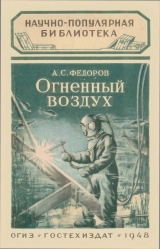
Текст книги "Огненный воздух"
Автор книги: Александр Фёдоров
сообщить о нарушении
Текущая страница: 3 (всего у книги 5 страниц)
ПОЛУЧЕНИЕ ЧИСТОГО КИСЛОРОДА
Читатель помнит, что азот и кислород, входящие в состав атмосферного воздуха, имеют различную температуру кипения. Жидкий азот начинает кипеть и испаряться уже при температуре около 196 градусов ниже нуля, в то время как температура кипения кислорода на 13 градусов больше, и он начинает испаряться из жидкой воздушной смеси позже, чем азот. Поэтому пары кипящего жидкого воздуха всегда содержат больше азота, чем сама испаряющаяся жидкость. Благодаря преимущественному испарению азота состав жидкого воздуха непрерывно меняется. Содержание кислорода в нем увеличивается. Жидкость обогащается кислородом.
Однако при простом испарении получить чистый кислород и целиком избавиться от азота, не удается: азот остается даже в последней капле испаряющегося жидкого воздуха. А для многих процессов в науке и промышленности необходимо иметь чистый кислород. Поэтому перед учеными была поставлена задача наиболее полного разделения воздуха на кислород и азот. И эта задача была успешно решена.
Ученые проделали такой опыт. В сосуд, наполненный жидким воздухом (рис. 8), они погрузили стеклянную трубку и начали пропускать через нее газообразный кислород.

Рис. 8. Газ, выделяющийся при пропускании кислорода через жидкую воздушную смесь, тушит спичку. Это – азот.
Пузырьки газа поднимались вверх и собирались в пробирку. Каково же было удивление исследователей, когда горящая спичка, внесенная в пробирку с собранным газом, мгновенно погасла! В пробирке оказался азот, не поддерживающий горения. Как же это произошло? Почему пузырьки кислорода неожиданно превратились в азот?
Виной всему оказалась разница в температурах ожижения азота и кислорода. Газообразный кислород, попадая в жидкость с температурой более низкой, чем температура его испарения, сам превращается в жидкость. При этом за счет поступившего с ним тепла из жидкой воздушной смеси испаряется некоторое количество азота, покидающего жидкость в виде пузырьков газа. Это интересное явление и привело ученых к созданию так называемого ректификационного аппарата – специального устройства для разделения жидкого воздуха.
Ректификационный аппарат представляет собою высокую металлическую колонну, снабженную большим количеством специальных тарелок с сетками или колпачками. Схема действия такой колонны с сетчатыми тарелками представлена на рисунке 9.

Рис. 9. Схема действия ректификационного аппарата – специального устройства для разделения жидкого воздуха.
Каждая тарелка снабжена сливным стаканом, по которому жидкость переливается с верхней тарелки на нижнюю. Пары испаряющегося жидкого воздуха, содержащие азот и кислород, поднимаются вверх. При этом они свободно проходят через мельчайшие отверстия сеток, препятствуя жидкому воздуху стекать через эти отверстия. Кислород, содержащийся в парах, постепенно конденсируется. Вследствие этого на тарелках накапливается жидкость, излишек которой стекает вниз через сливные стаканы.
Чем длиннее путь пузырьков пара сквозь жидкость и чем больше тарелок вмещает ректификационная колонна, тем чище получится азот, выходящий из ее верхней части, тем меньше примесей будет содержать кислород, остающийся в жидком виде в нижней части колонны. Поэтому современные колонны для разделения воздуха представляют собою высокие сооружения – в 5–6 и более метров; они снабжаются десятками тарелок.
Специальные устройства в ректификационном аппарате позволяют не только разделять жидкий воздух на азот и кислород, но и отделять от воздушной смеси еще одну важную составляющую часть – аргон. Этот газ широко используется для наполнения электрических ламп, а также в других отраслях промышленности.
Современные разделительные аппараты дают возможность получать газ, содержащий до 99,9 процента азота, и кислород почти такой же чистоты.
КИСЛОРОДНЫЕ ТАНКИ
При обычном атмосферном давлении температура жидкого кислорода лишь на 9 градусов выше температуры жидкого воздуха. Поэтому все сосуды, предназначенные для хранения жидкого воздуха, с неменьшим успехом могут быть использованы и для жидкого кислорода.
Жидкий кислород применяется более широко, чем жидкий воздух. Приходится хранить и перевозить десятки тонн жидкого кислорода. Сосуды, в которых сохраняются и перевозятся небольшие количества жидкого воздуха, здесь уже неудобны. Их заменяют специальные «танки».
Основной частью танка является сосуд, обычно шарообразной формы, изготовленный из латуни. Этот пустотелый шар подвешивается на цепях внутри кожуха, сваренного из листового железа. Пространство между латунным шаром и кожухом заполняется веществом, плохо проводящим тепло, – шлаковой ватой или углекислой магнезией.
Жидкий кислород при хранении в шаре танка постепенно испаряется. Если шар плотно закрыть, давление в танке будет непрерывно возрастать и в конечном счете приведет к разрыву сосуда. Чтобы этого не случилось, верхняя часть кислородного танка снабжена особой трубкой, по которой испаряющийся кислород удаляется в атмосферу или направляется в специальные хранилища – газгольдеры.
Каждый кислородный танк снабжается указателем уровня жидкости и манометром, с помощью которого можно следить за давлением во внутреннем сосуде. Однако этого мало. В танке есть предохранительный клапан. Если давление в танке станет больше определенного, клапан автоматически открывается и выпускает часть газа в атмосферу.
Но и этим не ограничиваются предохранительные устройства в кислородных танках. Обычно танки снабжаются еще предохранительной мембраной. Если давление во внутреннем сосуде танка превысит нормальное на полторы-две атмосферы, а клапан почему-либо не открывается, мембрана разрывается и тем самым предотвращает, казалось бы, неминуемую аварию.
Кислородные танки строят самых различных размеров. Они могут вмещать от нескольких десятков килограммов до нескольких десятков тонн жидкого кислорода.
Танки применяются не только для хранения, но и для перевозки жидких газов. Они устанавливаются на площадки грузовых автомобилей или на железнодорожные платформы (рис. 10).

Рис. 10. Транспортный танк, установленный на автомобиле, наполняется жидким кислородом.
В транспортных танках жидкий кислород можно перевозить на большие расстояния. Конечно, в пути часть кислорода испаряется. Исправный, вмещающий одну тонну жидкого кислорода танк за час обычно теряет не более 3–4 килограммов кислорода. Однако в некоторых случаях испаряющийся кислород удается улавливать. Специальные компрессоры нагнетают испаряющийся газ в небольшие стальные баллоны.
Наполнить танк жидким кислородом исключительно просто. Проследим эту работу на кислородном заводе.
Вот на завод прибывает грузовик с пустым танком. С помощью гибкого шланга пустой транспортный танк соединяется с танком, в котором хранится кислород. Поворотом вентиля плотно закрывается труба, соединяющая внутренний сосуд танка с атмосферой. Испаряющийся кислород не находит себе выхода. Давление в верхней части танка увеличивается. Расширяющийся газ давит на жидкость и заставляет ее перетекать по шлангу в пустой танк. Для того чтобы заполнить полуторатонный транспортный танк жидким кислородом, требуется не больше 10–15 минут. После этого шланг снимается, и кислород направляется к своему потребителю.
Кто же и для каких целей использует эту холодную светло-голубую жидкость?
ОКСИЛИКВИТЫ
Читателю, вероятно, известен такой опыт. Тлеющая лучина, введенная в сосуд с газообразным кислородом, вспыхивает ослепительно ярким пламенем и быстро сгорает. Кислород активно поддерживает горение. Если поджечь спичкой кусок угля, дерева или ваты, пропитанный жидким кислородом, пламя будет еще ярче.
В обычных условиях жидкий кислород очень быстро испаряется. При этом каждый литр жидкости превращается почти в 800 литров газообразного кислорода. В атмосфере чистого кислорода углерод и вещества, богатые углеродом, сгорают почти мгновенно, как порох, образуя большое количество газообразных продуктов горения. И если такое сжигание вести в закрытом сосуде, то давление очень быстро возрастет, произойдет огромной силы взрыв, и сосуд разлетится на мелкие куски.
Таким образом, пористые горючие вещества, пропитанные жидким кислородом, обладают способностью взрываться. Эти вещества называются оксиликвитами. Оксиликвиты дают взрыв такой же силы, как и динамит.
В Советском Союзе оксиликвиты применялись еще в годы первой сталинской пятилетки при строительстве Днепровской гидроэлектрической станции, а также при разработке залежей апатитов в Хибинах, на Коунрадских медных рудниках и на других горно-рудных предприятиях. В годы Великой Отечественной войны оксиликвиты заменяли на отдельных рудниках обычные аммиачно-селитренные взрывчатые вещества. Это позволило дать фронту больше взрывчатки, столь необходимой для разгрома врага.
Как же используют кислород при взрывных работах в горно-рудной промышленности?
СОЛОМА, КОТОРАЯ МОЖЕТ ВЗРЫВАТЬСЯ
Основой оксиликвита является поглотитель – какое-нибудь пористое вещество, содержащее много углерода и способное впитывать жидкий кислород. Особенно ценный поглотитель – сажа. Она содержит до 99 процентов чистого углерода и способна впитать в себя жидкого кислорода больше, чем любое другое вещество. Очень хорошо поглощают жидкий кислород древесный уголь и опилки. Для изготовления оксиликвитов можно брать также и солому, сено, сухой камыш, таежный торф-сфагнум.
Вещество-поглотитель предварительно измельчают и тщательно перемешивают в особых вращающихся металлических барабанах. Тогда поглотитель становится однородным, а это повышает его взрывные свойства. Когда смесь станет достаточно мелкой и однородной, она поступает к набивочным станкам. В этих станках поглотителем наполняются бумажные или картонные гильзы. Часто оболочкой для поглотителей вместо бумаги служит дешевая ткань.
Если поглотитель готовится из соломы или древесины, его просто спрессовывают в брикеты.
Незадолго до начала взрывных работ, когда во взрываемых породах уже проделаны ряды глубоких отверстий – скважин, рабочие приступают к пропитке патронов жидким кислородом. Патроны с поглотителем помещаются в термосы – специальные сосуды с двойными стенками, между которыми находится слой вещества, плохо проводящего тепло. Затем термосы наполняются жидким кислородом.
Разница в температурах кислорода и поглощающего вещества сначала очень велика, и жидкий кислород бурно кипит и испаряется. Когда температуры выравняются, жидкость начнет проникать во все поры поглотителя, и патроны сделаются тяжелыми, твердыми и очень холодными. К таким патронам уже нельзя прикасаться незащищенной рукой – может произойти сильное обморожение. Оксиликвиты вынимаются из термоса особыми щипцами или крючьями.
В специальные отверстия, заранее сделанные в патронах, вставляются капсюли или электрические детонаторы, и оксиликвиты осторожно опускаются в скважины.
Проворно работают взрывники-оксиликвитчики. В их распоряжении немного времени. Жидкий кислород быстро улетучивается из патронов и их взрывные свойства постепенно ослабевают. Срок «жизни» оксиликвита невелик. Маленькие патроны теряют способность взрываться уже через 15–20 минут после пропитки. «Жизнедеятельность» больших оксиликвитных патронов измеряется несколькими часами.
Но вот зарядка скважин закончена. Сеть электрических проводов соединяет их между собой. Сигнал. Рабочие удаляются в безопасный блиндаж. Еще сигнал и затем легкий нажим кнопки.
Взрыв огромной силы сотрясает воздух. На десятки метров в стороны летят куски породы и грунта. Земля открывает свои недра. Через несколько минут к месту взрыва подходят экскаваторы, и начинается разработка ценных ископаемых.
Огромное количество скважин взорвано на рудниках всех стран мира с помощью оксиликвитов. Область их применения непрерывно расширяется. И это не случайно. Использование оксиликвитов часто оказывается значительно более выгодным, чем применение обычных взрывчатых веществ.
Оксиликвиты дешевы. Их можно изготовлять из подручных местных материалов. Взрывные работы с помощью оксиликвитов обходятся вдвое дешевле, чем с помощью такого недорогого взрывчатого вещества, как аммонал. Для получения одного килограмма оксиликвита расходуется полтора-два килограмма жидкого кислорода. А для получения такого количества жидкого кислорода нужно всего около четырех киловатт-часов. Столько энергии потребляет за 10 часов обычная электроплитка.
Хранение патронов-поглотителей и их перевозка, так же как и перевозка жидкого кислорода, абсолютно безопасны. Взорваться может только пропитанный кислородом патрон. Но как только кислород из патронов испарится, они опять становятся безопасными. Это обстоятельство выгодно отличает оксиликвиты от других взрывчатых веществ.
При горно-взрывных работах взрывчатым веществом заряжается много скважин. После того как произошел взрыв, почти невозможно установить, все ли патроны взорвались. Бывают случаи, когда невзорвавшиеся сразу заряды аммонала взрываются во время работы экскаватора при уборке руды. При работе с оксиликвитами такой опасности нет. Невзорвавшиеся оксиликвиты быстро теряют свою взрывную силу и становятся совсем неопасными.
Кроме того, применение оксиликвитов не требует дальних перевозок больших количеств твердых взрывчатых веществ. Оксиликвиты могут производиться прямо на месте горно-рудных разработок. Вблизи всегда найдется для них сырье: древесина, уголь, солома, торф, а жидкий кислород можно подвозить тоннами в специальных железнодорожных цистернах или получать на месте из воздуха.
Однако это еще не все. Оксиликвиты сохранят нам немало ценных химических продуктов (например, селитру), которые необходимы для получения сельскохозяйственных удобрений и незаменимы в других отраслях народного хозяйства.
КАК ЖИДКИЙ КИСЛОРОД СНОВА ПРЕВРАЩАЮТ В ГАЗ
Мы рассмотрели несколько примеров применения жидкого кислорода. Однако еще больше промышленность нуждается в газообразном кислороде.
Газообразный кислород можно получать непосредственно на установках глубокого холода. Но не во всех случаях это бывает выгодно. Часто потребители предпочитают привозить жидкий кислород с кислородного завода и уже на месте потребления превращать его в газ.
Возьмем, например, весьма распространенную в промышленности сварку и резку металлов. Газообразный кислород поступает к месту сварочных работ в специальных баллонах. Объем такого баллона не превышает обычно 40–60 литров. Чтобы поместить в баллоне возможно больше газообразного кислорода, последний сжимают до 150 атмосфер. При таком давлении 40-литровый баллон вмешает уже шесть кубических метров газообразного кислорода.
Баллоны для перевозки сжатых газов должны быть очень прочными. Они делаются из массивных стальных труб, изготовленных без шва. Сталь для труб должна быть высокого качества, и баллоны эти обходятся очень дорого. Пустой 40-литровый баллон весит около 80 килограммов – в 9 раз больше, чем помещаемый в него газ. Представьте себе, что кислород нужно перевозить на значительные расстояния. Здесь-то и скажутся преимущества жидкого кислорода.
Тысяча кубометров газообразного кислорода весит менее полутора тонн. Чтобы вместить столько газа, потребуется 167 баллонов общим весом в… 13 тонн. Для перевозки их придется занять целую железнодорожную платформу или 9 грузовиков-полуторатонок.
Другое дело – перевозка жидкого кислорода. Полторы тонны его свободно помещаются в легком резервуаре объемом всего в 1300 литров и перевозятся одним грузовиком.
Однако экономией на перевозке преимущества жидкого кислорода не ограничиваются. Жидкий кислород не содержит влаги, которая обычно есть в газе. Отсутствие влаги значительно улучшает качество сварочных работ, для которых используется кислород.
Правда, перевозка жидкого кислорода тоже не свободна от недостатков. Жидкий кислород непрерывно испаряется. Однако с этим недостатком можно бороться. Цистерны для жидкого кислорода снабжаются компрессорами, которые накачивают испаряющийся газ в баллоны. Но даже в тех случаях, когда жидкий кислород просто испаряется в атмосферу, перевозить его на дальние расстояния гораздо выгоднее, чем газообразный.
Как же жидкий кислород снова превращают в газ? Для этого применяются особые аппараты – газификаторы. Жидкий кислород, налитый в резервуар такого аппарата, быстро испаряется и под давлением в 10–15 атмосфер идет по трубам к месту сварки.
Существуют специальные газификаторы, в которых давление испаряющегося газа повышается до 150 атмосфер. Эти газификаторы служат для быстрого наполнения кислородом знакомых нам баллонов.
«ОГНЕННЫЙ ВОЗДУХ» ИЗ … ВОДЫ
170 лет назад ученые впервые обнаружили любопытное явление: если через ванну с подкисленной водой пропускать электрический ток, то у погруженных в воду металлических пластинок, к которым подводится ток, возникают пузырьки каких-то газов. Этот процесс был назван электролизом, то-есть разложением с помощью электричества.
Оказалось, что при электролизе вода разлагается на свои составные части – кислород и водород. При этом кислород выделяется на положительном электроде – пластинке, а водород – на отрицательном.
Долгое время электролиз воды не использовался на практике. Единственным источником электрической энергии были в то время гальванические элементы, и ток стоил дорого. Лишь в конце прошлого века, когда была изобретена динамомашина, дающая огромные количества дешевой электрической энергии, электролиз воды стал применяться для получения водорода и кислорода. Делается это так.
В большую ванну-электролизер наливают воду, к которой прибавляется немного кислоты или щелочи. Такая добавка увеличивает электропроводность воды. К металлическим пластинкам, опущенным в воду, подводится постоянный ток от аккумулятора или электрической сети.
Над пластинками помещаются специальные сосуды для улавливания водорода и кислорода (рис. 11).

Рис. 11. Схема устройства электролизера – аппарата для разложения воды электрическим током.
В последнее время строятся установки для электролиза воды, работающие под высоким давлением – до 200 атмосфер. Газы, полученные на таких установках, сразу поступают в баллоны, не требуя дополнительного сжатия.
Однако такой способ получения кислорода связан с большим расходом электрической энергии. Чтобы получить 1 кубический метр кислорода, нужно затратить 10–12 киловатт-часов электрической энергии. Поэтому электролиз воды не применяют в тех случаях, когда требуется получать только один кислород. Зато этот способ широко используется там, где нужен чистый водород. В этом случае «огненный воздух» выделяется и используется как побочный продукт.
Особенно много электролизных установок работает в химической промышленности, где водород и кислород нужны для получения синтетического аммиака, идущего для производства удобрений и различных химических веществ. Кроме того они необходимы при изготовлении искусственных камней, прозрачного кварца, твердых, сплавов, электроламп и т. д.
ОБРАБОТКА МЕТАЛЛОВ ОГНЕМ
Кислород особенно широко используется для сварки и резки различных металлов и сплавов.
Любое горючее вещество энергично сгорает в кислороде и выделяет при этом много тепла. И это вполне понятно: если какое-либо вещество сгорает в воздухе, много тепла бесполезно тратится на нагревание азота, а он, как мы знаем, составляет четыре пятых атмосферного воздуха. Другое дело, когда горение происходит в чистом кислороде. При этом гораздо больше выделяющегося тепла идет на повышение температуры пламени, и горение протекает быстро и полно.
При сжигании в чистом кислороде горючего газа – водорода, ацетилен или светильного газа – развивается огромная температура, выше 3 тысяч градусов! При такой температуре плавятся самые тугоплавкие металлы. Поэтому для сварки металлов применяют пламя кислородно-ацетиленовой горелки. Эта горелка состоит из двух трубок, заканчивающихся общим наконечником. Одна трубка соединяется с кислородным баллоном, а по другой подводится горючий газ. Чаще всего это – ацетилен, соединение углерода с водородом, получающееся при действии воды на особое химическое вещество – карбид кальция. Получается он прямо на месте сварки в так называемом ацетиленовом генераторе. Образующийся газ по шлангу идет в горелку (рис. 12).

Рис. 12. Схема действия установки для кислородно-ацетиленовой сварки.
Здесь же устанавливается и баллон с кислородом. Конечно, давление в 150 атмосфер, под которым заключен кислород в баллоне, слишком велико для работы. Поэтому его понижают до 3–4 атмосфер в специальном аппарате – редукторе.
Иногда ацетилен, так же как и кислород, подвозится в баллонах, сжатый до 15 атмосфер. Баллоны с разными газами имеют разную окраску. Это позволяет избежать путаницы при работе и легко найти баллон с нужным газом.
Как же идет газовая сварка? Пламя горелки направляется на свариваемое место. Под действием высокой температуры металлические поверхности быстро оплавляются и при остывании соединяются в одно целое. Обычно при сварке металлов применяется какой-нибудь присадочный материал. Это – металлическая пластинка или проволока, дающая при расплавлении добавочное количество металла для заполнения промежутка между свариваемыми предметами.
Кислород используют также и для резки металлов. Приспособление для резки металлов – резак – в отличие от сварочной горелки имеет дополнительный канал, через который подводится чистый кислород. Когда пламя газовой горелки раскалит небольшой участок поверхности металлического изделия, в резаке открывается канал и к раскаленному металлу идет узкая струя кислорода. В этой струе металл плавится и быстро сгорает, а часть его выдувается, образуя тонкую и узкую щель, разделяющую кусок металла на две части. Даже большие стальные бруски толщиною в 1 метр легко перерезаются струей «огненного воздуха».
Существуют газорезные машины, разделяющие на части огромные стальные слитки и вырезающие из металлического листа изделия различной формы. Многие из таких машин работают совершенно автоматически. Они дают сотни одинаковых деталей, не требуя за собою непрерывного наблюдения.
Кислородной струей можно и очищать поверхности металлических изделий. Слитки стали нередко имеют на своей поверхности загрязнения шлаком, неглубокие трещины и т. д. При дальнейшей обработке слитка эти изъяны могут привести к неисправимой порче получаемых из него изделий. До последнего времени эти изъяны удалялись путем вырубки части наружного слоя пневматическими зубилами. Это была весьма тяжелая работа, требующая большого физического труда.
Сейчас и здесь на помощь приходит кислород. Место изъяна в стальном слитке сначала нагревается пламенем кислородно-ацетиленовой горелки, а затем в струе чистого кислорода поверхностные слои металла сгорают, и от наружного порока слитка не остается и следа.
Огневая зачистка кислородом используется также и для предварительной обработки слитков высококачественной инструментальной стали. Такие слитки, прежде чем поступить в обработку на прокатных станах или ковочных прессах, обычно подвергаются обработке на металлорежущих станках – обдирке. На токарных или строгальных станках с поверхности слитков снимается более или менее толстый слой металла.
Кислород «обдирает» слиток гораздо быстрее станка. Уже начали применяться для этого специальные машины – самоходные тележки с рядами горелок-резаков. Передвигаясь вдоль слитка, такая машина сразу срезает необходимый слой металла по всей его ширине.
Наиболее сложные и интересные многопламенные резаки обдирают огромные стальные заготовки при их обработке на больших прокатных станах – блюмингах. Нагретая добела стальная болванка, прежде чем поступить под вращающиеся валки блюминга, охватывается со всех сторон десятками кислородных струй резаков. В одну минуту они зачищают до 20 погонных метров болванки.
На современных заводах кислородная сварка и резка все чаще заменяет штамповку, отливку и даже механическую обработку металлов на станках. При этом очень быстро получаются изделия высокого качества, а отходы металла незначительны.