заявили: «Дров, товарищи, наломаете. БИП – дело хорошее, но не для судоремонта».
И поначалу казалось, что наши оппоненты правы. Хотя на заводе и удалось поднять технологическую дисциплину, утвердить авторитет ОТК, тем не менее в дальнейшем нас ждало горькое разочарование.
В 1966 году на саратовскую систему было переведено три вспомогательных подразделения. Однако итоги их работы ничего утешительного не принесли: по-прежнему давался брак, должный учет отсутствовал, требованиям системы не отвечало и материальное стимулирование. Словом, эксперимент не удался.
Но мы не опускали руки. Стали искать, выверять, совершенствовать. Силу и уверенность придало нам то, что дирекция и партком во всем помогали ОТК. И тем не менее потребовалось целое семилетие, чтобы от отдельных экспериментов заводу полностью перейти на саратовский метод. Произошло это в июне 1971 года. С тех пор БИП прочно закрепился во всех цехах.
В разработанном положении был предусмотрен целый комплекс моральных и материальных поощрений тем рабочим, которые старались производить только отличную продукцию. Это явилось неплохим производственным стимулятором.
Для наглядности обратимся к примеру корпусников, до внедрения БИПа имевших немало нареканий на качество. Они-то и стали предметом серьезных разговоров в коллективе. И не только разговоров, но и дела. О качестве заговорили и на планерках, и на собраниях, наладили регулярный выпуск «молний», стенгазет, по «шапке» стали бить бракоделов. И вот итог: много раз подряд корпусники удерживали первенство в соревновании по качеству. Здесь, пожалуй, каждый усвоил, что лучший контролер – это его рабочая совесть. Существенные сдвиги в смысле повышения качества произошли, конечно, и в других коллективах.
Теперь на заводе не единицы, а сотни рабочих, которые являются застрельщиками в движении за честь заводской марки. Но лучшие из лучших – это Е. А. Кабзистов, В. И. Телепень, П. А. Тятенко, А. Н. Кулешов, В. Н. Щекотин, А. Н. Никаноров, Б. И. Лушников, Т. К. Яловой, В. И. Рассохин, Г. А. Шаболин, В. Д. Завьялов и многие другие. 40 человек по доверенности ОТК работают с личным клеймом.
БИП, к слову сказать, существенно изменил и весь прежний метод деятельности ОТК. Каждое утро начинается у нас с разговора о дне вчерашнем. Как сработали цеха, где изъян допустили, где дефект, почему нарушили технические условия. Анализируем, обобщаем, рекомендуем, ну, а если надо, и свои санкции применяем. Активно и грамотно делают свое дело контролеры Н. И. Слободяник, Л. В. Якимчук, В. М. Пигарев, В. И. Маштаков, Г. Р. Клименко. С 1973 года мы приступили к очень трудоемкой и важной работе: начали вести статистический учет всех дефектов, выявленных в процессе ремонта и сдачи судов. На прицеле контролеров – каждый механизм, узел, каждая система. А цель ее вот какая. На основе результатов учета мы в будущем планируем перейти на статистический метод контроля – к активному управлению качеством продукции.
Целое десятилетие заводской коллектив ведет большую работу по внедрению БИП. Результаты определенно обнадеживающие: почти полностью исчезли рекламации на выпускаемую продукцию, в десяток раз сократились претензии заказчиков к качеству ремонта, резко снизились потери от брака.
БИП прижился на заводе. Рабочему человеку он по душе. Кузнец Корецкий, которому ОТК одному из первых доверило личное клеймо, рассуждает так:
– Волнуюсь и горжусь, когда на детали ставлю свою отметку. Личное клеймо – высшее признание рабочего мастерства, человеческого достоинства.
– Цеха завода -
…Здесь, у заводской стенки, всегда лес судовых мачт. Над ними – стальные шеи портальных кранов. Круглосуточный фейерверк сварочных искр и дробный стук пневматических молотков лишний раз напомнят: вы – в царстве большого судоремонта. В одну прямую вытянулись разноцветные заводские корпуса: трубопроводный, корпусный, механомонтажный… А там, за ними, – другие. Все они начинены станками, прессами, машинами, кранами. Давайте-ка заглянем сюда сами, совершим своеобразную экскурсию.
По душе мне, к примеру, трубопроводчики. Народ веселый, с юмором, за словом в карман не полезет. Захаживал к ним частенько. Как-то встретил у верстака невысокого, лет шестидесяти, мужчину. Он проворно жестикулировал руками, объяснял что-то стоявшему напротив парню. Как потом узнал, парень – это его, Мамонтова, сын. За отцом, выходит, к трубопроводному делу потянулся. Разговорились.
– Когда я таким, как мой Славка, был, туго тут нашему брату приходилось. Плита для гибки труб, два горна для нагрева, площадка для их набивки. И баста. Подай, принеси, все вручную. А теперь?
Бригадир молча повел глазами по цеху: дескать, смотри сам и сравнивай. На что сразу обращаешь внимание, так это порядок. Ни суеты, ни толкотни. Все здесь отлажено, как часовой механизм. У стенок – гибочные станки, специальные прессы, новые верстаки, механические ножовки. В считанные минуты опрессовщицы могут испытать любую трубу, предназначенную для монтажа судовых систем. Хотя эти новшества появились тут сравнительно недавно, они уже заметно повысили механизацию работ. А весь комплекс мероприятий, проведенных за последние шесть лет, дал ощутимый экономический выигрыш.
– Смена у нас достойная, – рассудительно говорил мне другой ветеран, сварщик Борис Васильевич Ткачев. – Убежден: уйду на пенсию, а мое место толковый парень займет. У нас, знаете, три четверти коллектива – это выпускники ГПТУ.
Часто называли такие фамилии: Коротков, Уланов, Шабалин, Аляев, Бобков. Все они – молодые бригадиры, тоже из профтехучилища. Многие из бригад уже в середине семьдесят четвертого личные пятилетние обязательства выполнили.
В корпусном моим гидом был Алексей Алексеевич Мороз. Он – один из немногих ветеранов, кто до сих пор трудится на родной верфи. Приехал в тридцать восьмом. Собственно, на его глазах шло становление цеха.
– Первый «жучок» как сейчас вижу: неказистый такой. Строили его долго и неумело. На площадке, которую отвели в цехе, – теснота. Металла в обрез. Опыта почти никакого. Сначала вверх килем строили: половину сделаем, выкатываем во двор, тут доделываем. В общем, в муках рождались наши первые «жучки». Работали много, иной раз по несколько смен подряд. Понимали: скорей надо, скорей. Завод хоть медленно, но набирал силу. Знали: чем быстрей станет на ноги, тем раньше и наша жизнь наладится.
Весной сорокового у нас своего рода выставка была организована. Это там, где сейчас диспетчерская. Выкатили мы из цеха четыре «жучка», поставили рядышком: дескать, смотрите, что за красавцы. Рабочие толпятся, руками по железной обшивке водят и переговариваются: «Ничего, и лучше будут». Не сомневались. Действительно, наши катера и по сей день бороздят камчатские воды. Трудятся.
Тому, кто, скажем, лет десять назад заходил в горячее отделение цеха, неизменно бросалась в глаза одна и та же картина: в одном углу чадила мазутная печь, в другом стояли времянки-будки; громадные двери – настежь; сквозняки, гарь, пыль. Слабо был оснащен участок и оборудованием. Поэтому корпусники-котельщики не расставались с кувалдой. А сейчас цех расширился, пополнился прекрасным оборудованием. В технологической последовательности выстроились фрикционный пресс, сверлильный станок, пресс-ножницы, станок абразивной резки дымогарных труб, правильные плиты, верстаки. Теперь здесь широко используются прогрессивная технология и научные методы труда. Канули в вечность дедовские лебедки, суета, скученность. Обязанности среди корпусников четко разграничены, нет дублирования, каждый знает, чем и когда заняться.
– Вот те же, к примеру, комплексные бригады, – пояснял Мороз. – Появились они у нас не так давно, а авторитет уже прочный завоевали. В таком коллективе обычно 8—10 человек. Каждый из них владеет, помимо основной, двумя-тремя смежными профессиями. Бригада ведет все работы в комплексе с начала ремонта до сдачи судна заказчику. Это резко уплотнило время и дало сильный импульс для роста производительности труда. Комплексных бригад сейчас 17. Есть тут и судосборщики, и резчики, и газосварщики. Что характерно, созданы они не за счет притока новых рабочих, а путем всевозможных реорганизаций внутри коллектива.
Корпусный цех – головной на верфи, стало быть, и более многочисленный. Было время, когда в нем около 500 человек трудилось. Сегодня – 320. Сокращение заметное. А вот объем выполняемых работ увеличился в несколько раз. По-моему, это и есть технический прогресс. В цехе 4 мостовых крана, 2 кран-балки мощностью 5 тонн, прессы, сверлильные станки. Правда, есть еще старенькое, изношенное оборудование. Но работает оно исправно. И все потому, что к нему прикасаются заботливые руки.
А вот и механомонтажный. Как и его собратья – корпусный и трубопроводный – родился он еще в тридцать шестом. Назывался тогда одним словом: механический. Потом стал механосборочным, нынче же – механомонтажный. Видите, сами названия этого цеха свидетельствуют о его росте и прогрессе. Поначалу – мелкие суда и шхуны, теперь – ремонт палубных и паровых механизмов всех типов судов современного флота. Преобразился механомонтажный, можно сказать, на глазах, за каких-то семь-восемь последних лет. Новенькие блестящие станки, испытательные стенды, различные приспособления плюс строгая специализация. Редко тут встретишь рабочего, у которого не было бы смежной профессии. Отсюда и результат: объем продукции в цехе вырос вдвое.
Здесь, в механомонтажном, припомнилось мне первое интервью с директором Потылицыным. Пришел я к нему из редакции с целью узнать о ходе выполнения социалистических обязательств. А беседу он начал тогда с… редуктора траловой лебедки БМРТ.
– Беда. Вот видите, какая кипа телеграмм? Все с промысла. Ломаются лебедки.
Факт этот пояснений особых не требовал. Я знал, что означали такие «молнии». В одной промысловой экспедиции сам наблюдал, как судно часами таскало за собой полный трал. Улов отменный, а лебедка поднять не может.
– И все это из-за вал-шестерни, – продолжал Анатолий Ефремович. – За этой деталью наши камчатские «толкачи» на материк летают.
Суда типа БМРТ выпускает Николаевский судостроительный завод. Однако запасных вал-шестерней он не производит. Не занимаются этим и другие предприятия страны. Вот и приходится рыбакам искать обходные пути.
– Каков же выход? – спрашиваю у директора.
– Выход срочный нужен. Вчера был в обкоме. Сказали так: «Пора самим судоремонтникам браться за эту проблему». Вот и думаем сейчас, с чего начать.
Это было четыре года назад, осенью семьдесят второго. Тогдашний разговор вспомнился при встрече с начальником механомонтажного.
– Помимо всего прочего мы и новый технологический процесс освоили: вал-шестерни для траловых лебедок изготовлять стали.
Со слов начальника было ясно, что освоение шло медленно и со скрипом.
– Начали по-кустарному. Даже куска спецстали, из которой изготавливаются фрезы, и то не оказалось. Пришлось слетать в Москву. И станка специального не было, свой переоборудовали. Вот тут-то и блеснули наши станочники. Мы, конечно, лучших к этой работе привлекли: токарей Терещенко и Галютина, зуборезчика Кузнецова. Настоящие асы! Представьте, при выточке и нарезке вал-шестерни нужен точнейший расчет, а необходимых инструментов тогда тоже не оказалось. Все на глазок да на чутье. Ну, ничего, приноровились ребята…
Позже, когда из района промысла придут долгожданные радиограммы, директор сообщит в своем рапорте: «Петропавловская судоверфь – первое и пока единственное предприятие Министерства рыбного хозяйства СССР – при отсутствии специального оборудования и оснастки успешно освоила опытное изготовление вал-шестерни редукторов траловых лебедок с зацеплением Новикова. Испытания на лову показали их высокие эксплуатационные качества».
Первая вал-шестерня, изготовленная здесь, в механомонтажном, была установлена на БМРТ «Камчатская правда». Капитан тогда радировал: «Спасибо, судоремонтники. Деталь – что надо». Потом их установили еще на десятках судов. Событие это, конечно, занимает достойное место в летописи цеха.
Впрочем, не только механомонтажного, но и инструментального. Потому, что именно здесь тогда были изготовлены первые червячные фрезы для зацепления Новикова. Это – исключительно сложный и тонкий многорезцовый инструмент, без которого станочникам просто было не обойтись. Кстати, в заводской летописи бюро инструментального хозяйства занимает особое место. Известно, к примеру, что его зачатки относятся к 1945 году. Одним из первых проектантов технологической оснастки был практик-конструктор Н. Г. Хромов. Сначала ютились в тесной комнатенке, оборудования было мало, да и то в основном допотопных образцов, примитивное. А заказы как-никак поступали самые современные. Скажем, помимо обычных инструментов, предназначенных для отечественных судов, приходилось изготавливать специальные метчики и фрезы для кораблей иностранной постройки. Их ремонтировали в свое время и в Японии, и в Китае. Поскольку иностранные стандарты не соответствовали нашим ГОСТам, сначала надо было сделать специнструмент, а уже потом изготовляли детали для ремонта. Со временем здесь выросла целая плеяда мастеров, работа которых аттестована по самой высшей шкале. Это В. И. Клеменко, награжденный орденом Октябрьской Революции, Г. А. Ершов, В. К. Суетин, П. М. Маркин, К. Г. Пересветов. Их лепта в развитии заводского инструментального хозяйства немалая.
Так закладывались основы крепкого и дружного коллектива, которому было присвоено звание коллектива коммунистического труда.
Сегодня в инструментальном будто в новенькой квартире. Чисто, светло, тепло. Всюду порядок. Оборудование размещено по отделениям: слесарному, заточному, термическому. Общий станочный участок разбит на группы: токарную, фрезерную, шлифовальную. Станки и стенды окрашены в соответствии с требованиями современной производственной эстетики. Люди сами приходят сюда и говорят: «Возьмите в свой цех».