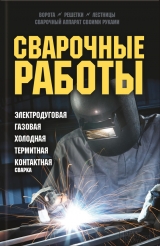
Текст книги "Сварочные работы. Электродуговая. Газовая. Холодная. Термитная. Контактная сварка"
Автор книги: Юрий Подольский
Жанры:
Технические науки
,сообщить о нарушении
Текущая страница: 1 (всего у книги 25 страниц) [доступный отрывок для чтения: 10 страниц]

Сварочные работы. Электродуговая. Газовая. Холодная. Термитная. Контактная сварка
Составитель Юрий Подольский
Введение

Сварка является одним из ведущих технологических процессов изготовления, упрочнения и ремонта строительных конструкций, трубопроводов, машин и механизмов, транспортных средств и прочих промышленных и бытовых изделий. Использование технологических приемов сварки очень эффективно и при резке металлов. Исторически сварка известна человечеству со времен использования меди, серебра, золота и особенно железа, при получении которого выполняли проковку, т. е. сваривание криц (кусочков технически чистого железа). Это и есть первый (и до недавнего времени основной) способ сварки – кузнечная сварка металла.
Газовая сварка появилась в конце XIX века после разработки промышленного способа производства карбида кальция путем спекания кокса с негашеной известью (1893–1895). Из карбида легко получается горючий газ – ацетилен, который и применяется при газовой сварке. Первые газовые горелки появились в 1900 г., а с 1906 г. ацетиленокислородная сварка получила промышленное применение. До 1950 г. газосварка называлась автогенной – по названию процесса автоматической генерации, т. е. получения ацетилена из карбида кальция при взаимодействии с водой в газогенераторе. До настоящего времени она применяется весьма широко как в производстве, так и при ремонте металлоизделий, а в ряде случаев является и единственно возможным способом сварки.
Наиболее же распространена в производстве и в быту электродуговая сварка – отечественное, кстати, изобретение. Впервые электрический дуговой разряд был выявлен профессором физики Петербургской медико-хирургической академии Василием Владимировичем Петровым в 1802 г. Через 80 лет (в 1882 г.) российский инженер Николай Николаевич Бенардос, работая со свинцовыми аккумуляторными батареями, открыл способ сварки неплавящим угольным электродом. Он же освоил технологию сварки свинцовых пластин, разработал способы сварки металла в среде защитного газа и электродуговой резки металла. Бенардос назвал свое изобретение «Электрогефест». В греческой мифологии бог Гефест – покровитель кузнецов, и этим названием ученый объединил наследие античных мастеров кузнечной сварки с новейшими технологическими достижениями и открытиями.
В 1888 г. другой российский инженер Николай Гаврилович Славянов разработал способ сварки плавящим электродом. Дальнейшую работу по разработке сварочных методик Славянов и Бенардос выполняли вместе. С 1890 по 1892 г. по их технологии в Российской империи было отремонтировано с высоким качеством 1631 изделие общим весом свыше 17 тыс. пудов, в основном чугунные и бронзовые детали. Они даже разработали проект ремонта Царь-колокола, но «благодаря» высочайшему запрету это чудо литейного искусства так ни разу и не зазвонило. Известный мостостроитель академик Евгений Оскарович Патон, предвидя огромную роль электросварки в мостостроении и в других отраслях хозяйства, в 1929 г. резко сменил поле своей научной деятельности и организовал в Киеве сначала лабораторию, а позднее первый в мире институт электросварки. Им было разработано и предложено много новых и эффективных технологических процессов электросварки. В годы войны под его руководством были разработаны технология и автоматические стенды для сварки под слоем флюса башен и корпусов танков, самоходных орудий, авиабомб.
В настоящее время широкое развитие получили такие способы сварки, как плазменная и электронно-лучевая, контактная и электрошлаковая, сварка под водой и в космосе, порошковыми материалами и др. Многие из них были разработаны именно в Институте электросварки имени Е. О. Патона.
Основы теории сварочных процессов

Сваркой называется процесс получения неразъемных соединений посредством установления межатомных связей между соединяемыми частями при их нагревании и (или) пластическом деформировании. Именно так определяет сварку ГОСТ 2601-84. Это определение относится к металлам, неметаллическим материалам (пластмассы, стекло и т. д.) и к их сочетаниям.
Классификация видов сварки
Сварка металлов, согласно ГОСТ 19521-74, классифицируется по основным физическим, техническим и технологическим признакам.
Физические признаки, в зависимости от формы энергии, используемой для образования сварного соединения, подразделяются на три класса: термический (плавление с использованием тепловой энергии), термомеханический (использование тепловой энергии и давления) и механический (сварка при помощи механической энергии и давления). К техническим признакам относятся: способ защиты металла в сварочной зоне, непрерывность сварки и степень механизации процесса. Технологические признаки установлены для каждого способа сварки отдельно.
К механическомуклассу относят сварку взрывом, при которой атомы свариваемых изделий сближаются за счет энергии, выделяемой при взрыве; холодную сварку пластической деформацией свариваемых металлов в зоне стыка под воздействием механического усилия и ультразвуковую сварку – соединение металлов энергией ультразвуковых колебаний.
Термомеханический класс содержит больше видов. Диффузионная сварка осуществляется за счет взаимного проникновения атомов свариваемых изделий (диффузии) при повышенной температуре в вакуумной установке.
Сварка высокочастотнымитоками осуществляется благодаря пластическому деформированию свариваемых изделий, предварительно нагретых высокочастотным током, проходящим между ними. При сварке трением сближают торцы вращающихся вокруг своих осей заготовок; от трения друг о друга торцы деталей сильно разогреваются, а при остановке вращения под большим давлением образуется качественное неразъемное соединение.
К термомеханическому классу относятся и разновидности контактной сварки.
Стыковую контактную сварку непрерывным оплавлением применяют для соединения заготовок сечением до 0,1 м. Типичными изделиями являются элементы трубчатых конструкций, колеса, рельсы, железобетонная арматура, листы, трубы. Плавление током металла ведется в постоянном или периодическом режиме, одновременно со сближением заготовок, которые в процессе оплавления укорачиваются на заданный припуск. При рельефной контактной сварке на заготовках предварительно создают рельефы – локальные возвышения на поверхности размером несколько миллиметров в диаметре. При контактной сварке таких деталей рельефы расплавляются проходящим через них сварочным током, выдавливаются оксиды и загрязнения.
Ввиду сложной технологии и необходимости использования дорогого оборудования вышеописанные виды сварки получили исключительно промышленное применение. Из видов этого класса в кустарном производстве применяются кузнечная и точечная контактная сварки. При точечной сварке детали зажимают в электродах сварочной машины или специальных сварочных клещах. После этого между электродами начинает протекать большой ток, который разогревает металл деталей в месте их контакта до температур плавления. Затем ток отключается и осуществляется «проковка» за счет увеличения силы сжатия электродов. Металл кристаллизуется при сжатых электродах, образуя сварное соединение[1]1
Оборудование и технология контактной сварки будут рассмотрены в разделе «Конструирование любительских сварочных аппаратов».
[Закрыть]. Кузнечная сварка осуществляется за счет возникновения в раскаленном металле межатомных связей при пластическом деформировании ковочным молотом. В настоящее время в промышленности практически не используется, но применяется в мелкосерийном и кустарном производстве[2]2
Кузнечные работы – отдельная обширная тема, которая в объеме данной книги не рассматривается.
[Закрыть].
Термический класс, как и термомеханический, тоже богат сложными промышленными видами. Так, при электрошлаковой сварке источником теплоты служит специальный флюс, разогревающийся проходящим через него электрическим током и при этом расплавляющий кромки свариваемых деталей и присадочную проволоку. Экзотермическая (термитная) сварка для нагрева металла использует расплавленный термит – порошкообразную смесь металлического алюминия или магния и железной окалины. Для плазменной сварки источником теплоты является плазменная струя, получаемая при ионизации рабочего газа в промежутке между электродами, одним из которых может быть само свариваемое изделие. Электронно-лучевая сварка ведется в вакуумных камерах электронным лучом, получаемым за счет термоэлектронной эмиссии с катода электронной пушки. При лазерной сварке источником теплоты служит мощный лазерный луч.
В то же время именно к этому классу относятся газосварка и дуговая электросварка, чаще всего применяемые в быту и мелкосерийном производстве. Они и будут рассмотрены в данной книге наиболее подробно.
Электродуговая сваркаС применением электродуговой сварки в настоящее время осуществляется примерно 65 % сварочных работ. Источником теплоты служит сварочная дуга – мощный электрический разряд в ионизированной среде, возникающий между торцом электрода и свариваемым изделием. Температура в столбе сварочной дуги колеблется от 5000 до 12 000 К и зависит только от состава газовой среды дуги. Это тепло нагревает торец электрода и оплавляет свариваемые поверхности. В процессе остывания и кристаллизации расплава образуется сварное соединение.
Электродуговая сварка имеет собственные подвиды.
Сварка неплавящимся электродом[3]3
В англоязычной литературе этот вид сварки известен как gas tungsten arc welding (GTA welding, GTAW) или tungsten inert gas welding (TIG welding, TIGW), в немецкоязычной литературе – wolfram-inertgasschweißen (WIG).
[Закрыть]. В качестве электрода используется стержень из графита или вольфрама, температура плавления которых выше температуры сварочной дуги. Сварка чаще всего происходит в среде защитного газа (аргон, гелий, азот и их смеси) для защиты шва и электрода от влияния атмосферы и устойчивого горения дуги. Сварку можно проводить как с присадочным материалом, так и без него.
Полуавтоматическая сваркапроволокой в защитных газах[4]4
В англоязычной иностранной литературе именуется gas metal arc welding (GMA welding, GMAW), в немецкоязычной литературе – metallschutzgasschweißen (MSG). Разделяют сварку в атмосфере инертного газа (metal inert gas, MIG) и в атмосфере активного газа (metal active gas, MAG).
[Закрыть]. Электродом здесь служит металлическая проволока, к которой через токопроводящий наконечник подводится ток, а электрическая дуга расплавляет проволоку. Для обеспечения постоянной длины дуги проволока подается автоматически. Вместе с электродной проволокой из сварочной горелки подаются защитные газы (аргон, гелий, углекислый газ и их смеси). Полуавтоматическую сварку можно вести и без газа, применяя самозащитную порошковую проволоку.
Ручная дуговая сварка[5]5
В англоязычной литературе именуется shielded metal arc welding (SMA welding, SMAW) или manual metal arc welding (MMA welding, MMAW). Чаще всего употребляется аббревиатура MMA. В старой отечественной литературе было принято сокращение РДС.
[Закрыть]. Для сварки используют проволочный электрод с нанесенным на его поверхность покрытием (обмазкой). При плавлении обмазки образуется защитный слой, отделяющий зону сварки от атмосферных газов (азота, кислорода) и способствующий легированию шва, повышению стабильности горения дуги, удалению неметаллических включений из металла шва, формированию шва и т. д.
Сварка под флюсом[6]6
Международное обозначение – SAW (Submerged Arc Welding).
[Закрыть]. В этом случае конец электрода в виде металлической проволоки или стержня подается под слой флюса. Горение дуги происходит в газовом пузыре, находящемся между металлом и слоем флюса, благодаря чему улучшается защита металла от вредного воздействия атмосферы и увеличивается глубина проплавления металла.
Источником теплоты является газовый факел, образующийся при сгорании смеси кислорода и горючего газа. В качестве последнего применяют ацетилен, водород, пропан-бутановую смесь, пары керосина, бензина, природный, светильный, нефтяной, коксовый и другие газы. В последнее время получил распространение сжиженный газ МАФ (метилацетилен-алленовая фракция), который обеспечивает хорошую скорость сварки и высокое качество сварочного шва, но требует применения особой присадочной проволоки с повышенным содержанием марганца и кремния. Тепло, выделяющееся при горении смеси, расплавляет свариваемые поверхности и присадочный материал с образованием сварочной ванны.
Физико-химическая сущность сварки металлов
Итак, для соединения двух металлов в единое целое необходимо сократить расстояние между их атомами настолько, чтобы активизировались силы взаимного притяжения и установилось равновесие между силами притяжения и отталкивания. Чтобы придать соединяемым атомам соответствующее смещение, извне необходимо сообщить энергию, которую называют энергией активации. Ее при сварке вводят путем нагрева (термическая активация) или пластического деформирования (механическая активация). По признаку применяемого вида активации в момент образования межатомных связей в неразъемном соединении различают два вида сварки: сварку плавлением и сварку давлением (рис. 1).

Рис. 1. Схемы возможных областей сварки давлением и плавлением в зависимости от температуры (Т) и давления (Р)
Сварка давлением
Сущность сварки давлением состоит в пластическом деформировании металла по кромкам свариваемых частей под статической или ударной нагрузкой. Для ускорения процесса обычно выполняют местный нагрев деталей. Благодаря пластической деформации у кромок свариваемых деталей разрушаются окисные пленки и поверхности сближаются до расстояний возникновения межатомных связей. Зона, где образовались межатомные связи соединяемых частей при сварке давлением, называется зоной соединения.
Характер процесса сварки давлением с нагревом может быть и другим. Например, при стыковой контактной сварке оплавлением свариваемые кромки первоначально оплавляются, а затем пластически деформируются. При этом часть пластически деформированного металла совместно с некоторыми загрязнениями выдавливаются наружу, образуя грат. На рис. 1 видно, что с увеличением температуры нагрева металла для сварки давлением требуются меньшие усилия.
Сварка плавлениемСущность сварки плавлением состоит в том, что при температурах выше Тпл жидкий металл одной оплавленной кромки самопроизвольно соединяется и в какой-то мере перемешивается с жидким металлом второй оплавленной кромки. Так создается общий объем жидкого металла, который называется сварочной ванной. Зачастую сварочная ванна получается смешиванием основного и присадочного металла, вносимого непосредственно в зону сварки электродом, сварочной проволокой и т. д.
Плавление основного и присадочного материалов в процессе сварки происходит под действием концентрированной энергии, вызванной сварочной дугой, пламенем горелки или каким-либо другим способом. Энергия теплового источника расходуется на нагрев металла детали, плавление присадочного материала, защитного флюса и на тепловые потери.
Распределение температуры в свариваемом металле зависит от мощности источника тепла, физических свойств металла, размеров конструкции, скорости перемещения и т. д. На рис. 2 показаны изотермы – овальные кривые, сгущающиеся впереди движущегося при сварке источника тепла (электрической дуги, пламени горелки). Изотерма 1600 °C – это температура плавления стали, она определяет ориентировочный размер сварочной ванны. Изотерма 1000 °C указывает на зону перегрева металла, изотерма 800 °C показывает зону закалочных явлений, а 500 °C – зону отпуска.

Рис. 2. Схема изотерм при сварке
Затвердевание расплавленного металла, происходящее в хвостовой части ванны, называется кристаллизацией. Динамика этого процесса такова: сварочная дуга, направленная в головную часть ванны, повышает в этой области температуру, в результате чего происходит плавление основного и электродного металлов. Механическое давление, оказываемое дугой на жидкую фазу основного и дополнительного металлов, вызывает их перемешивание и перемещение в хвостовую часть ванны, вытесняя металл из основания ванны и открывая доступ к следующим слоям. По мере удаления металла от зоны плавления отвод тепла начинает преобладать над его притоком, и температура жидкой фазы снижается. Затвердевая, она образует сварной шов – общие для основного и электродного металла кристаллы, обеспечивающие монолитность сварочного соединения (рис. 3, а).

Рис. 3. Зоны сварного шва (а) и возможные дефекты в нем (б)
Снижение температуры в хвостовой части ванны происходит за счет усиленного теплоотвода в прилегающий холодный металл, так как его масса по сравнению с ванной значительно преобладает. Кристаллы металла начинают формироваться от готовых центров основного металла в направлении ведения сварки и принимают форму кристаллических столбов, вытянутых в сторону, противоположную теплоотводу.
Свойства сварного соединения определяются характером тепловых воздействий на металл в околошовных зонах. Участок основного металла, не подвергшийся расплавлению, структура и свойства которого изменились в результате нагрева при сварке или наплавке, называется зоной термического влияния. Здесь находятся участки старения (200–300 °C); отпуска (250–650 °C); неполной перекристаллизации (700–870 °C); нормализации (840—1000 °C); перегрева (1000–1250 °C); околошовный участок, примыкающий к линии сплавления (1250–1600 °C). Зона сплавления расположена вблизи границы оплавленной кромки свариваемой детали и шва и содержит образовавшиеся межатомные связи. В поперечном сечении сварного соединения она измеряется микрометрами, но роль ее в прочности металла очень велика.
В зоне термического влияния из-за быстрого нагрева и охлаждения металла происходят его структурные изменения. Следовательно, сварочный шов может получиться прочным и пластичным, но из-за термических воздействий на деталь качество сварки в целом будет низким (рис. 3, б).
Величина зоны термического влияния составляет при ручной электродуговой сварке для обычного электрода 2–2,5 мм, а для электродов с повышенной толщиной обмазки – 4—10 мм. При газовой сварке зона термического влияния существенно возрастает – до 20–25 мм.
Химический состав сварочного шваХимический состав сварочного шва значительно отличается от основного металла, так как в этой области происходит перемешивание основного и электродного металлов, различных присадок, используемых при сварке, а также реакций взаимодействия жидкой фазы с атмосферными газами и защитными средствами. Соотношения отдельных компонентов, из которых состоит сварочный шов, зависят от способа наложения шва, режимов сварки. Например, если сварочный шов ведется с разделкой, то доля основного металла в структуре шва значительно снижается. Определение доли элемента, содержащегося в металле шва, учитывают с помощью поправочного коэффициента n, показывающего, какая доля металла, содержащегося в электроде или сварочной проволоке, переходит в металл шва. Величина n может колебаться в пределах от 0,3 до 0,95.
В процессе сварки расплавленный металл активно вступает в реакцию с атмосферными газами, поглощая их и тем самым снижая механические качества сварочного шва. Так, при дуговой сварке дуга, контактирующая с металлом, состоит из смеси N2, O2, Н2, СО2, СО, паров Н2О, паров металла и шлака. В зоне плавления металла происходит процесс диссоциации – распад молекул на атомы. Под воздействием высоких температур молекулярный азот, водород и кислород распадаются и переходят в атомарное состояние, при котором активность газов значительно повышается.
Атомы кислорода активно растворяются в жидкой фазе металла, образуя оксиды, окисляя примеси и легирующие элементы, содержащиеся в металле. Из-за этого снижается предел прочности, предел текучести, ударная вязкость металла, ухудшается коррозионная стойкость и жаропрочность сталей. Кислород попадает в зону сварки из окружающего воздуха, из влаги, находящейся на свариваемых кромках и флюсах, с обмазки электродов. Кислород из расплавленного металла удаляют путем введения в сварочную ванну кремния и марганца, которые взаимодействуют с оксидом железа, образуя шлак. Шлак в процессе кристаллизации образует на поверхности шва твердую корку, которую удаляют механическим путем.
Растворение азота в жидкой фазе большинства металлов сопровождается образованием нитридов, что приводит к старению металла и повышению его хрупкости. Как и кислород, азот попадает в зону сварки из окружающего воздуха, и для недопущения образования нитридов сварочную ванну для легированных, жаропрочных сталей и большинства цветных металлов изолируют средой защитных газов.
Весьма нежелательным процессом является растворение водорода, что приводит к возникновению гидридов. Их образование в зоне термического влияния приводит к появлению пор, микро– и макротрещин. Водород попадает в зону сварки из атмосферного воздуха и при разложении влаги, которая имеется на свариваемых кромках, в обмазке электродов, защитных флюсах и т. д. Снижению содержания водорода способствует предварительное прокаливание электродов, свариваемых поверхностей и тщательная их зачистка.
Окись углерода в жидкой фазе металла практически не растворяется, но влияние этого соединения на качество сварочного шва огромно. В процессе кристаллизации металла окись углерода начинает выделять пузырьки, образуя поры в массиве сварочного шва.
Негативное влияние на состав сварочного шва оказывает сера, которая находится в основном и присадочном металлах, покрытиях, флюсах и т. д. Под действием высоких температур в сварочной ванне образуется сульфид железа (FeS), в процессе кристаллизации которого возникает эвтектика[7]7
Эвтектика – тонкая смесь твердых веществ, одновременно выкристаллизовывающихся из расплава при температуре более низкой, чем температура плавления отдельных компонентов, а также жидкий расплав или раствор, из которого возможна такая кристаллизация.
[Закрыть] (ее температура плавления ниже, чем у основного металла).
Пары воды, находящиеся в жидкой фазе металла, взаимодействуют с ней, образуя оксиды железа и водород.
Бороться с этими вредными явлениями чрезвычайно трудно, и полностью изолировать сварочную ванну от влияния атмосферных газов чаще всего не удается. Чтобы снизить влияние на сварочную ванну атмосферных газов, применяют разные виды защиты – электродное покрытие, защитные газы, флюсы, вакуум и т. д. Это значительно снижает интенсивность металлургических реакций и позволяет добиться хорошего качества сварочного шва. Кроме того, большая скорость охлаждения сварочной ванны не позволяет металлургическим реакциям завершиться полностью.