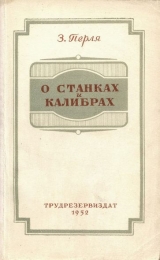
Текст книги "О станках и калибрах"
Автор книги: Зигмунд Перля
сообщить о нарушении
Текущая страница: 4 (всего у книги 14 страниц)
На токарном станке обрабатывались только наружные поверхности цилиндрических изделий. Со временем удалось приспособить его и для обработки небольших плоскостей, но техника требовала очень много разнообразных по форме деталей.
Тут были и большие плоскости, и зубья шестерен, и криволинейные «фасонные» поверхности. Такие задачи были уже не под силу токарному станку. Приходилось либо отказываться от изготовления изделия, либо ухитряться обрабатывать деталь с помощью дорогостоящих приспособлений. С ними мог управиться только очень квалифицированный мастер. Работал он вручную, и потому очень медленно. И получалось так, что обработка одного квадратного фута (около 1/ 10квадратного метра) плоской металлической поверхности обходилась в девять рублей золотом. Это была очень большая для того времени сумма. Попрежнему машины обходились дорого и выпускались в небольшом количестве. Вот почему станкостроители пришли к выводу, что для дальнейшего движения вперед необходимо создать новый станок.
Тогда уже существовал особый металлообрабатывающий инструмент – фреза. Этот инструмент выглядел не как стержень (резец), а как диск. На окружности этого диска располагалось несколько резцов одинаковой формы. Получалось нечто вроде звезды, лучами которой служили резцы.
Фрезу с успехом применяли часовщики, отличавшиеся тонким мастерством в области точной ручной металлообработки. Для фрезы они построили специальное приспособление, которое вращало этот инструмент с большой скоростью. Конечно, фрезы эти были очень, очень малы. С их помощью часовщики изготовляли крохотные зубчатые колесики и пластинки для часов. {40}
Станкостроители знали и об этом, когда решили построить новый станок: вместо неподвижного резца на скользящем супорте они установили фрезу на вращающемся шпинделе. Но в таком случае она все время обрабатывала бы один и тот же участок поверхности детали. Поэтому снабдили станок подвижным столом. Обрабатываемая деталь закреплялась на этом столе и вместе с ним постепенно, с определенной скоростью подавалась к вращающемуся инструменту. Стол станка превратился в супорт, но уже не для инструмента, а для изделия. Так снова вернулись к способу обработки, при котором деталь приближалась к инструменту, а не наоборот. Но делали это на основе новой, уже более совершенной техники, и потому результат получился отличный. Новый станок производительно и точно обрабатывал изделия всевозможной формы. Вскоре был изобретен и строгальный станок, но его появление ничуть не умалило роли фрезерного станка.
К середине прошлого столетия (за пятьдесят лет) стоимость обработки одного квадратного фута металлической поверхности снизилась в двести двадцать пять раз: вместо девяти рублей золотом – четыре копейки.
Тот же обмен ролями между инструментом и обрабатываемой деталью – инструмент вращается, изделие неподвижно – осуществлен и в сверлильном станке. Режущий инструмент этого станка – сверло – сконструирован в виде цилиндрического стержня, на рабочем конце которого имеются две режущие кромки, а на боковой поверхности вьются две винтообразные канавки. Сверло вращается, врезывается в металл изделия, снимает стружку, которая по боковым канавкам резца вытесняется наружу
В 1867 году в Париже, а четыре года спустя в Вене были организованы международные промышленные выставки. Знакомясь с экспонатами выставки, посетитель убеждался, что техника станкостроения очень улучшилась и стояла на очень высоком уровне.
Точность обработки, которая сто лет назад в Англии определялась толщиной мизинца Рейнольдса, дошла до одной десятой доли миллиметра.
Но и этого было мало. Требования к качеству и точности обработки поверхности деталей машин повышались с каждым днем. Все более тонкие, тончайшие стружки приходилось снимать с металла. Приходилось обрабатывать и доводить до окончательного размера рабочие {41} поверхности деталей, прошедших закалку и ставших очень твердыми.
Старые инструменты, резцы, изготовленные из закаленной стали, уже не справлялись с этой задачей. Их твердость оказалась недостаточной. И тогда машиностроители, опираясь на новую, далеко шагнувшую вперед технику, вернулись к первобытному инструменту – камню – и создали шлифовальный станок. Инструментом для этого станка служил шлифовальный круг, изготовленный из мелких зерен камня – корунда, твердость которого была немногим ниже твердости алмаза. Шлифовальный круг вращался со скоростью, значительно превышавшей скорости вращения фрез и сверл, и снимал тончайшую, пылевидную стружку с твердых, закаленных поверхностей. Точность изготовления начала подходить ксотым долям миллиметра.
Казалось, трудно было добиться большей точности, трудно было улучшить конструкцию станков. Но техника требовала еще большей производительности и точности. Потребность в лучших станках нарастала.
В конце прошлого столетия в машиностроительной промышленности бурно развивалось серийное и массовое производство. Приближался «век автомобиля». И тогда в станкостроении произошел второй переворот. Электрический двигатель заменил паровую машину. Электрический ток, точно свежая кровь, влился в «артерии» управления механизмами станков. Он сделал их более быстрыми, точными и, наконец, самодействующими.
Глава II. ВТОРОЙ ПЕРЕВОРОТ
Исчезнувший «лес»Если бы станочник конца прошлого столетия каким-то чудом оказался в цехах современного машиностроительного завода, многое показалось бы ему странным и непонятным. Но среди многих странностей одно явление показалось бы ему особенно необъяснимым, чудесным и невероятным.
Конечно, его поразили бы не новые, незнакомые очертания станков. Станки должны были измениться за шестьдесят лет. Но что, какая сила приводит их в движение? Где валы трансмиссий, где «лес» приводных ремней? Где прячутся могучие руки, влекущие взад и вперед под {42} потолком цеха огромный кран, точно мост, скользящий по рельсам?, И та же невидимая сила катит по крану тележку с крановщиком, который управляет движением этого моста, поднимает немыслимые тяжести и с непонятной легкостью переносит их с места на место. Где же она, эта сила?
На все эти вопросы пришельцу из прошлого столетия пришлось бы ответить подробно.
Мы уже знаем, что во второй половине XVIII столетия появился новый двигатель – паровая машина.
Она стала источником энергии, приводившим в движение все рабочие машины на всех заводах и фабриках. В цехах как будто и не было видно никаких двигателей. Под потолками вдоль цеховых помещений тянулись вращающиеся валы с насаженными на них приводными колесами-шкивами. С них сбегали к станкам ремни, много ремней. Каждый станок имел свои приводные колеса-шкивы. Насаженные на главный вал станка, они образовывали своего рода лестницу с круговыми ступенями. Лента бесконечного ремня надевалась на тот или другой шкив станка (в зависимости от величины скорости, которую хотели получить) и сообщала ему движение.
Станков было много, значит и ремней было много. Получался лес ремней, чуть ли не джунгли, затемнявшие помещение цеха, загромождавшие все пространство цеховых пролетов. Легко можно было быть задетым приводным ремнем и стать жертвой несчастного случая.
Для чего нужен был этот лес ремней? Оказывается, одна мощная паровая машина, скрытая где-то вне цеха, вращала с помощью приводного ремня всю систему валов, их называли трансмиссиями. А трансмиссии, в свою очередь, отдавали полученную энергию, посылая ее к станкам по ветвям таких же приводных ремней.
На длинном извилистом пути от единого источника – паровой машины – до рабочего шпинделя станка терялось много энергии. Очень много передаваемой энергии пропадало зря. Стоило произойти аварии где-нибудь на одном участке трансмиссии, – и вся линия станков выходила из строя. И наоборот, пуск в работу только одного станка требовал вращения всей трансмиссии со всеми ее шкивами. И тут терялось необычайно много драгоценной энергии. {43}
Все же, несмотря на эти недостатки, паровая машина целое столетие безраздельно господствовала в промышленности.
Первая половина XIX века ознаменовалась важнейшим событием: в 1834 году крупнейший русский ученый, академик Б. С. Якоби изобрел первый практически пригодный электрический двигатель. Несколько десятилетии длилось его усовершенствование. В восьмидесятых годах прошлого века рабочие шпиндели станков завертелись от электродвигателя, питаемого электротоком от центральной установки, вырабатывающей электроэнергию, а еще через два десятилетия паровая машина стала терять позицию за позицией, уступая свое место новому двигателю, победно и прочно завоевавшему господство в цехах заводов и фабрик.
Это был второй переворот в промышленности и в то же время начало второго переворота в развитии станкостроения. Но сократился ли от этого путь энергии к станку? Исчезли ли джунгли приводных ремней? Нет, не сократился извилистый путь энергии и ее потери, не исчез лес ремней!
Победа над паровой машиной досталась электродвигателю легко. Новый двигатель оказался не только экономичнее, но и компактнее (занимал меньше места) и требовал гораздо меньшей заботы о себе во время работы. Именно эти неоспоримые достоинства электродвигателя и заставили машиностроителей предпочесть его паровой машине. Но в остальном все осталось по-старому.
Новый двигатель занял место старого, а вся система передачи энергии к станкам не изменилась. Попрежнему от одного мощного мотора через общие трансмиссии приводились в движение линии станков, а в этих линиях выстраивались десятки и даже сотни станков. Попрежнему все промежуточные звенья цепи передачи урывали для себя часть силовой энергии, отпускаемой электродвигателем. Попрежнему лес ремней затемнял цех и грозил опасностью неосторожному рабочему. И бывало, что вся энергия мощного электродвигателя расходовалась на работу одного станка.
А можно ли было устранить недостатки общей передачи энергии? Конечно, можно было! Но машиностроители и конструкторы станков не сразу учли природу электрической энергии и компактность электродвигателя. {44} Первая из этих двух особенностей как бы говорила: «К чему вся эта громоздкая и прожорливая система трансмиссий, все эти шкивы и ремни, если электроэнергию можно передавать на расстояние по проводам?» Вторая особенность продолжала: «... а компактность электродвигателя и простота ухода за ним позволяют рассредоточить энергию единого мощного двигателя на несколько менее мощных и перенести их ближе, чтобы уменьшились потери в цепи передачи, чтобы проще и легче стало управление работой станков».
Вторая особенность была учтена раньше первой.
Единую трансмиссионную передачу разбили на несколько отдельных участков, обслуживающих небольшие группы станков. И каждая из этих групп приводилась в движение отдельным двигателем. Единый мощный электродвигатель «породил» несколько менее сильных двигателей, и эти двигатели «шагнули» в производственные помещения, поближе к станкам. С этого и началось «путешествие» электродвигателя к станку, которое длилось несколько десятилетий и о котором стоит рассказать.
От разделения единой трансмиссии на несколько отдельных участков лес ремней не стал реже. Но именно в этом разделении было заложено начало его исчезновения.
Все меньше и меньше становилось станков, связанных с одним двигателем. Все больше и больше приближался он к станкам. Наконец, пришло время, «когда только один станок обслуживался одним двигателем, его стали называть «индивидуальным» двигателем. Как же теперь передавалась к станку энергия движения? «Лес» ремней не исчез. Пожалуй, он даже не стал реже. Но теперь это уже был карликовый «лес».
Трансмиссия тоже стала «индивидуальной»: невысоко над станком устанавливался небольшой вал со шкивами – контрпривод. От вала двигателя к валу контрпривода взбегал бесконечный ремень привода и вращал шкив, а с другого шкива сбегал вниз другой бесконечный ремень и вращал соответствующий шкив станка. Опять энергия движения на своем пути к станку делала большой крюк, прежде чем приложить свою мощь к вращению шпинделя.
Зачем же нужно было делать этот крюк? Причина скрывалась в устройстве самих станков. {45}
Конструкторы не успели приспособить станки к новому виду двигателя. У них не было «ворот» для непосредственного подвода электрической энергии к рабочим органам станка. Скрытно (под полом) добравшись к станку и «вынырнув» наружу в непосредственной близости от него, электроэнергия все же сворачивала с прямого пути: чтобы попасть в станок, ей приходилось идти по давно проторенной дорожке – через приводной ремень, вал контрпривода и шкив станка.
Но вскоре станкостроители переконструировали станки. Теперь их строили так, чтобы двигатель и станок, поставленные на общей станине, составляли одно целое. На таком станке вал двигателя уже где-то внутри всей машины вращал систему шестерен и промежуточных валов и через них приводил в движение главный рабочий орган – шпиндель станка. Отпала нужда в индивидуальной трансмиссии, или контрприводе. Наконец-то мотор вплотную приблизился к станку, стал частью машины. Лес ремней исчез.
Второе «путешествие» двигателяВместе с лесом ремней ушли из цехов темнота, грязь, опасность увечий. Цехи машиностроительных заводов стали просторными, светлыми, чистыми, и неровный резкий гул ременной передачи сменился однообразным шумом работающих двигателей. Но и на этом путешествие двигателя не закончилось.
Путь энергии к рабочему органу – шпинделю станка – стал значительно короче. Однако и здесь значительная часть энергии расходовалась на преодоление трения между соприкасающимися звеньями передачи: многочисленными шестернями, валами, маховичками. Этих звеньев было очень много. Энергию приходилось расходовать не только на вращение рабочего шпинделя, но и на другие движущиеся части станка. Так, например, в большом радиально-сверлильном станке, кроме сверла, приходилось передвигать тяжелую поперечину (подвижную часть станка, несущую сверлильную головку), приводить в действие масляный насос, обслуживать промежуточные передачи.
За всеми этими операциями, требовавшими внимания, времени, усилий, следил рабочий. Передаточные механизмы {46} также поглощали часть энергии, отдаваемой двигателем.
Сделать путь энергии короче, уменьшить цепь передаточных звеньев и этим сократить потери энергии и улучшить работу станка – вот какие задачи встали перед станкостроителями. И тогда началось второе путешествие электродвигателя, но теперь уж не к станку, а по станку. Это значит, что двигатель стали пристраивать все ближе и ближе к рабочим органам станка.
Станкостроители сделали еще один шаг вперед: в конструкции сложных станков ввели не един, а несколько небольших электродвигателей. Один из них обслуживал рабочий шпиндель станка, а другие – отдельные его механизмы.
В том же радиально-сверлильном станке единый двигатель, дошедший было уже до самого шпинделя, «размножился» на четыре электродвигателя: один из них примостился непосредственно на рабочем шпинделе и вращал сверло, другой – у основания колонны станка приводил в движение насос для подачи жидкости, охлаждающей инструмент; третий – на верхушке колонны передвигал траверсу вверх и вниз, и, наконец, четвертый, под траверсой, закреплял ее в определенном положении и освобождал, когда нужно было ее передвинуть. В наши дни существуют {47} станки, у которых число двигателей доходит до десяти. Каждый из них приводит в движение определенную работающую часть станка.
Еще до Великой Отечественной войны в Ленинграде был спроектирован огромный станок для обработки поверхностей вращающейся сцены Дворца Советов. В этом станке число электродвигателей дошло до 32, а их общая мощность достигла 1500 киловатт. Такой мощности было бы достаточно для электроцентрали небольшого города.
С помощью электрических двигателей станкостроители стали осуществлять свои, даже самые смелые, казалось бы, невыполнимые замыслы.
Электрический помощникЭлектричество – подручный станочника, его помощник. Оно экономит время, освобождает руки рабочего, ускоряет темп работы, делает ее более точной.
Пуск станка в ход, его остановка, изменение скорости – все, что еще не так давно требовало ручного труда, времени и опыта, в наши дни заменено легким нажимом пусковых кнопок на щите управления станком. Электрический ток не только приводит в движение рабочие органы станка, он выполняет много других вспомогательных работ. Поэтому современный станок как бы оброс электроприборами.
Одни из них точным движением стрелок по шкале измеряют нагрузку станка, так как перегрузка грозит поломкой и выходом станка из строя.
Другие аккуратно «докладывают», с какой скоростью вращается обрабатываемая деталь, и «стерегут» любое отклонение от заданной скорости.
Существуют и такие электроизмерительные приборы, которые во время самой точной обработки, когда изменения размеров выражаются тысячными долями миллиметра, зорко и неустанно «следят» за этими изменениями. Как только инструмент – пусть это будет даже быстро вращающийся круг шлифовального станка – снимет последнюю, чуть ли не микроскопическую стружку, рабочий получит сигнал: стоп, отведи инструмент от детали!
На столе плоско-шлифовального станка выстроились одинаковые детали. Их поверхности нужно отшлифовать, {48} сделать предельно гладкими и точными. Для этого детали следует надежно закрепить, чтоб они не сдвинулись ни на одну тысячную миллиметра. Операцию эту можно выполнить вручную, поручив ее рабочему высокой квалификации. Но человеческие руки, даже самые искусные, все же могут ошибиться, допустить неточность. И тут опять приходит на помощь электричество. Новейшие шлифовальные станки оборудованы для крепления деталей особыми плитами, собранными из электромагнитов. Рабочий включает ток и замыкает магнитное поле через обрабатываемые детали. Один миг – и детали «прилипают» к столу станка и находятся в таком положении, пока рука рабочего не разомкнет ток.
И еще много других электроприборов «помогают» станку, измеряют и контролируют его работу, считают и записывают ее, сигнализируют о неисправностях и, наконец, всячески автоматизируют рабочие движения исполнительных органов машины.
Электрический привод и электрическое обслуживание всех вспомогательных операций – это тот фундамент, на котором современные станкостроители создали и создают новейшие станки. Какие же это станки?
«Мир» станковДо сих пор мы насчитывали всего лишь пять основных разновидностей станков: токарный, строгальный, фрезерный, сверлильный и шлифовальный.
В давние, начальные, времена своего существования каждый из основных станков, к примеру токарный или фрезерный, был чем-то вроде «мастера на все руки». На токарном станке научились обрабатывать цилиндрические детали не только снаружи, но и внутри. На этом же станке нарезали резьбу и обрабатывали небольшие плоские торцы деталей. Кое-какие из этих операций не всегда удавалось достаточно хорошо и быстро выполнить. Обыкновенный токарный станок был для этого мало приспособлен. Такими же недостатками страдали и другие основные виды станков. Тогда появились станки-специалисты, выполнявшие определенную операцию. От каждого основного вида станка, точно ветви от ствола дерева, выросли и развились новые, родственные виды станков.
От токарного отпочковался станок для растачивания длинных цилиндрических и полых изделий – орудийных {49}

Современный советский токарно-винторезный станок: 1 – коробка скоростей, передняя бабка; 2 – коробка подач; 3 – каретка сулорта; 4 – супорт; 5 – резцедержатель; 6 – задняя бабка; 7 – сменный центр задней бабки, вставленный в пиноль; 8 – рукоятки перемещения пиноли; 9 – трубопровод для подачи охлаждающей жидкости; 10 – ходовой винт для нарезания резьб; 11 – ходовой валик для самохода; 12 – валик пуска; 13 – рукоятки установки числа оборотов шпинделя; 14 – рукоятка изменения шага нарезаемой резьбы; 15 – рукоятка изменения направления витков нарезаемой резьбы (правой и левой); 16 – рукоятки настройки подачи резца (по таблице на коробке подач); 17 – рукоятка включения ходового винта или валика; 18 – кнопочная станция – включение и выключение электродвигателя; 19 – рукоятка ручного хода супорта; 20 – рукоятка механической подачи; 21 – включение и выключение гайки ходового винта; 22 – поперечная подача супорта; 23 – продольная подача супорта
{50}
стволов и гребных валов. Затем появился станок-специалист по точной расточке внутренних поверхностей коротких блок цилиндров двигателя. Этот станок называется горизонтально-расточным. В конструкцию этого станка введен стол, на котором крепится изделие. Почти одновременно родился и лобовой токарный станок для обработки больших плоскостей. Если же изделия с этими плоскостями слишком велики, тяжелы и громоздки, то на помощь приходит карусельный токарный станок, действительно, напоминающий карусель. Круглый стол станка расположен горизонтально и вращается так же, как и патрон или планшайба токарного станка. Изделие крепится на столе, а резцы подводятся супортом сверху или {51} сбоку. Также много ответвлений и у других основных станков.

Современный советский универсально-фрезерный станок: 1 – механизм подачи стола; 2 – коробка скоростей; 3 – кожух „хобота” станка; 4 – шпиндель; 5 – стол; 6 и 7 – механизм поперечной подачи стола; 8 – винт подъема стола; 9 – фундаментная плита; 10 – рычаг остановки стола; 11 – механизм продольного перемещения стола
Существуют и строгальные, и сверлильные, и фрезерные, и долбежные, и шлифовальные, и протяжные станки – «специалисты» по определенной операции. Но машиностроители сумели создать и создают в наши дни новые виды станков – узких «специалистов» по изготовлению какой-либо одной детали целиком. Такие станки, наоборот, выполняют много различных, но строго определенных операций.
Количество видов и типов станков непрерывно увеличивается. Есть среди них и «великаны» и «карлики». Откройте, например, крышку ручных часов. Вы найдете среди их деталей и крошечные зубчатые колесики, и фигурные плоскости, и мельчайшие винтики. Резьба на этих винтиках настолько мала, что почти не воспринимается невооруженным глазом, а лишь нащупывается пальцем. Только микроскоп и пинцет помогают часовщику обработать столь крохотные детали и собрать механизм воедино. Весь этот механизм времени можно легко спрятать в ладони. Мельчайшие детали часов изготовляются также на станках-специалистах. Это станки-карлики, очень точные настольные станочки.
А вот статор мощного турбогенератора. Человек, стоящий рядом с ним, кажется лилипутом. Статор тоже изготовлен на станке, но на карусельном станке-великане. По огромному круглому столу этого гиганта, как по автодрому, свободно могут катиться друг за другом две-три, а то и больше грузовых автомашин.
Существуют станки для обработки огромных орудийных стволов корабельной и береговой артиллерии. О величине такого станка могут дать представление детали, которые он обрабатывает: длина заготовок – 30, 35, 40 и больше метров, диаметр – 3 метра. Вес заготовки – сотни тонн!
Обработка броневых плит кораблей требует таких же строгальных станков-великанов. На столе такого станка можно играть в теннис. Вес станка доходит до 300 тонн. Чтобы изготовить один такой станок, нужно около 20 вагонов металла: его траверса, несущая супорты, выглядит точно мост-виадук через железнодорожные пути. {52}
Для этой же цели – обработки броневых плит – служит фрезерный станок весом тоже в 300 тонн. Представление о размерах станка может дать его фреза: ее диаметр – 2,5 метра.

Современный советский поперечно-строгальный станок: 1 – микрометрическое кольцо для точной установки резца; 2 – супорт; 3 – резцедержатель; 4 – стол; 5 – механизмы подачи; 6 – электродвигатель; 7 – коробка скоростей; 8 – ползун
Электрический ток как бы оживил станки, заставил их механизмы работать быстрее, точнее. И, наконец, с помощью электричества удалось полностью автоматизировать работу станков, добиться, чтобы станки работали сами, без вмешательства человека, и чтобы детали машин изготовлялись с еще небывалой скоростью при еще большей точности.