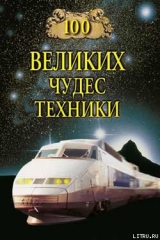
Текст книги "100 великих чудес техники"
Автор книги: Сергей Мусский
сообщить о нарушении
Текущая страница: 4 (всего у книги 42 страниц)
Печатные машины
Как правило, первопечатником называют немца Иоганна Гутенберга. Хотя есть сведения, что еще в 1045 году китаец Пи Чень, член императорского суда, придумал разборный шрифт.
Еще раньше, в IX веке на востоке – в Китае, Тибете – был известен способ печатания с деревянных досок, на которых гравировались целые страницы рукописи. Этот способ в Европе получил название «ксилография». Студент Страсбургского университета Иоганн Гутенберг вместе с несколькими компаньонами занялся изготовлением ксилографических книг. Ему пришла идея гравировать не целые страницы сразу, с каждой из которых можно было снять очень мало качественных оттисков, а делать отдельные буквы и потом из них, словно из кубиков, складывать строки. Он придумал следующий способ изготовления шрифта сначала на торце металлического бруска – пуансона – гравировали обратное выпуклое изображение буквы, потом выбивали ее на мягкой медной пластинке. Затем эту пластинку – матрицу – вставляли в нижнюю часть полой трубки, а через открытый верх заливали специальный сплав, который позднее стали называть гартом. В результате можно было сделать сколько угодно точных копий пуансона – литер. А из литер уже строка за строкой набиралась книга. Только на пятом десятке лет жизни Гутенберг сумел изготовить нужное количество литер – первую наборную кассу и сделать печатный станок.
Способ получения оттисков с помощью таких форм называется высокой печатью. Изготовить такие формы несложно. Ведь достаточно лишь получить с них оттиски. Для этого нужно нанести ровный тонкий слой краски на печатающие элементы и надавить ими на бумагу. Высокую печать выгодно отличает нетребовательность к краске. Она может быть практически любого химического состава: и на жировой основе, и на основе водных и спиртовых растворителей.
Позднее изобрели иную разновидность высокого способа – флексографическую печать. Здесь применяются резиновые или полимерные печатные формы. С их помощью добиваются хороших оттисков не только на бумаге, но и на других материалах, таких как алюминиевая фольга, целлофан, гофрокартон.
Со временем, естественно, росли и требования к качеству печати. Возникла необходимость в воспроизведении на бумаге полутоновых изображений всей цветовой гаммы. Решение пришло вместе с изобретением глубокой печати. При этом способе печатающие элементы делают не выше, а ниже пробельных, причем глубина их различна. Чем темнее должен быть тот или иной участок оттиска, тем глубже соответствующий ему элемент печатной формы, толще слой заполняющей его краски и тем больше ее перейдет с формы на оттиск.
Сегодня наиболее распространены два типа печатных машин – листовые и офсетные. В листовой печатной машине талер, на котором закрепляется печатная форма, непрерывно движется вперед и назад. В то же время опускается и прокатывается по форме валик красящего аппарата и смазывает ее краской. Над талером вращается большой печатный цилиндр. Опускаясь, он прижимает к форме чистый бумажный лист, на котором остается отпечаток текста и рисунков. Листовая печатная машина все делает самостоятельно. Мастер только нажимает кнопку включателя. Установленные на машине самонаклады – захваты с резиновыми присосами сами берут с верха стопы бумаги только один лист и аккуратно кладут его на талер. А другие самонаклады прижимают отпечатанный лист и также осторожно укладывают на приемный стол. Машина сама следит за тем, правильно ли она работает. Стоит лишь присосам захватить по ошибке из стопы не один лист, а два, как машина тотчас останавливается.
Примером может служить листовая печатная машина «Speedmaster SM 102» фирмы «Хайдельберг», предназначенная для печати коммерческой продукции, этикеток, печати на пленке и на других упаковочных материалах. Оснастив эту машину соответствующими дополнительными устройствами, можно печатать этикетки на особо тонкой бумаге.
В них применено около двух тысяч новых узлов и деталей. Инженеры фирмы получили более сорока патентов на изобретения, сделанные в ходе конструкторской проработки.
Во время исследовательского этапа работы были проведены маркетинговые исследования, направленные на выявление потребностей пользователей. Результаты показали, что в большинстве профессиональных типографий и печатных центров применяются листовые офсетные машины формата 70x100 сантиметров. Поэтому специалисты фирмы сосредоточили усилия на повышении производительности именно этого класса машин. Им удалось добиться производительности 15000 оттисков в час. Высокая производительность новых печатных машин в большой степени определяется рабочей скоростью. Особое внимание было уделено сокращению времени на подготовку к печати и обслуживание машины.
На «Speedmaster SM 102» используется новое поколение самонакладов. Эти самонаклады оборудованы удлиненными направляющими для проводки отдельных листов над передними упорами на накладной стол. Листы тормозятся непосредственно перед передними упорами до скорости, составляющей 25 процентов от скорости машины, что позволяет точно выравнивать листы даже малой массы при работе на высоких скоростях. Подъем стапеля регулируется автоматически в зависимости от толщины бумаги. Присосы вакуумной головки предварительно устанавливаются по определенной кривой в зависимости от свойств запечатываемого материала, что обеспечивает высокую производительность. Стабильность подачи бумаги достигается благодаря малому ходу качающихся присосов. Прозрачное ограждение позволяет снизить уровень шума.
Оснащение самонаклада листорезальным устройством – это альтернатива обычному листовому стапелю, позволяющая снизить стоимость запечатываемого материала.
В настоящее время наиболее распространен офсетный способ печати. Он отличается широкими возможностями художественного оформления издания, сравнительной дешевизной изготовления печатных форм, довольно высокой скоростью печати и рядом других положительных качеств. По оценкам многих специалистов, в ближайшее время классический офсетный способ печати будет продолжать доминировать в мировой практике.
Офсетные машины работают гораздо быстрее обычных плоских печатных машин. Внутри такой машины вращается еще один печатный цилиндр – офсетный, покрытый резиной. Он пробегает по форме раньше бумажного листа. Отпечаток шрифта и иллюстраций сперва переводится на эту резину, а уже с нее на бумажный лист. В таких машинах бывает обычно по несколько секций, которые заправляют различными красками. Бумажный лист поочередно проходит через все секции, и на нем появляется либо разноцветный шрифт, либо цветная картинка.
Листовая печатная машина дает за час до 15 тысяч оттисков. Офсетная – десятки тысяч. Но печатников, выпускающих газеты и журналы, эта скорость не удовлетворяет.
Более высокую скорость обеспечивают ротационные печатные машины. Первую такую машину разработал в 1904 году немецкий инженер Э. Мертенсон. В ротационной печатной машине все главные детали имеют цилиндрическую форму. Это упрощает конструкцию аппарата и позволяет значительно увеличить скорость печатания.
Такую машину заправляют бумажной лентой длиной 6-7 километров, намотанной в огромный рулон. Ротационная машина работает с огромной скоростью. Бумажная лента пробегает с быстротой поезда под вращающимися валами со стереотипами, по которым с той же быстротой уже прокатились валы с краской. На бумаге отпечатывается сперва одна сторона газетного или журнального листа, а затем другая. Машина сама отрезает отпечатанные листы, фальцует (сгибает), сама выбрасывает готовые пачки на конвейер.
Самая современная и эффективная ротационная машина – «Экоман» (Ecoman) фирмы «MAN Roland». Одно из важнейших преимуществ этой машины – широкие возможности варьирования ее компоновки. Благодаря гибкому построению на этой машине можно организовать эффективное производство практически любой газетной продукции.
Восьмиярусное расположение печатных секций – составная часть системы «Экоман». Такое построение в сочетании со сдвоенным фальцаппаратом делает машину идеальной для печати больших тиражей. Для печатания коммерческой продукции машину можно оснастить ИК-сушкой или сушкой горячим воздухом.
Конструкция бумагопроводящей системы обеспечивает постоянное натяжение бумажного полотна. Для высококачественной четырехкрасочной печати используется дополнительное автоматическое устройство контроля и регулировки натяжения бумажного полотна. Проводка бумажного полотна может быть выбрана с левым или правым направлением. Это позволяет оптимизировать путь бумажного полотна. При двустороннем запечатывании двух полотен в одну краску оснащается двумя лентопроводящими системами.
Машина «Экоман» в стандартном исполнении оснащена рулонной зарядкой, отличающейся простотой конструкции и надежностью работы.
Компактный пленочный красочный аппарат обеспечивает быструю смену краски, простоту обслуживания, высокое качество печати. Для лучшей очистки красочного ящика предусмотрено его разделение на две-четыре откидывающиеся части.
В машине «Экоман» применяется увлажняющий аппарат разбрызгивающего типа, в котором передаточный валик расположен между накатным валиком и растирочным цилиндром увлажняющего аппарата.
В «Экоман» все узлы машины (рулонная зарядка, печатные секции, фальцаппарат) объединены в общую систему управления – PECOM, которая производит централизованную обработку сигналов от исполнительных механизмов, после чего подает соответствующие команды.
Система управления позволяет использовать станцию технического планирования продукции TPP для обработки заказов. Эта станция проводит подготовку к печатному процессу, начиная от обработки сведений о характере продукции, о плане загрузки машины и заканчивая подачей необходимых команд исполнительным механизмам.
Не так давно полиграфические машины годились только для многократного воспроизведения одного и того же изображения. После изобретения цифровой печати положение изменилось. Цифровая печатная машина работает под управлением компьютера и по принципу действия аналогична лазерному принтеру. С помощью компьютера можно быстро вносить изменения в печатную форму после каждого оборота формного цилиндра и получать на выходе в той или иной степени отличающиеся экземпляры оттисков. Цифровой способ используется главным образом для печатания небольших тиражей (даже одного экземпляра) или в целях оперативной полиграфии.
Зерноуборочные комбайны
Давно ушло в прошлое время, когда хлеб убирали вручную: жали серпами, связывали в снопы, обмолачивали цепами, отделяли зерно от соломы и половы на ручных веялках. Чтобы вручную за день сжать хлеб на одном гектаре земли, требовалось тридцать жнецов, а чтобы вымолотить зерно из колосьев и отделить его от соломы – еще сорок человек.
Для облегчения этих тяжелых и трудоемких работ были созданы машины: жатки, скашивающие хлеб; молотилки, обмолачивающие зерно; сортировки, отделяющие полноценное зерно от негодных семян и семян сорняков, очищающие зерно от примесей. А потом жатку, молотилку и сортировку объединили в одну машину, поставили ее на колеса – и появился зерноуборочный комбайн. Первую такую машину в 1868 году разработал русский изобретатель А.Р. Власенко. Сначала такие машины за собой возил трактор, а позднее они стали самоходными.
Комбайнер работает сейчас в значительно более комфортных условиях, чем раньше. Кабина оборудована кондиционером, отопителем, вентиляционной установкой, очищающей подаваемый воздух, электрическим стеклоочистителем, тонированными стеклами, солнцезащитными козырьками, фарами для работы в ночное время, зеркалом заднего вида, термосом для питьевой воды.
На комбайнах марки «Дон» впервые в нашей стране были применены бесконтактные электронные устройства для контроля за всеми основными сборочными единицами и агрегатами.
Система автоматического контроля технологического процесса и состояния важнейших агрегатов комбайна «Дон» обеспечивает измерение частоты вращения основных рабочих органов комбайна и скорости его движения. Она также выявляет отклонения от номинала частоты вращения валов или режимов двигателя, гидросистемы, молотильного аппарата и других агрегатов от нормы и предупреждает об этом комбайнера с помощью светового табло и звуковой сигнализации.
Световое табло установлено в кабине на передней стенке отсека кондиционирования и вентиляции, здесь же расположен блок переключателей электрооборудования комбайна.
На комбайнах последнего поколения для контроля основных эксплуатационных параметров и управления технологическим процессом широко используются компьютерные устройства.
А вот как работает современный комбайн. Сначала полосу стеблей убираемой культуры захватывают лопасти мотовила и подводят к режущему аппарату. Срезанные стебли подаются мотовилом к шнеку жатки.
Шнек, имея спирали правого и левого направления, перемещает срезанные стебли от краев к центру жатки, где расположен пальчиковый механизм. Пальчиковый механизм шнека захватывает их, а также стебли, непосредственно поступающие на него, и направляет в окно жатки, из которого масса отбирается битером проставки и передается к транспортеру наклонной камеры, который направляет ее в приемную камеру молотилки.
В комбайнах используют три типа молотильных аппаратов: бильный, штифтовый и аксиально-роторный. Основное назначение молотильного аппарата – выделить из колоса все зерна, по возможности не повреждая их. При этом стремятся и к минимальным повреждениям стеблей, чтобы не затруднять сепарацию зерна на решетах очистки и соломотрясе.
В своей книге «Зерновые комбайны» А.Ф. Морозов отмечает, что в процессе обмолота должна быть разрушена естественная связь между семенами, пленками и колосковыми чешуйками. Обмолот в молотильном устройстве происходит в результате многократных ударов по стеблям и колосу при протаскивании массы через молотильный зазор между барабаном и подбарабаньем (декой). Барабан, вращаясь, захватывает массу бичами, нанося при этом по ней удары, и продвигает ее по молотильному зазору. Скорость перемещения массы зависит как от скорости вращения барабана, так и от величины молотильного зазора. Верхний слой стеблей движется значительно быстрее нижнего, соприкасающегося с неподвижной декой.
Обмолот в штифтовом молотильном устройстве происходит в результате многократных ударов по стеблям и колосу при протаскивании массы между штифтами подбарабанья.
В аксиально-роторном молотильно-сепарирующем устройстве хлебная масса обмолачивается также благодаря воздействию на нее бичей, но в процессе обмолота она совершает винтообразное движение.
Молотилки отечественных комбайнов «Дон» и «Нива» выполнены по классической схеме, наиболее распространенной в зарубежных комбайнах. В нее входят молотильное устройство с одним бильным барабаном и решетчатым подбарабаньем, активный отбойный битер, клавишный сепаратор соломистого вороха, двухстанная решетная очистка.
Из молотильного аппарата хлебная масса выходит в виде двух фракций – соломенного и зернового вороха. Соломенный ворох, содержащий в основном крупную солому и часть зерна, попадает на соломотряс, на котором выделяются оставшееся зерно и мелкие соломистые частицы, а солома по соломотрясу поступает к копнителю.
В зависимости от конструкции молотильного устройства и условий уборки в соломе, поступающей на соломотряс, содержится от 5 до 30 процентов общего количества зерна, проходящего через комбайн.
В отечественных комбайнах применяются соломотрясы только клавишного типа. Принцип работы такого соломотряса основан на выделении зерна из слоя соломистого вороха в результате встречных ударов, наносимых клавишами по падающей на них массе.
При сходе с соломотряса солома захватывается граблинами соломонабивателя и направляется в камеру копнителя. По мере наполнения копнителя растет усилие подпрессовки соломы, которое воздействует на клапан аварийного заполнения и включает сигнал полного заполнения копнителя. Если механизатор почему-либо не заметил этого сигнала и не сбросил копну, то включается автомат сброса копны.
Зерновой ворох, выделенный через подбарабанье, а также зерно и мелкие соломистые частицы, выделенные на соломотрясе, поступают на транспортную доску, которая подает этот ворох на очистку.
На решетах очистки, обдуваемых вентилятором, зерно окончательно отделяется от соломистых примесей. Чистое зерно, прошедшее через оба решета, поступает по скатной доске решетного стана в зерновой шнек и транспортируется элеватором в бункер.
«Недомолоченные колоски, сходящие с нижнего решета и с удлинителя верхнего решета вместе с примесью свободного зерна и половы, – пишет А.Ф. Морозов, – попадают в колосовой шнек и перемещаются шнеком и элеватором к автономному домолачивающему устройству, где выделяется оставшееся в колосках зерно.
Образовавшийся после домолота ворох поступает в горловину распределительного шнека, который сбрасывает его на конец транспортной доски (благодаря специальной конструкции кожуха распределительного шнека ворох равномерно распределяется по ширине молотилки). При этом труднообмолачиваемые колоски могут несколько раз циркулировать по контуру "домолот-очистка", пока не произойдет их полный вымолот.
Мелкая соломистая часть вороха транспортируется воздушным потоком и решетами к половонабивателю, который подает ее в камеру копнителя или в шнек половоотборника измельчителя.
При использовании навесного измельчителя солома с соломотряса поступает непосредственно на измельчающий аппарат и после измельчения молотковыми ножами выбрасывается через дефлектор в тележку или на поле. При этом она проходит через нижний люк и лопатки разбрасывателя, которые можно устанавливать в одно из двух положений: для разбрасывания по полю или укладки в валок».
К зерноуборочным комбайнам выпускаются дополнительные приспособления, позволяющие собирать разные сельскохозяйственные культуры. Так, кукурузоуборочный комбайн срезает высокий кукурузный стебель, отделяет от него початок и дробит стебель на мелкие кусочки (после дополнительной обработки из этой массы готовят корм для скота – силос).
Льноуборочный комбайн сначала осторожно вытягивает нежные стебельки льна из земли, стальными гребенками счесывает с них коробочки с семенами и листочки, а потом связывает стебельки в снопы.
Существует и специальный комбайн для уборки сахарной свеклы. Стальными пальцами он захватывает ботву, выдергивает растение из грядки, отрезает ножом зелень и стряхивает прилипшую землю.
Картофелеуборочный комбайн сначала подкапывает большой пласт земли и осторожно размельчает его, чтобы не повредить клубни. Затем, перемещая и одновременно встряхивая, просеивает землю на прутковом транспортере, освобождает картофель и подает его в кузов грузовика.
Помимо перечисленных комбайнов инженеры создали и продолжают совершенствовать машины для уборки других видов зерновых и овощей.
Микромеханика
Точная механика родилась еще в XVII веке – с появлением стенных и настольных часов. Она не потребовала качественного технологического скачка, поскольку использовала традиционные приемы, но только в более мелких масштабах. И сегодня, как ни малы здесь детали, их еще можно изготовлять по общим стандартам, работая теми же инструментами и на тех же станках – пусть самых прецизионных, – применяя обычные способы сборки изделий.
«Ключевым тут является, пожалуй, механический обрабатывающий инструмент, – пишет в журнале «Техника – молодежи» Борис Понкратов. – Его возможности и ставят пределы миниатюризации. Но в этих пределах точная механика переживает ныне бурный расцвет. Она все шире внедряется в самую массовую продукцию – фотоаппараты, аудио– и видеотехнику, дисководы и принтеры для персональных компьютеров, ксероксы – не говоря уж о различном специальном оборудовании, например, для состыковки волоконно-оптических линий связи.
Лазерная микрообработка одна занимает целый диапазон, хотя, надо сразу сказать, самостоятельного значения не имеет: принципиально новых операций тут немного. В основном речь идет о пайке микросхем и создании отверстий различной формы (скажем, в фильерах для получения сверхтонких волокон из синтетических смол). Зато настоящего революционного технологического перевооружения требует следующий шаг – микромеханика. Размеры микромеханических устройств таковы, что для их создания недостаточно малых и сверхмалых устройств. В качестве критерия возьмем минимальные размеры объектов, с которыми способна манипулировать данная технология. Для упрощения картины округлим величины с точностью до порядка. И нанеся их на масштабную шкалу, получим своего рода спектр, где каждая технология занимает определенный «диапазон» (примерные минимальные размеры даны в миллиметрах): классическая точная механика – 1, лазерная микрообработка – 0,01, микромеханика и микроэлектроника – 0,0001, нанотехнология – 0,000001».
Рубеж поистине роковой для любых механизмов – расстояния менее 100 нм. Тогда заметно «слабеют» законы классической механики, и все больше дают себя знать межатомные силы, тепловые колебания, квантовые эффекты. Резко затрудняется локализация элементов устройств, теряет смысл понятие траекторий их движения. Короче, в подобных условиях вообще нельзя говорить о «механизмах», состоящих из «деталей».
Микромеханике повезло: ей с самого начала удалось устроиться «на плечах гиганта» – микроэлектроники, получив от нее практически готовую технологию массового производства. Ведь отработанная и постоянно развивающаяся технология сложнейших электронных микросхем лежит в том же диапазоне масштабов. И точно так же, как на одной пластинке кремния получают многие сотни готовых интегральных схем, оказалось возможным делать разом несколько сот механических деталей. То есть наладить нормальное массовое производство.
Кремний, используемый в микроэлектронике, стал основным материалом и для микромеханизмов. Тем более что здесь открылась замечательная возможность создавать и те и другие структуры в комплексе, в едином технологическом процессе. Производство таких гибридов оказалось настолько дешевым, что некоторые образцы быстро нашли применение в производстве самой массовой коммерческой продукции, например, кремниевый акселерометр, которым теперь снабжена одна из известных систем безопасности в автомобилях – надувной мешок.
Инерционный датчик этого прибора спроектирован Ричардом Мюллером из Калифорнийского университета. В общих чертах конструкция предельно проста: кремниевый стерженек диаметром в несколько микрон подвешен над отверстием, проделанным в кремниевой же подложке. Когда возникает ускорение, стерженек с подведенным к нему электрическим потенциалом начинает вибрировать и индуцирует сигнал, поступающий на обработку в микропроцессор, расположенный в десятке микрон по соседству. Достаточно резкое падение скорости (в момент удара при аварии) мгновенно фиксируется акселерометром, и он выдает команду на наполнение воздушной подушки в центре рулевого колеса, предохраняющей водителя от самой типичной травмы – удара о руль или ветровое стекло.
Японская корпорация «Тошиба» создала электромагнитный двигатель диаметром 0,8 миллиметра и весом 4 миллиграмма. Мощность его, разумеется, невелика, но достаточна для миниатюрных роботов, разработкой которых сейчас упорно занимаются ведущие компании страны под общим руководством министерства экономики и промышленности. Помимо «Тошибы» главную скрипку в этой программе играют корпорации «Мицубиси электрик» и «Хитачи». Длина разрабатываемых ими роботов – от сантиметра до нескольких миллиметров. Человек будет заглатывать капсулу с таким устройством, и после растворения ее оболочки аппарат, повинуясь радиосигналам и вложенной в него программе, начнет самостоятельное движение по кровеносным сосудам, желудочно-кишечному тракту и другим путям.
Миниатюрные роботы предназначены для диагностики, проведения микроопераций, для доставки лекарств точно по назначению и в нужное время. Их предполагают использовать также для ремонта и смены батарей у искусственных органов.
Немецкая фирма «Микротек» уже создала прототип медицинского инструмента нового типа – миниатюрную «подводную лодку» для плавания по кровеносным сосудам. Под управлением врача она способна выполнять некоторые операции. Длина этого автономного зонда – 4 миллиметра, а диаметр – 0,65 миллиметра. Двигателя у него нет, винт приводится во вращение с помощью внешнего переменного магнитного поля, которое позволяет развивать скорость до одного метр в час. В дальнейшем микрозонд оснастят фрезой для снятия холестериновых бляшек со стенок сосудов. Он сможет переносить капсулы с лекарством в нужное место. Предлагается и еще один вариант – размещать на таких микроаппаратах генераторы ультразвука. Просвечивая органы пациента изнутри, врачи получат информацию, остающуюся недоступной при обычной диагностике.
Нашли применение и еще несколько скромных, но полезных микроприборов – например, встроенный непосредственно в подшипник измеритель скорости вращения или внутренние датчики артериального давления, сердечного ритма, содержания сахара в крови и других параметров организма, передающие информацию наружу радиосигналом.