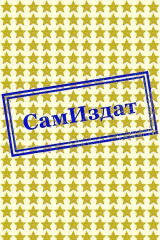
Текст книги "Технологическое древо Фронтир Индикона (СИ)"
Автор книги: Яр Серебров
Жанры:
Прочая фантастика
,сообщить о нарушении
Текущая страница: 5 (всего у книги 8 страниц)
– У нас такой 'ветроход' Симон Стевин ещё в тысяча шестисотом году изобрёл, только четырёхколёсный, – Мартин гордо задрал нос, – но только католические священники сочли мчащийся по земле парусник 'кораблем дьявола' и вознамерились передать изобретателя в руки святой инквизиции. Его спасло лишь заступничество принца Оранского, для которого он прежде построил колесную яхту. На ней принц любил катать придворных дам, временами съезжая с пляжа на мелководье и радуясь истошным вигам женщин. А когда голландцы взяли в плен испанского адмирала Франсиско Мендосу, принц и его прокатил по берегу моря, чтобы адмирал, так сказать, привыкал к новой для себя сухопутной жизни.
– Уверяю вас, Мартин, ваш математик далеко не первый изобретатель парусника на колёсах, – я немного осадил Мартина. – Впервые о таких парусниках упоминается еще за две тысячи лет до нашей эры! В годы правления египетского фараона Аменехмета третьего. На таком фараон путешествовал по окружающим его дворцы пустыням.
– С точно такими же мачтами как в ваше проекте?
– Почти.
– В самом деле?! Не может быть! – Мартин был ошарашен.
– Ещё как может! Потом в Китае, в шестом веке, создали повозку с парусом, которая могла перевозить тридцать человек и за день покрывала расстояние в несколько сотен ли.
– Врут! – безапелляционно заявил Павел. – Быть того не может! Если бы по льду, то ещё бы поверил, а на колёсах. Увольте-с!
Мы довольно долго спорили и обсуждали особенности паруса и устройства мачты и, наконец, пришли к общему мнению, что мы сможем построит буер в короткое время. Работу разбили на несколько частей. Мартин брал на себя колёса, Павел мачты и гики, Джон и Меринго плели циновки для паруса, а я на пару с Нганго занимался фермой, рамами колёс и общей координацией проекта.
Колеса изготавливали очень прочными, с плоскими спицами, количество которых было увлечено вдвое, поскольку чем больше колесо, тем больше спиц надо. Опыт в их изготовлении у нас набрался приличный. Ступица вышла даже проще в изготовлении – толстое, плоское кольцо, выточенное из пальмы дум и пазы под спицы. Когда колёс были готовы, их крепили на на ось сбивали раму стенки которой служили боковыми ограничителями подшипникового узла.
Для уменьшения износа с помощью деревянных гвоздей и клея, обод колеса обернули и обили кожей буйвола. Колёса, стойки и колёсную раму изготовили из древесины дум чтобы центр тяжести буера был ближе к земле.
Коробчатые стержни фермы склеивали из метровых сегментов соединяя их вкладками из массива. Поперечные сечения пазов обеспечивали возможность простого изготовления решетчатой балки.
Каждый из раскосов соединявших верхний пояс и нижний пояс имел на своих концах шипы вклеенные в пазы верхнего и нижнего пояса. Пазы делали стандартными под размер шпунтубеля с таким расчётом чтобы они заполняли и герметизировали объем пазов, а шипы сужались обеспечивая прочное склеивание и сцепление. Места крепления мачт, ворота дополнительно фиксировались фанерными пластина и прихватывались деревянными болтами, а иногда медными заклёпками.
Для крепления фермы на балках предусмотрели пазы и муфты для винтового крепления. В случае необходимости её можно было снять и поставить, например на поплавки, или снять перенести буер в разобранном виде. Удобно, что и не говори! Место между задними балками частично застелили доской из баобаба сделав небольшой настил, а остальное со временем планировали затянуть прочной сеткой для транспортировки людей или груза. В саму ферму, ближе к переднему колесу встроили цилиндрический ворот с фиксаторами и вставными рычагами вращаемыми ногами, для чего в ферме, с двух сторон крепились снимаемые сидения.
Передняя вилка с большим колесом соединялась с опорой медной шпилькой. На ней был установлен рычаг тормоза и высверлены отверстия для шипа-фиксатор направления движения, а для руления к ней был приделан рычаг поворачиваемый ногами сидевшего на ферме человека.
Для изготовления пустотелых мачт круглого сечения нам пришлось удлинять верстак, изготавливать шаблоны, во множестве готовить доски и брус. Мачты не были толстыми и на каждую шло всего шесть досок. В каждой второй доске с торцов делали угловой паз. Уложив их и зажав струбцинами, склеивали, образуя угловатые трубки длиной чуть больше метра и выдерживали не меньше суток в сжатом состоянии. Трубки сращивали шипами и клеем, установив внутрь короткий стержень и выравнивая края киянкой. После нам осталось снять уголки у шестиугольника, придав мачте округлую форму и обрезать в размер по длине. Все торцевые связки, кроме нижней сделали из цельных круглых реек. Жёстко зафиксированная мачта равномерно распределяет нагрузку по всему буеру и не даёт ему перевернуться от резких порывов, а также не требует никаких растяжек. Она оказалась настолько прочной, что по ней можно было не только лазить на верх, чтобы осмотреть местность.
Формировали парус так – циновки обшивали вокруг лат и оставляли карманы, на задние шкаторины нашивали полоску и прошивали двойной нитью, после соединяли готовые элементы в целое полотно. Как только парус был сшит мы подняли его наверх. Рога удерживали парус при рифлении и уборке, а также передавали основное давление на раму буера. Сам парус изготовили более пузатый, чтобы ловить слабый ветер. Дело в том, что паруса для разных ветров выкраиваются с разной кривизной. Для слабых ветров применяют более пузатые паруса, для сильных – плоские. Пузо достигается с помощью закладок, которые представляют собой полоски переменной ширины, отрезаемые от кромки полотнища. Чем больше закладка, тем более пузатым становится парус.
Общий вес буера с парусом, со стойками и фермой достигал с
емисот килограмм, что значительно больше той же грузовой телеги. Но у телег маленькие колёса и нет подшипников. Телега не выдержит полторы тонны груза, а наш буер без проблем. Обвязку крепили за переднюю вилку. Тонну груза два человека с трудом, но все же толкали, даже при отсутствии ветра. Будучи нагруженным буер не показывал рекордов скорости вследствие малой площади паруса и выдавал пять-десять километров в час по относительно ровной площадке при средней силе ветре, что не так плохо.
До разлома мы обычно ехали на буере, при этом чтобы не разгоняться осуществляли рифление и поднимали, когда два, а когда и три нижних сектора паруса. Обратно же шли под полным парусом и во многих местах вдвоём толкали буер, который совершено не хотел катиться сам через густую траву. По мере работы мы переделали обвязку, добавили длинные шесты под светильники и погремушки, которые представляли фарфоровые трубочки на нитках, издающие при движении мелодичный звук, отпугивающий змей.
Буер снял с нас громадную кучу проблем по доставке дерева, камней, глины. Однако, когда ехали налегке, сохранялся риск переворачивания, разгона и крушения рамы. По-хорошему, надо бы его переделать... Ничего решили проблему – несколько мешков с щебнем привязанные к раме в нужных местах навсегда прописались в качестве балласта. Тяговое усилие ворота, примерно, не меньше двух тонн, он вытаскивал буер из глубоких расщелин, куда мы дважды, не справившись с управлением, умудрились заехать. Нганго, я всё-таки через неделю научил управлять парусом. С видимым удовольствием он, стоя у паруса управлял духами ветра. Понимаешь ли, вбил себе в голову, что будто бы я их приручил. Да и пусть, я не стал его разубеждать. Жаль что он по-прежнему боялся спускаться в разлом.
Для ускорения подъёма глины из разлома мы изготовили кран с наклоняемой, А-образной стрелой установленной на задней площадке буера. В верхней части стрелы был установлен шкив, такой же установили на верхней части мачты. Верёвка проходила через оба шкива и наматывалась на ворот. Для того чтобы поднять мешок буер устанавливали задом к разлому и крепили верёвками, после фиксировали стрелу и поднимали груз вращая ворот, поднятый вверх мешок подтягивали к платформе. Кстати про мешок. Для этого я сшил не обычный, а хитрый – Биг-Бэг. Они появились в СССР как средство для транспортировки и перевалки цемента только в конце семидесятых. Двойной слой циновки, тройные швы из сухожильной нити, треугольные накладки для крепления строп, а в дно вшит высыпной цилиндрический клапан. Достаточно потянуть хитрый узел и глина разом высыплется вниз.
Лопарь* – морск. трос, канат у талей и снастей на судне
Треугольная вилка колеса Треугольная вилка колеса-2 Сборка деревянной фермы Тип балок фермы Соединения балок фермы без анкеров Упорный роликовый подшипник Балка усиленная Ферма квадратная усиленная Буер 17 век Деревянный велосипед Тип задней вилки буера Тип передней вилки буера Буер-1 Буер 18 век Мачты Буер на жел. дороге Сухопутная яхта Симона Стевина Тип платформы Буер площадка СССР Детали паруса тип джонка Такелаж A образная мачта A образная мачта-2 Парус типа Дельта Парус типа Дельта-2 Тормоз рычажный Биг Бэг Компоновка корпуса Компоновка корпуса с колёсами
К оглавлению
Получение шликера
Ярослав.
В двух словах шликер – это глина, разведенная водой до состояния, напоминающего густые сливки. Гипсовая форма, в которую наливают шликер, вбирает в себя воду. При этом слой глинистой массы равномерно оседает на внутренних поверхностях, образуя стенки будущего изделия. После высыхания полое глиняное изделие извлекают из формы, досушивают, а потом обжигают. Шликерное литьё известно более четырёх тысяч лет и появилось ещё в древнем Китае. Оно дает возможность с большой точностью передавать тончайшие детали, особенно когда нужно изготовить несколько одинаковых тонкостенных сосудов и применяется в массовом производстве изделий. Как раз то, что нам надо. Изделия сложной формы иным способом в наших условиях получить невозможно. С помощью шликера можно скреплять различные уже готовые детали из керамики. Вроде ничего сложного – кашеобразная, мягкая масса, состоящая из каолина, кварца и полевого шпата, а вот и нет! Хитростей масса. Начнём с того, что шликер – это не раствор, а суспензия на основе глины, для формования керамических изделий методом литья в гипсовые формы. Для каждого состава требуется своя влажность – для фарфора тридцать, тридцать три процента, для фаянсa чуть больше, а шликеры на основе красножгущихся глин вообще могут иметь влажность и вовсе более сорока процентов. Чем меньше влажность шликера, тем быстрее происходит формирование слоя керамической массы на поверхности гипсовой формы и меньше усадка и деформация при сушке. Поэтому для приготовления шликера с низкой влажностью в его состав вводят разжижители или электролиты – жидкое стекло, соду или поташ. Шликер даёт равноплотные по объёму изделия сложной формы. В отличие от прессования, частицы порошка при литье не испытывают нагрузки, не деформируются, укладываются плотно друг к другу, тем самым образуя ненапряженную регулярную микроструктуру и это очень важно для большеразмерных изделий. Качество изделий очень сильно зависит от свойств литейного шликера. Составная шихта должна иметь строго заданный состав, минимальную влажность, обеспечивающую необходимую текучесть, обладать оптимальной загустеваемостью и высокой фильтрующей способностью и при этом быть устойчивой против расслаивания при длительном хранении, дабы обеспечивать достаточную механическую прочность на изгиб отлитых изделий. Задачка даже для меня очень и очень непростая.
Днём таскаю глину, а вечерами провожу бесконечные эксперименты с подбором шихты, подогреванием состава, измельчением, процентным соотношением электролита. Чуть передержал, подогрел лишка и всё, шликер загустел, а если он очень жидкий, то изделия из такого выходят негодными. Качество шликера критически зависит от тонкости помола и температурного режима, и чистоты исходных компонентов. Мне пришлось провести колоссальную работу, чтобы подобрать вещественный и химический состав, рассчитать необходимую текучесть, устойчивость к расслаиванию и загустеваемости, обеспечивать прочность отливок за счет влагопроводности и плотности. Естественно, я ранее знал примерные составы, так что не с чистого листа работал. Но тут тонкостей масса – каолин обожженный, к примеру, повышает текучесть и фильтрующую способность, по сравнению с необожженным, каждый компонент влияет по-своему на температурный режим.
Отобрал три вида шликера. Первый – фарфоровый. Состав смеси в процентах: каолина – шестьдесят пять, кварцевого песка – пятнадцать и полевого шпата – двадцать. Предварительный обжиг компонентов способствовал их активации за счет процессов дегидратации, а также полиморфного превращения кварца. Высокая плотность суспензии способствует формированию наиболее плотной структуры отливки, что в свою очередь приводит к снижению усадочных явлений при сушке и обжиге и достижению высоких показателей. Затем шихту подвергал помолу в течении десяти часов. Полученную массу разбавлял водой и сливал на гипсовую плиту, накрытую тканью. На ней выдерживал массу в течение пяти часов. Полученные коржи сушил на слабом огне ещё десять часов и снова измельчал. Шихта готова. Подогретую шихту добавлял небольшими порциями к нагретой до кипения воде с разведённым электролитом, непрерывно перемешивая массу. Воды в мешалке тридцать пять процентов от общего веса шликера. На каждый килограмм шихты сорок сантиметров кубических раствора электролита. Начинаю медленно, помешивая руками, добавлять шликер. Чуть позже, для более интенсивного перемешивания подсоединяю мешалку к ветряку. Для каждой партии делаю замеры на вязкость, тягучесть, плотность раствора. В случае необходимости, для разжижения шликера добавляю электролит. Но есть одна тонкость: сода должна храниться в плотно закупоренных сосудах, иначе она начинает действовать как коагулятор.На первом этапе ввожу семьдесят процентов шихты и всю воду, а затем остатки шихты. Всё, шликер для фарфора готов.
Второй состав – терракота, что в переводе с итальянского 'жженая земля'. Терракота термостойка и допускает резкое охлаждение, что самым лучшим образом подходит для нанесения глазурей. Подобрать терракотовую массу для отминки и литья большого ума не надо. Память слава богу не дырявая. Шестьдесят процентов глины на сорок процентов воды, плюс электролит добавить – ноль целых две десятых процента соды и ноль целых три десятых процента жидкого стекла. Для глины только тонкий помол, в состав порошка добавить четвёртую часть шамота, который нужен для снижения усадки и повышения плотности отливок. Сам шамот в изобилии имелся кругом, масса лопнувших черепков и кирпичей – обжёг второй раз, измельчил и готово.
С подбором шихты для литейной майоликовой массы пришлось ещё пару дней покопаться, но справился. Глина тугоплавкая – тридцать восемь процентов, легкоплавкая – двадцать один процент, стекло – восемь, кварцевый песок – двадцать один, нефелин-сиенит – пять и шамота – семь процентов. Для отмучивания глины мы использовали три конических бочки с кранами-заглушками. Бочки установили на разной высоте так, чтобы воду можно было сливать, открывая их попеременно. В каждой по три крана. Система слива для мульчи позволяла избежать перемешивания слоёв и не строить сложных систем очистки. Чтобы ускорить процесс оседания глины, в раствор добавляли поташ. Отстоявшийся глиняный раствор из верхнего слоя захватывал черпаком и перекладывал в длинное корыто, где из него испарялась лишняя влага. После того, как глина приобрела консистенцию густого теста и перестала прилипать к рукам, делал из неё шары и складывал их в маленькую бочку. Прежде чем использовать тесто, ему нужно отлежаться пару дней, дозреть. Самая чистая глина после отмучивания шла на обогащение каолина. Её сперва снова высушивали, измельчали, а после растворяли в горячей воде с добавлением электролита, смеси жидкого стекла и соды. Полученный раствор, постоянно помешивая, упаривали в котле до сметанообразного состояния – считай чистый каолин. Использовали только на самые ответственные изделия и глазури. Воды не напасёшься.
Плотность шликера определял пикнометрическим методом. Метод основан на использовании сосуда с точно известным объемом – пикнометра. У меня это колбы объемом сто миллилитров, с нанесенной на узком горле риской точного объема. Кстати, практически на все мои приборы сразу накладывает свои лапки Иван Сергеевич. Не жалко, у него там тоже всё кипит и клокочет, тем более он мне здорово помогает и большую часть рутинных измерений я перекладываю на его плечи. Заполнил пикнометр кипяченой и остуженной дистиллированной водой.
Отливка шликера в гипсовые формы вновь потребовала вычислений и доочистки гипса. Для получения гипса мы измельчали ольгдамит и обжигали его на открытом огне в широких поддонах. Полученный гипс измельчали и промывали, продували воздухом и фильтровали, после чего высушивали. Для дальнейшего использования его нужно обжигать. При повышении температуры, но не более чем до ста восьмидесяти градусов, гипс теряет часть воды, переходя в полуводный – жжёный гипс, известный как алебастр, пригодный для дальнейшего применения как вяжущее вещество. Если обжиг вести при температуре выше двухсот двадцати, то получается безводный гипс, который влагу не поглощает и не 'схватывается' при смешивании с водой – мёртвый гипс.
Прежде, чем мы приступили к литью, в течении недели мы провели большую подготовительную работу: выполнили чертежи моделей, изготовили из молочая модели будущих изделии, отлили из гипса разъемные литейные формы и сбили для них деревянные опалубки. Изготовление опалубки, стержней, разборных форм, расчёт и проектирование литников и литниковых каналов являлся самой трудоёмкой частью работы. Мартин для быстрого изготовления моделей пользовался пропорциональным циркулем. Большая часть форм состояла из двух половин – верхней и нижней. Но были опалубки, собираемые из трёх, и были даже из семи элементов и внутренних стержней. Для изготовления заготовок мы применяли как сливной, так и наливной способы. В первом случаем шликером заполняют гипсовую форму, отбор влаги происходит на поверхности соприкосновения формы и шликера. После образования заданной толщины стенки заготовки избыток шликера сливают. При наливном способе его заливают между двумя гипсовыми поверхностями, с которых происходит отбор влаги. При этом полость между двумя гипсовыми поверхностями образует соответственно внутреннюю и наружную конфигурацию заготовки. Наливной способ – это более интенсивный способ литья; он позволяет получать изделия меньшей влажности и более сложной формы, что требует более сложных литьевых форм и избыточного давления, которое нам сможет обеспечить лишь установка центробежного литья. Хорошо, что хоть её делать не нужно, я позаботился о ней при изготовлении вальцов. Для наглядности разные части форм подписывали и пигментами подкрашивали гипсовый раствор. Для нижней половины в розовый цвет, а для верхней – в зелёный. Со стороны донышка в основании модели оставили неглубокий полусферический вырез – для устойчивости. Иван подобрал разъединительную смазку из жиров, гуммиарабика, каучука и масла баобаба сплавленных на водяной бане.
В качестве эксперимента, после отработки состава и технологии, отлил корпус центробежного, нагнетательного вентилятора и крыльчатку. Корпус две детали – крышка и узкий каркас с невысокими стенками радиусом метр тридцать. Сама крыльчатка так же из керамики, но элементов в ней больше. Целиком отливать её я не решился. Основа – тонкий с рёбрами жёсткости диск с выемками под шестнадцать лопастей, сверху на них одевалось вогнутое вниз, словно горлышко кувшина, кольцо. Лопасти с крышкой и основой соединил шликером, а после слегка, через гипсовые формы подпрессовал.
Сушил сперва два дня на солнце, а после сутки горячим воздухом в печи. Сутки Карл! Сутки непрерывной работы мехами. После этого никто из нашей компании не заикался о ненужности ветряного привода. Дальше по накатанной: первичный обжиг в печи, покрыл глазурью, а затем второй обжиг – утильный. Печь то как раз под размер вентилятора делал. Ничего сверхъестественного, лишь как следует продумать заранее, чего ты хочешь.
К этому времени мы уже запустили ветряк, и проблема с измельчением шихты была решена. Мы сбили формы и отлили массу мелких деталей для печей: трубки и трубы, тигли, сосуды, мензулы, фитинги для труб Y и T образного типа, разных размеров и диаметров, муфты, переходники, крышки, дверки, ручки и ещё куча мелочи, из больших деталей – два корпуса флотационных пульсирующих машин, кристаллизатор, корпуса перегонных аппаратов и большого автоклава, цилиндрический корпус и диски ратификационной колонны, элементы плоской спирали для винтового сепаратора, реторты, котлы и вкладыши для мельниц – всего более трёх сотен позиций, плюс полторы сотни кувшинов, стаканов, свистулек, игрушек, плошек и тарелок себе на хозяйство и на продажу в селение кевенги.
Когда у тебя есть формы, изделия как пирожки можно печь. Отлили деталь и сразу на просушку, а к вечеру можно новую отливать. Изделия делали с двойным, а некоторые и с тройным резервированием. Мало ли потрескаются, а времени на длительные эксперименты с обжигом у нас не было, печи всё под эксперименты со стеклом заняты.
Вискозиметр Осквальда Шликерное литьё Типы шликерного литья Процесс шликерного литья Процесс шликерного литья-2 Процесс шликерного литья-3 Инструмент Гипсовые формы
Химия
Иван Сергеевич.
После того, как Ярослав Александрович провёл глазурный обжиг, мне досталась большая часть изделий оттуда: три пузатых пифоса литров на двести каждый, трубки, реторты, тигли и масса другой мелочёвки. Пифосы, без сомнения, самая ценная часть приобретений. Под каждый из них сложили печь, а после установили сверху. Они довольно тяжёлые, и чтобы их установить мне понадобилась помощь. Сосуды ребристые, за счёт верёвки, обвивавшей и выгоревшей при обжиге. Как оказалось это сделано вовсе не для облегчения веса, а для того, чтобы предотвратить растрескивания большого сосуда при обжиге. Толстые стенки и дно пифоса хорошо накапливали тепло и позволяли поддерживать более равномерную температуру внутри. Дистиллятор, собранный на его основе, за счёт своей глазурованной поверхности уменьшал потери воды до ноля, а новый, целиком керамический охладитель значительно поднимал КПД всего процесса. Старая печь пошла на слом, а вместо неё мне сложили утеплённую перлитом рекуперативную печь с дымовыми трубами, дверками на салазках, поддувалами, колосниковыми решётками. Печи сложили с общей топкой, оборудованной тремя перегородками: справа реторты для дистилляции и сухой перегонки древесины, слева – варочная панель с тремя конфорками. Ярослав Александрович предусмотрел для них квадратные варочные панели из керамики, конечно, не из чугуна. Откуда такое богатство? Толстые, трапециевидного сечения кольца, вкладываемые друг в друга, позволяли удерживать самые тяжёлые реторты, к ним даже крышечка имелась. Единственная деталь из железа – крюк для поддевания эти тяжёлых, по два с лишним килограмма колец, да и то на деревянной ручке. Дефицит, батенька... Дефицит. Печь здорово экономила дрова, при дистилляции за сутки я получал вместо двухсот литров воды триста пятьдесят. КПД улучшилось почти вдвое, а рекуперативная печь длительного горения позволяла на одной закладке дров выпаривать древесину всю ночь. Закладку из сердцевины баобаба меняли четыре раза в сутки. Я уже выявил потребное количество дров и температурный режим. Наладили более эффективное охлаждение. На раму на высоте двух метров установили две закрытые, обмазанные глиной для уменьшения потерь воды от испарения, конические бочки из баобаба. Его оказалось легче всего обработать. Наскоро схваченные верёвкой вместо обручей, они и составили основу проточной системы охлаждения. Вода из бочек, соединенных по низу трубой, поступала в керамический охладитель. Там она нагревалась и стекала вниз, в подземный холодильник-трубу, заполненный до половины галькой. За счёт большой площади окатышей происходило интенсивное испарение и охлаждение воды.Из трубы она попадала прямиком в колодец-термос, похожий по устройству на аккумулятор холода. Кольца из самана образовывали внутреннюю стену, а между ней и грунтом засыпали гальку и залили водой, которую по мере испарения подливали. Такой холодильник позволил уменьшить потери воды на испарение, да и время охлаждения сократилось в два раза, также понизили температуру воды градусов до пятнадцати. Резервуар мы расположили прямо под бочками, рядом установили журавль, так что каждые два часа мне приходилось зачерпывать ведро воды из резервуара и опрокидывать его в бочку. Ведро-непроливайку мне сделал Павел Петрович. Он человек, без сомнения, достойный уважения. Необходимость каждые два часа заполнять бочки утомляла, за целый день так устаёшь, словно вагон угля разгрузил. Но другим не легче, так что старался сам, ну а позже, когда мы добавили ещё две бочки и составили график ночных работ, стало куда легче.
Для лаборатории оборудовали навес и стол.Стол необычный – из пальмы дум, предварительно выдержанной несколько дней в глиняном растворе чтобы, значит, не сгорел. Под каждую реторту или котёл обязательно универсальная подставка – треножник из кольца и коротких, конических ножек. Деревянные штативы для поддержки труб имели вкладыши-прокладки. Всё продумали, дабы пожара избежать. Даже маты навеса хорошенько пропитали глиняной мульчей, да ещё раз в два дня Нганго приставлял лестницу и дополнительно проливал их. Примитив-лаборатория была оборудована весами, мензурками, ретортами, часами и песочными, и большими солнечными и соседствовала с печью, где мой коллега занимался подбором годного для глазурей состава шихты. Так что и столом, и приборами мы делились с друг другом, да и помогали по мере сил. Два химика всё же лучше, чем один. У меня тут и топчан был, над которым висел график и план работ, диаграммы и единственный справочник, который мы с Ярославом Александровичем составили и постоянно пополняли, вытаскивая из памяти новые для этого мира знания.
К слову сказать, все эти замечательные вещи появились далеко не сразу, и как только просохла печь я приступил к выделению поташа из золы – у нас её скопилось не меньше тонны, и соды – короб золы солероса давно дожидался, когда о нём вспомнят. Сухие остатки костра состоят в основном из негорючих минеральных компонентов, они и придают белый цвет золе. Первый шаг – бросить золу в котел с водой. Черная недогоревшая угольная пыль всплывет на поверхность, а те древесные минералы, что нерастворимы, в виде осадка выпадут на дно. Но нам то нужно заполучить те, что растворяются. Нам надо слить с поверхности и удалить угольную пыль, а водный раствор перелить в другую посуду, стараясь, чтобы туда не попал осадок. Затем эту воду можно или кипятить, или разлить в широкие мелкие сосуды и оставить на солнце. После выпаривания там останется белый кристаллический осадок, похожий на соль или сахар, вот это и есть поташ. Словечко то английское и означает, буквально, горшок золы. Зола потребна свежая, выгоревшая дотла, не залитая дождем, в такой есть нужные вам растворимые минералы. Ну а у нас тут какие дожди-то? Белый кристаллический осадок на самом деле состоит из нескольких компонентов, но главный, добытый из древесного пепла – это карбонат кальция, а вот если вместо дров сжечь охапку водорослей или того-же солероса и повторить выпаривание, то мы уже получим не поташ, а кальцинированную соду, или карбонат натрия. В тканях этих растения совсем другой химический состав. Однако, это самый простой способ получения, а Ярослав Александрович недвусмысленно намекнул, что поташ и сода ему нужны максимально очищенные и много, а значит к процессу очистки надо подойти со всей тщательностью.