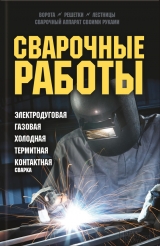
Текст книги "Сварочные работы. Электродуговая. Газовая. Холодная. Термитная. Контактная сварка"
Автор книги: Юрий Подольский
Жанры:
Технические науки
,сообщить о нарушении
Текущая страница: 4 (всего у книги 25 страниц) [доступный отрывок для чтения: 10 страниц]
На изготовленных из металла заготовках и деталях после отжига, сварки, вырезки и других операций появляются изгибы, местные неровности, выпучины и вмятины различной формы, волнистость и прочие дефекты. Операция по устранению этих дефектов называется правкой.
Ручную правку листового металла производят на плите или наковальне при помощи деревянных киянок или молотков, сделанных из меди, свинца, алюминия или резины.
Заготовки из прутковой и профильной стали правят стальными молотками с круглым выпуклым бойком. Крупные заготовки правят ударами кувалды или на механических молотах и прессах. Так как при ударах стальным молотком на металле неизбежно остаются следы, при правке изделий с уже обработанной поверхностью применяют подкладки из мягких материалов (дерево, латунь и др.).
Наиболее трудоемкой является операция правки листового металла. Различают три случая: правка волнистости полосы или на краях, правка изогнутых (серповидных) заготовок под линейку и правка выпучин.
При правке волнистости полосы или края заготовки, что чаще всего получается при вырезании ее из листа, наносят удары молотком, начиная от наиболее выпуклых мест к краям. Наиболее сильные удары наносят в середине выпуклости и уменьшают силу удара по мере приближения к краям. Таким образом, выпуклые участки полосы осаживаются и волнистость выравнивается. Чем тоньше листовая заготовка, тем аккуратнее и внимательнее надо ее править, так как при неправильном ударе молотком его боковые грани легко могут испортить заготовку или даже пробить ее.
Правку длинных, узких,серповидно изогнутыхзаготовок производят на плите под линейку с помощью деревянной киянки или молотка со стальным выпуклым бойком. Заготовку кладут плашмя на плиту, прижимают одной рукой и наносят удары, начиная с более короткой вогнутой кромки изогнутой заготовки, т. е. той, где металл сжат и его необходимо растянуть. В начале правки удары по вогнутой кромке должны быть более сильные и по мере приближения к противоположной кромке – всё слабее и слабее. Этим достигают того, что вогнутая, более короткая, кромка постепенно вытягивается и заготовка выпрямляется. Процесс выпрямления периодически контролируют линейкой.
Правку выпучин производят на плите, которая по своим размерам должна быть больше заготовки настолько, чтобы края последней не свешивались с плиты. Перед началом правки выпучины обводят мелом или простым карандашом, затем заготовку кладут на плиту выпуклым местом вверх и начинают наносить удары молотком рядами, от края заготовки в направлении выпучины. Под ударами молотка металл вокруг выпуклого места вытягивается, постепенно выравнивается, и выпучина исчезает. Нельзя сразу наносить удары по выпуклому месту – от этого оно еще больше увеличивается. Удары наносят частые, но не сильные. По мере приближения к центру выпуклости удары должны становиться слабее.
Полосы из мягких алюминиевых и медных сплавов лучше править через прокладку из гетинакса или текстолита толщиной 1,5–3 мм. В этом случае ровная неповрежденная поверхность получается даже при работе обычным стальным молотком.
Тонкий (до 0,5 мм) листовой металл правят на стальной плите, притирая металлическим или деревянным бруском с закругленными кромками.
ГибкаПутем гибки из прямолинейной заготовки получают криволинейное изделие. Сгибают заготовки вокруг какой-либо оправки, форму которой она принимает, в тисках или на плите на нужный угол. На рис. 13 изображены оправка и последовательные операции гибки квадратного прутка для изготовления фигурного элемента решетки.

Рис.13. Последовательные операции гибки элемента решетки из квадратного прутка на специальной оправке
При толстых заготовках гибку осуществляют ударами молотка, лучше всего деревянного, не оставляющего на металле следов от удара. Проволоку гнут плоскогубцами или круглогубцами.
В процессе гибки наружные слои металла растягиваются и удлиняются, а внутренние, сжимаясь, укорачиваются. Неизменным по длине остается так называемый нейтральный слой, который у симметричных по сечению заготовок (квадратных, прямоугольных, круглых, овальных, шестигранных и др.) лежит на равном расстоянии от сторон, посередине, а у несимметричных профилей (треугольного, полукруглого) нейтральный слой проходит через центр тяжести сечения. Если радиус гибки очень мал, в металле могут образоваться трещины. Чтобы этого избежать, не следует гнуть по радиусам меньшим, чем двойная толщина заготовки.
Листовой металл после прокатки имеет волокнистую структуру. Чтобы не получалось трещин, его следует гнуть поперек волокон или так, чтобы линия сгиба составляла с направлением прокатки угол, равный 45°.
При гибке деталей из листового металла, проволоки круглого и квадратного сечения, полос и т. п. часто возникает распружинение, т. е. угол изгиба несколько увеличивается, а деталь выпрямляется после снятия напряжения. Величина угла, на который распрямляется деталь, вследствие упругой отдачи зависит от степени упругости металла, его толщины и радиуса изгиба. Заранее точно определить угол пружинения очень трудно, поэтому приходится заготовки загибать сильнее, т. е. с заведомо меньшими радиусами и углами изгиба, а оснастку (оправки) для получения точных изгибов деталей необходимо подбирать и доводить опытным путем.
Гибку деталей из тонких заготовок производят не ударами, а сглаживанием. Гибку заготовок из листового и полосового металла толщиной более 0,5 мм и из круглого материала диаметром более 4 мм производят на оправках ударами молотка. Форма оправки должна соответствовать форме изгибаемого профиля с учетом деформации металла. Наименьшие радиусы гибки листового материала в холодном виде приведены в табл. 2 Приложения. При меньших радиусах гибку следует производить в нагретом состоянии.
При гибке деталей под углом 90° заготовку детали зажимают в тиски так, чтобы линия гибки находилась на уровне верхней кромки губок или нагубников тисков. Гибку производят обычно за два приема: сначала ударом по верхней части заготовки, а затем внизу у губок под углом 90°. Первый прием лучше выполнять деревянным молотком, так как он не портит поверхности детали. Угол в месте перегиба обычно формируют металлическим молотком. Ударять им нужно равномерно всей поверхностью бойка.
Гибка деталей, имеющих несколько прямых углов, производится вышеописанным способом на оправках, зажимаемых в тисках.
При гибке полос под острым углом на заготовке чертилкой размечается место изгиба, затем заготовку закрепляют вместе с оправкой так, чтобы риска была обращена в сторону загиба и выступала над ребром оправки на 0,5 мм. Ударами молотка полосу изгибают до полного прилегания ее к грани оправки.
Кроме тисков и молотков, для гибки металла используют различные оправки и приспособления, чаще всего – простейшие (рис. 14).
Детали с несколькими изгибами подвергают гибке на специальных оправках, размеры и форма которых соответствуют размерам и форме детали. С помощью такой оснастки из полосовой стали и прутков получают самые замысловатые формы гнутых элементов, которые сваркой объединяют в прочное и изящное изделие.

Рис. 14. Простейшие приспособления для гнутья полосовой стали:
а – выгибание дуги с помощью клиновых подкладок; б – выгибание дуги по шаблону; в – гибка под прямым углом с помощью струбцины; г – гибка завитка в тисках; д – гибка завитка по шаблону
Гибка декоративных элементов
Линейная гибка хотя и позволяет получить замечательные узоры, но возможности металла гораздо шире. В былые годы (хотя и сегодня этот элемент не забывают) очень популярным украшением решеток был торсированный стержень – четырехгранный стальной прут, скрученный спиралью (рис. 15, а). Четырехгранные стержни толщиной до 20 мм скручивают, как правило, в холодном состоянии. Очень толстые стержни в холодном состоянии скрутить невозможно, поэтому приходится применять нагрев, но это не так просто. Неравномерно нагретый стержень приводит к неравномерному скручиванию, т. е. браку. Равномерно нагреть толстые стержни можно только в печи. В кузнечном горне, тем более газовой горелкой такой нагрев практически невозможен.
Чтобы скрутить стержень толщиной до 20 мм, нужно точно отметить участок, который должен быть скручен, и зажать стержень по нижней риске в тисках. Затем нужна трубка, которая свободно надевается на этот стержень. Ее обрезают на длину участка скручивания, надевают на стержень, а сверху надевают ворот с четырехгранным отверстием. Скручивание выполняют двухплечим воротом, а если стержень большой толщины – то и четырехплечим. Ворот крутят до тех пор, пока не получат требуемую закрутку.
Очень красиво выглядят торсированные стержни, у которых перед скручиванием вдоль всех четырех граней выдавлены глубокие бороздки. И даже плоские стержни и полосы можно скручивать таким же методом – правильно закрученные, они будут выглядеть очень эффектно.
На рубеже XIX и XX столетий был разработан так называемый торсировочный станок, на котором можно было скручивать без особых усилий и помощи трубки стержни толщиной до 50 мм. В наши дни этих станков уже почти нет, ими иногда пользуются только в некоторых старых деревенских кузницах.
Распространенным кованым элементом украшения с незапамятных времен являются различной формы шишки. Их делают свертыванием проволоки в спираль из одной нитки либо из двух – шести ниток, связанных в пучок. Шишки первого типа используют в качестве концевых элементов выступов у решеток, а второго – в качестве украшения срединных участков стержней решеток или как рукоятки.
Шишки из одной нитки делают довольно просто. От проволоки ∅5–8 мм отрезают кусок нужной длины. Конец проволоки (примерно 3 см) отгибают под прямым углом, а оставшуюся ее часть нагревают. Отогнутый конец проволоки зажимают в тисках так, чтобы над губками тисков выступал участок длиной не более толщины проволоки, а длинная часть проволоки размещалась параллельно губкам. После этого проволоку туго закручивают вокруг образовавшегося таким образом центра на половину ее длины (рис. 15, б). То же самое делают с другой половиной проволоки. Когда проволока скручена в одной плоскости, ей нужно придать форму шишки. Центры спиралей вытягивают клещами. Далее спираль опускают в обрезок трубы соответствующего ее основанию диаметра и наставкой с одного удара молотка получают конус шишки (рис. 15, в). Такую же операцию производят со второй спиралью и совмещают половинки шишки основаниями в одно целое.
Чем больше проволок берется для скручивания, тем изделие больше походит на настоящую шишку. Несколько проволок с одного конца сваривают, проковывают в квадрат и фиксируют в тисках в горячем состоянии, а с другого – закручивают воротком (рис. 15, г). В зависимости от того, насколько сложную хотят получить шишку, связку скручивают на 1,5–3 оборота. Чтобы проволоки образовали перед закруткой цилиндр, их располагают вокруг осевого прутка, загнув концы длиной 2 см на 180° вовнутрь проволочного пучка, сваривают их внахлест, образуя цилиндр, и так же проковывают в квадрат.
После скручивания заготовку оставляют в тисках для остывания. Остывшую поковку раскручивают в обратном направлении. В результате связка начинает распускаться до тех пор, пока не получится требуемая форма шишки. Если шишку надо сделать шире, то в процессе раскручивания связку осаживают в продольном направлении.
Шишки такого типа кузнецы в далеком прошлом делали не из связки прутков, а из цельного прутка квадратного сечения, рассекая его в продольном направлении на несколько ветвей также четырехгранного сечения, после чего его скручивали. Полученная таким способом шишка выглядит привлекательнее.
Наиболее распространенными декоративными коваными элементами являются волюты – украшения в форме спиралевидного завитка (рис. 15, е). Конечно, кованый металл обладает особой привлекательностью, но и слесарная техника позволяет изготовить очень красивые детали.
По количеству завитков волюта бывает односторонняя и двусторонняя (симметричная и асимметричная), по типу скручивания – с обратной закруткой и с разветвлением от металлического прута.
Вначале следует определить необходимую длину заготовки. Проще всего это сделать с помощью тонкой проволоки, которую сначала скручивают по форме волюты, потом распрямляют и измеряют. Затем отрубают заготовку этой длины и выгибают основной наиболее крутой завиток. После этого молотком на оправке выгибают спираль (рис. 15, д).

Рис.15. Гнутые кузнечные изделия:
а – торсированный стержень; б, в – скручивание шишки из одного прутка; г – шишка из связки прутков; д – формование завитка волюты; е – виды волют
Заготовки, предназначенные для изготовления волют, можно украсить продольными желобками или орнаментами, выполненными с помощью чеканов или рельефных пуансонов. Чтобы упростить работу, украсить желобками или другим орнаментом можно только концы волют.
При изготовлении однотипных мелких спиралей, требующихся в решетках и других изделиях в больших количествах, пользуются шаблонами, которые облегчают работу, ускоряют процесс изготовления и повышают точность размеров полученных деталей.
Сварные соединения и швы
Сварные соединения могут быть стыковыми, угловыми, тавровыми и нахлесточными (рис. 16).

Рис.16. Сварные соединения:
а – стыковое; б – угловое; в – нахлесточное; г – тавровое; д – торцовое
Стыковым называется сварное соединение двух элементов, расположенных в одной плоскости или на одной поверхности.
Угловым называется соединение двух элементов, расположенных под прямым углом и сваренных в месте примыкания их краев.
Нахлесточным называется сварное соединение, в котором свариваемые элементы расположены параллельно и перекрывают друг друга.
Разновидностью нахлесточного соединения является торцовое, в котором боковые поверхности свариваемых элементов примыкают друг к другу.
Тавровым называется сварное соединение, в котором к боковой поверхности одного элемента примыкает под углом и приварен торцом другой элемент.
Часть конструкции, в которой сварены примыкающие друг к другу элементы, называется сварным узлом.
Сварные швы могут быть стыковыми и угловыми (рис. 17, а – г). Стыковой шов – сварной шов стыкового соединения. Угловой шов – сварной шов углового, таврового и нахлесточного соединений. Разновидностью этих типов являются швы пробочные и прорезные, выполняемые в нахлесточных соединениях.
По форме в продольном направлении сварные швы могут быть непрерывными, прерывистыми, одно- и многослойными, одно- и двусторонними (рис. 17, д – к). С помощью стыковых швов образуют в основном стыковые соединения, с помощью угловых швов – тавровые, крестовые, угловые и нахлесточные соединения, с помощью пробочных и прорезных швов могут быть образованы нахлесточные и иногда тавровые соединения.
В зависимости от формы и размеров изделия швы могут отличаться пространственным положением. Швы разделяют на нижние, вертикальные, горизонтальные и потолочные (рис. 17, л).
Горизонтальные швы выполняют на вертикальной плоскости в горизонтальном направлении. Согласно ГОСТ 11969-79, швы по положению в пространстве подразделяются на: нижние – Н и нижние в лодочку – Л; полугоризонтальные – Пг; горизонтальные – Г; полувертикальные – Пв; вертикальные – В; полупотолочные – Пп; потолочные – П.

Рис.17. Сварные швы:
а – стыковые; б – угловые; в – пробочные; г – прорезные; д – непрерывные; е – прерывистые цепные; ж – прерывистые шахматные; з – односторонние; и – двусторонние; к – многослойные (показано 2 слоя); л – основные и промежуточные пространственные положения сварочных швов (I – нижнее; II – вертикальное или горизонтальное; III – потолочное); м—о – прихватки
Сварные швы, применяемые для фиксации взаимного расположения, размеров и формы собираемых под сварку элементов, называются прихватками. Длина каждой прихватки составляет от 3 до 6 толщин свариваемого металла, расстояние между ними выдерживается от 20 до 40 толщин. Ставят прихватки с лицевой стороны соединения, очищают от шлака, а при сварке полностью удаляют или полностью переплавляют. На коротких и средних швах прихватки расставляют от центра к краям, поочередно в каждую сторону (рис. 17, м). На длинных швах поступают наоборот: прихватывают вначале края, затем центр и поочередно с каждой стороны двигаются от краев к центру (рис. 17, н). При кольцевых швах (рис. 17, о) прихватки ставят попеременно по главным координатным осям (под 90°), а при необходимости – и по дополнительным диагоналям (под 45°).
Стыковые швы, как правило, выполняют непрерывными; отличительным признаком для них обычно служит форма разделки кромок[15]15
Разделка кромок – придание кромкам, подлежащим сварке, необходимой формы.
[Закрыть] соединяемых деталей в поперечном сечении (рис. 18, а – е).
По этому признаку различают следующие основные типы стыковых швов: с отбортовкой кромок (применяются при газовой сварке тонкого металла); без разделки кромок – односторонние (при толщине свариваемых деталей 1–6 мм) и двусторонние (при толщине деталей 3–8 мм); с разделкой одной кромки – односторонней, двусторонней (до 60 мм); с прямолинейной или криволинейной формой разделки; с односторонней разделкой двух кромок; с V-образной разделкой; с двусторонней разделкой двух кромок; Х-образной разделкой (с толщиной деталей до 120 мм). Разделка может быть образована прямыми линиями (скос кромок) либо иметь криволинейную форму (U-образная разделка).
Угловые швы различают по форме подготовки свариваемых кромок в поперечном сечении и сплошности шва по длине (рис. 18, ж – и).
По форме поперечного сечения швы могут быть без разделки кромок (при толщине свариваемых деталей от 2 до 30 мм), с односторонней разделкойкромки (3—60 мм), с двусторонней разделкой кромок (до 100 мм).

Рис.18. Подготовка кромок стыковых (а – е) и угловых (ж – и) швов:
а – с отбортовкой кромок; б – без разделки кромок; в – с разделкой одной кромки; г – с односторонней разделкой двух кромок; д – с Х-образной разделкой двух кромок: е – с U-образной разделкой; ж – без разделки; з – с односторонней разделкой; и – с двусторонней разделкой; к – конструктивные элементы разделки
По протяженности угловые швы могут быть непрерывными и прерывистыми, с шахматным и цепным расположением отрезков шва (рис. 17, д—ж). Тавровые, нахлесточные и угловые соединения могут быть выполнены отрезками швов небольшой протяженности – точечными швами.
Пробочные швы по своей форме в плане (вид сверху) обычно имеют круглую форму и получаются в результате полного проплавления верхнего и частичного проплавления нижнего листов (их часто называют электрозаклепками) либо путем проплавления верхнего листа через предварительно проделанное отверстие.
Прорезные швы, обычно удлиненной формы, получают путем приварки верхнего (накрывающего) листа к нижнему угловым швом по периметру прорези. В отдельных случаях прорезь может заполняться полностью.
Подготовку кромок при ручной сварке регламентирует ГОСТ 5264-80. Чаще всего приходится разделывать кромки при сварке металла большой толщины. Форму разделки кромок и их сборку под сварку характеризуют четыре основных конструктивных элемента: зазор b, притупление с, угол скоса кромки β и угол разделки кромок α, равный β или 2β (рис. 18, к). Стандартный угол разделки кромок в зависимости от способа сварки и типа соединения изменяется в пределах от 45±2° до 12±2°. Тип разделки и величина угла разделки кромок определяют количество необходимого дополнительного металла для заполнения разделки, а значит, производительность сварки. Так, например, Х-образная разделка кромок по сравнению с V-образной позволяет уменьшить объем наплавленного металла в 1,6–1,7 раза. Уменьшается время на обработку кромок. Правда, в этом случае возникает необходимость вести сварку с одной стороны шва в неудобном потолочном положении или кантовать свариваемые изделия.
Притупление кромки, т. е. нескошенная часть торца кромки, с обычно составляет 2±1 мм и выбирается в зависимости от толщины свариваемого металла. Его назначение – обеспечить правильное формирование шва и предотвратить прожоги в корне шва. Зазор b обычно равен 1–2 мм (допускается до 5 мм), так как при принятых углах разделки кромок наличие зазора необходимо для провара корня шва. Чем больше зазор, тем глубже проплавление металла.

Рис.19. Виды сварных швов:
а – плоский; б – выпуклый; в – вогнутый; г – стыковой; д – угловой; е – ширина шва; h – глубина проплавления; g – выпуклость (усиление) шва; а – толщина шва; k – катет шва
Основными геометрическими параметрами сварных швов являются: при стыковых соединениях – ширина, выпуклость и глубина проплавления шва; при угловых, тавровых и нахлесточных соединениях – ширина, толщина и катет шва (рис. 19, г – д).
Глубина проплавления стыкового шва (h) – наибольшая глубина расплавления основного металла в сечении шва.
Толщина углового шва (а) – наибольшее расстояние от поверхности углового шва до точки максимального проплавления основного металла.
Катет углового шва (k) – кратчайшее расстояние от поверхности одной из свариваемых частей до границы углового шва на поверхности второй свариваемой части. При симметричном угловом шве за расчетный катет принимается любой из равных катетов, при несимметричном шве – меньший.
Выпуклость сварного шва (g) – выпуклость шва, определяемая расстоянием между плоскостью, проходящей через видимые линии границы сварного шва с основным металлом, и поверхностью сварного шва, измеренного в месте наибольшей выпуклости.
Основным показателем формы швов является коэффициент формы сварного шва (ψ). Для стыкового шва этот коэффициент равен отношению ширины шва к глубине проплавления ; для углового шва – отношению ширины к толщине шва
. Форма и размеры сварного шва существенно влияют на качество сварного соединения. При ручной сварке покрытыми электродами коэффициент формы провара колеблется в пределах ψ = 1,0–2,5.
Таким образом, по форме наружной поверхности стыковые швы могут быть нормальными (плоскими), выпуклыми (с усилением) или вогнутыми (рис. 19, а – в). Причем вогнутость стыковых швов недопустима, это является серьезным браком сварки.
Угловые швы выполняют выпуклыми, плоскими, вогнутыми. Вогнутость угловых швов при сварке во всех пространственных положениях допускается не более 3 мм. Выпуклость (усиление) сварных швов допускается не более 2 мм при сварке в нижнем положении и не более 3 мм при сварке в остальных положениях. Допускается увеличение усиления сварных швов, выполненных в вертикальном, горизонтальном и потолочном положениях, на 1 мм при толщине основного металла до 26 мм и на 2 мм при толщине основного металла свыше 26 мм.
Сварные соединения с выпуклыми (стыковыми и угловыми) швами лучше работают на статическую нагрузку. Но швы с чрезмерным усилением нежелательны по двум причинам: из-за повышенного расхода электродов и электрической энергии, а также вследствие концентрации напряжений в точках пересечения поверхности шва с основным металлом.
Сварные соединения с плоскими (стыковыми и угловыми) и вогнутыми (угловыми) швами лучше работают на переменную и динамическую нагрузку, так как нет резкого перехода от основного металла к сварному шву. В противном случае создается концентрация напряжений, от которых может начаться разрушение сварного соединения.
Для всех типов швов важны полный провар кромок соединяемых элементов и внешняя форма шва как с лицевой, так и с обратной стороны. В стыковых, особенно односторонних, швах трудно проваривать кромки притупления на всю их толщину без специальных приемов, предупреждающих прожог и обеспечивающих хорошее формирование обратного валика.
Важное значение также имеет образование плавного перехода металла лицевого и обратного валиков к основному металлу, так как это обеспечивает высокую прочность соединения при динамических нагрузках. В угловых швах бывает трудно проварить корень шва на всю его толщину, и тогда рекомендуется вогнутая форма поперечного сечения шва с плавным переходом к основному металлу. Это снижает концентрацию напряжений в месте перехода и повышает прочность соединения при динамических нагрузках.