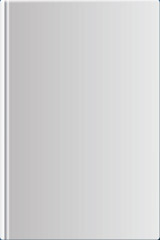
Текст книги "Метод определения энергоэффективности технологий и механизации горных работ по добыче полезных ископаемых открытым способом"
Автор книги: Юрий Анистратов
Жанр:
Технические науки
сообщить о нарушении
Текущая страница: 2 (всего у книги 8 страниц)
Для открытых горных работ сущность этого метода заключается в том, что для производства горных работ на карьере при определенной технике и технологии необходимо затратить энергию на дробление массива для получения требуемого состава горной массы по крупности и степени разрыхления, выемку и погрузку породы, перемещение и укладку ее в отвал для вскрыши или переработку для полезного ископаемого.
При этом энергия расходуется на преодоление сопротивления рабочих органов самих машин в технологических процессах и для совершения полезной работы по переводу объекта приложения энергии (горной породы) из одного состояния в другое.
Расход первой части энергии учитывается коэффициентом полезного действия передачи энергии от источника к рабочим органам и коэффициентом полезного действия самих рабочих органов.
Расход второй части энергии зависит от технологии процесса и определяется свойствами горной породы, степенью изменения качества и состояния в процессе воздействия на неё.
Изменение качества, обусловленное технологией и на карьерах породами, представляет собой разрушение массива и создание разрыхления горной массы, подъем для погрузки, перемещение и т.п.
Вторая часть энергии, которая как бы “поглощается” горной породой в процессе производства, называется технологическим энергопоглощением. Оно измеряется в джоулях (Ет =F × L – сила на путь). Сила (F) измеряется в ньютонах, путь (L) – в метрах.
Применительно к горному производству под энергопоглощением горной породой понимается расход полезной энергии для превращения массива в горную массу требуемого состава по крупности, подъёме её на высоту, перемещение и укладку в отвал для пустых пород и переработку для полезного ископаемого. При этом во время дробления массива энергия расходуется на преодоление природных сил сопротивления разрушению, при подъёме – преодоление сил гравитации, при перемещении – преодоление сопротивления движению.
Использование понятия «поглощение энергии» вместо «расход энергии» позволяет конкретизировать то обстоятельство, что расходуется полезная, а не фактически затрачиваемая энергия, выражая собой закон перехода количества энергии в качество горной массы и её перемещение.
Величина энергопоглощения зависит от свойств горных пород и от технологических параметров производственного процесса.
В расчетной зависимости энергопоглощения в общем виде свойства горных пород выражаются через сопротивление, оказываемое рабочему органу машины, а технологические параметры через путь, который рабочий орган преодолевает, это сопротивление и производит определенное количество продукции, заданного технологией качества
,
где Эт – удельное технологическое энергопоглощение Дж/кг;
F– сопротивление, оказываемой горной породой, Н;
L – величина пути, на котором преодолевается сопротивление горной породы, м;
Р – количество продукции, произведенный в рабочий цикл, кг
Основное сопротивление горной породы оказывают: в процессе подготовки горных пород к выемке – молекулярные связи, плотность горных пород и физическое состояние массива. В процессе выемки и погрузки – связанность, объемный вес, зацепление кусков горной породы, состав по крупности, трение. В процессе перемещения – объемный вес, связанность горной массы, трение. При отвалообразовании – объемный вес, зацепление, трение. При переработке – молекулярные связи, петрографический состав и плотность.
Некоторые из перечисленных свойств горных пород не являются постоянными, а изменяются под воздействием окружающей среды. Например, связанность горной массы и сопротивление внедрению ковша увеличиваются в результате слеживания горной массы, смерзаемости, заснеженности и т.д.
Некоторые свойства являются результатом принятой технологии или качеством выполнения работ в предыдущих процессах, например, состав горной массы по крупности, зацепление, степень разрыхления и т.п.
Общее энергопоглощение горной массы будет представлять собой сумму энергопоглощений по процессам технологического потока.
Вследствие того, что энергопоглощение зависит как от свойств горных пород, так и от технологических параметров, появляется возможность сравнивать между собой в аналогичных условиях различные комплекты оборудования технологических потоков или отдельные их звенья и выбирать вариант с меньшими значениями как наиболее эффективный.
В конкретных природных условиях месторождения или отдельной природно-технологической зоны карьера в сравнительных расчётах для выбора варианта с меньшим энергопоглощением комплекта оборудования технологического потока или технологии горных работ целесообразно пользоваться показателем энергопоглощения единицей горной массы (удельное энергопоглощение )
Для расчетных зависимостей определения энергопоглощения необходимо рассмотреть взаимосвязь свойств горных пород с технологией производства работ по процессам в технологическом потоке.
В настоящие время широко развиваются исследования по физике горных пород. Накопление данных о свойствах горных пород в массиве, образце и разрыхленном состоянии и их сопротивлении при добывании позволяет использовать их в энергетическом методе исследования горных работ на карьерах.
2.2. Энергопоглощение по процессам технологического потока.
Процесс подготовки горных пород к выемке.
Это первый процесс технологического потока. Мягкие горные породы не требуют специальной подготовки к выемке, а массив крепких (скальных и полускальных) требует предварительного разрушения и дробления для обеспечения следующего процесса – экскавации.
Энергопоглощение горных пород при дроблении зависит от молекулярных сил связи, дислокаций кристаллической структуры горных пород и нарушенности массива под действием эрозионных разрушений, естественной трещиноватости (блочности) и трещинообразования от сейсмического воздействия предшествующих взрывных работ на уступе.
Расходуемая при взрыве массива кинетическая энергия продуктов взрывчатого вещества переходит в потенциальную энергию вновь создаваемых поверхностей и другие формы – тепло, звук и сейсмические волны.
Энергопоглощение монолитных, не нарушенными трещинами зон массива или отдельного блока, при разрушении взрывом, подчиняется теории Риттингера, согласно которой работа дробления полностью переходит в поверхностную энергию и равна
где W – работа измельчения, Дж;
D и d – размеры кусков до и после дробления;
k1 – постоянная величина.
Если принять отношение как степень измельчения, то формула будет иметь вид
По теории Кирпичева-Кика работа, требуемая для изменений конфигураций геометрически подобных тел из одинакового материала, изменяется пропорционально объемам или весам этих тел. В общей формуле закон Кика выражается:
По теории Бонда работа, расходуемая на дробление материала от размера D до размера d, равна разнице количеств суммарной энергии, необходимой для того, чтобы довести размер материала от теоретически бесконечного до размеров D и d. Эта теория является промежуточной между теориями Риттингера и Кика. В ней предполагается, что энергия, передаваемая телу при сжатии, распределяется сначала по его массе и, следовательно, пропорциональна D3 , но с момента начала образования на поверхности трещины эта энергия концентрируется на поверхности краев трещины и тогда она пропорциональна D2. На этом основании применяется, что работа разрушения тела пропорциональна D2,5 и, следовательно, удельная работа дробления выражается формулой
Если ввести зависимость от степени дробления n, то формула примет вид
Помимо указанных теорий дробления существует ряд других.
Для расчета энергии при дроблении массива взрывом используется теория Бонда; ее математический аппарат и прикладное значение имеет отношение также к дроблению и измельчению в дробилках и мельницах.
В формуле Ванга установлена взаимосвязь между степенью дробления и силой сжатия, удельным весом материала и его модулем упругости
где F– предел прочности на сжатие (сж)
– удельный вес породы;
Е – модуль упругости;
k – коэффициент пропорциональности.
Эффект дробления от сжатия или удара, по данным исследований
Р. Гийо, практически одинакова.
Модель расчета энергопоглощения процесса подготовки горных пород к выемке на карьере при n – ой степени дробления можно представить следующим образом.
Взрывной блок представляет собой массив объёмом Vбл. высотой, равной высоте уступа Н, шириной, равной ширине заходки по целику А, и длиной Lбл. Этот блок разбит естественной трещиноватостью и трещиноватостью от сейсмического воздействия предыдущих взрывов на блоки средней величины dо.
Связь между этими блоками в массиве меньше, чем молекулярная связь горной породы внутри этих блоков.
Таким образом, при подготовке взрывного блока энергия расходуется на разрушения массива на блоки и блоков на куски.
– коэффициенты пропорциональности;
– степень трещиноватости взрываемого массива;
L – ширина взрывного блока,
– степень дробления монолитного блока;
do – средний размер отдельности в массиве;
dср – средней размер куска горной массы, подготовленной к экскавации.
Для сравнительных расчетов по выбору оптимальных комплектов оборудования технологических потоков в одинаковых условиях можно условно принять разрушение только монолитов взрывного блока и использовать более простую формулу для расчета затрат энергии на дробление по теории В.Л. Кирпичева, по которой энергия разрушения пропорциональна объёмам или массам разрушаемых тел.
где е – прочностные свойства горных пород, называемые удельной энергией упругой деформации.
V – объём или масса тела.
Это выражение получается в результате анализа диаграммы: напряжение-деформация горной породы.
В этом выражении: – предел прочности среды на разрушение, Па;
Е – модуль упругости, Па.
При условии упругопластической деформации горной породы при её разрушении величина удельной энергии деформации больше в 3 раза.
Учитывая это, расчёт необходимой энергии (Дж) для дробления единицы объёма горных пород (V=1) с конкретными свойствами, которая как бы поглощается породой при дроблении в необходимой степени и может именоваться как удельное энергопоглощение, производиться по формуле:
,
Сопротивление горной породой разрушению при взрывном дроблении массива связано с явлением практически всех деформаций, однако для инженерного расчёта затрат энергии на этот процесс целесообразно использовать простой для измерения показатель предел прочности породы на сжатие.
Из экспериментальных исследований многих авторов известно, что соотношение сил сжатия и растяжения при динамическом нагружении тела составляет
= 0,1сж.д + р.д.
Соотношение между динамическим и статическим напряжением пропорционально коэффициенту динамичности kд = Ед/Ест., где Ед и Ест. модули упругости при динамическом и статическом нагружении.
При статической нагрузке соотношение между пределом прочности на сжатие и растяжение р = 0,1сж., следовательно, сопротивление среды взрывному, разрушению выраженное через предел прочности на сжатие при статическом напряжении по аналогии можно представить как = 0,2сж.kд В этом случае формула расчёта энергопоглощения для дробления горных пород в n-ной степени может быть представлена в следующем виде :
Помимо энергопоглощения на разрушение массива в процессе подготовки крепких горных пород к выемке на карьере взрывным способом необходимо затратить энергию для получения по принятой технологии и технике требуемой степени разрыхления и формирования развала горной массы допустимого по правилам безопасности.
Энергопоглощение горных пород при создании необходимой степени разрыхления и перемещения центра тяжести развала горной массы пропорциональны кинетической энергии движущихся массы с учётом её плотности и массы. В свою очередь кинетическая энергия зависит от начальной скорости движения горной массы vо.
где kp – коэффициент разрыхления:
lц – расстояние от центра тяжести заходки массива до центра тяжести развала горной массы (рис. 5)
dср.– величина среднего куска взорванной горной массы.
Рис.5 Схема к расчёту перемещения центра тяжести развала
Это выражение получено из условия, что центр тяжести заходки
l = ½ А, центр тяжести развала lр = ½(А-1/2R).
Тогда lц = lр – lз = 1/4R.
Величина развала
которая получена
Sз = AН = (с + НCtg) H,
Sг.м.= kрАН = kр(c + HCtg)H
Sр = Sг.м. – Ahр = (с + НСtg)(kрH – hр) = 1/2Rhч.
где Н– высота уступа, м;
hр– высота развала, м;
с – расстояние первого ряда скважин от верхней бровки уступа, м;
А – ширина заходки по целику, м;
R – ширина развала, м;
– угол откоса уступа, град.
Общая энергия равна сумме энергии на дробление массива, создание разрыхления и перемещение его центра тяжести
Эд = Эдр. + Эр .
Удельное энергопоглощение единицей объёма взорванной горной массы в развернутом виде
Удельное энергопоглощение единицей массы взорванной горной массы в развернутом виде
Оно представляет собой энергию, которую необходимо затратить при подготовке горной массы требуемой по технологии крупности и параметрам развала с учётом конкретных свойств массива.
В случае подготовки горных пород механическими средствами при безвзрывной технологии необходимая удельная энергия в Дж/кг складывается из разрушения и создания разрыхления:
При взрывной подготовке горных пород в технологическом грузопотоке для размещения взрывчатого вещества в массиве необходимо затратить энергию на бурение скважин.
В этом процессе горная порода будет поглощать энергию при разрушении (измельчении) буровым инструментом в объеме скважины в степени
n’ = dскв./dч
где dскв. – диаметр скважины;
dч – диаметр частиц и продуктов разрушения при бурении.
Пользуясь принятыми выше зависимостями расчета энергопоглощения при разрушении горных пород, можно посчитать удельное энергопоглощение в процессе бурения в Дж/кг при тех же условиях по следующей формуле:
где сж – предел прочности породы на сжатие при шарошечном или ударном бурении, Па;
lcкв. – глубина скважины, м;
– часть энергопоглощения горной породы при бурении, приходящегося на единицу объёма взрываемого блока,
nскв. – количество скважин взрываемого блока;
Sскв. – площадь скважины, м2;
h – высота уступа, м;
A – ширина заходки, м.
Выемочно-погрузочный процесс.
В выемочно-погрузочном процессе горная масса при переходе из одного состояния (развал горной массы) в другое (захват и перемещение в транспортный сосуд) поглощает энергию.
В процессе черпания горная масса оказывает сопротивление. Чем больше степень дробления и коэффициент разрыхления, тем меньше сопротивление.
Второй операцией в цикле погрузочного процесса является подъём горной массы для погрузки. Все существующие погрузочные машины совмещают процесс черпания с подъёмом на уровень погрузки.
Подъем ковша на уровень разгрузки связан с затратами энергии на преодоление единицы веса горной породы в ковше.
Расчетную зависимость энергопоглощения выемочно-погрузочного процесса на единицу горной массы в Дж/кг можно представить следующим образом:
Первое слагаемое представляет собой выражение для расчёта энергопоглощения при преодолении сопротивления горной массы внедрению ковша. В нём не учитывается скорость, с которой перемещается ковш во время черпания, так как пределы изменения ее на выемке и вносимая при этом погрешность незначительны.
Второе слагаемое представляет собой выражение для расчёта энергопоглощения в процессе поворота со средней скоростью ковша для разгрузки, т.е. своего рода преодоление сопротивления инерции.
Третье и четвёртое слагаемые выражают энергопоглощение в процессе перемещения ковша к месту и на уровень разгрузки,
где F – сила сопротивления перемещению ковша. По проф. Н.Г. Домбровскому она может быть определена F = kc B c;
kc – удельное сопротивление горной породы копанию, кг/см2 (для хорошо взорванных пород kc= 2,25-2,50 кг/см2);
В – ширина ковша , см;
c – толщина стружки, см (0,33В);
– длина пути, на котором происходит заполнение ковша (для ковшевого экскаватора 2/3 hч , для многочерпакового экскаватора hуступа/Sinα).
hч – высота черпания экскаватора.
Р – вес породы в ковше, P = (Ек )/kр ;
Ек – вместимость ковша, м3;
kр -коэффициент разрыхления;
– плотность породы, кг/м3;
vп – скорость перемещения ковша к месту разгрузки (vп = 5 – 11 м/сек – большее для вскрышных экскаваторов);
g – 9,8 м/сек2 ;
l – расстояние перемещения ковша к месту разгрузки, м
hр – высота разгрузки экскаватора, м.
Для многоковшового и роторного экскаватора
о – основное сопротивление движению конвейерного транспорта, на экскаваторе, Н/kH;
L – расстояние перемещения по конвейеру на экскаваторе, м.
Процесс перемещения горной массы
Энергопоглощение горной массы в процессе перемещения транспортными средствами происходит в момент преодоления инерции и в процессе преодоления сопротивления во время движения. Если по пути перемещения происходит подъем горной массы, то энергопоглощение увеличивается на преодоление сопротивления от уклона для колесных видов транспорта и на величину Н подъема горной массы при других видах транспорта.
В общем виде выражение энергопоглощения единицы горной массы в процессе перемещения в Дж/кг может быть представлено следующим образом:
Эт = + oL +H.
где – энергопоглощение во время преодоления инерции;
V – скорость перемещения, м/сек;
о – основное сопротивление движению, Н/кН ;
L – длина перемещения, м;
H – высота подъема в процессе перемещения, м.
Конкретно для видов транспорта расчетные зависимости представляются в следующем виде.
Железнодорожный транспорт
Ет = +oL + iLi +rLr ..
где V – скорость движения транспорта, м/сек;
g – ускорение свободного падения, м/сек2;
o – основное сопротивление движению, Н/кН
(обычно 0,002-0,003 Н/кН);
L – расстояние перемещения, м.
С учетом движения на подъем
, м
L2 – длина горизонтальной части, м;
H2 – высота подъема, м;
i – сопротивление от подъема или уклона,
(равно уклону i = 0.0030.004);
Li – длина участка перемещения с уклоном
i – уклон трассы;
r – сопротивление на криволинейном участке пути:
для стационарных путей – 1300/1000R,
для забойных путей – 700/1000R.
R – радиус закругления, м;
Lr – длина участка криволинейного пути, м.
Автомобильный транспорт
Ет = V2/2g + oL + iL.
где о = 0,015-0,045 Н/кН – для главных откаточных дорог;
0,050-0,080 Н/кН – для забойных дорог;
0,080-0,300 Н/кН – для отвальных дорог;
i= i – аналогично железнодорожному транспорту, Н/кН.
Конвейерный транспорт
Ет = V2/2g + oL + Hк
где о=0,025-0,030, Н/кН ;
Нк – высота подъема горной массы в процессе перемещения конвейерным транспортом, м.
Расчётная формула для трубопроводного транспорта аналогична конвейерному транспорту.
Процесс отвалообразования
При отвалообразовании горная масса перемещается из пункта разгрузки к месту складирования различными средствами. При экскаваторном отвалообразовании расчетная зависимость аналогична приведенной при описании выемочно-погрузочного процесса, при плужном и бульдозерном может быть представлена в Дж/кг следующим образом:
Эо = (f1±i + f1f2)l.
где f1 = 0,7 1,0 – коэффициент трения породы о породу;
i – уклон отвала;
f2 = 0,4 0,6 – коэффициент трения породы по металлу;
l – расстояние перемещения породы на отвале.
Процесс переработки полезного ископаемого
Энергопоглощение в процессе переработки зависит от вида самого полезного ископаемого и его назначения.
Для примера можно рассмотреть переработку полезного ископаемого для получения готового продукта – щебня и второй пример – переработка полезного ископаемого для получения промежуточного продукта – тонкого помола для раскрытия зерен полезного ископаемого перед последующем обогащением.
В процессе переработки на щебень поступающая в бункер дробильно-сортировочной фабрики горная масса имеет крупность dср. и проходит несколько стадий дробления (крупное, среднее и мелкое), в результате которого получается продукт – щебень фракции d. Перед и между дроблениями горная масса подвергается грохочению и промывке, от одной технологической операции к другой она перемещается конвейерным транспортом.
Энергопоглощение в процессе дробления определяется по той же зависимости, по которой определяется энергопоглощение в процессе подготовки горных пород к выемке (Дж/кг):
Энергопоглощение активного грохочения связано с преодолением сил инерции покоя и сопротивления перемещению горной массы по грохоту:
Эгр. = + Fгр.l,
где vгр. – скорость перемещения горной массы по грохоту;
Fгр.– сопротивление перемещению горной массы по грохоту;
l – длина грохота.
Энергопоглощение в процессе перемещения между отдельными операциями переработки зависит от сопротивления конвейеров:
Эп = + olф + Н
где v – скорость движения конвейера;
o – основное сопротивление движению;
lф – суммарная длина перемещения конвейерным транспортом, м;
H – суммарная высота подъема полезного ископаемого в процессе перемещения, м.
Если полезное ископаемое при переработке подвергается обогащению, то руда после крупного, среднего и мелкого дробления подвергается измельчению в шаровых мельницах. Это самый энергоемкий процесс потому, что для раскрытия зерен полезного компонента требуется тонкий помол. Энергопоглощение при помоле примерно в 200 раз больше энергопоглощения при подготовке горных пород к выемке.
Эмпирические исследования показывает, что общие энергозатраты при крупном дроблении крепких руд составляет 3-4 кВт-ч/т, для мелкого дробления 5-6 кВт-ч/т, для грубого помола при подготовке горной массы к обогащению 20-30 кВт-ч/т и для тонкого помола 100-1000 кВт-ч/т.
Установленные расчетные зависимости для определения энергопоглощения единицы горной массы являются минимально необходимыми для определенного вида технологического потока и комплекта оборудования. Энергопоглощение горной массой складывается из энергопоглощения в технологических процессах при переводе единицы горной массы определенного качества и свойств из одного состояния в другое согласно технологии производства продукции требуемых кондицией.
Общее выражение энергопоглощения горной массой в технологическом потоке
Общее выражение технологического энергопоглощения в потоке будет представлять сумму энергопоглощений по технологическим процессам: подготовка горных пород к выемке (бурение и взрывание) выемка-погрузка, перемещение и отвалообразование во вскрышном технологическом потоке или переработка в добычном технологическом потоке.
Суммарное по всем процессам технологическое энергопоглощение горной массыв в Дж/кг
Эт = Эб. + Э в.д. + Ээ + Эт.+ Эо. (перераб)
В расчётном виде:
+ oL + H для вскрыши + (f1±i + f1f2)l
для полезного ископаемого + ( + Fгр.l + + olф + Н).
При проектировании или модернизации комплекта оборудования технологического потока в конкретных природных условиях месторождения или отдельной природно-технологической зоны карьера сравнение вариантов механизации горных работ предложенным методом позволяет выбрать вариант с меньшим энергопоглощением, а, следовательно, меньшими затратами.
Например, сравнение по энергопоглощению трёх вариантов механизации технологического потока по добыче апатита и доставки его до бункера обогатительной фабрики:
1 – СБШ-200 + ЭКГ-4,6 + БелАз-540, средний кусок взорванной горной массы в забое dср.=300 мм, энергопоглощение 91121 Дж/кг;
2 – СБШ-200 + ЭКГ-4,6 + мобильная дробилка + конвейер, средний кусок взорванной горной массы в забое dср.=300 мм, после дробилки dср= 200 мм, энергопоглощение 1266 Дж/кг;
– Бурозарядный комбайн + Роторный погрузчик (или ЭКГ-4,6) + конвейер, средний кусок взорванной горной массы в забое dср.= 200 мм, энергопоглощение 1167 Дж/кг показывает наиболее эффективным третий вариант.
Он помимо меньших затрат позволяет использовать в карьере поточность производства и исключить стадию крупного дробления на обогатительной фабрике, что повышает эффективность добычи апатита на карьере и производство апатитового концентрата на обогатительной фабрике.
(Необходимые данные по свойствам горных пород и взрывчатого вещества необходимых для расчётов приведены в приложении)
3. 2 Понятие о физическом энергопоглощении
Поскольку процесс производства на карьере со скальными породами в любом потоке и в любом случае связан с дроблением горной породы или отделением от массива блоков, подъемом на высоту и перемещением на определенное расстояние, на производство этой работы без учёта технологических требований и параметров механизации, которой выполнялся процесс, необходимо затратить энергию. Это будет физическим энергопоглощением (Эф) горной породой в процессе производства на карьере.
Физическое энергопоглощение горной массы в процессе производства работ на карьере связано только с состоянием, местом положения материала до производства работ и местом положения конечного продукта.
На карьере с крепкими породами конечный продукт технологического потока (вскрыша или полезное ископаемое) представляет собой дробленую горную массу до необходимой крупности. Перемещение от места добычи с подъёмом из карьера до места складирования (отвал или бункер готовой продукции), поэтому выражение для определения физического энергопоглощения можно представить как сумму энергопоглощений дробления массива горных пород и перемещения вместе с подъёмом из карьера:
где – предел прочности горной породы, Па;
– модуль упругости, Па;
n – степень дробления;
L – расстояние от пункта добычи до склада по горизонтали , м;
– разность уровней добычи и складирования готового продукта, м.
Отношение физического энергопоглощения к технологическому показывает степень совершенность технологии или комплекта оборудования технологического потока.
4.2 Область применения энергетического метода.
Предложенный метод не претендует на возможность точного определения затрат энергии в процессах горных работ на карьере. Он позволяет производить сравнительный анализ при выборе вида технологического потока и комплекта оборудования для него с учетом основных свойств горных пород, горной массы и конечного продукта в конкретных условиях.
При анализе конкретного комплекта на карьере расчет энергопоглощения производится непосредственно по данным практики. Для проектируемых предприятий расчет производится по данным геологической разведки.
Данный метод позволяет учитывать наиболее полно природные условия месторождения, такие, как климат, топография, обводненность и т.д. Например, низкие температурные условия, заснеженность увеличивает связность взорванной горной массы, а, следовательно, увеличивают сопротивление копанию, уменьшает пропускную способность перегрузочных и аккумулирующих емкостей в транспортных звеньях грузопотоков. В этом случае при производстве выемчно-погрузочных работ и транспорте энергопоглощение увеличивается.
Для уменьшения заснеженности или слеживаемости горной массы из-за ее повышенной влажности на обводненных горизонтах месторождения на практике уменьшают объем взрываемого блока, что увеличивает простои оборудования во время взрывных работ.
При разработке нагорных месторождений обычно рассматриваются варианты гравитационной доставки горной массы по рудоспускам или рудоскатам. При этом всегда возможно использовать попутно естественное дробление руды в гравитационных выработках, эффективность которого в технологических потоках может быть определена предложенным энергетическим методом.
В сложных топографических условиях использование энергетического метода позволяет решать задачи по определению эффективности подземных горных выработок для вскрытия рабочей зоны карьера, особенно для месторождений с суровыми климатическими условиями, где рудная масса при перемещении в открытых горных выработках смерзается, вызывая дополнительные затраты на ее рыхление в процессе перемещения и переработки.
Особое значение имеет использование энергетического метода при выборе технологических потоков, где горная масса подвергается многократному дроблению. В этом случае в зависимости от применяемых технических средств, занятых на выемке, перемещении и укладки в отвал или переработке, полускальные и скальные горные породы подвергаются различной степени дробления.
С точки зрения затрат энергии, дробление вскрышных пород целесообразно до той степени, при которой обеспечивается максимальная производительность машин в технологическом потоке.
Однако вследствие того, что производство вскрышных работ может выполняться различным комплектом оборудования, степень дробления в каждом конкретном случаи будет различной. Например, при разработке скальных вскрышных пород комплектом с автотранспортом требуемая степень дробления меньше, чем при разработке комплектом с конвейерным транспортом. А при отделении от массива крупных каменных блоков (на мраморных или гранитных карьерах) затраты энергии на разрушение массива еще меньше.
В тоже время благодаря высокой степени совершенства механизации производительность экскавации дробленной горной массы значительно выше, чем при выемке блоками, а трудоемкость меньше.
Степень дробления массива при добыче полезного ископаемого является актуальной нерешенной проблемой. Кондиции конечного продукта горного предприятия требует в одном случае определенную кусковатость (например, при отгрузке товарного угля), а другом – горную массу, крупностью не более размера приемной щели дробилки перерабатывающего комплекса.
В ряде случаев технология получения продукта связана с сортировкой горной массы, в результате которой горная масса ниже установленной крупности является отходом производства и поэтому доставка на дробильно-сортировочный комплекс всей добываемой горной массы связана с излишней тратой энергии на перемещение отходов. В этом случае применяют дробильно-сортировочные агрегаты в забое. Однако передвижное оборудование менее долговечно, обладает меньшей надежностью, степень использования его в забое значительно отличается от степени использования однотипного оборудования на ДСФ. Это обстоятельство приводит к дополнительным затратам на единицу продукции, которые могут быть больше экономии, полученной от исключения транспортирования горной массы, идущей в процессе переработки в отходы.
Применение комбинированного транспорта связано с бункеризацией горной массы, при котором для исключения слеживаемости горной массы требуется, чтобы дробление горных пород в забое обеспечивало минимальное количество рудной мелочи.
Дозирование горной массы из емкостей (выпуск) накладывает ограничения в габаритных размерах кусков и т.п.
В тоже время полезное ископаемое, которое подвергается дроблению и измельчению на обогатительных или агломерационных фабриках, в конечном виде представляет собой помол крупностью 0,01-0,025 мм. Общие затраты энергии на дробление будут складываться из дробления массива в забое, естественного дробления в процессе погрузки в средства транспорта, перегрузок и дробления и измельчения на обогатительных фабриках. Известно, что высокая степень дробления обеспечивает возможность применения поточного транспорта. В связи с этим при проектировании технологического потока и комплекта оборудования для него закономерно встает вопрос: какая степень дробления оптимальна по процессам в различных вариантах комплектов оборудования технологического потока?