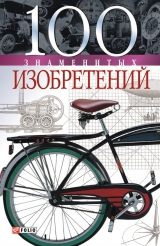
Текст книги "100 знаменитых изобретений"
Автор книги: Владислав Пристинский
Жанры:
Публицистика
,сообщить о нарушении
Текущая страница: 17 (всего у книги 47 страниц) [доступный отрывок для чтения: 17 страниц]
Ледокол
Люди издавна стремились проникнуть в полярные моря и освоить их. Русские поморы и норвежские китобои плавали в Арктике летом, добираясь при благоприятных условиях до сравнительно высоких широт.
В 1733 г. в России была организована Великая северная экспедиция, перед которой стояла задача нанести на карту все побережье Северного Ледовитого океана и собрать разнообразные сведения о северных морях. Позже мореплаватели прилагали немало усилий, чтобы найти Северо-западный и Северо-восточный проходы в южные моря или достичь Северного полюса. Но все эти экспедиции терпели неудачу.
Одной из причин неудач было отсутствие кораблей, способных противостоять разрушающей силе льдов. При движении ледяных полей на судно наступает огромный ледяной вал, достигающий огромной высоты. Он может превратить корабль в груду смятого железа.
Активная борьба со льдом стала возможной, когда появились корабли со стальным корпусом и паровым двигателем.
В 1864 г. сообщение между Кронштадтом и Ораниенбаумом поддерживалось небольшими пароходами. Их владелец, промышленник Бритнев, изменил форму носа у одного из них, «Пайлота», как бы подрезав его. В результате пароход стал налезать на льдины и расталкивать их. Это позволило продлить на несколько недель сообщение, обычно прерывавшееся с началом ледостава.
Бритнев не преследовал цель создать специальное судно для плавания во льдах и продал чертежи своего изобретения немцам.
Немецкие инженеры построили суда с ложкообразной формой носа. Самое крупное из них имело водоизмещение около 900 тонн, самое маленькое – 90 тонн. Впоследствии все они получили название «гамбургских ледоколов». Они расчищали заторы на реке Эльба и восстанавливали сообщение с портом Гамбург. Они хорошо работали в ровном льду без торосистых нагромождений. Но для ледовых условий на морях и океанах такая форма носа оказалась малоподходящей: ложкообразные обводы носа способствовали скоплению снега и льда перед форштевнем, ледокол сильно рыскал на ходу, а иногда застревал во льдах.
В 1893 г. норвежский ученый Ф. Нансен построил специальное судно «Фрам». Корпус этого судна имел округлую яйцеобразную форму, поэтому льды не могли разрушить его, выжимая вверх. Нансен преследовал цель достичь Северного плюса, дрейфуя вместе со льдом. Это ему не удалось, но в течение всего путешествия, длившегося три года, «Фрам» оставался невредимым.
К концу XIX в. было построено немало ледоколов, но все они могли работать лишь в слабых ледяных полях и были бессильны против мощных льдов и торосистых нагромождений.
Русский адмирал и ученый С. О. Макаров решил создать новый мощный ледокол, способный плавать в арктических льдах. Для этого Макаров изучил опыт «Фрама», знакомился с работой ледяных паромов на американских озерах Гурон, Мичиган и Эри, изучал летние условия плавания в Карском море. Благодаря этому он понял, каким должен быть будущий ледокол.
Детище Макарова было построено в Ньюкасле на верфях фирмы «Армстронг и Витворт». Ледокол получил название «Ермак».
В марте 1899 г. «Ермак» подошел к Кронштадту. В это время льды в Финском заливе достигают наибольшей толщины. Несмотря на это, «Ермак» пробил канал во льдах, сковавших Большой Кронштадтский рейд, и вошел в гавань. До него ни одно судно в это время года не могло войти в Кронштадт.
Летом того же года «Ермак» совершил первое арктическое плавание. Во время плавания возникла течь, и ледокол вернулся на ремонт в Ньюкасл. Летом того же года «Ермак» вновь вернулся в Арктику, но испытания завершились пробоиной в носу.
В 1901 г. ледокол исследовал район севернее Шпицбергена. Спустя несколько дней после выхода из порта Тромсе он попал в сплошной лед и остановился у побережья Новой Земли. Около месяца «Ермак» был зажат льдами. В конце июля ледовая обстановка улучшилась, и «Ермак» весь август работал в Арктике. За время плавания он прошел свыше 200 миль в условиях, где любой другой корабль погиб бы. Расчеты адмирала Макарова оказались правильными.
Долгие годы «Ермак» плавал на Балтике. За первые 12 лет он провел в Финском заливе свыше 1000 судов. В феврале 1918 г. в порту Ревеля (ныне Таллинн) были скованы льдом корабли Балтийского флота. Портовые ледоколы не могли разбить лед, а в это время на Ревель надвигались немецкие войска. На помощь эскадре пришел «Ермак». Он взломал лед и вывел большую часть кораблей из гавани. 25 февраля они ушли в Гельсингфорс (Хельсинки). Но и из Гельсингфорса вскоре пришлось уйти. 12 марта эскадра направилась в Кронштадт. Ей предстояло пройти 200 миль. Дорогу кораблям прокладывали «Ермак» и вспомогательный ледокол «Волынец».
Несмотря на торосистый лед, туманы и обстрел, корабли тремя отрядами пришли в Кронштадт. Решающий вклад в успех этого беспримерного похода внес «Ермак».
С началом освоения Северного морского пути «Ермак» был направлен в Арктику. Он выводил замерзшие во льдах пароходы, доставлял им продукты и топливо.
В феврале 1938 г. «Ермак» участвовал в снятии с льдины экипажа станции «Северный полюс», которую возглавлял И. Д. Папанин.
В 1938 г. за пять месяцев плавания «Ермак» освободил из ледового плена 17 и провел в Карское море и море Лаптевых 10 пароходов. В том же году он достиг 83-го градуса северной широты. До этого ни одно судно, самостоятельно передвигаясь во льдах, не достигало таких высоких широт.
Во время Великой Отечественной войны ветеран проводил на буксире в Кронштадт и обратно баржи с углем, продуктами и оборудованием, госпитальные суда.
В 1949 г. ледокол был награжден орденом Ленина. «Ермак» был в строю до 1963 г.
В 1917 г. в Англии был построен ледокол «Святогор», в 1927 г. переименованный в «Красин». В 1928 г. «Красин» участвовал в спасении участников экспедиции У. Нобиле, которые потерпели катастрофу на дирижабле «Италия».
В 1932 г. «Красин» совершил первое зимнее плавание в Арктике, а в 1933 г. впервые достиг зимой северной оконечности Новой Земли.
В 1932 г. советский ледокольный пароход «Сибиряков» впервые прошел Северный морской путь за одну навигацию. Он вышел из Архангельска в июле. Проходя льды у побережья Чукотки, судно повредило винт, но экипажу удалось отремонтировать повреждение. Затем от удара о ледяную глыбу обломился конец гребного вала и пошел ко дну вместе с винтом. Моряки взрывали лед аммоналом, а когда судно вышло на чистую воду, подняли на мачтах брезентовые полотнища. 1 октября 1932 г. «Сибиряков» вышел в Берингов пролив.
Конструкция ледоколов рассчитана на очень большую нагрузку. Ледокол редко двигается непрерывно, чаще он останавливается, отходит назад и наскакивает на льдину с разбега. Иногда ему приходится ударять в лед и кормой. Чтобы вползти на льдину, форштевень и ахтерштевень (носовая и кормовая части судна) имеют уклон 23–25°. Весь ледокол, особенно его нос и корма, должны быть прочными, а их штевни – массивными. Так, форштевень советского ледокола «Сибирь», построенного в начале 40-х гг., весил 26 тонн, а ахтерштевень – 36 тонн. У обычных судов вес этих частей не превышает 6–7 тонн.
Один квадратный метр борта «Ермака» выдерживал нагрузку в 55 тонн, а «Сибири» – 75 тонн. Шпангоуты на ледоколах, особенно в носовой и кормовой части, установлены чаще, чем на других судах.
Стремление к повышенной прочности корпуса усложнило его конструкцию. Повышенная жесткость достигается применением многочисленных палуб и платформ. К поперечным водонепроницаемым переборкам, которые есть на каждом судне, добавлены продольные, отделяющие машинные и котельные помещения. Двойное дно судна переходит во второй борт.
Вдоль ватерлинии судна обшивка утолщена и образует так называемый ледовый пояс в том месте, где корпус ледокола наиболее часто соприкасается со льдом. На «Ермаке» высота ледового пояса достигала 5,4 м, на «Сибири» – 6,1 м.
Непрерывным ходом ледоколы могут сокрушать сравнительно тонкий лед. «Ермак» и «Красин» ломали ходом лед толщиной 50–60 см. Особенно тяжелые льды ледоколы бьют «звездочкой», ударяя в одно и то же место, но в разных направлениях.
Если ледокол, ударив в лед, не расколол его и застрял, в действие приводится креново-дифферентная система. Электрические помпы начинают качать воду в носовую дифферентную цистерну, нос судна становится тяжелее и сильнее давит на лед. Вода поочередно перекачивается из цистерн правого борта в левый и наоборот. Ледокол начинает бортами давить на лед.
Если не удается выйти из ледового плена, с кормы на лед подают так называемый ледовой якорь, лапу которого вставляют в пробитую лунку. Машины работают назад, лебедка выбирает трос, и ледокол сам стаскивает себя с льдины. В крайних случаях лед взрывают.
Машины ледоколов работают в очень жестком режиме. Они дают то передний ход, то задний. Число реверсов машины может достигать 15–20 в минуту. На первых ледоколах стояли паровые поршневые машины. Они оказались простыми и надежными для эксплуатации во льдах: быстро меняли режим работы, долго и безаварийно действовали на переменных ходах, легко меняли направление вращения. Но при движении ледокола во льду из-за возрастающего сопротивления скорость хода значительно уменьшалась, паровая машина снижала количество оборотов. В результате снижалась мощность в тот момент, когда она была нужна судну.
Позже на ледоколах в качестве главных двигателей стали устанавливать дизели. Они неустойчиво работают при малых нагрузках и не выносят длительных перегрузок, возникающих при движении ледокола во льдах. Этот недостаток был преодолен с помощью электрической передачи. Дизель равномерно вращает электрогенератор, подающий энергию на моторы, вращающие гребные винты. Гребные двигатели работают в переменном режиме, потребляя нужное в данный момент количество электроэнергии. Число их оборотов легко регулируется, что позволяет подобрать наиболее выгодный для работы режим и использовать полную мощность для работы на заднем ходу. Каждый гребной двигатель обслуживается 2–3 генераторами.
Уязвимым местом ледоколов являются гребные винты: их лопасти часто гнутся и ломаются под ударами льдин. Чтобы защитить лопасти и руль от ударов, ледоколы имеют максимально возможную осадку. Но кормовым винтам грозят также и льдины, скользящие по корпусу судна. Для их защиты на корпусе сделаны своеобразные «ножи», отводящие льдины от винтов.
Гребные винты ледоколов не отливаются целиком как обычно, а имеют съемные лопасти, которые в случае повреждения можно заменить запасными. Винты делаются из специальных ванадиево-никелевых сплавов. Винты обычно имеют 4 лопасти: при меньшем количестве куски льда, застревающие между ними, ломают винт.
В 1957 г. в СССР был спущен на воду первый в мире атомный ледокол «Ленин». Он имел водоизмещение 16 000 тонн и мощность главных турбин 44 000 л. с. «Ленин» мог работать целый год, не заходя в порт.
В 1977 г. другой советский ледокол, «Арктика», дошел до Северного полюса, осуществив мечту Ф. Нансена.
Ледоколы сыграли важную роль в освоении Арктики, расширив возможности доставки людей и грузов в ранее недоступные районы.
Литье стали
В середине XIX в. в связи с быстрым ростом производства резко выросла потребность в стали. Существовавшие в то время кричный передел, тигльная выплавка стали и пудлингование не могли удовлетворить эту потребность.
В конце 1854 г., в разгар Крымской войны, на Венсенском полигоне во Франции испытывался мощный артиллерийский снаряд конструкции англичанина Генри Бессемера. Глава экспертной комиссии капитан Минье отметил, что дело за малым: создать еще и пушку для стрельбы такими снарядами. Это побудило Бессемера начать разработку новой пушки.
Первое – материал, способный выдержать значительные напряжения при стрельбе снарядами крупного калибра. Использовавшиеся в то время бронза и чугун его не устраивали, и он решил получить чугун более высокого качества. Свои опыты Бессемер сначала проводил в небольшом горне, затем в пламенной (пудлинговой) печи. Во время очередного эксперимента он обратил внимание на несколько кусков чугуна, которые, несмотря на сильный жар, не расплавлялись. Изобретатель пустил сильную струю воздуха, чтобы усилить сгорание. Спустя полчаса Бессемер увидел, что от кусков чугуна остались лишь тонкие пленки обезуглероженного железа. Итак, атмосферный воздух может обезуглероживать чугун, превращая его в ковкое железо без пудлингования и других операций. То, что происходит в металле, когда на него воздействуют воздухом, сам Бессемер объяснял так: содержащийся в чугуне «углерод не может в условиях белокалильного жара находиться в присутствии кислорода, не соединяясь с ним и, таким образом, не производя горения… Следовательно, достаточно привести в соприкосновение кислород и углерод так, чтобы значительные их количества подвергались взаимному действию, чтобы получить температуру, не достигнутую до сих пор в крупнейших печах». Хотя на самом деле больше тепла выделяется при реакции с кислородом не углерода, а кремния, суть идеи от этого не менялась: для обезуглероживания расплавленного чугуна его следует продувать воздухом.
Эта гениальная идея, вскоре совершившая переворот в металлургии, сначала казалась многим, по меньшей мере, нелепой. Так, когда Бессемер сказал литейщику, нанятому для проведения практических плавок, что хочет продуть холодный воздух через жидкий металл, тот без сомнения заявил: «Металл весь скоро превратится в глыбу». И мастер очень удивился, когда после продувки в изложницу по желобу полилась ослепительная струя металла. Бессемер писал: «Я не в состоянии передать, что я чувствовал, когда увидел эту раскаленную массу, медленно поднимающуюся из формы. Это был первый большой слиток литого железа, который когда-либо видел человеческий глаз».
В 1856 г. Бессемер взял патент на продувку раскаленного чугуна воздухом. Сначала он проводил опыты в небольшом лабораторном сосуде. Попытка перейти к экспериментам в более крупных масштабах едва не закончилась катастрофой. Для опытов Бессемер решил использовать сосуд-конвертер (от латинского слова convertere —превращать) высотой чуть более метра, изготовленный из листового железа и выложенный внутри огнеупорным кирпичом. Не прошло и десяти минут после начала продувки, как из отверстия в крышке внезапно вылетел сноп искр, который с каждым мигом все ширился и ширился, пока не превратился в столб пламени. Раздались громкие хлопки, и высоко в воздух начали извергаться расплавленный металл и шлак. Конвертер напоминал вулкан во время извержения. Бессемер мог только наблюдать, понимая, что в любой момент мог начаться пожар или произойти взрыв. К счастью, спустя несколько минут «извержение» прекратилось. Полученный металл оказался ковким железом.
Взволнованный изобретатель повторил эксперимент, приняв, как он полагал, надлежащие меры против огненного фонтана: над отверстием конвертера он подвесил на цепи чугунную крышку. Но при новой продувке вновь началось извержение. Крышка быстро раскалилась, стала плавиться и через несколько минут о ней напоминал лишь обрывок цепи.
Новый способ получения стали многими был встречен скептически. И когда Бессемер решил взять патент на свое изобретение в Германии, прусское патентное ведомство отказало ему, мотивировав свое решение тем, что «никому нельзя запретить продувать воздух через жидкое железо».
В течение нескольких лет английский изобретатель усовершенствовал свой процесс. Бессемерование чугуна – это процесс превращения жидкого чугуна в литую сталь путем продувки сжатым воздухом. Продувка проводится в специальном резервуаре – конвертере. Превращение чугуна в сталь в конвертере происходит благодаря окислению углерода и примесей (кремния, марганца), содержащихся в чугуне, кислородом воздуха. Процесс бессемерования происходит без подвода тепла извне и без применения какого-либо горючего материала: тепло, необходимое для процесса, образуется благодаря окислению железа и его примесей.
Практически бессемерование происходит следующим образом. Чугун в том виде, в каком он изливается из доменной печи, заливается в конвертер – резервуар, похожий на грушу с отверстиями на дне для подвода воздуха. Он укреплен на двух подвижных опорах, по одной с каждой стороны, что позволяет переводить его из горизонтального в вертикальное положение и наоборот.
Наполнив конвертер, его поворачивают в вертикальное положение и через отверстия начинают вдувать воздух, который пузырьками проходит через расплавленный металл. Кислород воздуха при этом приходит в соприкосновение с каждой частицей чугуна и в результате соединяется с углеродом, находящимся в чугуне. Когда процесс закончен, конвертер переводят в горизонтальное положение и прекращают вдувание воздуха. После окончания процесса в конвертере образуется железо, в которое затем добавляют строго определенную дозу примеси, содержащей углерод, поддерживающий дальнейший процесс окисления железа. В результате в конвертере образуется сталь, содержащая требуемый процент углерода.
Процесс бессемерования протекает чрезвычайно быстро, продолжительность его не превышает 15 минут. Количество перерабатываемого чугуна и пропускная способность конвертера весьма велики: в конвертере 10–15 тонн чугуна превращается в железо или сталь в течение 10 минут. В пудлинговой печи на это уходило несколько дней. По качеству бессемеровская сталь во многом превосходила пудлинговое железо.
Признание пришло к Бессемеру в 1862 г.: на Всемирной выставке в Лондоне с успехом демонстрировалась разнообразная продукция из бессемеровской стали. В 1867 г. на Всемирной выставке в Париже изобретатель был удостоен Большой золотой медали. В 1871 г. Бессемер был избран президентом вновь созданного британского Института железа и стали, а в 1879 г. стал членом Лондонского королевского общества.
Следует отметить, что наряду с очевидными достоинствами бессемеровский конвертер имел и недостатки. Основной из них заключался в том, что далеко не любой чугун можно было в конвертере переделывать в сталь. Если для выплавки чугуна использовались железные руды, богатые фосфором, то последний переходил в чугун, а затем и в сталь. В результате сталь становилась хрупкой и не находила применения. В конвертере нельзя переплавлять железный лом или твердый чугун, т. к. не хватает тепла, чтобы расплавить твердые куски металла. К тому же в конвертере можно получать лишь сталь, идущую на обычные нужды.
Один из недостатков конвертера исправил соотечественник Бессемера Сидни Томас. Он подошел к конвертерной плавке с точки зрения химика. На миниатюрном конвертере, вмещавшем около 2,5 кг чугуна, Томас вместе с двоюродным братом начал производить опыты по удалению фосфора из расплавленного металла. Для этого необходимо, чтобы шлаки были не кислыми, а основными, т. е. состоящими из основных окислов. Это требовало, чтобы и огнеупорная футеровка конвертера была основной, иначе она разъедалась бы шлаком и выходила бы из строя. После многочисленных опытов Томас остановился на огнеупорной футеровке, состоящей из извести, смешанной с жидким стеклом. Первые опыты были успешными, и Томас уговорил владельцев завода в Бленавоне, где работал его двоюродный брат, провести опытные плавки. После нескольких десятков плавок Томасу удалось снизить содержание фосфора в стали до сотых долей процента.
Одна из причин его успеха заключалась в следующем: примеси в чугуне выгорали в строгой очередности, зависящей от химических свойств кислорода. Первым выгорал кремний, затем марганец, частично железо. Потом доходит очередь до углерода. Как только запасы углерода иссекают, конвертерный костер начинает угасать. В этот момент металлурги прекращали продувку, считая, что больше гореть нечему, кроме железа. При бессемеровском процессе действительно не стоило продолжать продувку, но если требовалось очистить металл от фосфора, то торопиться не следовало. К этому времени фосфор в металле оставался практически в том же количестве. Томас решил продолжать продувку. И выяснилось, что фосфор сгорает с большим тепловым эффектом, почти не уступая кремнию. В 1877 г. Томас взял патент на один из вариантов технологии, связанной с удалением фосфора, и продал его, чтобы продолжать опыты. Он искал наиболее удачный материал для футеровки и постепенно пришел к выводу, что лучше всего подходит хорошо обожженный доломит. Стенки из него выдерживали воздействие извести, необходимой для создания основного шлака, поглощавшего выделяющийся из металла фосфор.
В 1878 г. Томас берет патент на свое изобретение. Спустя несколько дней после этого на сессии британского Института железа Томасу даже не дали слова, чтобы он мог рассказать о своем изобретении. Среди участников собрания был и Бессемер. Несмотря ни на что, Томас шлифовал свою технологию в промышленных условиях, и вскоре его ждал триумф. Уже после его смерти в конце XIX в. томасовский конвертер по масштабам выплывки стали уступал лишь «старшему брату» – бессемеровскому конвертеру.
Но постепенно роль конвертеров в выплавке стали начала понижаться. До середины XX в. основная нагрузка приходилась на мартеновские печи. Но конвертеры восстановили утраченные было позиции благодаря применению кислородного дутья. Эту идею выдвинул еще в 1875 г. Д. К. Чернов. По его мнению, это должно было повысить температуру металла и сократить время процесса, а также затраты на воздуходувную машину. Но реализовать эту идею стало возможным лишь тогда, когда удалось создать установки для сжижения атмосферного воздуха и получения из него кислорода. В 1933 г. советский ученый Н. И. Мозговой приступил к экспериментам по продувке жидкого чугуна чистым техническим кислородом. В 1950-е годы во многих странах были построены кислородные конвертеры. Кислородное дутье имеет серьезные преимущества: при сохранившейся высокой производительности постройка кислородно-конвертерных цехов обходится дешевле. Кислородное дутье повысило температуру в конвертере, что позволило перерабатывать большие объемы металлолома. Теперь в конвертерах можно было выплавлять легированную сталь многих марок, что раньше считалось привилегией электропечей. Сегодня кислородно-конвертерным способом выплавляется более половины всей производимой в мире стали.
Несмотря на громадное значение бессемеровской стали, проблема улучшения качества металла осталась не решенной. А специальное машиностроение требовало массового производства именно высококачественной стали. Кроме того, дешевая бессемеровская сталь вытеснила старый пудлинговый металл, и появились крупные нереализованные запасы последнего. Требовалось найти пути передела его в сталь.
Проводились опыты, в ходе которых пытались сплавить в пламенных печах чугун и железо, но в них не удавалось достичь необходимой температуры.
В 1856 г. немецкие инженеры братья Вильгельм и Фридрих Сименс сконструировали для нужд стекольной промышленности регенеративную газовую печь. Смешиваясь с воздухом, газ горел, развивая высокую температуру, достаточную для плавки даже тугоплавких металлов. Регенератор представлял собой сдвоенную камеру, заполненную решетчатой кирпичной кладкой, через которую пропускались печные газы, отдававшие кладке значительную часть своего тепла. Затем по этой же кладке в обратном направлении пропускали воздух и горючий газ, предназначенные для горения. Подогрев предотвращал охлаждение печи воздухом или газом и повышал температуру в печи примерно на 1000 градусов.
Но именно высокая температура, как ни странно, вначале тормозила внедрение регенеративных печей в металлургическое производство. Поначалу металл загружали в печь в огнеупорных тиглях, и в ходе плавки расплавлялся не только металл, но и тигль. В ряде опытов оплавлялись даже стенки печи, а однажды рухнул ее свод.
Принцип регенерации тепла и отопления печи газом использовал в своей печи французский металлург Пьер Мартен. По предоставленным В. Сименсом чертежам он построил регенеративную сталеплавильную печь, использовав для кладки ее стен и свода огнеупорный кирпич, способный выдерживать высокие температуры. Она была запущена в 1864 г. Сущность мартеновского процесса заключается в том, что сталь производится на поду регенеративных пламенных печей путем переработки в них чугуна и стального лома (скрапа). В мартеновской печи происходит не просто плавка загруженных материалов: до самого конца процесса в печи идет химическое взаимодействие между металлом, шлаком и газом.
Мартеновская печь относится к типу отражательных печей. Ванна, где идет плавка, выложена огнеупорным кирпичом. Над ванной – сферический свод. Продукты горения топлива, а вместе с ними и тепло отражаются от него и направляются в ванну, где расплавляют металл. Такая конструкция обеспечивает равномерное распределение тепла по всей площади ванны. Сначала в качестве топлива в мартене применяли смесь доменного и коксового газов, сейчас все шире используется природный газ. Нагретые в регенераторах воздух и газ подаются в верхнюю часть мартена, где смешиваются и сгорают, давая температуру до 1800–2000 °C.
Для загрузки сырья в передней стенке печи имеются завалочные окна, закрываемые стальными задвижками. В задней стене – выпускное отверстие, через которое готовую сталь сливают в ковш. Когда идет плавка, выпускное отверстие забито пробкой из огнеупорной глины.
Работа в мартеновской печи происходит в несколько этапов, сначала в печь загружают холодные материалы (шихту) – железный лом, руду, известь. Их насыпают в стальные ящики – мульды. Завалочная машина захватывает мульду, вносит через завалочное окно в печь, переворачивает, высыпая содержимое. После окончания загрузки заслонки опускают и в печь вводят максимальное количество газа и воздуха, чтобы шихта быстрее прогрелась и расплавилась. После этого к печам подвозят ковши с доменным чугуном. Его доставляют из миксера, где чугун хранится в жидком виде. Мостовой кран поочередно поднимает ковши, наклоняет их, и чугун по специальному желобу льется в печь. Выплавка стали в мартене продолжается много часов. За это время пробы металла несколько раз отправляют в лабораторию, где исследуется их химический состав. В случае необходимости в печь вводятся недостающие вещества. На последнем этапе плавки происходит очищение стали от вредных примесей и раскисление – удаление из металла кислорода. Для этого в ванну добавляют раскислители: ферросилиций, ферромарганец, алюминий.
Во второй половине XX в. были созданы двухванные печи. В них применяют не воздух, а чистый кислород. Это дает такое количество тепла, что позволяет печам обходиться без регенераторов. Их производительность в 2–4 раза выше, чем однованных, а расход топлива – в 10–15 раз меньше.
Самые большие в мире мартеновские печи построены на Мариупольском металлургическом комбинате. Объем ванны в этих печах 900 м 3.
Но даже кислород не помог мартеновским печам выдержать конкуренцию с электрическим конвертером.
Электросталеплавильный процесс ведет свое начало от электрической дуги, которую получил, экспериментируя с гальваническим элементом, профессор физики Санкт-Петербургской медико-хирургической академии В. В. Петров в 1802 г. Спустя год он опубликовал книгу «Известие о Гальвани-Вольтовских опытах», в одной из глав которой описал превращение некоторых оксидов в металлы посредством электрического тока.
В 1853 г. во Франции был взят патент на конструкцию электропечи для плавки стали. В 1879 г. Вильгельм Сименс сконструировал электропечь, в которой впервые сумел выплавить железо из руды. Однако эта печь была далека от совершенства и полученное железо содержало много примесей.
В 1891 г. создатель дуговой электросварки Н. Г. Славянов осуществил плавку стали и других металлов в небольших тигльных печах с электродами. Большой вклад в развитие электропечей внес французский ученый Анри Муассан. В 1892 г. он представил во Французской академии наук свою конструкцию, позволявшую получать температуры до 4000 °C.
Широкому применению электрического тока мешала его относительно высокая стоимость. Но эта проблема была решена после появления первых гидроэлектростанций. На стыке XIX–XX вв. Поль Эру во Франции и Эрнесто Стассано в Италии практически одновременно построили дуговые плавильные печи.
Благодаря особым условиям в плавильном пространстве, прежде всего восстановительной атмосфере и температуре до 5000 °C, металлурги получили возможность не только полнее очищать металл от нежелательных примесей, но и выплавлять легированную сталь. Спрос на электросталь резко возрос в годы Первой мировой войны, когда металл высокого качества понадобился для производства пушек, брони и других видов вооружения.
За несколько десятилетий с момента возникновения электрического способа выплавки электропечи прибавили в объеме, их конструкции стали более совершенными. Поскольку в них можно плавить даже такие тугоплавкие металлы, как вольфрам и молибден, металлурги могут плавить сталь, легированную любыми металлами. В 1940–1950-е годы в электропечах стало применяться кислородное дутье. Оно позволило увеличить производительность электропечей, сократить расход электроэнергии, электродов, дорогих легирующих добавок. Повысилось и качество металла.
В индукционных электропечах нет электродов, что позволяет получать практически безуглеродную высоколегированную сталь.
Следующим шагом в развитии электропечей стали вакуумные индукционные и дуговые печи. Создаваемое в вакуумной камере разрежение заставляет пузырьки газа выходить из жидкого металла.
Современные методы литья позволяют производить качественную сталь без дефектов. Это помогает сократить дальнейшую механическую обработку и получить высокие эксплуатационные свойства материала.