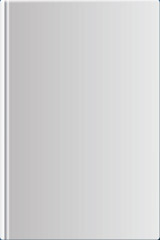
Текст книги "Водородное топливо. Производство, хранение, использование"
Автор книги: Юрий Почанин
Жанр:
Научпоп
сообщить о нарушении
Текущая страница: 4 (всего у книги 4 страниц)
Одним из процессов, основанном на использовании многоступенчатой газификации является железо-паровой процесс производства водорода. Процесс основан на том, что активные металлы вытесняют водород из воды, например, натрий и кальций разлагают воду при обычных условиях, магний – при нагревании, цинк – при накаливании с водяным паром, железо – при нагревании около 700°С. На первой ступени газификации используемый кокс газифицируется с помощью паровоздушного дутья, в результате чего получается газ, содержащий СО, Н2 и N2. Наличие азота не является недостатком, так как промежуточные процессы позволяют от него избавиться. Полученный газ используется для восстановления окисла железа Fe3O4 до FeO в соответствии с реакциями:
Fe3O4 + СО = 3FeO + СО2;
Fe3O4 + Н2 = 3FeO + Н2О.
Образовавшиеся в результате этих реакций СО2, Н2О и N2 после утилизации теплоты выбрасываются в атмосферу. Если исходное дутье имеет повышенное давление, то наиболее целесообразно использовать эти газы в газотурбинной установке. При этом КПД процесса получения водорода достигает 63 %, из которых 18 % приходится на вырабатываемую электроэнергию.
На следующей стадии полученная окись железа FeO направляется в окислитель, где при более низкой температуре одна из двух прежних реакций происходит в обратном направлении:
3FeO + Н2О = Fe3O4 + Н2
При обычных для этого процесса температурах равновесие реакции таково, что ее продукты содержат около 37 % водорода (остальное – в основном водяной пар, который удаляется конденсацией).
Железо-паровой процесс обладает рядом существенных недостатков сравнительно с конверсионным: он требует большего расхода водяного газа и дает водород со значительным содержанием примесей.
2.2.5. Процесс СО2-акцепторВсе рассмотренные выше методы газификации основываются на автотермическом проведении реакции. Поэтому газифицирующая газовая смесь содержит водяной пар и кислород (или воздух), соотношение которых определяет конечную температуру процесса газификации. При этом для получения газа с более высокой теплотой сгорания и для уменьшения затрат на очистку от азота предпочитают использовать не паровоздушное, а парокислородное дутье. Это существенно удорожает процесс за счет включения в него установки для разделения воздуха.
Однако, есть и другая возможность получить недостающую теплоту для эндотермической реакции угля с водяным паром. Среди схем с аллотермическим подводом теплоты, реализующих эту возможность, представляют интерес схемы, в которых недостающая теплота образуется за счет побочной химической реакции с участием дополнительно вводимого в зону реакции реагента. В качестве примера такого способа следует упомянуть метод СО2-акцептор, разработанный в США. Здесь теплота вводится в зону газификации за счет реакции СаО с двуокисью углерода с образованием доломита:
СаО + СО2 = СаСО3.
При этой реакции выделяется около 176,8 кДж/моль. Этого количества теплоты достаточно, чтобы осуществить газификацию угля только водяным паром. Схема газификации по методу СО2-акцептор представлена на рис. 2.14. Процесс газификации происходит в кипящем слое при давлении 1–2 МПа. Отсортированный и высушенный уголь подается через шлюз вначале в камеру термического разложения, где при температуре 800–850°C происходит пиролиз исходного угля продуктами газификации. Поэтому получающийся газ содержит продукты пиролиза, хотя при указанной температуре в среде водяного пара они частично разлагаются. Часть образовавшегося полукокса поступает в собственно кипящий слой газификатора. В верхнюю часть слоя поступает регенерированный доломит с температурой около 1025°C.
В нижнюю часть слоя подается паровое дутье. Образующаяся в результате реакции с водяным паром двуокись углерода вступает в реакцию с СаО, образуя доломит и поставляя теплоту для эндотермической реакции угля с водяным паром. Более крупные и тяжелые частицы СаСО3 постепенно опускаются в нижнюю часть слоя. Непрореагировавший уголь и зола уносятся газами вверх, а СаСО3 выводится из газификатора и направляется на регенерацию.

Рис. 2.14. Схема газификации по методу СО2-акцептор:
1-зона подготовки угля, 2-загрузочный шлюз, 3-зона термического разложения, 4-газификатор с кипящим слоем, 5-система котел-утилизатор + водяной скрубер, 6-аппарат для очистки газа, 7-реактор метанирования, 8-регенератор с кипящим слоем
Регенерация представляет собой эндотермический процесс, происходящий при температуре около 1025°C:
СаСО3 = СаО + СО2.
В регенераторе также организуется кипящий слой. Здесь теплоту для реакции регенерации поставляет сжигание в воздухе части полукокса, выводимого из камеры термического разложения. Регенерированный доломит возвращается в газификатор, а дымовые газы из регенератора вместе с золой направляются на утилизацию теплоты, в частности на производство водяного пара в котле-утилизаторе.
Недостатком процесса СО2-акцептор является сравнительно низкая температура газификации, лимитируемая термической стойкостью доломита (~850°C). Из-за этого в газе, как уже отмечалось, остаются продукты пиролиза и требуются специальная очистка как газов, так и воды. Газ, получаемый по этому методу, содержит (по объему): 16 % СО, 11 % СО2, 56 % Н2, 15 % СН4 (прочие компоненты– около 2 %). Таким образом, содержание водорода достаточно велико, но велико и содержание метана, связанное с высоким давлением.
Сравнительный состав синтез-газа, полученный различными методами показан в таблице 2.6.
Таблица 2.6. Сравнительный состав синтез-газа

Таким образом, в конечном итоге теплоту для эндотермической реакции газификации угля водяным паром поставляет горение того же угля, но так как продукты сгорания не смешиваются с продуктами газификации, может быть использовано дешевое воздушное дутье.
Для выделения водорода из синтез-газа используются разнообразные методы: адсорбция, абсорбция, диффузии через мембраны, электрохимическая конверсия, глубокое охлаждение, катализ.
2.3 Плазменная газификация угля
Находит применение плазменная парокислородная газификация угля, который относится к классу процессов с внутренним подводом тепла. Данный метод позволяет удерживать постоянную температуру процесса порядка 1500–2000°C во всем объеме газогенератора. Высокая рабочая температура обеспечивает получение синтез-газа, который не содержит окислителей таких, как СО2 и Н2О.
Процесс заключается в том, что измельченный уголь в смеси с кислородом перемешивается плазменной струей водяного пара в плазмотроне, а затем попадают в газогенератор, где при температурах 1500°C и выше получают синтез-газ с достаточно высоким содержанием водорода и оксида углерода и незначительным содержанием СО2, Н2О и N2. КПД такого газогенератора достигает 80–90 %.
В плазменных газификаторах также используются плазменные фурмы для газификации твердого топлива. Этот тип газификаторов зачастую используют для уничтожения сложно-газифицируемых бытовых и коммунальных отходов, а также отходов медицинской деятельности. Главная отличительная особенность плазменной технологии газификации заключается в значительной интенсификации процесса деструкции отходов, который протекает за весьма короткий промежуток времени за счет передачи энергии обрабатываемым материалам излучением и конвекцией. На рис. 2.15 представлена схема плазменного газификатора.

Рис. 2.15. Плазменный газификатор
Твердое топливо загружается с боковой стороны газификатора, плазменные фурмы расположены по направлению движущегося слоя. Вблизи фурм температура может достигать значений 3000°С. Расплавленный метал и шлак выгружаются из нижней части реактора. Организация выгрузки шлака является привлекательной для переработки твердых коммунальных отходов, т. к. токсичные металлы в шлаке практически не извлекаемы. Газ поднимается в верхнюю часть газификатора и попадает в расширенную надслоевую зону, которая позволяет крупным твердым частичкам снова попасть в слой. Газ покидает газификатор при температуре 900–1000°С, что достаточно для деструкции пиролизных смол.
Теплота сгорания синтез-газа составляет примерно 80 % от теплоты сгорания исходного топлива. Синтез газ может быть использован для генерации электроэнергии. Электричество для работы плазменных фурм составляет от 2 до 5 % энергии поступающего сырья.
Существует множество технологий с различными конструкциями газогенераторов, но все они являются «синтезом» основных и не имеют столь широкого применения. Это основные, хорошо освоенные и изученные методы промышленного получения водорода. Однако все они дороги в сравнении с традиционной энергетикой.
Производство синтез-газа, в состав которого входят: водород, метан, окислы углерода и прочие газы – может быть также основано на переработке биомассы и промышленно-бытовых отходов, что одновременно способствует решению экологических проблем. Например, переработать отходы жизнедеятельности рогатого скота, да и вообще любого другого сельскохозяйственного животного.
Конец ознакомительного фрагмента.
Текст предоставлен ООО «ЛитРес».
Прочитайте эту книгу целиком, купив полную легальную версию на ЛитРес.
Безопасно оплатить книгу можно банковской картой Visa, MasterCard, Maestro, со счета мобильного телефона, с платежного терминала, в салоне МТС или Связной, через PayPal, WebMoney, Яндекс.Деньги, QIWI Кошелек, бонусными картами или другим удобным Вам способом.