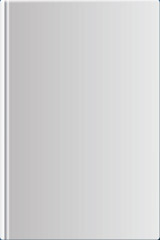
Текст книги "Водородное топливо. Производство, хранение, использование"
Автор книги: Юрий Почанин
Жанр:
Научпоп
сообщить о нарушении
Текущая страница: 3 (всего у книги 4 страниц)
Разработанная в России новая технология адиабатической конверсии метана существенно упрощает промышленный процесс получения метано-водородной смеси (МВС), поскольку не требует производства кислорода, энерго– и капиталозатратного электролиза воды, происходит при более низких температурах (до 680°С) и построена на отработанных в крупнотоннажной химии технологических решениях, режимах и катализаторах. Адиабатическим процессом называется процесс, идущий без теплообмена с окружающей средой
Принципиальная схема получения метано-водородной смеси по технологии адиабатической конверсии метана (АКМ) изображена на рис. 2.6.

Рис. 2.6. Принципиальная схема получения метано-водородной смеси
Природный газ, очищенный от сернистых соединений, поступает в узел смешения с водяным паром. Водяной пар поступает из котла-утилизатора. Природный газ с водяными парами при температуре примерно 450°С поступают в огневой подогреватель. На выходной линии огневого подогревателя температура смеси составляет примерно 680°С. С такой температурой смесь поступает в адиабатический реактор. В реакторе, благодаря адиабатической конверсии метана, получаем метано-водородную смесь и водяные пары с температурой примерно 590°С. Так как в адиабатическом реакторе часть воды тратится для получения водорода, производится постоянная подпитка воды в систему. Перед тем как попасть в систему вода проходит через фильтр. Все расходные показатели по природному газу, метано-водородной смеси, водяному пару и воде показаны на схеме.
В данной установке при подаче на вход природного газа в количестве 1000 нм3/ч, а на выходе из установки получают метано-водородную смесь в количестве 1792 нм3/ч, а компонентный состав входного природного газа и выходной метано-водородной смеси показан в таблице 2.2.
Таблица 2.2. Компонентный состав входного природного газа и выходной метано-водородной смеси

Входящий продукт (природный газ) в основном состоит из метана (99 %). Выходящий продукт является смесью трех компонентов: водяного пара – 67,7 % (об.), водорода – 13,6 % (об.) и метана – 15 %. Повышенное содержание по сравнению с входящим продуктом имеют: диоксид углерода – 3,3 % и оксид углерода – 0,233 %. Однако при использовании МВС в качестве топливного газа выбросы СО2 и СО уменьшаются в полтора раза. Расчеты специалистов показали, что содержание водорода в МВС может изменяться от 0 до 44–48 % как путем изменения температуры нагрева парогазовой смеси, так и путем разбавления товарной МВС природным газом.
Метано-водородное топливо может быть преобразовано в дальнейшем в синтез-газ для применения в процессах газохимии (GTL), либо из него может быть выделен водород как целевой продукт для различных отраслей с помощью методов PSA (короткоцикловой адсорбции) или мембранных крупнотоннажных технологий, освоенных в мировой практике.
2.2. Газификация угля
Газификация угля – процесс высокотемпературного взаимодействия угля с парами воды, кислородом, диоксидом углерода или их смесями, с целью получения горючих газов: Н2, СО, СH4. Они могут использоваться как топливо и как сырье для химической промышленности. Газифицироваться могут практически все виды газообразных, жидких и твердых топлив. Выбор сырья для процесса обычно бывает обусловлен экономическими соображениями, а иногда – направлением дальнейшей переработки образующейся газовой смеси.
Существуют различные типы процессов газификации углей. Наиболее эффективным и отработанным в промышленном масштабе, является процесс газификации угля под давлением, позволяющий получать как средне калорийный бытовой газ, так и газ для последующего синтеза. Существуют различные технологии газификации углей, отличающихся организацией процесса взаимодействия топлива и окислителя. Например, газификация с неподвижным или псевдоожиженным слоем или же со с путным потоком пылевидного топлива. Газификация проводится в специальных аппаратах – газогенераторах, которые также отличаются друг от друга в зависимости от типа процесса. При использовании воздушного дутья получается низкокалорийный газ (до 7 МДж/м3), в случае кислородного дутья – средне калорийный газ (до 17 МДж/м3). В то время как генераторы с воздушным дутьём работают при атмосферном давлении, генераторы с кислородным дутьём работают преимущественно при повышенных давлениях, что приводит к увеличению выхода метана.
Газификацией твердого топлива с парокислородным дутьем происходит под высоким давлением при температуре около 1500°С и последующим метанированием. На рис. 2.7 схематически показаны реакционные зоны газификатора. В нижней части реактора непосредственно над колосниковой решеткой, через которую непрерывно поступает газифицирующий компонент (перегретый пар и кислород), находится зона горения (окислительная зона) с основными реакциями образования СО2. Над ней расположена первичная восстановительная зона (зона теплопоглощения) с основными реакциями раскалённого углерода и водяного пара, в которой генерируется Н2. Еще выше находится вторичная восстановительная зона (зона прогрева топлива) с основными реакциями образования СО, СО2 и Н2.

Рис. 2.7. Реакционные зоны в газогенераторе
Образовавшийся в окислительной и восстановительных зонах диоксид углерода (при недостатке кислорода) восстанавливается новыми порциями углерода в оксид углерода СО. При взаимодействии СО и Н2 может образовываться метан, который в процессе подвергается термическому распаду СО + 3Н2 = СН4 + Н2О + 203,7 МДж/кмоль, СН4 = С + 2Н2–71,1 МДж/кмоль.
В верхней части реактора имеется газовое пространство с газ выпускным отверстием. Ниже располагается зона выделения летучих или зона полукоксования. Сочетание всех этих основных реакций определяет состав образующегося газа, который изменяется по высоте газификатора. Таким образом, генераторный газ обычно получают продуванием смеси воздуха или кислорода с паром через слой угля, организуя неполное сгорание топлива.
При анализе реакционных зон (без учёта зольной зоны над колосниками) в противоточной установке можно выделить три основные зоны. В нижней зоне происходит окисление угля до СО2 (окислительная зона), в средней зоне СО2 восстанавливается до СО (восстановительная зона). Эти зоны вместе называются зоной газификации, из которой выходят горячие газы с температурой 800–900°С. Они нагревают уголь, который подвергается пиролизу в вышележащей зоне. Эту зону принято называть зоной пиролиза (зоной выделения летучих), или зоной полукоксования. Выходящие из этой зоны газы подогревают уголь в зоне сушки. Вместе эти две зоны образуют зону подготовки топлива. В газификаторе протекают как экзотермические, так и эндотермические реакции. При этом отношение СО/СО2 зависит от различных факторов: избытка воздуха, температуры процесса и способа контактирования части топлива с окислителем и других.
В таблице 2.3 приведены характеристики продуктов термического разложения при различных температурах.
Таблица 2.3. Характеристики продуктов термического разложения (коксования) углей

Паровоздушная газификация крупнокускового топлива для получения отопительного газа осуществляется в стационарных газификаторах прямого процесса с непрерывным процессом в плотном слое, как в установках атмосферного давления с гидравлическим затвором и твердым шлакоудалением, так и в установках под давлением (процесс Лурги).
Паровоздушная газификация мелкозернистых топлив осуществляется в кипящем слое. Газификация пылевидного топлива на паровоздушном дутье практически осуществляется путем неполного сгорания в прямоточном факеле.
Видно, что в разных температурных режимах процесса газификации можно получать различные продукты, которые могут быть отобраны из газификатора после прохождения их через зоны постепенно снижающихся температур при противотоке топлива и газов (прямой процесс) или после пропускания их через зоны повышающихся температур при параллельном токе топлива и газов (обратный процесс).
Коксование– разновидность сухой перегонки (пиролиза) каменного угля без доступа воздуха, с целью получения кокса, горючих газов и сырья для химической промышленности.
Под процессом полукоксования понимают термическую переработку угля при 500–600°С, среднетемпературное коксование – при 700–800°С, высокотемпературное коксование – при 950°С и выше.
В настоящее время существует более 70 типов газогенераторных процессов, часть которых используется в промышленных масштабах. Это объясняется прежде всего различием физических и химических свойств угля из разных месторождений: по элементарному составу, происхождению, содержанию летучих веществ, содержанию и составу золы, влажности, соотношению Н/С в угольной массе, спекаемости углей, их термической стойкости. Не менее существенным является и различие во фракционном составе добываемых углей: крупнокусковой уголь, угольная мелочь, топливная пыль. Наконец, различаются требования к получаемому конечному продукту:
– генераторный (энергетический) газ с теплотой сгорания 3800–4600 кДж/нм3;
– синтез-газ (технологический) для химической технологии с теплотой сгорания 10 900–12 600 кДж/нм3;
– восстановительный газ (для металлургических и машиностроительных производств) с теплотой сгорания 12 600–16 800 кДж/нм3;
– городской газ (отопительный) с теплотой сгорания 16 800–21 000кДж/нм3;
– синтетический природный (богатый) газ для транспортировки на дальние расстояния – 25 000–38 000кДж/нм3.
При всем своем многообразии процессы газификации делят на два основных класса:
Автотермические процессы газификации, в которых тепло, необходимое для проведения эндотермических процессов, для нагрева газифицируемого материала и газифицирующих средств до температуры газификации (900–1200°С), производят за счет сжигания в кислороде части газифицируемого топлива до диоксида углерода.
Аллотермические процессы газификации, в которых сжигание и газификация разделены, и тепло для обеспечения прохождения процесса газификации подводится через теплопередающую стенку внутри единого газогенераторного объема или при помощи автономно нагретого теплоносителя, который вводится в газифицируемую среду.
Типичные составы газов, получаемых в автотермических и аллотермических процессах представлен в таблице 2.4.
Таблица 2.4. Типичные составы газов, получаемых в автотермических и аллотермических процессах

Как автотермические, так и аллотермические процессы газификации в зависимости от зернистости топлива могут протекать в плотном и «кипящем» слоях (крупнокусковое топливо), в аэрозольном потоке (топливная пыль). Эти принципы проведения гетерогенных процессов, разработанные в газогенераторной технике, получили широкое применение в химической технологии при проведении, например, гетерогенных каталитических процессов.
Для всех этих производств характерны большие единичные мощности агрегатов и отсутствие ограничений по потокам энергии. Общий вид промышленной установки газификации угля представлен на рис. 2.8.

Рис. 2.8. Установка газификации угля
Параметры, определяющие активность и скорость процессов газификации:
– тип газифицирующего агента: воздух, водяной пар, кислород;
– температура и давление процесса: Т=850–2000°С, р=0,1–10МПа;
– способ образования минерального остатка и его удаление: высокотемпературный процесс (1300–1400°С, зольная часть угля из генератора выводится в виде жидкого шлака, конечный продукт газификации-смесь СО+Н2; низкотемпературный или среднетемпературный процесс (1200–1250°С), зольная часть угля из генератора выводится в сухом виде;
– способ подачи газифицирующего агента: оксогазификация и гидрогазификация;
– способ отвода тепла в реакционную зону: автотермическое, аллотермическое.
К настоящему времени освоены различные модификации промышленных процессов газификации углей, наиболее распространенными из которых являются процессы Лурги (стационарный слой кускового угля), Винклера (кипящий слой угольных частиц), Копперс—Тотцека (пылеугольный поток) и их различные модификации. На опытно-промышленном уровне сейчас отрабатывается около 20 технологий газификации угля нового поколения.
2.2.1. Процесс ЛургиГазогенераторы Лурги являются одним из старейших типов газогенераторов, которые до сих пор широко используется в мире. Они работают на всем спектре углей, от антрацита до бурых углей.
На рис. 2.9 представлена принципиальная схема газогенератора.

Рис. 2.9. Схема газогенератора Лурги
Уголь находится в реакционном объеме газогенератора примерно 1 час пока окислитель и пар протекают через решетку и слой угля. На рис. 2.10 показано как уголь и газы движутся навстречу друг другу. Это делает устройство газогенераторов Лурги энергоэффективной технологией газификации. Наибольшие температуры (от 615 до 760°С) достигаются сразу над решеткой, где и происходит газификация кокса. Горячие газы поднимаются вверх и поступают в камеру охлаждения, которая расположена выше зоны газификации. В средней части слоя, поднимающиеся горячие газы пиролизуют уголь, в результате чего образуются пиролизные смолы и кокс. В верхней части слоя (самый холодный участок) уголь нагревается и сушится перед поступлением в зону пиролиза. Синтез-газ и смолы выходят из реактора при температуре 370–590°С. По сравнению с другими процессами газификации, рабочие температуры в газогенераторах Лурги относительно низкие, в связи с чем не требуется их футеровка.

Рис. 2.10. Противоточное движение газ/твердое топливо
Вследствие того, что слой должен быть свободно движущимся, в газогенераторах такого типа могут использоваться только неспекающиеся марки углей. Высокодисперсное топливо в данной технологии не используется, т. к. мелкие частицы локально затыкают межпоровое пространство между большими кусками угля, ухудшая тем самым газодинамические свойства слоя. Средний фракционный размер используемого топлива составляет ~30 мм, что является недостатком данной технологии, т. к. требует дополнительной операции сортировки (просеивание) поступающего угля. Газогенераторы Лурги производят значительное количество смол (в зависимости от марки угля до 30 % органической массы), затрудняющих их эксплуатацию, в частности это приводит к ограничению срока службы шлюзовой камеры, что является еще одним недостатком. Покидающие реактор горячие газы охлаждаются циркулирующим потоком воды. Жидкость после охладителя, состоящая из большого количества смол и надсмольной воды, используется для дальнейшего производства органических жидкостей. Надсмольная вода содержит водорастворимые соединения смол, включая фенол и крезоловую кислоту (смесь изомеров метилфенолов).
Увеличение давления позволяет существенно повысить теплоту сгорания получаемого газа за счет протекания реакций метанирования. Эти реакции экзотермичны, благодаря чему при давлении 2,8–3 МПа можно сократить потребность в кислороде на 30–35 %. Кроме того, одновременно возрастает производительность газогенератора (пропорционально давлению) и повышается КПД газификации.
Этот технологический процесс доказал свою коммерческую успешность, а получаемая продукция особенно хорошо подходит для использования в производстве синтетического природного газа или восстановлении железной руды (ГБЖ).
Недостатки метода Лурги:
– жесткие ограничения по размерам частиц – не менее 5 мм (так как при большом содержании мелочи снижается производительность аппарата);
– наряду с газификацией происходит термическое разложение топлива с образованием продуктов полукоксования, которые необходимо извлекать из газа и перерабатывать;
– низкая степень разложения водяного пара (30–40 %), вследствие чего остальное его количество при охлаждении газа конденсируется с образованием химически загрязненной воды, требующей тщательной очистки.
2.2.2. Процесс Копперса-ТотцекаВ процессе Копперса-Тотцека твердые топлива газифицируют кислородом и водяным паром при нормальном давлении в режиме прямотока (т. е. сырье и газифицирующий агент движутся в одном направлении). На рис. 2.11 представлена общая схема газификаторов такого типа. Первая промышленная установка была введена в эксплуатацию в 1952 году в Финляндии. Эта технология позволяет перерабатывать любой уголь, причем его фракционный состав не должен превышать 0.1 мм. Температура размягчения золы имеет непринципиальное значение, так как данная технология основана на жидком шлакоудалении. Пылевидный уголь (верхний предел зольности по экономическим соображениям составляет около 40 % на сухую массу угля, а влажность – 6–8 % для бурых и 1–2 % для каменных углей) потоком азота подается в расходные бункера, откуда шнеком направляется в форсунки, захватывается потоком кислорода и водяного пара и распыляется в камеру.

Рис. 2.11. Схема газификатора Копперса-Тотцека
Соотношение потоков на 0,05–0,5 кг пара. При этом подача пара организована таким образом, чтобы он «обволакивал» пылеугольный факел снаружи, тем самым предохраняя футеровку от зашлаковывания, эрозии, а также действия высоких температур. В реакционной камере достигается высокая степень превращения органической части угля с образованием смеси газов. Состав сырого газа изменяется в следующих пределах (% об.): СО -55–66, Н2– 21–32, С02– 7–12, N2– около 1, H2S – 0,5–1, СН4– 0,1. Теплота сгорания газа составляет 10–12 МДж/м3. При использовании низко реакционного топлива (например, кокса) содержание СО2 повышается, а Н2 снижается, при высоко реакционном топливе, наблюдается противоположный эффект. Полученный газ вначале проходит котел-утилизатор, вырабатывающий пар высокого давления, затем осуществляется его очистка. После обработки в скрубберах Вентури содержание пыли составляет около 5–15 мг/м3. В случае необходимости оно может быть снижено до 0,25 мг/м3 при пропускании газа через электрофильтр. Затем газ охлаждается и подвергается обессериванию традиционными методами.
Температуры газификации составляет обычно 1500–1700°С, в следствии чего достигается высокая степень конверсии углерода, при этом почти все органические вещества угля превращаются в газообразные продукты, в которых практически отсутствуют пиролизные смолы. Это существенно упрощает очистку продукт-газа. Еще одним достоинством данного метода является возможность переработки практически любых топлив независимо от их спекаемости.
Различные конструкции реакторов данного типа позволяют проводить процесс во вращающемся или вихревом потоке, в потоке, направленном вверх или вниз, а также с переменным направлением. При любом варианте топливо сначала реагирует с кислородом, при этом достигается максимальная температура, а затем накопленный потенциал тепла расходуется в эндотермических реакциях газификации.
Для получения водорода процесс Копперса-Тотцека достаточно эффективен.
Одним из недостатков процесса является необходимость в использовании дорогостоящих мельниц для тонкого размола топлива, а также повышенный расход кислорода по сравнению с другими методами газификации. Главной проблемой при эксплуатации данных газогенераторов является необходимость в обеспечении бесперебойной подачи пылевидного топлива, так как из-за малого времени его пребывания в реакционной зоне незначительные перерывы в питании могут привести к появлению свободного кислорода в камере и других частях, что может привести к взрывоопасной ситуации. Необходимо подчеркнуть, что именно этот способ сейчас наиболее распространен в мире.
2.2.3. Процесс ВинклераГазогенераторы Винклера, коммерциализованные в 1926 году, являются первым промышленным применением технологии газификации в кипящем слое. Газогенераторы Винклера работают при давлении близком к атмосферному, в режиме кипящего псевдоожиженного слоя. Уголь измельчают до размеров менее 8 мм. Как показано на рис. 2.12 уголь поступает в бункер, а затем шнековым питателем подается в объем газогенератора, где создается кипящий слой. Поскольку слой находится практически при атмосферном давлении, могут использоваться относительно простые системы подачи угля. Подаваемый в газогенератор газифицирующий агент, состоящий из пара, а также воздуха или кислорода, разбит на два потока. Газ, подаваемый через колосник, ожижает слой и реагирует с ним. Частицы угля в результате горения уменьшаются в размере и становятся более легкими. Примерно 30 % золы проваливаются сквозь колосник и образуют «донную» золу. Оставшиеся 70 % золы улавливаются гидроциклоном и возвращаются в газогенератор, увеличивая тем самым тепловую емкость и инерцию слоя, а также для повторной конверсии остатков углерода в ней.

Рис. 2.12. Схема газогенераторов Винклера
К преимуществу технологий кипящего слоя можно отнести возможность введения дополнительных реагентов, помимо угля и инертного материала. В частности, введение в кипящий слой соединений кальция (обычно известняк или доломит) позволяет связывать серу, находящуюся в угле. Преимуществом этих газогенераторов является возможность использования более широких фракций угля, включая мелочь, которая выносится из слоя и газифицируется в надслойном пространстве. Основной же проблемой данных газогенераторов является то, что унесенная зола содержит значительное количество непрореагировавшего углерода. Температура кипящего слоя составляет примерно 1000–1100°С, что чуть ниже температуры размягчения золы. Для максимализации конверсии углерода рабочая температура слоя находится близко к этой лимитирующей температуре. Тепло отводится через верхнюю часть газификатора. Газогенераторы Винклера ранее широко использовались, но недолго, в настоящее время практически нигде не используются из-за низкой степени конверсии углерода.
В 1970–80 гг. был разработан высокотемпературный газогенератор Винклера. Главным отличием от оригинальной конструкции явилась возможность работы под давлением (примерно 1 МПа). Увеличение давления позволило повысить степень конверсии углерода. Работа под давлением повлекла изменения в системе подачи угля, рис. 2.13. Уголь при атмосферном давлении загружается в бункер. Далее в одной из двух шлюзовых камер сбрасывается давление и в нее поступает уголь из бункера. Затем входной клапан закрывается и в камеру нагнетается давление, после чего открывается нижний клапан и уголь проваливается на линию, где пневматически транспортируется на фильтр.

Рис. 2.13. Схема высокотемпературного генератора Винклера
Газ после фильтра повторно идет в компрессор, а уголь поступает в загрузочный бак. Питание газогенератора происходит за счет дозирующего клапана, расположенного на дне загрузочного бака. Использование двух шлюзовых камер позволяет данным газогенераторам работать в непрерывном режиме.
Процесс имеет существенные достоинства:
– возможность непрерывной подачи топлива в газогенератор;
– интенсивную теплопередачу и хорошее перемешивание, обеспечивающее изотермический режим в реакционной зоне;
– простоту регулирования температуры и высокую производительность аппарата.
Наиболее предпочтительными топливами для газификации по этому методу являются бурые и реакционноспособные каменные угли, буроугольный кокс или полукокс. Усовершенствование процесса Винклера возможно путем повышения температуры и давления процесса.
У процесса есть следующие недостатки:
– большой унос с газом непрореагировавшего топлива, которое трудно возвратить на газификацию,
– пониженные температуры в зоне реакции, лимитируемые выводом золы в сухом виде;
– невозможность переработки спекающихся каменных углей из-за слипания их частиц нарушается режим работы газогенератора;
– сложная система загрузки топлива.
Для сравнения процессов, рассмотренных выше в таблице 2.5, приведены основные их показатели.
Таблица 2.5. Основные показатели процессов газификации твердых топлив

Наряду с рассмотренными выше методами газификации угля, которые можно сейчас уже назвать классическими, начиная с середины прошлого столетия в разных странах интенсивно разрабатываются более прогрессивные методы. В ряде случаев они представляют собой усовершенствованные варианты рассмотренных процессов.