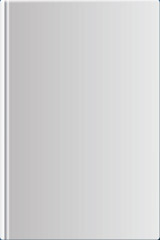
Текст книги "Метод определения энергоэффективности технологий и механизации горных работ по добыче полезных ископаемых открытым способом"
Автор книги: Юрий Анистратов
Жанр:
Технические науки
сообщить о нарушении
Текущая страница: 7 (всего у книги 8 страниц)
Комбайн ВАФ-170 немецкой фирмы с двумя поперечно расположенными на поворотной стреле головками, нагребающими лапами на погрузочный скребковый конвейер разрабатывает горные породы с пределом прочности до 1001200 МПа при высоте забоя 5,5 м, ширине захвата 6,3 м и производительности 300 т/ч (рис. 36).
Рис.36 Стреловой фрезерный комбайн с двумя головками:
1 – стрела, 2 – погрузочный механизм, 3 – конвейер, 4 – фрезерные головки.
При разработке крепких горных пород с буровзрывной подготовкой операция зачерпывания энергоемкая, усилие рабочего органа должно преодолеть сопротивление сцепления кусков горной массы и их вес. Выше в работе было рассмотрено, что это сопротивление уменьшается с увеличением степени дробления горной массы и коэффициента разрыхления.
В этих условиях эффективным становится применение погрузочных машин непрерывного действия с роторным рабочим органом.
Отличительной чертой этой погрузочной машины от существующих роторных экскаваторов является отсутствие рукояти. Роторное колесо диаметром равным высоте развала укреплено непосредственно на поворотной платформе экскаватора.
Этим создается возможность создания усилий черпания для погрузки хорошо раздробленной горной массы. Как показано в работе хорошее дробление может быть достигнуто при взрывной подготовке горных пород к выемке скважинами малого диаметра на уступах высотой 5—8 м или механическим рыхлением, со штабелированием разрушенной горной массы бульдозером-рыхлителем. В этом случае высота развала будет 4—8 м, следовательно, диаметр ротора погрузочной машины тоже будет в пределах 8 м.
Ширина ковша роторного колеса (В) согласно исследованию взаимосвязи свойств горной массы и параметров погрузочного органа должна быть В>3dср. т.е. 1200—1500 мм.
Принцип действия роторной погрузочной машины, как известно, полностью соответствует специфике открытых горных работ, обеспечивает минимальное энергопоглощение в выемочно-погрузочном процессе.
Данная погрузочная машина может работать как с автомобильным транспортом в комплектах оборудования дискретного действия, так и с конвейерным с перегружателем в комплектах непрерывного действия.
8.6 Перемещение
Энергоемкость процесса перемещения в технологии горных работ на карьере занимает 50—60%. Это показывает его значение. В основу рассматриваемого в настоящей работе принципа формирования комплектов оборудования технологических потоков положено использование преимуществ транспорта в конкретных условиях их отдельных частей и звеньев. В данном разделе рассмотрены основные тенденции в развитии существующих видов транспорта и перспективности новых, применительно к забойной части технологического потока частей комплекта по доставке горной массы из карьера и на поверхности.
Тенденции в развитии существующих видов транспорта заключаются в увеличении количества горной массы, перемещаемой транспортной единицей, т.е. увеличение вместимости транспортных сосудов, грузоподъемности составов, ширины и скорости движения ленты, диаметра трубопровода, диаметра рудоспусков для гравитационного транспорта и т.д. С энергетической позиции концентрация мощности, увеличение производительности ведут к уменьшению затрат на перемещение единицы горной массы,
Однако увеличение вместимости сосудов колесных транспортных средств увеличивают его стоимость. При сохранении степени его использования в единицу времени увеличиваются затраты на единицу продукции в комплекте оборудования технологического потока, особенно при большой длине пути перемещения, поэтому тенденция увеличения грузоподъемности колесных видов транспорта дает существенный экономический эффект только при одновременном повышении степени его использования.
Специфика работы забойной части транспорта потока заключается в том, что движение транспорта этого звена осуществляется по горизонтали от забоя до пункта приема груза в сложных комплектах оборудования потоков и по горизонтальным и наклонным путям траншей в простых комплектах оборудования технологических потоков. Экономичность ведения горных работ на карьере требует уменьшения ширины рабочей площадки и транспортной полосы на горизонте. Этой специфике и требованиям отвечает специальный вид карьерного транспорта – дизель-электрический карьерный автопоезд большой грузоподъемности с двусторонним движением для исключения разворотов в забое и у пунктов приема груза с разгрузкой на бок (Рис.37).
Рис.37 Специальный карьерный автопоезд особо большой грузоподъёмности и с двухсторонним движением.
Использование предложенного вида транспорта позволяет сократить рабочую площадку за счет исключения разворотов в забое и, следовательно, увеличить угол рабочего борта карьера, а также организовать поточную подачу транспорта пот погрузку в забое.
Эффективный путем увеличения степени использования колесных транспортных средств, точнее, источника энергии, в потоках небольшой производительности является применение прицепных кузовов, количество которых на один тягач устанавливается в зависимости от длины перемещения, времени погрузки и времени разгрузки. Применение прицепных кузовов позволяет повысить степень использования тягачей до 0,9.
В настоящее время в связи с увеличением загазованности от эксплуатации автотранспорта на глубоких горизонтах карьеров и ограничением в расходах дизельного топлива возрос интерес к использованию на карьерах троллейвозов. Современные автосамосвалы большой грузоподъёмности с мотор-колесами вполне способны использовать питание от контактных приводов на стационарных участках трассы.
В США фирмами «Юнит Риг» и «Вабко» дизель-троллейвозы выпускаются на базе серийных автосамосвалов, работающих на постоянном токе. В Японии фирма «Комацу» выпускает дизель-троллейвозы на базе 120-тонного самосвала, питаемого переменным током. Применение дизель-троллейвозов увеличивает производительность автотранспорта на 30%, повышает скорость на уклонах на 70%, при этом экономия топлива – до 60%. Канадская фирма «Квебек картьер майнир» за год эксплуатации 22 дизель-троллейвозов большой грузоподъемности при средней длине транспортирования 2,5 м снизила расход дизельного топлива на 87% и увеличила производительность транспортных единиц на 20%.
БелАзом разработаны типовые дизель-троллейвозы грузоподъемностью от 60 до 125 т.
Скорость движения дизель-троллеивозов на горизонтальном участке пути составляет при питании от контактной сети 60 км/ч, от дизель-генераторной установки– 15 км/ч.
Наибольшую эффективность имеет перспектива применения конвейеров для перемещения скальной горной массы. Конвейер как непрерывный вид транспорта при большой производительности потока является средством на пути повышения степени использования всех машин комплекта оборудования технологического потока.
В настоящее время ведутся работы по созданию конвейеров для перемещения скальной горной массы при снижении вредного воздействия кусков горной массы на конвейерную ленту, разработка устройств для загрузки горной массы на конвейер, создание специальных видов конвейеров для скальной горной массы и т.д.
Для доставки руды с нагорных карьеров с энергетических позиций целесообразнее гравитационный транспорт, средством которого являются рудоспуски, рудоскаты. Эффективность рудоспусков повышает возможность использования силы гравитации для попутного естественного дробления.
При доставке руды по 600-метровым рудоспускам с карьера «Центральный». комбината «Апатит» степень дробления руды без специальных дополнительных устройств только за счет естественного дробления увеличивается на 40,6% .Это увеличение степени дробления сокращает активное энергопоглощение в процессе производства продукции на карьере «Центральный» на 68,6 кДж/кг, т.е. на 17%. Целенаправленное использование сил гравитации для дробления руды возможно в коленчатом рудоспуске, (рис.38 ).
Рис.38 Конструкция нижней части рудоспуска с использованием сил гравитации для дробления транспортируемой руды:
1 –вертикальная часть рудоспуска,
2 –наклонная часть рудоспуска,
3 –дробящая плита,
4 – колосниковые грохоты,
5 – контрольные ходки,
6 – контрольные восстающие,
7 – днище рудоспуска.
Расчетные параметры его основаны на экспериментальных и теоретических исследованиях по определению энергии для дробления руды с помощью сил гравитации.
Возможная степень дробления в рудоспуске предложенной конструкции зависит от физико-механических свойств горной массы и глубины рудоспуска.
Сущность естественного дробления руды заключается в том, что при мгновенной остановке движущегося тела, что имеет место при ударе руды о плиту, каждая частица, за исключением тех, которые непосредственно соприкасаются с плитой, продолжает движение в пределах упругих деформаций, что вызывает в одних частях куска сжимающие напряжения, в других – напряжения растяжения. Если эти напряжения превышают предельные, куски руды разрушаются. Для разрушения куска руды от сжимающих усилий требуется больше энергии, чем для разрушения от усилия растяжения. С целью надежности расчетов энергии падающих кусков и возможности их разрушения необходимо предположить, что куски при ударе разрушаются от сжимающих усилий и случайно попавший среди руды кусок породы раздробился до необходимых размеров.
Надежность работы этой конструкции рудоспуска по сравнению с обычно применяющейся вследствие отсутствия остановки рудного потока значительно выше.
В заключение анализа транспорта можно на основании энергетического метода сделать сравнение видов транспорта для забойной части технологического потока для следующего примера: длина фронта 1500 м, высота уступа 20 м из которого видно, что наименьшее технологическое энергопоглощение происходит при перемещении горной массы автомобильным транспортом.
Вместе с преимуществом в энергопоглощении технологические преимущества использования в сложных условиях карьера делают автомобильный транспорт эффективным для забойной части грузопотока.
Для части грузопотока по доставке горной массы из карьера аналогичное сравнение (при глубине карьера 100, 200 и 300 м.) показывает, что наименьшие технологическое энергопоглощения при перемещении горной массы скиповым и конвейерным подъемниками (табл. 13)
Таблица 13
Сравнительные показатели технологического энергопоглощения транспорта части потока по доставке гарной массы из карьера
Вид транспорта
Расчетная зависимость
Энергопоглощение, Дж/кг
Глубина карьера
100 м
200 м
300 м
Железнодорожный
Eж =v2/2g +ωo L +ωi Li
1068
2112
3273
Автомобильный
Eа =v2/2g +ωo L +ωi Li
1073
2122
3190
Конвейерный
Eк =v2/2g +ωo L + Hк
1056
2110
3143
Скиповой подъемник
Eп =v2/2g +ωo L +ωi Li + Нк
998
1998
3080
Энергопоглощение при доставке горной массы конвейерным транспортом является конкурентным автомобильному и железнодорожному транспорту. Если учесть, что горно-капитальные работы для подъемников (скипового и конвейерного) меньше, чем для железнодорожного и автомобильного, то применение их в грузопотоке по доставке горной массы из карьера является перспективным
В технологических потоках на нагорных карьерах активное энергопоглощение в гравитационных средствах доставки (рудоспуски и рудоскаты) отсутствует, поэтому они эффективны для перемещения горной массы,
Для части транспорта поток по доставке горной массы на поверхности карьера по результатам исследования можно считать наиболее эффективным железнодорожный транспорт.
В этой части он обладает большими преимуществами перед остальными видами транспорта, вследствие того, что он обладает меньшим сопротивлением перемещению, включая отрезки пути на отвале.
Сопротивление движению на отвале при автомобильном транспорте возрастает в два раза (в забое ωо = 50—80 Н/кН, на отвале ωо = 150-130 Н/кН ).
9.6 Отвалообразование
Отвалообразование – конечный процесс технологического потока на вскрышных работах. Специфика работы машины на отвалообразовании состоит в том. что пункт приема груза все время перемещается. В настоящее время тенденция увеличения мощности бульдозеров на отвале энергетически целесообразна, применение одноковшовых экскаваторов по тем же причинам, которые были изложены в разделе выемочно-погрузочных работ на отвалообразовании, нерационально.
Увеличение мощности бульдозеров сделало возможным их применение для отвалообразования при железнодорожном транспорте.
Если учитывать сказанное по эффективности выемочно-погрузочного процесса технологического потока во взаимосвязи с качеством горной массы, то можно сделать предположение, что на отвале при колесном транспорте возможно применение выемочно-погрузочных машин непрерывного действия с рабочим органом роторного типа.
Отвальный плуг по принципу действия отвечает технологии непрерывного отвалообразования, но при увеличении производительности требуется увеличение мощности отвального плуга, его веса, однако, увеличение веса вступает в противоречие с устойчивостью отвала и допустимой нагрузкой на временный железнодорожный путь отвала, поэтому перспектива применения отвальных плугов ограничена небольшой производительностью.
При конвейерном транспорте отвалообразование предусматривается с помощью ленточного отвалообразователя. Принципиальные положения по мощности и технологии работ практически не отличаются от отвалообразования мягких пород в транспортно-отвальных комплексах.
10. Выводы анализа технологических процессов на карьерах
Анализ перспектив развития техники и технологии на карьерах со скальными породами по процессам на основе энергетического метода позволяет сделать следующие выводы:
Перспективными для открытых горных работ являются:
1) совершенствование существующей технологии разработки месторождений с крепкими горными породами и главное организации горных работ для доведения степени использования мощного надёжного оборудования в технологическом потоке до 95-97 %
2) уменьшение диаметра скважин;
3) применение агрегатов для бурения сразу нескольких рядов
скважин с механическим заряжанием взрывчатым веществом;
4) механическое рыхление при подготовке горных пород к выемке крепостью до f = 8;
5) использование специальной роторной погрузочной машины непрерывного действия в выемочно-погрузочном процессе;
6) перемещение горной массы в забойной части технологического грузопотока специальными карьерными автопоездами большой грузоподъемности с двусторонним движением при большой производительности потока или использования прицепных кузовов для потоков малой производительности;
7) применение подъемников (скиповых, или
конвейерных) для доставки скальной горной массы из карьера, а
с нагорных карьеров гравитационных средств доставки;
8) применение для отвалообразования бульдозеров и специальных машин непрерывного действия.
Исходя из этого анализа, принципиальная схема перспективного оборудования технологического потока, отвечающая специфике открытых работ на карьерах со скальными и полускальными породами, представляется в вариантах;
– мощные выемочно-погрузочные машины высокой надёжности и производительности с высокой степенью использования во времени;
– выемочно-погрузочный машина непрерывного действия или комбайн с автомобильным или конвейерным транспортом;
– буровзрывной агрегат, выемочно-погрузочная машина непрерывного действия с перемещением горной массы автомобильным или конвейерным транспортом.
Глава 7
Влияние параметров элементов систем разработки месторождений на энергосбережение в технологии добычи полезных ископаемых.
1.7 Угол откоса рабочего борта карьера.
Высокие темпы развития открытых горных работ на базе внедрения новой техники и технологии, снижение на этой основе затрат на добычные и вскрышные работы на карьерах позволили значительно увеличить эффективные границы открытых горных работ. Так, на некоторых отечественных карьерах горные работы проводятся уже на глубине 350—500 м проектируется глубина 500—800 м.
Большая глубина разработки при существующих системах разработки требует значительного разноса бортов карьера, что повышает объёмы вскрыши, текущий коэффициент вскрыши, а следовательно, энергетические и материальные затраты на производство продукции карьера.
Рассматривать влияние элементов систем разработки в совокупности с параметрами комплектов оборудования технологических потоков на энергозатраты производства продукции карьера можно через текущий коэффициент вскрыши. Известно, что он уменьшается при увеличении угла рабочего борта карьера (рис.39).
Рис.39 Влияние элементов систем разработки:
а – изменение текущего коэффициента вскрыши в зависимости от угла рабочего борта карьера,
б – влияние угла наклона уступа на угол рабочего борта карьера.
В настоящее время имеются два пути увеличения угла рабочего борта карьеров:
1. Увеличение угла откоса уступа, в результате чего угол рабочего борта карьера повышается на 13%.
Средством получения устойчивого безопасного крутого откоса является контурное взрывание.
2. Сокращение рабочей площадки вкрест простиранию фронта работ, т.е. по направлению разноса бортов карьера.
В настоящее время ширина рабочей площадки, как правило, проектируется с учетом размещения развала горной массы, транспортных коммуникаций и резервной зоны, учитывающей неравномерность подвигания фронта работ на горизонтах.
Средством сокращения ширины рабочей площадки в направлении расширения контура карьера является панельная схема отработки горизонтов.
Сущность этой схемы заключается в том, что развал горной массы направляется в торец широкой заходки (рис.40). В результате появляется возможность сокращения рабочей площадки в сторону расширения контура карьера до величины транспортной полосы и резервной зоны.
Величина широкой заходки, которая влияет на ширину панели, определяется в зависимости от учёта наклона рудного тела и принятой
схемы проведения разрезной траншеи.
Рис.40 Панельная схема отработки горизонтов: а 1 –ряд контурных скважин, 2 – заряды на рыхления массива горных пород с направлением развала вдоль фронта работ, в – обычная схема отработки горизонтов с направлением развала горой массы взрывом вкрест простиранию фронта работ.
Использование в данной схеме изложенного выше способа увеличения угла рабочего борта карьера за счет контурного взрывания увеличивает ее эффективность. Затраты на контурное взрывание при этой схеме отработки горизонтов уменьшается обратно пропорционально увеличению ширины заходки по сравнению с общей.
Дальнейшее сокращение рабочей площадки до величины предохранительной бермы приводит к схеме отработки горизонтов с тупиковым движением транспорта забойной части технологического потока (рис. 41).
Рис.41. Изменение угла наклона рабочего борта карьера при сокращении ширины рабочей площадки в направлении разноса бортов карьера: а – при существующей технике и технологии отработки горизонтов; б – при направлении развала горной массы при взрыве в торец заходки и расположение вдоль фронта работ; в – при направлении развала горной массы в торец заходки и при тупиковой подаче транспортных средств в забой; г – при панельной схеме отработки горизонтов с расположением рабочей площадки по простиранию фронта работ.
Высота уступа является функцией рабочих параметров выемочных машин. Но известно, что с увеличением высоты уступа увеличивается и угол рабочего борта карьеров.
В то же время увеличение высоты уступа приводит к необходимости иметь большую рабочую площадку для размещения развала горной массы.
В этом случае панельная технология отработки горизонтов, при которой развал горной массы направлен в торец уступа, позволяет совместить стремление увеличить высоту уступа, иметь достаточное пространство для размещения развала и сократить ширину рабочей площадки вкрест фронта работ.
С другой стороны, исследование способов подготовки горных пород к выемке показывает, что надежное получение качественной горной массы возможно при скважинах малого диаметра. Средством для ее получения является комбайн или буро-зарядный агрегат.
Как показало исследование, высокопроизводительная работа комплектов с комбайном или бурозарядным агрегатом обеспечивается при высоте уступа 5—8 м. Для существующих типов выемочно-погрузочных машин, как показывают моделирование и исследования за рубежом, что высота забоя в развале горной массы в пределах 1,8—4 м. обеспечивает минимальные затраты рабочего времени на заполнение ковша.
При подготовке горных пород к выемке рыхлителем или фрезерным органом комбайна разработка ведется слоями глубиной 0,20—0,40 м. Поэтому, учитывая увеличения угла рабочего борта карьера и рассмотрев возможные пути его увеличения, необходимо на основании вышеизложенного сделать вывод эффективности технологии разработки уступами любой технологически принятой высоты (Рис.42).
Рис.42 Технология разработки горных пород комбайнами уступами малой высоты: а – фрезерным комбайном с погрузкой в автотранспорт, б – комбайном слоями на высоком уступе с погрузкой в штабель.
2.7 Технология отработки месторождений полезных ископаемых этапами под углами бортов этапа, равных углу погашения горных работ или близким к нему
Геологические условия месторождений со скальными породами в большинстве своем представляют собой наклонные и крутопадающие залежи рудных тел. Основные формы рудных тел – штокообразная или жильная и пластообразная.
В настоящее время для разработки месторождений применяются технологии, предусматривающие развитие горных работ под рабочими углами бортов карьера. Коэффициент вскрыши при этом по мере развития горных работ растет и, достигая предельной величины (при kт = kгр т.е. максимальном разносе бортов карьера) а следовательно энергозатрат, начинает уменьшаться при углублении в отстроенных бортах карьера под углами погашения. Особенно ощутим рост коэффициентов вскрыши в первый период эксплуатации карьера.
Стремление уменьшить текущий коэффициент вскрыши выражается сокращением ширины рабочей площадки, сдваиванием горизонтов для увеличения высоты уступа, применением панельной схемы отработки горизонтов с направлением развала внутри широкой заходки.
Однако все эти мероприятия, улучшая энергетические и экономические показатели, сохраняют в целом порядок разработки месторождений, а следовательно, в принципе и характер изменения коэффициента вскрыши.
Исследования показывают большую эффективность разработки месторождений этапами, которые позволяют снизить величину текущего коэффициента вскрыши в период отработки этапа (заштрихованная площадь рис. 44), а, следовательно, энергозатраты.
Глубина первого этапа определяется эффективностью работы одного вида транспорта (200-250 м), второго – комбинацией автомобильного в качестве сборочного транспорта и конвейерного магистрального по борту карьера, третьего – комбинацией автомобильного в качестве сборочного транспорта и конвейерного или грузоподъёмного магистрального в подземных вскрывающих выработках.
Время отработки каждого этапа в 15 – 20 лет соразмерно сроку модернизации оборудования и необходимостью перехода на новую технологию и вследствие этого реконструкцию карьера (Рис. 43).
Рис 43 Эффективность отработки крутопадающего месторождения этапами по глубине.
Оставленный объём вскрыши в первом этапе попадает в контуры второго этапа, но в тоже время часть вскрыши второго этапа переносится на период отработки третьего этапа. Учитывая время отработки этапа 15-20 лет вследствие совершенствования техники и технологии за это время переносимые объёмы вскрыши в следующие этапы, будут отработаны большой эффективностью.
Угол рабочего борта карьера в пределах этапа принимается из условия сохранения принятых элементов систем разработки. Угол откоса контура этапа могут быть равными углу погашения отработки месторождения (βmax) или, чтобы не останавливать работу по добыче полезного ископаемого в период перехода от одного этапа к другому, равному промежуточной величине между углом рабочего борта и погашения (Рис.44).
Рис.44 Углы откосов бортов карьера промежуточных этапов отработки: а – равными углу погашения в конце отработки месторождения, б – равными промежуточной величине между углом рабочего борта и погашения
В контуре каждого этапа вытянутого пластообразного месторождения направление фронта работ может совпадать с направлением простирания (Рис.45), для округлого в плане штокообразного крутопадающего месторождения – по периметру или по спирали (Рис.46 а, б).
Рис. 45. Разрез и план при технологии разработки этапами на вытянутом пластообразном месторождении
а
б.
Рис. 46. Разрез и план при технологии разработки этапами на крутопадающем штокообразном месторождении: а – с направление фронта работ по периметру, б – по спирали.
Этап может отрабатываться уступами любой высоты, начиная от нескольких десятков сантиметров, при отработке горных пород комбайнами, до любой технически возможной.
Ширина этапа на горизонте определяется высотой этапа и углом наклона залежи и бортов карьера (рис.45)
где П – производительность карьера по полезному ископаемому;
n – число добычных экскаваторов на каждом горизонте;
Q – эксплуатационная производительность добычного экскаватора;
β – угол наклона борта карьера, град.
Этапы отрабатываются последовательно. Причем при изменении плановой производственной мощности карьера возможно изменение параметров этапа в течение его отработки иди в момент перехода от одного этапа на другой.
Подготовка горных пород к выемке при комплексах из существующего оборудования производится сразу на всю ширину этапа.
Развал горной массы при взрыве направлен внутрь широкой заходки, т.е. по простиранию фронта работ (рис.47).
Рис.47 Технология отработки вытянутого по простиранию платообразного месторождения этапами
Откос уступа может быть любым. При вертикальном или крутом откосе для повышения устойчивости целесообразно производить контурное взрывание для оконтуривания взрывного блока в направлении расширения контура карьера.
Благодаря большой ширине этапа транспортные коммуникации при данной технологии можно располагать на безопасном расстоянии от откоса уступа.
Выемку разрыхленной горной массы от забоя можно проводить одним или несколькими экскаваторами, создавая мощный концентрированный поток горной массы с горизонтов. Концентрация горных работ на горизонте повышает эффективность разработки месторождений, вследствие сокращения числа рабочих технологических потоков на карьерах. Уменьшение количества потоков упрощает инженерное решение их размещений, упрощает организацию работ.
При переходе с одного этапа на другой объемы вскрышных работ увеличиваются, поэтому текущий коэффициент вскрыши при переходе с одного этапа на другой будет увеличиваться на постоянную величину. Соответственно этому график текущего коэффициента вскрыши при отработке этапа примет вид прямой, а для всего месторождения – ступенчатой.
Данная технология разработки дает возможность планировать ступенчатое изменение экономических показателей предприятия после добычи определенного количества полезного ископаемого.
Это дает возможность планировать и получать постоянную прибыль в течение отработки этапа. Разработка месторождений при данной технологии начинается с минимальных объемов вскрыши и, следовательно, с капитальными минимальными затратами. Разработка месторождения прекращается отработкой этапа, в котором текущий коэффициент вскрыши равен предельному по эффективности открытых горных работ.
Разработка месторождения этапами дает возможность перенести основную массу вскрышных работ на более поздние периоды отработки месторождения, что позволяет произвести эти работы новейшими типами оборудования, которые появятся в результате рассмотренных перспектив технического прогресса в механизации производственных процессов с более высокой производительностью и меньшими затратами.
При технологии разработки месторождений этапами эффективно применение грузопотоков с комбинированным транспортом, где в забойной части используется автомобильный транспорт.
Вместе с этим независимость параметров от высоты уступа делает ее перспективной для новых средств разработки горных пород: рыхлителей, автопогрузчиков, погрузочных машин непрерывного действия, комбайнов и т.п. Появление технологии разработки этапами является следствием тенденции увеличения и концентрации мощности, машин в забое, развития исследований по разработке месторождений этапами и панельного способа отработки горизонтов.
Применение технологии разработки этапами позволяет:
Непосредственно после строительства карьера обеспечить
его проектную мощность, причем период строительства сокращается.
Время отработки одного этапа зависит от длины карьерного поля.
На первом этапе работает минимальное количество экскаваторов, а при переходе с одного этапа на другой их количество увеличивается. Оборудование, занятое на отработке этапа, может полностью амортизироваться в конце его отработки. Для следующего этапа появляется возможность применять новые виды горного оборудования, причем это не потребует дополнительных затрат на реконструкцию карьера.
В связи с уменьшением текущего коэффициента вскрыши,
а также объема вскрышных работ на первых этапах снижаются
затраты на производство продукции, а, следовательно, себестоимость полезного ископаемого. Так, на первом этапе сокращение затрат на производство единицы продукции по сравнению с существующей технологией достигает 40—50%.
ЗАКЛЮЧЕНИЕ
Для добычи твердых полезных ископаемых открытым способом комплектом оборудования при определенной технологии, схеме вскрытия и системе разработки необходимо затратить энергию на вскрышные и добычные работы.
Добыча твёрдых полезных ископаемых является самым энергоёмким производством среди промышленных отраслей.
Энергозатраты определяются свойствами разрабатываемых горных пород, природными условиями месторождения и механизацией производственных процессов. Чем выше соответствие технологии и механизации горных работ природным условиям месторождения, тем выше энергоэффективность добычи полезных ископаемых, а, следовательно, ниже себестоимость добычи.
Рассмотренные в книге пути и энергетическая оценка касаются всех аспектов технологии и механизации горных работ на карьерах: разрушения массива горных пород, технологических процессов, систем разработки и вскрытия карьерных полей.
Энергетический метод позволяет в конкретных горно-геологических условиях выбирать соответствующую природным условиям механизацию горных работ по технологически потокам и энегоэкономичную технологию разработки месторождения, что позволяют существенно снизить затраты на открытую добычу полезного ископаемого.