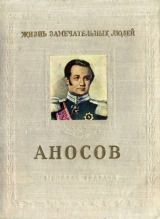
Текст книги "Аносов"
Автор книги: Илья Пешкин
Жанр:
Биографии и мемуары
сообщить о нарушении
Текущая страница: 5 (всего у книги 18 страниц)
Все делалось «втемную», никто не знал, что происходит с металлом. Лишь в последней четверти XVIII века был открыт кислород. Химия только отвоевывала позиции у алхимии. Процесс горения объясняли тем, что из горючего материала будто бы выделяется таинственное вещество «флогистон». Флогистонная теория держалась до самого конца XVIII века (и даже позднее). Решительный удар по ней, как известно, нанес великий русский ученый М. В. Ломоносов.
После того как М. В. Ломоносов заложил основы современной химии, наметился и научный подход к объяснению явлений, происходящих при восстановлении железа и при образовании из него столь различных по своим свойствам материалов, как чугун, сталь и железо. Это могло подсказать и решение вопроса, каким образом легче и быстрее переделывать чугун в сталь.
Задача эта становилась все более актуальной, так как старые, малосовершенные методы не могли больше обеспечить получение в необходимых количествах железа и стали.
Гениальное изобретение И. И. Ползуновым паровой машины, возникновение машинного производства, развитие железных дорог требовали организации массовогоизготовления железа и стали.
Карл Маркс в «Капитале» писал:
«Увеличение размера двигательных машин, передаточного механизма и рабочих машин, увеличение сложности и многообразия, более строгая правильность составных частей рабочей машины, возрастающие по мере того, как последняя порывает с своим ремесленным образцом… развитие автоматической системы и все более неизбежное и растущее применение материала, труднее поддающегося обработке, напр., железа, вместо дерева, вот те естественно выросшие задачи, разрешение которых повсюду наталкивалось на рамки, которые обусловливаются зависимостью работ от личности рабочего и которые даже комбинированный рабочий персонал в мануфактуре мог лишь несколько раздвинуть, но не уничтожить по существу» [15]15
К. Маркс, Капитал, т. 1. Соцэкгиз, 1931, стр. 289–290.
[Закрыть].
Маркс привел ряд примеров применения железа вместо дерева: «Механический ткацкий станок в своей первоначальной форме состоит преимущественно из дерева, усовершенствованный, современный – из железа».
Попытки применить в разных конструкциях чугун только на время отложили решение вопроса о прочном и дешевом металле. Нужна была сталь.
Передел чугуна в сталь становился узким местом развития новой техники. Поисками новых, лучших методов решения этой задачи занимались металлурги и ученые всех стран, среди них были выдающиеся физики Реомюр, Фарадей и другие.
Значительный шаг вперед по пути решения этой задачи сделали два английских рабочих – Томас и Джордж Кранеджи, которые в 1780 году изобрели так называемый метод пудлингования. По их предложению печь была разделена на две части – в одной помещался горючий материал, в другой – металл; между ними делался «пламенный порог», который предохраняет находящийся в ванне печи металл от непосредственного соприкосновения с пламенем. Над ванной печи – свод куполообразного очертания, чтобы газы отдавали металлу возможно больше тепла.
Недостатком таких печей было то, что металл необходимо было непрерывно перемешивать, причем это делалось вручную, и количество загружаемого в печь чугуна ограничивалось физическими возможностями рабочих-пудлинговщиков.
«…Рабочий-пудлинговщик, – писал К. Маркс, – занятый тем, чтобы освобождать чугун от углерода, должен выполнять ручной труд такого рода, что величина печи, которую он в состоянии обслуживать, ограничивается его личными способностями, и эта граница задерживает в настоящее время (1874 г.) тот изумительный подъем, который начался в металлургической промышленности с 1780 г., со времени изобретения пудлингования» [16]16
К. Маркс, Капитал, т. 1. Соцэкгиз, 1931, стр. 494.
[Закрыть].
Своими, особыми путями шли к разрешению проблемы передела чугуна в железо и сталь металлурги нашей страны. Правда, и на некоторых русских заводах стали вводить пудлингование, для чего даже выписывали из Англии специалистов.
Русские сталевары могли перенять у англичан и у металлургов других стран гораздо меньше, чем те могли заимствовать у русских. Надо думать, что не случайным является недавно установленный факт, что из всех русских архивов бесследно исчезли описания различных приемов получения стали, применявшихся на заводах нашей страны.
Одно за другим появлялись в России предложения о новых путях выплавки стали, исходившие от Полюхова, Бадаева, Всеволожского и от других русских сталеваров. Эти новаторы вносили коренные усовершенствования в широко применявшиеся в то время методы производства стали, настойчиво искали новые пути. Русская металлургия того времени подготавливала почву для открытий П. П. Аносова.
Больших успехов добились русские в производстве так называемой очищенной стали, которая отличалась высоким качеством и однородностью.
Очищенная сталь получалась путем сваривания сложенных в пучки полос, из уклада (то-есть кричного железа с содержанием 0,5–0,6 процента углерода). После окончания проварки весь пучок проковывали под молотом так, «чтобы спаев, где складки были, незнаемо было». Полученный брусок сгибали, снова разогревали и проковывали до тех пор, пока не достигали хорошего излома.
Качество стали оценивалось по числу «загибов». Пружинная сталь делалась в шесть «загибов», монетная – в восемь, инструментальная и дамасская – в двенадцать. Особенно славилась очищенная сталь Пышминской фабрики и Златоустовская.
Русские сталевары не имели соперников и в цементации, то-есть науглероживании кричного железа в специальных ящиках. На русских заводах стали применять ящики, в которые загружали вдесятеро больше железа, чем на заводах Англии. Тагильские мастера грузили в ящики одновременно 500–600 пудов железа.
Для разных сортов стали применяли особые карбюризаторы [17]17
Карбюризатор– материал, при помощи которого науглероживают сталь. Обычно применяли смесь разных сортов древесного угля с солями.
[Закрыть], обеспечивавшие ускорение процесса науглероживания и высокое качество стали.
Цементованная русская сталь была лучше импортной английской стали, но в этом очень трудно было убедить чиновников из Горного департамента и еще труднее было добиться признания изобретений русских людей.
Яркий пример этого – история заявки заводчика Полюхова о выдаче ему привилегии на изобретенный им способ производства цементованной стали.
Образцы полюховской стали подверглись испытаниям на многих производствах. Механики, монетчики, ситцепечатники, инструментальщики единогласно признали сталь Полюхова отличной.
Монетный двор дал такое заключение: «…она (сталь) оказалась на дело инструмента годной и прочной, сыпь имеет мелкую и ровную». Несмотря на это, Полюхову в выдаче привилегии было отказано.
«Департамент горных и соляных дел, находя, что приготовление стали в разных ее видах доведено уже в России до совершенства и на других заводах, и притом, выделка ее, быв весьма уже значительна, составляет важную ветвь частной промышленности, полезную и для самого государства… полагать прошение купца Полюхова без уважения».
Так «обосновывался» отказ Полюхову в выдаче привилегии. При этом выдвигались еще и высокие «государственные мотивы»: «…выдача привилегии, испрашиваемой Полюховым на исключительное приготовление стали на его заводах изобретенным им способом, – указывалось в том же заключении, – неминуемо остановит прочие сего рода заведения… послужит к подрыву и разорению заводчиков… а сие противно выгодам самого правительства» 21.
Больших успехов в производстве цементованной стали удалось добиться на Нижне-Исетском заводе, управителем которого в двадцатых годах XIX столетия был выдающийся изобретатель Подоксенов.
Прекрасными мастерами по выделке цементованной стали зарекомендовали себя работники Нижне-Гурьинского и Нижне-Тагильского заводов Антроп Кетов, Демид Крохалев, Лев Симбирцев и Андрей Субботин.
Не отставали от уральских и заводы, расположенные в центральной полосе страны.
Так, с баташовских заводов сообщали, что «все сорта стали, какие доселе известны, с давних времен выделываются на заводах г. Баташова и не только употребляются на свои заводские нужды, но и продаются частным людям и самой казне. Тульский оружейный завод не раз заказывал значительные количества, отдавая здешней стали преимущество пред другими. Самой булат, или подражание дамаскинской стали, делался на заводах г. Баташова с успехом» 22.
Русские металлурги давно задумывались над разрешением задачи получения литой,то-есть жидкой, а не цементованной стали.
Попытки изготовлять литую сталь делались не раз. Много нашумел своей сталью английский промышленник Генцман, но он расплавлял предварительно нацементованную сталь, чтобы сделать ее более однородной. Известно, что и Реомюр пробовал лить сталь.
Решающее и веское слово в этом деле сказали русские металлурги. Окончательное решение вопроса, как мы увидим ниже, дал П. П. Аносов. Но важно отметить, что идея организовать производство литой стали самостоятельно и параллельно разрабатывалась на разных русских заводах. Серьезных успехов добились С. И. Бадаев, впоследствии работавший на Камско-Воткинском заводе, и В. А. Всеволожский с Пожевского завода на Северном Урале.
Изобретение С. И. Бадаева относится «1808 году. Им в свое время даже заинтересовались в Петербурге и Бадаева вызвали в столицу, чтобы он на месте продемонстрировал свой метод производства стали.
Для приготовления стали Бадаев сконструировал специальную печь, состоявшую из двух отделений цементационного и тигельного. Исходным материалом для изготовления стали являлось кричное полосовое железо. Производство стали состояло сначала в цементации и в расплавлении цементованной стали. Затем снова производилась цементация с карбюризаторами, в которые входили различные сорта угля, белая глина, мел и др.
О приезде С. И. Бадаева в Санкт-Петербург тогда писалось в газетах. Вот что сообщалось в газете «Северная почта» от 14 января 1811 года:
«Некто из дворовых людей Семен Бадаев вызвался правительству, что он знает способ делать литую сталь превосходной доброты. Опыт, произведенный им при Санкт-Петербургском заводе хирургических инструментов под надзором особо отряженного до сего горного чиновника, совершенно оправдал предложение Бадаева. Сталь, выделанная им, представлена была Горному совету и по пробам разных вещей, из нее отработанных, как то: пуансонов, зубил, пружин, грабшихтелей и сверл, найдена не уступающей лучшей английской стали.
Из сей же стали Бадаева сделаны разные хирургические инструменты и бритвы здесь и в Москве, кои равным образом признаны хорошими. Бадаев как изобретатель сего способа, желая открыть оный на пользу общую, предал себя совершенно в волю всемилостивейшего государя, объявя, что он готов служить где угодно и открыть секрет свой кому повелено будет» 23.
Достижения С. И. Бадаева были настолько значительными, что правительство решило его выкупить и уплатило за него помещику 1800 рублей. Кроме того. Бадаева, наградили золотой медалью на Владимирской ленте и выдали единовременно 500 рублей.
Знаменитый русский хирург Н. И. Пирогов, руководивший впоследствии заводом хирургических инструментов, писал: «Мастера петербургского инструментального завода умели изготовлять наборы хирургических инструментов, по всей справедливости могущие служить образцом для заграничных мастеров» 24.
Работая на Камско-Воткинском заводе, С. И. Бадаев продолжал совершенствовать методы производства стали. Он приготовлял платинистую сталь и другие сорта ее.
В 1813 году бывший крепостной С. И. Бадаев, получил низший офицерский чин – шихтмейстера 14-го класса. Бадаев был самоучкой, никакого образования не имел. В его формулярном списке в графе «образование» значится: «русской грамоте читать и писать умеет» 25.
О дальнейшей работе Бадаева сообщает «Энциклопедический лексикон» Плюшара (1835 год). Там говорится следующее:
«Основал сталеделательное дело на казенном Камско-Воткинском заводе… Иностранный мастер Броун в отзыве об инструментальной бадаевской стали говорил, что до того он не видывал столь добротной стали. Сталь Бадаева оказалась лучше знаменитой гунцмановской (английской) стали, применявшейся для приготовления штемпелей. Россия тогда ежегодно ввозила стали и разных стальных изделий более чем на 3 млн. рублей. С распространением бадаевской стали ввоз этот мог прекратиться…
…Без сомнения выделка стали и изделий из нея будет приносить еще гораздо более выгоды, чем для Англии, – заканчивается заметка в энциклопедии, – ибо сталь мы будем приготовлять из собственного железа, между тем, как Англия покупает для этого наше русское или шведское железо» 26.
С. И. Бадаев умер в 1847 году, 69 лет от роду.
Еще ближе подошел к разрешению задачи передела чугуна в сталь русский изобретатель, владелец Пожевского завода В. А. Всеволожский. 17 марта 1814 года изобретатель подал заявку в Пермское горное правление на выдачу ему десятилетней привилегии на «новый способ делать из чугуна всякое железо, не переделывая оного в полосы кричным способом, и литую сталь» 27.
В своей заявке Всеволожский писал: «…малая цена, по которой сталь обойтись может, уменьшит привоз ее из чужих краев», а «большие количества, в каковых оная одним разом приготовляется… дают возможность отливать стальные цилиндры, прессовые винты, наковальни и др. огромные вещи». Изобретатель предлагал коренным образом изменить технологический процесс производства стали.
В то время на всех заводах мира железо и сталь получали из «свежеванного», или кричного, железа. Схема процесса была такой: отливка на доменном дворе в песке чугунных чушек; выжигание углерода из чугуна в кричном горне (окисление происходило за счет кислорода воздуха); проковка криц; рубка и повторная обработка в кричном горне; вторая проковка; протяжка в полосы.
По схеме Всеволожского, осуществленной на Пожевском заводе, процесс производства стали был значительно упрощен. Чугун разливался на доменном дворе в формы; затем в специальной, сконструированной Всеволожским печи чугун обрабатывался твердым окислителем, то-есть железной рудой, до получения мягкого железа; и последний этап – прокат железа на сорта, а также штамповка.
Здесь все ново, все необычно: и применение твердого окислителя и прокат вместо ковки.
Вместе с заявкой на привилегию В. А. Всеволожский послал в Пермь образцы полученных им железа и стали, из Перми их переотправили в Петербург.
Была создана специальная техническая комиссия, которая испытала присланные образцы стали.
Члены технической комиссии признали метод, предложенный Всеволожским, заслуживающим внимания и решили провести дополнительное испытание металла на Монетном дворе, а также дать его на пробу обергиттенфервалтеру, шотландцу Берду.
Из Монетного двора был получен положительный отзыв.
Берд ответил лишь через тринадцать месяцев. Он дал резко отрицательную оценку пожевской стали и сделал все, чтобы не дать изобретению русских сталеваров ходу. Причины этого нетрудно понять. Берд был владельцем механического завода в Петербурге, он претендовал на то, чтобы занять монопольное положение в стране по производству паровых и других машин. Владелец Пожевского завода русский механик Всеволожский был конкурентом Берда. На Пожевском заводе также делали паровые машины, здесь в 1815 году начали строить и пароходы. В 1816–1817 годах стимботы, то-есть пароходы, Всеволожского уже ходили по Каме н Волге. На заводе было построено два паровых судна – одно в 36, а другое в 6 лошадиных сил. На этом предприятии были изготовлены также первые фрезерные станки. Словом, это передовое предприятие своего времени было весьма чувствительным «бельмом» на глазу Берда.
В 1815 году Берд подал в министерство внутренних дел прошение о выдаче ему привилегии на десять лет на введение паровых судов по всем водным путям Европейской России. Понятно, что Берд делал все, чтобы провалить конкурента, и добился своего. Прошение Всеволожского было положено под сукно и лишь спустя десять лет было обнаружено среди неразрешенных дел.
Несмотря, однако, на старания Берда и других иностранцев, пожевские машиностроители продолжали поиски новых путей производства железа и стали, это было продиктовано потребностями машиностроительного производства. Пожевский завод был тогда одним из крупнейших предприятий по выделке железа и стали, его годовое производство достигало 120 тысяч пудов. Только на нескольких заводах России годовое производство железа превышало 100 тысяч пудов.
Всеволожский стоял на верном пути. Полное осуществление предложенной им схемы производства тормозилось лишь из-за несовершенства конструкции печи, в которой чугун превращался в мягкое железо.
Павел Петрович Аносов внимательно следил за напряженными поисками, которые велись в первой четверти XIX века для отыскания наилучших методов производства стали. Установлено, что С. И. Бадаев присылал Аносову в Златоуст образцы своей стали.
Но Аносов понимал, что никакие поправки, внесенные в старые схемы и методы изготовления стали, не могут дать удовлетворительного решения проблемы – обеспечить развитие машинного производства необходимым прочным материалом.
V. ЛИТАЯ СТАЛЬ AНOCOBA
Применявшийся на Златоустовской оружейной фабрике метод производства стали мало чем отличался от приемов работы на других предприятиях Урала. В основе всего процесса лежал кричный горн с последующей обработкой криц под молотами.
Иностранные мастера ничего нового, более прогрессивного в это дело не внесли. Попытки золингенца Петра Каймера ввести на фабрике производство литой стали провалились. Он обставил свою работу с наивозможнейшей таинственностью, к плавке готовился долго, разговоров и обещаний было много, но вышло по пословице: «хвалилась синица море зажечь». За два года Каймер выдал относительно годной едва… 9 пудов стали, а обошлась она больше чем по 169 рублей за пуд, то-есть примерно в десять-пятнадцать раз дороже существовавшей тогда цены на сталь. Ввиду дороговизны и низкого качества литой стали дальнейшее производство ее было приостановлено.
Аносов располагал замечательной базой для широкого развертывания опытов – в его распоряжении была специальная фабрика стали. Правда, Аносов не мог рассчитывать и не рассчитывал на помощь начальства: его в этом убедил разговор с Татариновым. Но он был уверен, что и мешать начальник горного округа не будет.
На Златоустовскую фабрику было возложено производство всего требовавшегося русской армии холодного оружия. Военное ведомство и Горный департамент все настойчивее напоминали о необходимости улучшить качество и снизить стоимость оружия.
А как это сделать, если нет никакой уверенности в качестве стали: сегодня сталь выходит хорошая, а завтра – негодная.
При таких условиях Татаринов не будет мешать опытам, хотя он в них и не верит.
Но неужели ему, Аносову, надо будет пройти весь путь исканий в одиночестве?
У Аносова был такой помощник – мастер по стали Николай Швецов. Что из того, что он неграмотен, что он крепостной человек? Это не мешает ему «чувствовать» сталь, видеть ее «насквозь». Дайте ему кусок стали, и он вам расскажет, как и при каких условиях она была откована, протянута.
– Эта сталь плоха потому, что полосы были неодинаково нагреты; если сделать из нее клинки, они будут непрочными, – говорил он, только взглянув на металл.
Сколько раз наблюдал Аносов за тем, как Швецов складывал «пучок» полос, как аккуратно посыпал полосы песком и бурой, а потом проковывал металл, рассматривал его излом, сравнивал размеры зерен.
– Неровно нагрели полосы, – сокрушенно качал Швецов головой. – Посмотрел бы на это Антроп Демидович, задал бы он им…
Антроп Демидович был учителем Швецова, мастером рафинированной стали на заводе в Тагиле. Оттуда и прибыл в Златоуст Швецов.
Аносов учился у Швецова узнавать качество стали по зернам, следил за тем, как меняется размер зерен в зависимости от нагрева.
Долгое время держалось мнение, что П. П. Аносов был чистым эмпириком, что все его успехи не более чем результат удачи, случайных опытов. Это была глубокая ошибка.
Напечатанная в «Горном журнале» № 1 за 1837 год статья П. П. Аносова «О приготовлении литой стали», как предупреждал автор, не носила научного или теоретического характера. «Не историческое повествование о времени, когда литая сталь сделалась известной, когда она совершенствовалась, когда терялась и снова появлялась; не подробное исследование состава и свойств ее, основанное на новейших успехах химии, составляют предмет сего сочинения, – писал Аносов, – но краткое и верное описание всех существенных правил и приемов, наблюдаемых при деле литой стали в Златоусте, с предназначенною начальством целию, чтобы всякий, хотя несколько знакомый с железным производством, мог иметь в нем руководство».
Тем не менее и в этом сочинении, которое как будто имеет чисто практическое предназначение, Аносов не остается на позициях эмпиризма. Смелый новатор не только излагает, как он совершает те или иные операции. В различных местах этого относительно небольшого труда он подробно касается и теории вопроса, объясняет, почему надо делать так, а не иначе.
Аносова прежде всего интересовало, при каких условиях углерод лучше и быстрее станет проникать в массу железа.
«С тех пор, как появились сочинения Ринмана в Швеции и Реомюра во Франции, – пишет в своем сочинении П. П. Аносов, – способы цементования сделались в Металлургии подробно известными, а вместе с тем сохранилось и правило, что для цементования железа необходимо непосредственное прикосновение угля к железу. Опыты заставили меня отступить от сего правила».
Из дальнейшего описания становится понятным, почему Аносов отбросил рекомендованный западноевропейскими учеными метод получения стали, основанный на соприкосновении угля с железом.
Аносов помещает железо в тигельный горшок, то-есть непосредственного контакта угля и железа уже нет. Но он отлично понимает, что это только кажущаяся изоляция. Тигель стоит в горне, насыщенном продуктами горения угля, углерод перешел в газообразное состояние. И пока тигель остается открытым, частицы углерода настойчивее атакуют железо, чем даже тогда, когда с ним непосредственно соприкасается твердый уголь.
На основании многочисленных опытов и наблюдений Аносов нашел средство (пусть еще примитивное) регулировать степень насыщения железа углеродом.
«Когда я, – писал он в сочинении «О приготовлении литой стали», – наполнил горшок железными обсечками без примеси угольного порошка, не покрывая их ни флюсом, ни крышкою, то вскоре заметил понижение обсечков, а потом и самое расплавление; но получил не ковкий металл, а чугун. Заключив из сего, что железо в излишестве насытилось углеродом, я накрыл горшок крышкой прежде, нежели все железо расплавилось, оставив в ней небольшую скважину для наблюдения за ходом работы, и спустя несколько времени удостоверился, что металл совершенно расплавился. Тогда, вылив в форму, я получил удобно ковкий металл – литую сталь.
Таким образом, для получения литой стали плавиленный горшок с крышею есть просто отпираемый ящик. Стоит только знать, когда его открыть и когда закрыть. Цементование железа, находящегося в горшке, совершается точно так же, как в ящике с угольным порошком, токмо тем скорее, чем возвышеннее температура».
Отсюда Аносов вывел одно из основных правил ведения плавки:
«Сплавление стали с угольным порошком или сажею в определенной пропорции в закрытом горшке, как предлагают Мушет и Бреан, хотя может дать сталь, но степень твердости ея подвержена большей неопределительности, нежели при описанном мною способе: ибо, положив угля более, опасаться должно, что она выйдет слишком твердою; а положив недостаточно, она будет трудно плавиться, особенно потому, что часть углерода улетучивается».
Аносов научился управлять «механизмом» насышения железа углем. Тигель он уподобляет «просто отпираемому ящику». Сталь плавится в том же тигле, но уже с закрытой крышкой.
Аносов разработал новый способ приготовления литой стали, который заключался «в сплавлении негодных к употреблению железных и стальных обсечков в глиняных горшках, при помощи возвышенной температуры воздушных печей».
Это открытие Аносова имело исключительно важное значение и для научной разработки процессов химико-термической обработки железа и стали, в частности для процесса газовой цементации.
Для плавки стали по новому способу Аносов сконструировал и построил специальную камерную воздушную печь, в которой удалось достигнуть необходимой для расплавления металла температуры. Он же исследовал огнеупорные материалы, из которых делаются тигли, и, наконец, детально разработал весь технологический процесс плавки и разливки стали.
Все это является несомненным свидетельством того, что Аносов был не эмпириком, а крупным ученым-мыслителем. Но одновременно он был инженером-производственником и свои научные открытия неуклонно претворял в жизнь.
По проекту Аносова был построен особый корпус с семью печами. Не останавливаясь подробно на конструкции печей, приведем лишь следующее замечание Аносова:
«Величина и вид их (печей) определены опытами, соображенными с возвышенностью температуры, необходимою для расплавления стали, с равномерностью какой должен быть по всем сторонам горна, и для сохранения плавиленных горшков и для успеха самой работы, с возможным сбережением горючего материала при наибольшем и удобнейшем получении металла».
Если считать это техническим заданием, то мы должны прийти к выводу, что автор задания – человек широких горизонтов, он стоит на государственных позициях. Получение литой стали для него не самоцель. В техническом задании предусмотрено все: и равномерный нагрев печи (чтобы она дольше простояла), и сохранение горшков, и экономия горючего, и высокая производительность, и удобства при получении металла.
Ни одной мелочи Аносов не упустил из виду при разработке проекта новой сталеплавильной печи. Он приложил к своему сочинению подробное описание и чертежи инструментов, которыми пользовались рабочие, обслуживавшие печи. Аносов уже тогда хорошо понимал, что сталь – материал капризный и чистота – первое условие успешной работы. Поэтому он ввел лопатки – одной формы для насыпания обсечек металла в тигель, а другой – для земли, флюсов.
Аносову много пришлось поработать, чтобы научиться приготовлять тигли. По поводу этой работы Аносов в своем сочинении пишет: «…предмет сей, ничтожный по названию и весьма важный для металлурга».
Может показаться странным, что даже такие изделия, как тигли, Россия в те времена выписывала из-за границы. Монопольным поставщиком их был тогда городок Пассау, вокруг которого находились залежи особого сорта высокоогнеупорной глины.
Аносов пришел к выводу, что «иностранные горшки особенно в столь отдаленном месте, как Златоуст, были бы слишком дороги для стального производства, и, не заменив их своими, успех был бы безнадежен».
Выход напрашивался сам собой: научиться делать горшки из местных материалов.
Это было вызовом всей сложившейся практике. До тех пор твердо придерживались мнения, «что одно токмо местечко Пассау может доставлять горшки, способные выдерживать самую высокую степень жара».
Аносов начал поиски сырья, чтобы делать свои тигли.
Прежде всего Аносов занялся исследованием причин образования трещин в горшках, сделанных из местной, челябинской глины. Многочисленные наблюдения привели его к выводу, что трещины в горшках получались вследствие расширения частиц глины от того, что одни частицы «давили» на другие. Это натолкнуло Аносова на мысль, что для предупреждения трещин необходимо в состав глины ввести «тело, которое бы уменьшило… способность сжимания».
Какое же «тело» для этого требуется? Аносов сделал анализ пассауской глины и нашел ответ на интересовавший его вопрос.
«В пассауских горшках сама природа позаботилась соединить глину с графитом».
Тогда Аносов решил изменить природу челябинской глины, он прибавил к ней угольный порошок. Так был найден рецепт массы для производства горшков: десять частей челябинской огнепостоянной глины, пять частей толченых, бывших в употреблении горшков и пять частей просеянного сквозь сито угольного мусора. Позднее угольный мусор заменили графитом, найденным на Южном Урале, у озера Еланчик.
Из этой массы Аносов при помощи пресса и медной формы стал приготовлять горшки. Конструкцию пресса он разработал сам.
Тигли Аносова оказались весьма огнестойкими и обходились «всеми расходами в 44 копейки» вместо 25 рублей, которые приходилось платить за заграничные.
«Разность в употреблении, – писал Аносов, – заключается единственно в том, что здешние горшки требуют соблюдения большей осторожности в прогреве, а вместе с тем, и более времени для начатия самой плавки, но в огнестойкости имеют положительное преимущество, которое, впрочем, дознано токмо на месте».
Последнее замечание сделано не случайно. Россия тогда была наводнена иностранными агентами, которые всячески стремились держать страну в экономической зависимости. Переход на производство отечественных горшков был серьезным уроном для промышленников Пассау, и через своих представителей они старались дискредитировать работу Аносова. Против них-то и направлены следующие строки сочинения о литой стали:
«В ученом мире иногда вкрадывается как бы некое предубеждение против простых средств, между тем, как многия из них, одетыя в систематическия выражения, занимают почетный места в науках. Еще недавно случилось мне видеть сему доказательство: один из известных химиков, получив для сплавки золота Златоустовские горшки, уведомил меня, что они никуда не годятся, и что он открыл в них вредную примесь – уголь, от которого они горят синим пламенем и разрушаются; тогда как в Златоусте, не говоря о стали, более трех лет сплавляется золото в сих горшках, и не было еще примера не токмо подобному разрушению, но не случалось, чтобы горшок, наполненный уже золотом, получил трещину. Напротив того, опытом дознано, что в одном горшке можно плавить золото до 6 и более раз, не останавливая работы» 28.
Аносов видел и перспективы развития русской огнеупорной промышленности, он высказал такую мысль: «может быть весьма скоро употребление литой стали распространится в России и вызовет предприимчивых людей к заведению сего производства», то-есть производства плавильных горшков.
Как видим, подготовка к выплавке стали новым способом потребовала решения ряда серьезных проблем и заняла много времени. Аносов не останавливался ни перед какими трудностями.
Чтобы создать пресс, он занялся механикой. Ему немало пришлось поработать над конструкцией печи. Наконец все приготовления были сделаны, и Аносов начал плавить сталь по новому методу.
Процесс плавки шел так.
После подготовки горшка, которая отнимала довольно много времени – около четырех часов, – в него по железному жолобу засыпали железные или стальные обсечки, «сколько поместиться может с верхом (в среднем около пуда)». Затем горн наполнялся углем, дверцы замазывали глиной и пускали мехи… Скоро в горне являлась «степень жара, потребная для расплавления стали, продолжающаяся до окончания работы…», «…закладываемое в горшки железо составляет особенность способа, – писал Аносов, – ибо в Англии сплавляют не железо, а цементованную сталь».