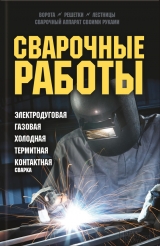
Текст книги "Сварочные работы. Электродуговая. Газовая. Холодная. Термитная. Контактная сварка"
Автор книги: Юрий Подольский
Жанры:
Технические науки
,сообщить о нарушении
Текущая страница: 9 (всего у книги 25 страниц) [доступный отрывок для чтения: 10 страниц]
Рукава I и II классов имеют четырехкратный, а III класса – трехкратный запас прочности по отношению к рабочему давлению.
Рукава изготавливают с внутренним диаметром, равным 6,3; 8; 9; 10; 12; 12,5 и 16 мм. Рукава длиной 10 и 20 м поставляют в виде бухт. Оптимальная длина рукава 9—30 м. При ее увеличении возрастают потери давления газа.
Правила безопасной работы с рукавами
До сварки:
– при укладке рукавов их нельзя сплющивать, скручивать и перегибать;
– кислородные рукава удлиняют с помощью латунных, а ацетиленовые – стальных ниппелей, закрепляемых снаружи хомутами;
– для защиты рукавов от механического воздействия при прокладке их через дорогу следует прикрывать их уголком или швеллером;
– рукава крепят к ниппелям хомутами или мягкой отожженной проволокой (в двух местах на одном ниппеле);
– на ниппели водяных затворов рукава должны плотно надеваться и оставаться незакрепленными.
Во время сварки:
– защищают рукава от нагрева солнечной радиацией и тепловым потоком, поступающим от свариваемого изделия;
– следят за тем, чтобы вещества, разрушающие резину, не соприкасались с рукавами или случайно не попадали на них;
– при перемещении рукавов избегают резких рывков;
– в случае возгорания рукава необходимо быстро перегнуть его возле горящего места со стороны редуктора или газогенератора и закрыть вентиль баллона.
После сварки:
– очистить рукава от остатков грязи, свернуть в бухту и разместить на хранение в сухом помещении при температуре 0—25 °C.
Запрещается:
– держать рукава в натянутом состоянии;
– наматывать их на руку, держать между ног, на плечах, обматывать вокруг пояса;
– допускать попадание на рукава искр, брызг металла и воздействие высоких температур;
– пользоваться дефектными или замасленными рукавами;
– использовать гладкие патрубки и обрезки труб для соединения рукавов;
– применять более двух соединений на одном рукаве;
– соединять рукава длиной менее 3 м;
– прокладывать рукава по лужам масла, грязи, химически активных отходов;
– ремонтировать рукава с применением изоляционных лент, лейкопластыря и других подобных материалов;
– использовать рукава, по которым подавались ацетилен и горючие жидкости, для транспортирования кислорода, и наоборот;
– хранить рукава в помещениях при высокой температуре.
Сварочные горелки
Основным инструментом газосварщика является сварочная горелка – устройство для смешения газов, формирования сварочного пламени и регулирования его вида и мощности. Сварочные горелки, в соответствии с ГОСТ 1077-79, классифицируют по следующим признакам:
– способу подачи горючего газа и кислорода в смесительную камеру – инжекторные и безынжекторные;
– роду горючего газа – ацетиленовые, водородные, для газов-заменителей и жидких горючих;
– числу факелов – однопламенные и многопламенные;
– назначению – универсальные (сварка, резка, пайка, наплавка) и специализированные для выполнения одной операции;
– мощности пламени – горелки микромощности (расход ацетилена 5—60 дм3/ч), малой (60—700 дм3/ч), средней (700—2500 дм3/ч) и высокой (2500–7000 дм3/ч) мощности;
– способу применения – ручные, машинные.
В безынжекторных горелках горючий газ и кислород поступают в смеситель под одинаковым давлением. Инжекторные горелки имеют устройство, обеспечивающее подачу горючего газа низкого давления в смесительную камеру за счет всасывания его струей кислорода, подводимого под более высоким давлением. Это устройство называется инжектором, а явление подсоса – инжекцией. Наиболее эффективны инжекторные горелки, отличающиеся высокой безопасностью, простотой обслуживания, надежностью работы и универсальностью.
На рис. 31, а – в представлены схема инжекторной горелки и конструкция инжекторного устройства. Кислород из баллона под рабочим давлением через ниппель, газоподводящую трубку и вентиль поступает в сопло инжектора. Выходя из сопла с большой скоростью, он создает разряжение в ацетиленовом канале, в результате чего ацетилен, проходя через ниппель, трубку и вентиль, подсасывается в смесительную камеру. В этой камере образуется горючая смесь, которая, проходя через наконечник и мундштук, сгорает на выходе из горелки, образуя сварочное пламя.
Для нормальной работы инжекторных горелок необходимо, чтобы давление кислорода составляло 150–500 кПа (1,5–5,0 кгс/см2), а давление ацетилена – 3—120 кПа (0,03—1,2 кгс/см2). Устойчивое горение пламени достигается при скорости истечения горючей смеси 50—170 м/с.
На рис. 31, д представлена схема безынжекторной горелки. Вместо инжектора у нее – смесительная камера наконечника. При подключении безынжекторной горелки к газовым баллонам применяют редуктор, который автоматически поддерживает равенство рабочих давлений кислорода и ацетилена (рис. 31, г).

Рис. 31. Горелки:
а – общий вид инжекторной горелки; б – в – конструкция горелки и инжектора (1 – мундштук; 2 – наконечник; 3 – смесительная камера; 4 – сопло инжектора; 5, 7 – вентили кислорода и ацетилена; 6 – ниппели; 8, 9 – каналы для подачи кислорода и ацетилена; 10 – инжектор); г – схема подключения безынжекторной горелки к газовым баллонам; д – конструкция безынжекторной горелки (1 – мундштук; 2 – наконечник; 3, 6 – вентили кислорода и ацетилена; 4, 5 – ниппели кислорода и ацетилена; 7, 8 – баллонные редукторы; 9 – редуктор равных давлений; 10 – рукава; 11 – горелка; 12 – предохранительные устройства); е – инжекторный резак (1 – вентиль режущей струи кислорода; 2 – трубка подачи кислорода к мундштуку; 3 – подогревающее пламя; 4 – режущая струя кислорода)
Кислород через ниппель, регулировочный вентиль и специальные дозирующие каналы поступает в смесительную камеру горелки. Аналогично через ниппель и вентиль подается ацетилен. Из смесительной камеры горючая смесь проходит через наконечник и выходит из мундштука, образуя сварочное пламя.
Мощность пламени выбирают в зависимости от толщины свариваемого металла и его теплофизических свойств. Регулируют пламя подбором наконечника горелки. Правила выбора сварочной горелки и наконечников к ней приведены в табл. 22 и 23.
Правила безопасной работы с газовыми горелками
До сварки:
– после осмотра горелки устанавливают наконечник того номера, который соответствует толщине свариваемого металла;
– проверяют надежность резьбовых соединений и при необходимости подтягивают накидные гайки наконечника и ниппелей рукавов;
– проверяют герметичность сальников вентилей и при необходимости подтягивают сальниковую гайку;
– проверяют наличие разрежения (подсоса) во входном ацетиленовом ниппеле при пуске кислорода. Для этого нужно присоединить кислородный шланг к ниппелю и установить давление кислорода по манометру редуктора (например, для наконечника № 4 давление выставляют 200–400 кПа). Затем полностью открыть вентиль ацетилена, а затем кислорода и убедиться в наличии разрежения, поднеся большой палец к ниппелю ацетилена (палец должен присасываться). При слабом разрежении должна быть проверена величина зазора между концом инжектора и входом в смесительную камеру. В случае необходимости нужно вывернуть инжектор на 1/2—1 оборота из смесительной камеры;
– если разрежение отсутствует (нет подсоса), следует проверить, не засорено ли отверстие инжектора или мундштука, плотно ли прижат инжектор к седлу горелки.
Вовремя сварки:
– устанавливают необходимые рабочие давления на редукторах: 100 кПа (1 кгс/см2) – на ацетиленовом, 400–500 кПа (4–5 кгс/см2) – на кислородном;
– для создания разрежения в канале горючего газа на четверть оборота открывают кислородный вентиль горелки;
– открывают вентиль горючего газа на 1 оборот и поджигают горючую смесь, истекающую из мундштука;
– с помощью вентилей горелки регулируют мощность и состав пламени в зависимости от марки свариваемого металла и его толщины;
– при хлопках следует перекрыть ацетиленовый, а затем кислородный вентили горелки;
– в случае интенсивного нагрева мундштука горелки необходимо погасить пламя и охладить горелку в воде.
После сварки:
– перекрывают вентили горелки: сначала вентиль горючего газа, а затем кислорода;
– вывертывают нажимные регулировочные винты редукторов;
– открывают вентили на горелке и выпускают остатки газов, находящихся в рукавах;
– проверяют состояние мундштуков и при необходимости очищают их наружную поверхность от брызг расплавленного металла протиркой о пластину свинца или брусок дерева;
– шестигранной иглой из латуни или другого металла, более мягкого, чем медь, прочищают внутренний канал мундштука;
– при чрезмерной разработке и обгорании мундштука его следует заменить.
Запрещается:
– проводить газосварочные работы при разгерметизации соединений;
– перемещаться с зажженной горелкой вне места сварки, подниматься по трапам, лесам, переходить с этажа на этаж;
– продолжать работу после обратного удара пламени или выявления неисправности аппаратуры;
– оставлять без присмотра горелку с открытыми вентилями или зажженным пламенем;
– проводить сварку при отсутствии на рабочем месте ведра с чистой водой;
– выполнять газосварочные работы в помещении без вентиляции.
Предохранительные устройства
При работе с газовым оборудованием серьезную опасность представляет возможность попадания в него взрывной волны при обратных ударах пламени из сварочной горелки или резака. Обратным ударом называется воспламенение смеси газов в каналах горелки или резака и распространение пламени навстречу потоку горючей смеси. Дело в том, что горючая смесь сгорает с определенной скоростью. Из отверстия мундштука горелки или резака она вытекает также с определенной скоростью, которая должна быть больше скорости сгорания. В противном случае пламя проникнет в канал мундштука и воспламенит смесь в каналах горелки или резака, что вызовет обратный удар пламени. Обратный удар может произойти также от перегрева и засорения канала мундштука горелки.
Обратный удар характеризуется резким хлопком и гашением пламени. Горящая смесь газов устремляется по ацетиленовому каналу горелки или резака в шланг, а при отсутствии предохранительного затвора – в источник горючего газа, что может привести к его взрыву и вызвать серьезные разрушения и травмы.
Безопасность работ при газовой сварке обеспечивает группа предохранительных устройств, устанавливаемых между баллоном и горелкой (рис. 31, г, поз. 12). К ним относятся обратный клапан, пламегаситель, предохранительный и отсечный клапаны.
Обратный клапан – предохранительное устройство, предотвращающее обратный ток газа. Его устанавливают на редуктор. Клапан открывается под действием газовой струи, а закрывается под действием пружины, когда давление газа на выходе из клапана превышает давление при нормальном потоке газа.
Обратный клапан, срабатывающий при определенном давлении, присоединяют к горелке для предотвращения обратного тока газа и снижения вероятности обратного удара пламени, когда давление газа на выходе превышает нормальное.
Пламегаситель подключают к горелке. Это предохранительное устройство, предотвращающее прохождение в защищаемое оборудование, аппаратуру и коммуникации пламени при его обратном ударе. Пламегасители подразделяют на два класса: класс I (тяжелый тип) и класс II (легкий тип). В зависимости от конструкции различают пламегасители одно– и двустороннего действия.
Предохранительный клапан – устройство, автоматически сбрасывающее газ в атмосферу при превышении заданного уровня давления и прекращающее истечение газа при снижении давления до этого уровня.
Предохранительные затворы бывают водяные и сухие. Первые предназначены для защиты ацетиленовых генераторов и трубопроводов для горючих газов от проникновения в них пламени при обратном ударе, а также кислорода из горелки или резака и воздуха из атмосферы. Для работы с баллонными редукторами применяют сухие затворы. Это комбинированные предохранительные устройства на основе пористой вставки из металлокерамики в сборе с обратными клапанами.
Отсечный клапан – предохранительное устройство, прекращающее подачу газа при критическом значении температуры, наличии противодавления на выходе из клапана либо превышении заданного значения расхода газа.
Техника выполнения сварных швовПодготовка кромок
Вид подготовки кромок зависит от толщины свариваемых деталей. При толщине листового металла 0,5–2 мм подготовка сводится к торцеванию или отбортовке кромок. Сварку осуществляют встык без присадочного материала – только за счет расплавления кромок.
При толщине 1–5 мм отторцованные без скоса кромки собирают с зазором 0,5–2 мм и сварку проводят с использованием присадки. При толщине металла 4–8 мм можно проводить сварку без скоса кромок, но при этом зазор увеличивается до 1–2 мм и шов должен быть двусторонним.
При толщине металла 5—10 мм выполняют V-образную разделку кромок (70–90°). Зазор под заполнение присадочным материалом составляет от 2 до 4 мм, притупление кромок 1,5–3 мм.
Для металла толщиной свыше 10 мм применяют двустороннюю (Х-образную) разделку со скосом кромок под углом 35–45°. Зазор может быть в пределах 2–4 мм, таким же по величине делают и притупление.
Перед сборкой область шириной 20–30 мм, расположенная вблизи свариваемых кромок, должна быть очищена от ржавчины, грязи, краски и окалины.
При выполнении угловых швов зазор между кромками свариваемых деталей устанавливается 1–2 мм. При толщине свариваемого металла более 5–6 мм производится одно– или двусторонний скос кромок под углом 50–60°.
Способы и техника сваркиОсновными параметрами газовой сварки являются вид и мощность пламени, диаметр присадочной проволоки и скорость сварки.
Вид пламени зависит от свариваемого материала: нормальным пламенем сваривают углеродистые и легированные стали, науглероживающим – чугун, окислительным – латуни. Выбор нужного вида пламени осуществляется по характеру его свечения.
Для выполнения сварочных работ необходимо, чтобы сварочное пламя обладало достаточной мощностью, которая определяется количеством ацетилена, проходящего за 1 ч через горелку, и регулируется наконечниками горелки. Мощность пламени горелки, выбираемая в соответствии с толщиной свариваемого металла и его теплофизическими свойствами, определяется расходом ацетилена, необходимым для его расплавления. Чем толще свариваемый металл и выше его теплопроводность (как, например, у меди и ее сплавов), тем выше должна быть мощность пламени. Ее регулируют ступенчато – подбором наконечника горелки и плавно – вентилями на горелке.
Для сварки низкоуглеродистой стали на 1 мм толщины свариваемого металла требуется 100–130 дм3 ацетилена в час. При сварке низкоуглеродистой стали толщиной 3 мм минимальная мощность сварочной горелки составит 100 ∙ 3 = 300 дм3/ч, максимальная – 130 ∙ 3 = 390 дм3/ч.
Диаметр присадочной проволоки (dп) выбирают в зависимости от толщины свариваемого металла (S) и способа сварки. При сварке низко– и среднеуглеродистых сталей левым способом (мм). При сварке правым способом
(мм).
Скорость сварки сварщик устанавливает в соответствии со скоростью плавления кромок детали. Этот параметр непосредственно зависит от мастерства сварщика.
При газовой сварке составными элементами техники сварки являются:
– угол наклона мундштука горелки к поверхности свариваемых кромок;
– способ сварки;
– манипуляции мундштуком горелки и присадочной проволокой при движении пламени вдоль шва.
Скорость плавления (и, соответственно, скорость сварки) регулируют путем изменения угла наклона мундштука к поверхности свариваемого металла (рис. 32). Угол выбирают в зависимости от толщины и рода свариваемого металла. Чем толще металл и выше его теплопроводность, тем больше угол наклона мундштука горелки к поверхности свариваемого металла. Так, при сварке меди угол должен быть большим, чем для углеродистых сталей. В начале сварки для лучшего прогрева металла угол наклона устанавливают около 90°, затем по мере прогрева свариваемого металла снижают до величины, соответствующей толщине металла, а в конце сварки постепенно уменьшают, чтобы лучше заполнить кратер и предотвратить пережог металла.

Рис. 32. Угол наклона мундштука горелки в зависимости от толщины металла
Способы сварки проиллюстрированы на рис. 33, а – б. Сварочную горелку держат в правой руке, а в левой – присадочную проволоку. Пламя горелки направляют на металл так, чтобы свариваемые кромки находились в восстановительной зоне на расстоянии 2–6 мм от конца ядра. Сварочную проволоку располагают под углом около 45° в сторону, противоположную наклону мундштука горелки. Конец присадочной проволоки должен находиться в восстановительной зоне или в сварочной ванне.
Рукоятка горелки может располагаться вдоль оси шва или перпендикулярно к ней. То или иное положение выбирается в зависимости от условий и удобства работы газосварщика: его руку не должен обжигать нагретый металл.
Горелка в руке сварщика может перемещаться в двух направлениях:
– справа налево, когда пламя направлено на холодные, еще не сваренные кромки металла, а присадочная проволока подается впереди пламени. Такой способ получил название левого и применяется при сварке тонкостенных (толщиной до 3 мм) конструкций и легкоплавких металлов и сплавов;
– слева направо, когда пламя направлено на сваренный участок шва, а присадочная проволока подается вслед за пламенем. Такой способ называется правым и используется для сварки конструкций с толщиной стенки свыше 3 мм и металлов с большой теплопроводностью. Качество шва при правом способе сварки выше, чем при левом, так как металл лучше защищен пламенем горелки от воздействия воздуха.
В процессе сварки конец мундштука горелки совершает одновременно два движения: поперечное – перпендикулярно к оси шва и продольное – вдоль оси шва. Основным является продольное движение, поперечное служит для равномерного прогрева кромок основного и присадочного металла и получения шва необходимой ширины.
Присадочной проволокой можно совершать такие же колебательные движения, но в направлениях, противоположных движениям конца мундштука горелки. Конец присадочной проволоки не рекомендуется извлекать из сварочной ванны и особенно из восстановительной зоны пламени.
Вид движений, совершаемых мундштуком и проволокой, зависит от положения шва в пространстве, толщины свариваемого металла, рода металла и требуемых размеров сварочного шва (рис. 33, в). Так, для сварки швов в нижнем положении наиболее распространено движение полумесяцем; при сварке металла средней толщины – по спирали; при толщине металла более 8 мм – зизгагообразное. При сварке угловых швов пламя и конец присадочной проволоки перемещают с большей задержкой по краям шва. Тонкий металл сваривают прямолинейным движением без поперечных колебаний горелки.

Рис. 33. Техника сварки:
а – левый способ; б – правый способ (сплошной линией показано движение горелки; пунктирной – движение присадочной проволоки; стрелками указано направление сварки); в – манипуляции мундштуком горелки при сварке: I – восьмеркой; II – по спирали; III – полумесяцем; IV – прямолинейно
Сварка в различных пространственных положениях
Сварка в нижнем положении. Нижние швы выполнять наиболее легко, так как расплавленный присадочный металл не вытекает из сварочной ванны. Кроме того, за сваркой такого шва удобно наблюдать.
В расплавленную ванну вводят конец проволоки и расплавляют небольшое ее количество, после чего перемещают в восстановительную зону пламени. Мундштуком совершают круговые движения и перемещают его для образования новой ванночки, которая должна перекрывать предыдущую на 1/3 диаметра. После расплавления новой ванны в нее погружают конец проволоки и повторяют процедуру.
Нижние швы выполняют как левым, так и правым способом в зависимости от толщины свариваемого металла. Тонкие пластины с отбортовкой кромок сваривают левым способом. Шов формируют без присадочного материала, за счет расплавления основного металла (рис. 34, а).
Сварка нахлесточных швов. Шов накладывают левым способом с присадочным материалом (рис. 34, б). При вынужденных перерывах в работе перед возобновлением процесса сварки нужно переплавить закристаллизовавшийся в кратере металл. Вообще, для получения нахлесточных швов рациональнее использовать дуговую сварку, а газовая применяется только при крайней необходимости (за исключением сварки свинца) из-за коробления соединяемых листов.
Сварка в вертикальном положении. Вертикальные швы при малой толщине металла сваривают сверху вниз правым способом (рис. 34, в) и снизу вверх правым или левым способом (рис. 34, г – д). Сварка тонколистового металла толщиной не более 4–5 мм производится снизу вверх левым способом. Горелку перемещают таким способом, чтобы не дать стечь расплавленному металлу, и давлением газов пламени поддерживают в зазоре ванночку металла. Сварка сверху вниз правым способом требует большой сноровки – металл удерживают от стекания концом присадочной проволоки, погруженной в ванну.
При сварке металла толщиной от 2 до 20 мм вертикальные швы целесообразно выполнять способом двойного валика (рис. 34, е). В этом случае скоса кромок не делают и свариваемые детали устанавливают с зазором, равным половине толщины свариваемого металла. Процесс ведется снизу вверх.

Рис. 34. Выполнение сварочных швов в разных пространственных положениях:
а – нижнем для тонкого металла с отбортовкой кромок; б – нахлесточных; в – вертикальных сверху вниз правым способом; г, д – вертикальных снизу вверх левым и правым способами; е – вертикальных двойным валиком; ж – горизонтальных; з, и – потолочных левым и правым способами
При толщине металла более 6 мм сварку таким способом выполняют два сварщика одновременно с противоположных сторон. В нижней части стыка проплавляется сквозное отверстие. Пламя, постепенно поднимаясь снизу вверх, оплавляет верхнюю часть отверстия. Шов формируется на всю толщину, а усиление получается с обеих сторон стыка. Затем перемещают пламя выше, оплавляя верхнюю кромку отверстия и накладывая следующий слой металла на нижнюю сторону отверстия. Процесс продолжают до полного получения шва.
Горизонтальные швы на вертикальной плоскости, при сварке которых металл может стекать на нижнюю кромку, выполняют правым способом, держа конец проволоки сверху, а мундштук горелки снизу ванны (рис. 34, ж). Сварочная ванна располагается под небольшим углом к оси шва, что облегчает формирование шва и предотвращает стекание жидкого металла.
Сварка в потолочном положении. Наибольшие трудности возникают при сварке потолочных швов. Кромки нагревают до начала оплавления и в этот момент в сварочную ванну вводят присадочную проволоку, конец которой быстро оплавляется (рис. 34, з, и). Металл сварочной ванны удерживается от стекания вниз давлением газов пламени. Сварку лучше вести правым способом и выполнять в несколько слоев с минимальной толщиной каждого слоя. Присадочный пруток следует держать полого во избежание стекания по нему жидкого металла.