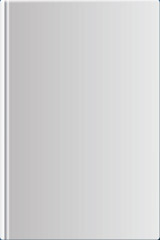
Текст книги "Метод определения энергоэффективности технологий и механизации горных работ по добыче полезных ископаемых открытым способом"
Автор книги: Юрий Анистратов
Жанр:
Технические науки
сообщить о нарушении
Текущая страница: 6 (всего у книги 8 страниц)
Поддержание расстояний автоперевозок на минимальном уровне с целью перераспределения части затрат со сборочного на магистральные виды транспорта, характеризуются высокими показателями энергетической эффективности.
Это достигается внедрением полустационарных и передвижных (мобильных) перегрузочных пунктов, крутонаклонных конвейеров, повышенных уклонов (до 60 о/оо).
Использование мобильных перегрузочных пунктов (Рис.30) расширяет возможности снижения энергопотребления за счет частичной (двух горизонтов из трёх) перевозки сборочным автотранспортом "сверху вниз", так как удельный расход при движении автосамосвалов на спуск горной массы сокращается в 1,10 – 1,75 раза по сравнению с работой на подъем, а производительность увеличивается на 15 – 40 %.
Рис.30 Мобильный перегрузочный пункт со сборочного автомобильного на крутонаклонный конвейерный транспорт
При эксплуатации автотранспорта в рабочей зоне карьеров важным направлением снижения энергопотребления является сокращение длины трассы путём эффективной технологии отработки рабочих горизонтов, выбора места расположения и использования временных наклонных берм в массиве или на насыпи.
Основными направлениями конструктивного совершенствования с целью повышения энергетической эффективности автосамосвалов на магистральных перевозках горной массы являются: электрификация автотранспорта, т.е. совершенствование дизель-троллейвозов, и применение повышенных (100 – 120о/оо) уклонов автодорог.
Эффективность дизель-троллейвозов обеспечивают следующие условия: соотношение между стоимостью дизельного топлива и электроэнергии более 4 кВт∙ч/кг, объем перевозок горной массы 8-10 млн. т/год, длина электрифицированного участка трассы 1,8-2,0 км, высота электрифицированного подъема 100-300 м.
Эффективная область применения дизель-троллейвозов характеризуется превышением фактического соотношения между стоимостью дизельного топлива и электроэнергии на конкретном предприятии над предельным. Предельное соотношение зависит от руководящего уклона и эксплуатационных показателей базового автосамосвала и троллейной системы. Фактическое соотношение составляет 10-12 кВт∙ч/кг, что свидетельствует о больших перспективах дизель-троллейвозов на глубоких карьерах. При создании отечественных дизель-троллейвозов нового поколения и увеличении руководящего уклона автодорог до 100-120о/оо коэффициент полезного использования энергии данным видом транспорта составит 7,6-7,8%, т.е. приблизится к показателям железнодорожного транспорта.
Глава 6.
Энергетический анализ развития техники и технологических процессов на карьерах
1.6 Современное состояние техники и технологии разработки месторождений полезных ископаемых.
Применение современной техники на карьерах позволило полностью механизировать добычу, применяя, как правило, разработку месторождений полезных ископаемых открытым способом уступами высотой 15—20 м, шириной заходки 18—24 м, высотой рабочей зоны 60—100 м, длиной фронта работ на горизонте при железнодорожном транспорте 3—4 км, при автомобильном – 1,5—2 км.
Угол откоса рабочего борта карьера составляет 24—28°. Вскрытие осуществляется наклонными траншеями внешнего и внутреннего заложения. Причем различий в технологии разработки полускальных и скальных пород в настоящее время практически нет. Отличаются только отдельные виды машин в комплексной механизации.
Анализ технологии с применением существующей техники, показывает, что за период развития открытого способа вместимость ковшей экскаватора увеличилась в среднем в 10 раз, рабочие параметры экскаваторов увеличились почти в 6 раз, вес и мощность примерно 8—10 раз, вместимость сосудов транспортной техники увеличилась в 5 раз.
В планах развития техники для разработки скальных горных пород эти параметры имеют тенденцию к еще большему увеличению при сохранении прежней технологии.
В настоящее время степень использования оборудования составляет 60-70 % поэтому с увеличением параметров существующих видов горнотранспортной техники при сохранении технологии ведения горных работ будут увеличиваться затраты на производство продукции горной массы.
Эти обстоятельства ставят вопрос о совершенствовании существующей технологии разработки месторождений с крепкими горными породами и главное организации горных работ для доведения степени использования мощного надёжного оборудования в технологическом потоке до 95-97 % , а также возможных перспективах развития техники и технологии на карьерах со скальными породами.
Принципы формирования комплектов оборудования для разработки скальных и полускальных горных пород на основе энергетического метода по технологическим потокам с внутренней организацией и автоматизацией в нем позволят специализировать технику, а, следовательно, снизить затраты на производство продукции.
2.6 Буровзрывная подготовка горных пород к выемке
Бурение. С энергетической позиции, как показано выше, разрушение единицы объема массива для получения горной массы требуемой степени дробления зависит от свойств массива и молекулярных связей горной породы. Дробление массы осуществляется взрывным или механическим способами.
В настоящее время взрывной способ благодаря концентрации большой энергии в единице объема взрывчатого вещества отвечает требованиям подготовки горной массы в больших объемах в единицу времени.
Преимущество взрывного дробления горных пород в массиве заключается в том, что взрыв воздействует сразу на весь массив и это позволяет использовать естественную трещиноватость для разрушения.
Механическое дробление создает напряжение только по осевой линии между контактами нагрузки. В этом случае в дроблении участвует только зона контакта. Периферийные части куска или части массива в процессе дробления в момент приложения напряжения не участвуют. Они участвуют в дроблении в следующий момент приложения нагрузки.
Эффект от взрывчатого вещества зависит от полноты его использования. При расположении обычного заряда на поверхности на дробление идёт только 5% энергии взрыва. При расположении заряда внутри взрываемого массива 7% энергии. Размещение взрывчатого вещества внутри массива связано с затратой дополнительной энергии на бурение скважин.
Но технологические требования открытого способа разработки (высота уступа, необходимость большого объема одновременно подготавливаемой горной массы и т.д.) и эффективность дробления массива взрывчатым веществом, при равномерном размещении в массиве, привели к появлению специальных средств бурения.
Возможные конструкционные параметры высоты определили оптимальный диаметр скважин 150—250 мм. История применения размещения заряда взрывчатого вещества в скважинах большого диаметра связана с постоянным присутствием негабаритов.
Интересно отметить в этой связи, что со времени появления возможности размещения заряда взрывчатого вещества в скважинах 250 мм вместимость ковшей экскаваторов увеличилась у нас в 6 раз, а процент выхода негабарита как при ковше 1,5 м3, так и 12.5 мэ, находится на уровне 1,5—3%. Это объясняется тем, что при увеличении вместимости ковша увеличивается одновременно и сетка скважин.
Существующие расчетные зависимости взрывного рыхления показывают, что с увеличением диаметра возможно увеличить сетку скважин, а следовательно, вследствие неравномерности свойств массива с рассредоточением зарядов уменьшается надежность получения необходимой степени дробления, а это в свою очередь, ведет к увеличению затрат на выемку, перемещение и переработку горной массы. В настоящее время технические сродства позволяют обеспечивать бурение скважин до 380-450 мм, поэтому необходимо менять сам принцип выбора диаметра. Он должен быть основан на свойстве заряда данного диаметра взрывчатого вещества определенного типа и обеспечивать надежное дробление объема массива в необходимой степени. Размещение зарядов с учетом размеров разрушаемых объемов определяет сетку скважин. При этом, естественно, диаметр заряда должен быть максимально возможный.
Затраты энергии на бурение пропорциональны квадрату диаметра скважин. Отсюда можно сделать вывод, что, уменьшая диаметр скважин в п раз, можно, прилагая такое же количество энергии, пробурить п2 скважин меньшего диаметра, увеличив тем равномерность размещения взрывчатого вещества и, следовательно, степень дробления.
Следовательно, с энергетических позиций уменьшение диаметра скважин позволяет уменьшать затраты как на бурение, так – через улучшение качества горной массы – на выемку, перемещение и переработку или отвалообразование.
Однако технология бурения скважин малого диаметра ставит ограничение в глубине бурения (малая жесткость штанг, затруднения удаления продуктов бурения и т.д.). Применение скважин малого диаметра требует уменьшения высоты уступа.
Экспериментальные работы и иностранный опыт показывают, что при снижении высоты уступа до 4-5 метров при хорошем качестве дробления производительность экскаватора не снижается. При автомобильном и конвейерном транспорте с консольным перегружателем заметного увеличения затрат в общем технологическом цикле от уменьшения высоты уступа не будет.
Технология разработки горизонтов при уменьшении высоты уступа потребуется иная. Горизонт, принятый в настоящее время высотой 20 м, может отрабатываться уступами (слоями) меньшей, но кратной горизонту, высоты. Эта технология отработки горизонта позволит сохранить, а в некоторых случаях (например, при увеличении высоты горизонтов до 30—50 м) и уменьшить угол рабочего борта карьера.
Уменьшение диаметра скважин высоты уступа ведет и уменьшению общего заряда, что вместе с короткозамедленным взрыванием уменьшает сейсмическое воздействие на борта карьера. Поэтому угол откоса борта карьера при погашении вследствие меньшей нарушенности может быть увеличен.
Следовательно, подготовка скальной горной массы скважинам малого диаметра перспективна. Величина его должна определяться свойствами заряда взрывчатого вещества и взрываемого массива обеспечения надежного дробления горной массы требуемого качества.
Однако в настоящее время нет буровых машин, позволяющих эффективно бурить скважины малого диаметра на карьерах.
Отсюда задача конструирования и создание высокопроизводительных буровых машин, объединенных в агрегаты для одновременного бурения серии скважин малого диаметра.
Взрывчатое вещество. С энергетических позиций вторая составляющая буровзрывного способа рыхления скального массива представляется в явном виде. Более мощное взрывчатое вещество – дороже в производстве и, вследствие дополнительных мер предосторожности, в употреблении. Принцип комплексной механизации и автоматизации требует от взрывчатого вещества сыпучести или текучести, безопасности при доставке и механическом заряжании. Учитывая вышеизложенную перспективу по буровой технике, задаче обеспечения высокой степени дробления отвечает взрывчатое вещество с большой степенью концентрации энергии в единице объема.
Малый диаметр заряда и небольшая глубина скважины позволяют, предположить целесообразность заводского изготовления готовых цилиндрических зарядов кратной глубине скважины, или шланговых (шнуровых) зарядов для механизации и автоматизации процесса заряжания
Мощное взрывчатое вещество в зарядах малого диаметра, в комплексе с механизацией заряжания, позволяет уменьшить затраты на процесс взрывного рыхления горной массы.
Целесообразность применения концентрированного взрывчатого вещества подтверждается уменьшением затрат на доставку к горному предприятию, хранение и заряжание.
3.6 Эффективность создания бурозарядных комбайнов для разработки крепких горных пород
Существующая технология на открытых горных разработках при скальных и полускальных породах базируется на разделении горных работ по процессам: подготовка горных пород к выемке (бурение скважин, заряжание, взрывание), выемка (экскавация), перемещение и складирование (отвалообразование или разгрузка в бункер).
Каждая операция в процессах выполняется отдельной машиной или механизмом. Все операции выполняются над одним объектом, поэтому выполнение их производится поочередно.
В настоящее время машины, выполняющие отдельные операции по добыванию полезного ископаемого, имеют большую мощность и в перспективе – тенденцию к ее увеличению.
При увеличении мощности машин свободная связь является причиной низкого коэффициента использования машин, а, следовательно, увеличения энергозатрат и себестоимости добычи полезного ископаемого. Чем больше мощность машин, тем больше в единицу времени потери производительности.
На карьерах с мягкими породами машины, выполняющие разные операции, объединены в один комплекс, например, транспортно-отвальный мост с многочерпаковыми экскаваторами: или роторный экскаватор с отвалообразователем или конвейерами.
В этих комплексах периодическое отделение горной массы от массива режущей кромкой ковша строго ритмично и выполняется в соответствии с установленной скоростью вращения привода. А мощность привода и его режим работы установлены в соответствии с конструктивными характеристиками рабочего органа экскаватора, физико-механическими свойствами разрабатываемой породы и объемом отделяемой породы.
Следующие за рабочим органом механизмы и машины внутренне с ними связаны и рассчитаны на работу, которую они должны выполнять с этими поступающими объемами породы по ее перемещению и погрузке.
Существующие перспективы развития технологии на карьерах со скальными породами предполагают конвейеризацию, а именно к перемещению породы ленточным или другими видами конвейеров. Но при этом сохраняется разделение процессов в производстве. Для бурения предлагаются многошпиндельные буровые станки, для погрузки —
гребково-погрузочные машины или экскаваторы с передвижными дробилками.
Однако сохранение технологии, основанной на разделенном в пространстве выполнении операций, не позволяет полностью использовать, например, погрузочную машину вследствие необходимости отгона оборудования во время взрыва, бурового станка – из-за неубранной взорванной породы в забое или необходимости заряжания скважин и т.п.
Таким образом, существующая механизация не предусматривает строгой внутренней взаимосвязи между машинами в различных процессах.
Одним из путей создания специальных средств для поточной технологии разработки полускальных и скальных горных пород является создание комбайнов, в которых машины и механизмы, выполняющие отдельные операции подготовки горных пород к выемке, объединяются общим технологическим циклом.
Конструкция комбайнов предусматривает взаимное соответствие по мощности и производительности всех рабочих узлов, выполняющих различные операции.
Обычно при рассмотрении возможности непрерывной разработки скальных пород подразумевают разрушение горных пород какими-либо новыми средствами (тепловыми, механическими и т.п.) и исключается существующий – буровзрывной.
В настоящее время буровзрывной метод хорошо освоен. Кроме того, все новые способы разрушения горных пород пока находятся на экспериментальной стадии. Поэтому в основу разрушения горных пород в комбайне может быть положен буровзрывной способ.
В настоящее время существует множество способов, позволяющих управлять взрывом, исключать разброс горной массы и разлет кусков породы на большие расстояния. Это свидетельствует о том, что при заранее рассчитанном использовании силы взрыва можно совершенно исключить стихийность разрушения горной породы взрывом, достигнуть такого положения, чтобы при взрыве был отдален от массива и раздроблен в нужной степени установленный объем горной породы.
В процессе взрывного рыхления массива энергия на разброс породы с точки зрения цели разработки породы является бесполезной. Энергия взрыва в этой части должна расходоваться только на дробление и разрыхление массива.
В цикл работы комбайна входят бурение скважин для необходимой степени дробления по установленной сетке, заряжание скважин, взрывное дробление массива, передвижка бурозарядной части на расстояние, равное расстоянию между рядами скважин. За время бурения в новом блоке взорванная порода в погрузочной части комбайна грузится на конвейер.
Малый диаметр скважин, жесткость сетки скважин позволяют предполагать устойчивое качество горной массы при разработке комбайном.
Производительность комбайна прямо пропорциональна объему отбиваемой породы за цикл и количеству циклов в единицу времени:
Количество циклов в единицу времени обратно пропорционально времени бурения скважины и времени передвижки комбайна, поэтому высота уступа в этом случае снижается до возможности снижения затрат времени на бурение без наращивания штанг.
В настоящее время разработаны два эскизных проекта: первый – комбайна (рис. 31), второй – комплекса, состоящего из буро-зарядного агрегата и погрузочной машины непрерывного действия (рис.32).
Создаваемый комбайн предназначен для поточной разработки скальных и полускальных пород, который обеспечивает полную механизацию процессов разрушения массива и погрузки.
Рис. 31. Комбайн для разработки скальных и полускальных пород на карьерах.
Рис. 32. Комплект из буро-зарядного агрегата и погрузочной машины непрерывного действия
Комбайн состоит из двух агретатов: верхнего буро-зарядного, и нижнего погрузочного. Бурение, заряжание и взрывание осуществляются агрегатом, расположенным на уступе, а погрузка – нижним агрегатом, расположенным у основания уступа.
В задачу схемы взрывания и конструкции зарядов в комбайне входят: использование энергии взрыва для погрузки, ограничение развала, силы динамического воздействия взорванной горной массы на погрузочную плиту и сейсмического воздействия на массив. В варианте комбайна требуется к тому же обеспечение контура отбойки, т.е. гладкий откол с вертикальным откосом для беспрепятственного перемещения и подведения погрузочной плиты к основанию забоя.
Бурозарядный агрегат представляет собой буровые машины, заряжающего механизма и ходовой части.
В качестве взрывчатого вещества может быть использовано льющиеся взрывчатое вещество. Однако не исключена возможность использования шланговых или стержневых зарядов с готовым внутренним рассредоточением и распределением по мощности зарядов.
Для предохранения от разлета кусков взорванной породы навешена рама с цепной защитой от разлёта кусков, расположенная над зоной взрыва.
Вариант комплекта из бурозарядного агрегата и погрузочной машины непрерывного действия отличается от комбайна только погрузочной частью и отсутствием необходимости образования гладкого откола.
Взрывание массива бурозарядным агрегатом по существу происходит под навал породы от предыдущих взрывов. Использование развала от предыдущих взрывов обеспечивает зажим, исключающий развал в направлении взрыва, а врубовая схема взрывания обеспечивает минимум развала в торцовой части.
Расчетная скорость разлета кусков при взрыве и величина развала в зависимости от величины навала неубранной породы приведены в табл. 11.
Таблица 11
Зависимость скорости разлета кусков породы и размера развала от величины неубранной породы (по В.К. Рубцову)
Величина неубранной породы в направлении взрыва, м
0
1
2
3
4
5
Скорость разлета кусков породы при взрыве, м/сек
30
15
10
7,5
6
5
Величина развала от старой бровки, м
30
13
7
3,5
1,0
нет
В комплекте может эффективно работать погрузочная машина роторного типа, одночерпаковый экскаватор, колёсный или нагребающего типа погрузчик
Погрузочные машины располагаются от бурозарядного агрегата на безопасном от разлета кусков расстоянии и производят погрузку горной массы при конвейерном транспорте на перегружатель или при автомобильном транспорте непосредственно в кузов автосамосвала.
4.6 Механическое рыхление горной породы
Механическое разрушение горной породы является результатом удара или статической нагрузки, превосходящей предел прочности горной породы при сжатии. В настоящее время применяется разрушение полускальных пород ударом клина, подающим грузом и т.п., разрушение тракторными рыхлителями.
Энергопоглощаемость материала в процессе механического рыхления существующими средствами в сравнении с буровзрывными работами (табл.12) в несколько раз меньше, а степень дробления больше.
Таблица 12
Энергопоглощаемость материала при использовании различных средствах разрушения
Средства разрушения
Энергопоглощаемость (кДж/ кг)
Количество вновь образованных плоскостей при разрушении
Откол клином
0,60
4—10
Ударом зубьев
10,9
20
Разрушение рыхлителем
7, 2
80—200
Разрушение падающим снарядом (шар)
2,2
200—500
Буровзрывной способ
11,2
100
Это дает основание предполагать, что механическое рыхление при увеличении мощности машины, занятой в процессе, позволит удовлетворить подготовку горных пород к выемке технологического потока большой производительности,
Механическое рыхление в отличие от взрывного вследствие постоянного зазора между зубьями рыхлителя, шага дробления клином или разрушение резцами позволяет получать устойчивый состав горной массы по крупности, а регулирование зазора или шага позволяет менять степень дробления горной массы.
Это преимущество позволяет применять механическое рыхление в поточных комплектах оборудования технологических потоков как при существующем оборудовании, так при создании специального.
При использовании комплекта оборудования технологического потока из существующего оборудования энергопоглощение происходит: при разрушении горных пород рыхлителем (на известняках σ = 480 ∙10 5 Па, Е =1,02 ∙10 10 Па,) Эа = 6,64– 104 Дж/кг; штабелировании разрушенной горной массы бульдозером Эш = 260 Дж/кг; погрузки машиной непрерывного действия Ээ = 6,5 Дж/кг; конвейерного транспорта Эт = 4,45 Дж/кг и переработки Эп = Дж/кг). В целом энергопоглощение при данной технологии составляет: Эо = 10,8×104 Дж/кг
Рассматривая подобные комплекты, необходимо отметить, что даже при одинаковой себестоимости с буровзрывным способом рыхления и колесным транспортом, технологическим потокам с механическим рыхлением и непрерывным транспортом следует отдавать предпочтение вследствие меньшей энергоемкости и трудоемкости производства горных работ.
5.6 Термическое и электротермическое разрушение горных пород
В последнее время практического значения достигли созданные методы и аппаратура для термического, электротермического и термомеханического разрушения горных пород при воздействии с поверхности массива и с заглублением рабочего поля.
Аппараты электротермического разрушения эффективны в поточных комплектах оборудования технологических потоков, однако, производительность пока невелика.
6.6 Резание полускальных пород
Совмещение операций отделения горных пород от массива с погрузкой уменьшает энергопоглощение, поэтому направление на создание роторных и фрезерных машин с повышенными усилиями резания является перспективным. В настоящее время усилие резания роторными экскаваторами составляет kг=14÷16 кг/см, что соответствует разработке пород крепостью f = 1,5. При этом производительность экскаватора достигает 4500 м3/час.
Достигнуто усилие резания 30 кг/см, которое позволяет разрабатывать аргиллиты, алевролиты, слабосцементированные песчаники и крепкие угли, т.е. породы крепостью f =3.
По аналогии с буровыми машинами вращательного бурения со специальными резцами можно высказать предположение, что в настоящее время возможно создание рабочих органов машин и для разработки полускальных пород крепостью до f = 14.
Для этого необходимо обеспечение давления до 2,5 т при скорости резания не более 720 м/час. В этом случае будет удовлетворительная стойкость резцов и твердого сплава. Указанное давление на открытых горных работах создать не трудно,
Учитывая, что отделение от массива резанием совмещается с погрузкой, состав горной массы по крупности будет однороден, горная масса может транспортироваться поточным транспортом и, исключая процесс дробления и измельчения, может быть сразу направлена на помол для обогащения, данный способ разрушения целесообразен для добычи руды (Рис.33)
Рис.33. Технически возможные и целесообразные границы использования способов разрушения массива
Эти границы целесообразны при условии рассмотрения всего комплекта оборудования технологического потока по производству горных работ и переработке полезного ископаемого, но они условны. При рассмотрении конкретных месторождений на основе энергетического метода, включая свойства горных пород, природные условия месторождения, кондиции конечного продукта и технологию самого энергоемкого процесса – переработки, эти границы могут быть передвинуты.
Однако это дает представление о направлении научных исследований и конструировании новых машин, связанных с разрушением массива о целесообразных границах их применения.
Принято, что при взрывной, буровзрывной и буроэлектротермической подготовке пород к выемке разрушение горной породы происходит в большей части от растяжения, в механическом разрушении ударом – в разной степени от сжатия и растяжения, в остальных разрушение принято в результате сжимающих нагрузок.
Учитывая цены на взрывчатое вещество и электроэнергию, даже при низком коэффициенте полезного использования электрической энергии при механическом дроблении (например в щековых дробилках) затраты на дробление почти в два раза ниже, чем при дроблении взрывом.
Это обстоятельство, вместе с преимуществом электроэнергии, в канализации месту потребления, возможности управления и автоматизацией процесса делает перспективными все комплекты оборудования для скальных пород с электротермическими и механическими способами подготовки горных пород к выемке, а для полускальных пород – резанием и механическим рыхлением агрегатами с электроприводом.
7.6 Выемка и погрузка
Выемочно-погрузочная техника на карьерах с полускальными и скальными породами в настоящее время представлена одноковшовыми экскаваторами, отличающимися друг от друга емкостью ковша, а следовательно, габаритами и мощностью. Принцип работы этих машин повторяет землекопа, т.е. повторение операций зачерпывания, подъем ковша, перемещение к транспортному сосуду, разгрузка и возвращение в забой.
Данный принцип целесообразен в случае, если операция перемещения имеет самостоятельное значение, как, например, во вскрышных мехлопатах. Специфика работы погрузочной машины в забое, от которой горная масса перемещается транспортными средствами, заключается в захвате горной массы и погрузке в транспортный сосуд причём эта функция постоянна и однообразна. Принцип работы применяющийся машины, у которой рабочая операция захвата горной массы и разгрузка занимают 33—35%, а остальное время затрачивается на подготовительные и вспомогательные операции, не соответствует специфике работ на карьере.
В расчете существующих карьерных машин мощность источников энергии и конструктивная прочность компоновки агрегатов рассчитываются для условий момента зачерпывания, точнее, внедрения ковша в забой. При этом обычно рассматриваются самые сложные условия сопротивление внедрению при плохо взорванной горной массе. Во время других операций мощность источника энергии и его конкретный вес не принимают участия. Следовательно, принцип работы машины, выполняющей строго определенную однообразную работу, не отвечает принципу рационального использования энергии.
Для разработки плотных и полускальных пород и особенно угля и руды используются комбайны, обеспечивающие по принципу действия одновременную непрерывную выемку и погрузку горной массы. Они эффективно работают в породах с прочностью на одноосное сжатие до 180200 МПа. В этих породах вследствие поточности производства и отсутствия буровзрывной подготовки горной массы затраты на разработку почти в 2 раза ниже. В настоящее время они успешно используются для добычи строительных материалов, угля, фосфоритов, бокситов, гипса.
Современные комбайны различаются принципом действия, конструкцией и расположением рабочего органа.
К первой группе относятся комбайны с рабочим органом в виде цилиндрической фрезы, расположенной в центре в нижней части опорной рамы между передними и задними гусеницами. Фреза представляет собой барабан, оснащенный штыревыми зубками, расположенными по винтовой линии и армированными вставками из твердого сплава. Вращение фрезы может осуществляться как в направлении движения комбайна, так и против (рис.34).
Рис.34 Принцип работы фрезерного комбайна.
Число зубков, их тип, расстояние между ними зависит от физико-механических свойств горных пород, необходимого состава горной массы по крупности и устанавливается применительно к конкретным природным условиям месторождения. Разрушенная горная порода со средним размером куска до 300 мм конвейером загружается в транспортные средствa или в штабель вдоль полосы выемки, из которого горная масса погрузчиком или экскаватором загружается в транспорт.
Наиболее известные комбайны этого типа выпускает немецкая фирма «Виртген». Используя опыт изготовления дорожных машин для фрезерования старых дорожных покрытий из бетона и асфальта, они создали ряд комбайнов для карьеров с шириной фрезы 1900 4200 мм, глубиной фрезерования за одни проход от 150 до 600 мм и теоретической производительностью до 1700 т/ч.
Фрезерные комбайны с передним креплением рабочего органа позволяют разрабатывать массив горных пород уступами высотой 1,8 2.5 м, шириной захвата 77,6 м н производительностью 5502100 т/ч .
Переднее расположение рабочего органа позволяет производить разработку горизонтов обычной технологией – уступами, как и ковшовой техникой, Работа с конвейерным транспортом обеспечивает поточную технологию разработки горных пород средней крепости.
Стреловые комбайны с фрезерным рабочим органом позволяют производить разработку массива горных пород забоями аналогично ковшовым экскаваторам. Отделенная рабочим органом от массива порода попадает на погрузочную плиту, с которой загружающими устройствами подается на конвейер.
Фрезерный стреловой комбайн ТВ-3000 английской фирмы «Доско» является наиболее крупным стреловым комбайном в мире. Он способен разрабатывать полускальные и скальные горные породы с пределом прочности на сжатие 160180 МПа производительностью до 690 т/ч, уступами высотой 5 м, с шириной захвата 9 м, обеспечивая кусковатость горной массы 0600 мм. Рабочие органы в виде продольных режущих головок расположены на двух стрелах. Привод головок, вращающихся навстречу друг другу, индивидуальный от электродвигателей. Привод стрел гидравлический, который обеспечивает независимое или синхронное движение (Рис.35).
Рис.35 Двухстреловой фрезерный комбайн.