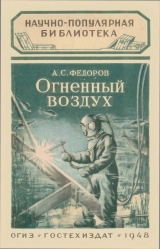
Текст книги "Огненный воздух"
Автор книги: Александр Фёдоров
сообщить о нарушении
Текущая страница: 4 (всего у книги 5 страниц)
СОКРОВИЩА СО ДНА МОРЕЙ И РЕК
На дне морей и рек лежит много металла. Немало больших и малых кораблей было потоплено в годы войны, сотни стальных мостов были взорваны врагом. Они загромождают русла рек и загораживают вход в бухты и заливы.
Еще не успели отгреметь последние выстрелы на полях сражений, как в нашей стране уже началась большая восстановительная работа. Советские люди неутомимо работают над тем, чтобы поднять затонувшие корабли и ввести их в строй, а те из них, которые явно устарели или не могут быть исправлены, переплавить для будущих сооружений. Много труда приходится затратить и для разборки сложных мостовых ферм, упавших в воду. Во всех этих работах на помощь человеку опять приходит чудесный «огненный воздух», разрезающий металлы под водой.
Как же идет под водой этот процесс? Почему вода, способная погасить огромный пожар, оказывается беспомощной перед крохотным факелом пламени кислородного резака?
Каждый знает, что вода и воздух – вещества совершенно различные. Вода в 850 раз плотнее воздуха. Ясно, что струя газов, вытекающая из сопла горелки, встретит в воде огромное сопротивление. Вода проводит тепло в 25 раз лучше, чем воздух. Поэтому нагретый предмет охлаждается в воде значительно быстрее, чем на воздухе. Наконец, вода поглощает тепла в 4 раза больше, чем равное ей по весу количество воздуха. В воде нельзя получить нормальное и устойчивое открытое пламя и нагреть поэтому погруженный в нее металлический предмет – задача нелегкая. Как же ученым удалось ее решить?
Первые горелки для кислородной резки под водой окружались специальной коробкой с отверстиями для удаления продуктов горения и с отодвигающейся крышкой. Коробка с горелкой погружалась в воду и прижималась к разрезаемому металлу. Затем крышка коробки открывалась, и пламя нагревало металл. Чтобы вода не проникала в коробку и не гасила пламя, в нее непрерывно подавался сжатый воздух, надежно защищавший ярко горящий факел от воды.
Вскоре оказалось, что коробка не является необходимой для подводной резки металлов. Появились специальные кислородные резаки, создающие защитный воздушный пузырь вокруг факела пламени и места разреза.
На борту небольшого судна водолазы готовятся к работе. Уже собрана установка для подводной резки, проверена полная герметичность всех шлангов и соединений. Водолаз-резчик, одев свой костюм – скафандр, берет в руки резак и опускается в воду.
Обычно резак зажигается еще до его погружения. Однако его можно зажечь и под водой. Для этого применяют металлический натрий или специальные порошки фосфористых соединений кальция, которые способны гореть в воде. В нужный момент при соприкосновении с водой эти порошки самовоспламеняются и зажигают горелку резака. Чаще для зажигания резака под водой используется вспомогательная газовая горелка, спускаемая в воду уже в зажженном состоянии. Наконец, этой же цели могут служить электрические зажигалки, дающие под водой электрическую искру, достаточную для воспламенения выходящей из резака горючей смеси.
Но вот водолаз подошел к месту работы. Перед ним стальная ферма взорванного моста. Он устанавливает резак на край разрезаемой металлической балки и начинает подогревать металл. Проходит несколько секунд. Возле места разреза появляются небольшие искры. Наступил момент для открытия вентиля режущего кислорода. И вот острая струя «огненного воздуха» устремилась к металлу. Место разреза вспыхивает ярким светом и окружается снопом искр. Медленно и равномерно передвигает водолаз свой режущий инструмент и разделяет на части стальные конструкции моста, перепутанные силой взрыва. Затем они извлекаются на поверхность и идут либо для новой стройки, либо направляются в переплавку. Река освобождается для судоходства.
Так кислород помогает извлекать со дна морей и рек тысячи тонн нужного стране металла.
САМОЕ «УДОБНОЕ» ТОПЛИВО
Одним из наиболее важных материалов, без которых не может обойтись человек, является топливо. Уголь и нефть приводят в движение паровозы и корабли, кокс необходим для выплавки чугуна. Энергия, заключенная в угле, нефти, торфе, превращается на электростанциях в энергию электрического тока, с помощью которого освещаются наши жилища, работают многочисленные станки и механизмы.
Не нужно быть большим специалистом в области энергетики, чтобы понять, что из трех видов топлива: твердого, жидкого и газообразного, последнее является самым удобным для использования. Действительно, твердое топливо нужно подвозить и загружать в печь. При горении оно дает большое количество золы; ее необходимо извлекать из печи и вывозить из котельной. Жидкое горючее обладает большими преимуществами. Нефть можно подводить по трубам и впрыскивать в печь через специальные форсунки. Но жидкое топливо – наиболее дорогой вид горючего. Из нефти можно получить бензин, керосин и другие очень ценные вещества, и переработка нефти приносит больше пользы, чем сжигание ее для отопления. Но обратимся к природному горючему газу. Газ тоже можно передавать по трубам. В печи он горит ровно и сгорает целиком, не оставляя золы, не выделяя дыма и копоти. Газовое пламя очень легко регулировать простым поворотом крана. Горючий газ можно предварительно подогревать отходящими из печи газами. Тогда при горении он даст еще больше тепла.
Все эти преимущества газообразного топлива давно заставили ученых и изобретателей заняться изысканием способов превращения твердого топлива в горючий газ. Их работы увенчались успехом. Ныне газификация каменного угля, дерева, торфа и других видов твердого топлива уже освоена техникой.
В последнее время газообразное топливо получает все более широкое применение, вытесняя другие виды горючего. Газом отапливаются печи, в которых выплавляется высококачественная сталь. Многие крупные машиностроительные заводы целиком работают на газообразном топливе, полученном из торфа, сланцев или низкосортных углей. Горючий газ, добытый из древесных чурок в небольших газогенераторах, приводит в движение автомобили и тракторы, сохраняя много ценного бензина. В крупных городах газ широко применяется для отопления зданий, кухонных плит и для других бытовых целей. Наконец, из горючего газа можно получить искусственное жидкое топливо – синтетический бензин.
В чем же заключается газификация твердого топлива? Каким образом куски каменного угля или торфа удается превратить в горючий газ?
КАК ИЗ УГЛЯ ПОЛУЧАЕТСЯ ГОРЮЧИЙ ГАЗ
Каждый из наших читателей не раз сидел у горящей печи или у костра, наблюдая за тем, как пламя пожирает поленья дров. Дерево сгорает, выделяя тепло. Весь углерод, содержащийся в топливе, соединяется с кислородом воздуха, образуя углекислый газ.
Но совсем другое происходит, если сжигание вести при весьма ограниченном доступе воздуха. В этом случае углерод полностью не сгорит. С кислородом воздуха он образует другое соединение, более бедное кислородом – окись углерода, газ, который сам может гореть. В этом, в сущности, и состоит газификация твердого топлива.
Для газификации топлива применяются особые аппараты – газогенераторы. Одни газогенераторы строятся для получения горючего газа из каменного угля, другие – для переработки сланцев, в третьих газифицируется торф. Познакомимся с устройством одного из газогенераторов, предназначенного для газификации угля.
Это – большой цилиндр, выложенный внутри огнеупорным кирпичом. Через верхнюю часть цилиндра – шахту – в газогенератор загружается уголь. Внизу аппарата находится вращающаяся колосниковая решетка, облегчающая удаление отходов от горения угля – шлаков. Снизу же подводится необходимое для горения дутье.
Газификацию можно вести на воздушном дутье. Однако в этом случае горючий газ будет содержать много азота. Как известно, азот не горит, не поддерживает горения и является вредным балластом, значительно ухудшающим качество горючего газа. Можно было бы вдувать в шахту чистый кислород. Но в этом случае в шахте развивается слишком высокая температура, и ход газификации нарушается. Поэтому, как правило, в газогенератор вместе с небольшим количеством воздуха или чистого кислорода вдувают водяной пар. Образующиеся при этом газы содержат новые горючие элементы: водород и соединения водорода с углеродом – так называемые углеводороды. Газ, богатый этими соединениями, горит так же хорошо, как природный газ или бензин, и дает много тепла.
При газификации твердого топлива часть скрытой в нем тепловой энергии безвозвратно теряется – ведь часть углерода сгорает полностью, образуя углекислый газ. Однако, несмотря на это, получение и использование газообразного топлива очень выгодно. Небольшие потери тепла при газификации с лихвой покрываются удобствами применения горючего газа. Поэтому-то пятилетний план восстановления и развития народного хозяйства СССР на 1946–1950 годы предусматривает большое развитие газификации твердого топлива.
Превращение хотя бы части низкосортного угля или торфа на месте их добычи в горючий газ и передача этого газа по трубам к потребителям позволяют значительно разгрузить железнодорожный транспорт от перевозок больших количеств твердого топлива и обеспечить наши города и промышленные центры высококачественным горючим, не дающим при сгорании ни золы, ни дыма, ни копоти.
ОДНА ИЗ ВЕЛИКИХ ПОБЕД ТЕХНИКИ
«Одна из великих побед техники» – так назвал В. И. Ленин свою статью, напечатанную в «Правде» в 1913 году и посвященную подземной газификации угля, то-есть добыче горючего газа прямо из каменноугольных пластов, находящихся глубоко в земле.
Блестящая идея подземной газификации принадлежит великому русскому химику, творцу знаменитой периодической системы элементов, Д. И. Менделееву. Более полвека назад Менделеев писал: «Настанет, вероятно, со временем такая эпоха, что угля из земли выламывать не будут, а там, в земле, его сумеют превращать в горючие газы и их по трубам будут распределять на далекие расстояния».
Немало ученых увлеклось мыслью о газификации угля под землей. Однако только в Советском Союзе эта замечательная идея была осуществлена практически.
Еще задолго до Великой Отечественной войны советские ученые провели большое количество опытов по получению горючего газа из зажженных под землей угольных пластов. Опытные станции подземной газификации угля были пущены в Донбассе, а также в Подмосковном угольном бассейне. Эти опыты, потребовавшие большого и напряженного труда, позволили установить, как идет в недрах земли невидимый и сложный процесс газификации угольного пласта, а затем перейти к практической работе по газификации.
Советские инженеры разработали так называемый поточный метод газификации. Он не требует тяжелого подземного труда и осуществляется так.
В земле с помощью механизмов для глубокого бурения делают два отверстия – выработки (рис. 13).

Рис. 13. Схематическое изображение станции подземной газификации угля. 1 – компрессоры, вдувающие под землю воздух, обогащенный кислородом; 2 – пласт угля; 3 и 5 – вертикальные выработки; 4 – горизонтальная выработка; 6 – скрубер – аппарат, в котором газ очищается от пыли и охлаждается; 7 – приборы управления; 8 – насосы для воды, подаваемой в скрубер; 9 – газопроводы.
Сначала эти отверстия минуют верхние, наносные слои земли – песок и глину. Затем они достигают угольного пласта и пронзают его насквозь. Под землей выработки соединяются между собою узким коридором, в котором и происходит газификация угля.
Угольный пласт зажигается опущенной под землю проволочной спиралью, раскаленной током. По одной из выработок с поверхности земли начинают вдувать воздух или, еще лучше, – кислород. Воздушный поток (поэтому, между прочим, этот способ газификации и называется поточным) омывает раскаленную нижнюю поверхность угольного пласта. Кислород соединяется с углеродом угля, образуя уже известный нам горючий газ – окись углерода.
Горючий газ поднимается по другой выработке на поверхность земли и поступает в специальный аппарат – скрубер, где он охлаждается и очищается от пыли. После этого газ по проложенным в земле трубопроводам направляется к потребителям.
Угольный пласт постепенно «выгазовывается». Выгазовывание идет по пласту, снизу вверх. На месте угольного пласта остается немного золы и свободное пространство, которое постепенно засыпается обвалившейся землей, прикрывавшей угольный пласт.
Специальные приборы, спущенные под землю и находящиеся на ее поверхности, позволяют постоянно следить за газификацией. Электрические пирометры в любой момент указывают температуру газифицируемой поверхности угольного пласта, а газоанализаторы точно устанавливают состав выходящего из недр земли горючего газа. По данным этих приборов технический персонал станции регулирует процесс, уменьшая или увеличивая количество кислорода, а иногда и водяного пара, вдуваемого под землю.
Фашистское нашествие временно приостановило работу наших основных станций подземной газификации, находящихся в Донбассе. Эти станции были разрушены врагом. Однако и в годы войны работа в области подземной газификации не прекращалась ни на минуту. Десятки миллионов кубических метров горючего газа выдала заводам станция «Подземгаз» в Подмосковном угольном бассейне.
Работа по дальнейшему совершенствованию подземной газификации угля продолжается. Перед народным хозяйством нашей страны открывается большое будущее. Ведь угольная промышленность, несмотря на механизацию многих трудоемких работ, требует огромных затрат человеческого труда. Добывая уголь, человек углубляется в землю на сотни метров, с помощью сложных машин он раздробляет угольный пласт, поднимает уголь на поверхность земли, очищает его, сортирует и развозит по всей стране. Немало угля при этом остается под землей. А многие угольные пласты и вовсе не разрабатываются, так как они слишком тонки: в них не могут разместиться для работы человек и его механизмы.
Газификация угля под землей освободит человека от тяжелого подземного труда, поможет избежать больших потерь при угледобыче и даст возможность использовать даже самые тонкие пласты угля.
Добыча газа из подземных угольных пластов потребует большого количества кислорода, ускоряющего процесс газификации и позволяющего получить полноценный горючий газ.
КИСЛОРОДНОЕ ДУТЬЕ В МЕТАЛЛУРГИИ
Кислород активно поддерживает горение. Значит, его целесообразно применять прежде всего в тех процессах, которые связаны с горением, с получением высоких температур. Таким процессом, помимо газификации твердых топлив, является производство чугуна, стали и многих других металлов. Использование кислорода в металлургии сулит настоящую техническую революцию в этой наиболее древней и наиболее важной отрасли промышленности. «Огненный воздух», поданный в домну или сталеплавильную печь, не только увеличит количество выплавляемого металла, но и позволит значительно упростить устройство металлургических агрегатов.
В металлургических печах, где выплавляются чугун и сталь, царят высокие температуры. Поэтому великий русский ученый Д. И. Менделеев назвал металлургию химией высоких температур. Кажется, ни одна отрасль промышленности не потребляет столько топлива и кислорода, сколько металлургия. Современный крупный металлургический завод, выпускающий в год один миллион тонн стали, требует два миллиона тонн угля и свыше трех миллиардов кубических метров кислорода.
До сих пор в металлургические печи вводится воздух. Но в воздухе азота в четыре раза больше, чем кислорода. Значит, вместе с тремя миллиардами кубометров кислорода через плавильные печи нашего завода пройдет не менее двенадцати миллиардов кубических метров азота. Этот азот является вредным балластом металлургического производства. Как много тепла необходимо затратить для бесполезного нагрева такого огромного количества азота! Если уменьшить количество азота, поступающего, например, в домну, то значительно возрастет температура в горне, быстрее будут выгорать примеси, скорее закончится выплавка металла.
Чтобы создать в доменной печи необходимую температуру, воздух предварительно подогревают до 700–800 градусов. Для этого мощные воздуходувные машины нагнетают воздух в громадные, высотой до 20 метров, башни – кауперы, стоящие возле каждой домны. По величине каждый каупер лишь немного уступает самой доменной печи. Кауперы, нагретые отходящими из домны газами, передают свое тепло воздуху. Выйдя из кауперов, горячий воздух по трубопроводам поступает в доменную печь.
Металлурги определили, что, вдувая в доменную печь воздух, в ней можно достигнуть температуры в 2000 градусов. Но если количество кислорода в дутье увеличить втрое, температура в домне возрастет до 3000 градусов и даже еще выше. Предварительное нагревание вдуваемого в печь воздуха становится ненужным даже тогда, когда он содержит 30 % кислорода.
Перед войной, в сентябре 1940 года, в СССР была пущена опытная доменная печь, работающая на дутье с увеличенным количеством кислорода. Печь давала до двухсот тонн чугуна в сутки, в 2–2,5 раза больше, чем обычная домна таких же размеров; вместе с тем сокращался расход топлива – кокса. Перед металлургией открылись, таким образом, новые блестящие перспективы. Появилась возможность не только резкого повышения производительности плавильных печей, но и значительного упрощения всех металлургических агрегатов.
Промышленность требует от металлургов не только обычный чугун, идущий для переработки в сталь или для производства литых изделий. Ей нужны и так называемые ферросплавы – чугуны специальных сортов. Они содержат больше кремния, марганца, хрома и других примесей, чем обычный чугун, и идут для выплавки специальных высококачественных сталей.
Получение некоторых ферросплавов в обычной доменной печи – дело крайне трудное. В домне нужно развить исключительно высокую температуру, а это приводит к огромному расходу топлива. Более того, отдельные сорта специальных чугунов (например, весьма важный для металлургии силикомарганец) вовсе не удавалось получить в доменной печи.
Кислород позволяет создать в домне любую практически необходимую температуру. Значит, работая на кислородном дутье, доменная печь будет выплавлять чугуны любых сортов и, кроме того, давать ценные тугоплавкие шлаки. А эти шлаки можно переработать в очень хороший строительный материал – портланд-цемент.
Один из побочных продуктов при работе домны – колошниковый или доменный газ. Он содержит около 30 процентов окиси углерода и поэтому является горючим газом.
Обычный доменный газ применяется для отопления кауперов и паровых котлов. По трубопроводам он направляется также и в сталеплавильные печи, но сжигается в них только в смеси с дорогим и ценным коксовым газом, получающимся при коксовании углей. Этим достигается необходимая для выплавки стали температура. Само собой разумеется, что если азота в дутье доменных печей будет меньше, то и выходящий из домны газ станет более ценным топливом. Поэтому колошниковый газ домны, работающей на кислородном дутье, явится прекрасным топливом для сталеплавильных печей. Он сможет пойти и для производства некоторых ценных химических продуктов. Такой доменный газ высвободит миллионы кубических метров коксового газа, которые целиком смогут быть использованы для получения искусственного жидкого топлива и других продуктов.
Не меньшие выгоды обещает применение кислородного дутья и при выплавке стали. Мартеновская сталеплавильная печь, работающая на кислороде, подобно домне, не потребует подогрева дутья. Самое сложное и дорогое устройство в современных мартеновских печах – громоздкие регенераторы, предназначенные для предварительного подогрева вдуваемого в печь воздуха, – станет ненужным. Кислородное дутье создаст в сталеплавильной печи необходимую температуру.
При кислородном дутье можно будет легко регулировать температуру в мартене: стоит только простым поворотом вентиля увеличить или уменьшить содержание кислорода в дутье.
Регенераторы современных мартеновских печей нагреваются за счет тепла отходящих из печи газов. Таким образом, значительная часть уходящего тепла возвращается в печь вместе с новыми порциями воздуха. Но как же удастся использовать огромное количество тепла, уносимое горячими газами из печи, работающей на кислородном дутье? Ведь регенераторы здесь не нужны.
Оказывается, решение этой задачи также под силу современной технике. Сталеплавильные печи, работающие на кислородном дутье, могут отдавать это тепло котельным установкам для производства пара, а пар всегда нужен любому заводу и для отопления и для приведения в действие ковочных молотов и других механизмов. Энергия пара может быть превращена в электрическую на заводской электростанции.
Подсчитано, что на каждую тонну стали, полученную в печи с кислородным дутьем, будет выработана тонна пара, а это весьма ощутимый вклад в энергетическое хозяйство металлургического завода.
Возможно, что применение кислорода в сталеделательной промышленности приведет к тому, что наши металлургические предприятия примут совершенно новый облик.
«Перспективы применения кислорода в металлургии, – говорит академик И. П. Бардин, – не воздушные замки, а крепости науки, которые надо взять. Но мы знаем, что нет таких крепостей, которых бы не взяла техника, вооруженная передовой наукой».