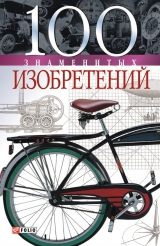
Текст книги "100 знаменитых изобретений"
Автор книги: Владислав Пристинский
Жанры:
Публицистика
,сообщить о нарушении
Текущая страница: 10 (всего у книги 47 страниц) [доступный отрывок для чтения: 17 страниц]
Железо
Современную цивилизацию невозможно представить без железа, ведь 95 % металлопродукции, производимой в мире, приходятся на различные сплавы железа. На протяжении веков железо играло и продолжает играть роль важнейшего конструкционного металла материальной культуры человечества.
Первое железо, которое стал использовать человек, было в самородном состоянии. Но в отличие от меди, золота или серебра, которые встречаются на Земле довольно часто в виде слитков, железо быстро окисляется кислородом, и в чистом виде встречается очень редко. А самородное железо буквально падало на головы наших предков с неба. Ежегодно на поверхность Земли выпадают тысячи тонн метеоритного вещества, содержащего до 90 % железа. Как правило, такие метеориты весят несколько килограммов. Самый крупный железный метеорит, найденный на Земле, весил около 60 тонн. Не случайно египтяне называли железо «бенипет» – «небесный металл», а греки – «сидерос», то есть «звездный». Да вот беда – метеориты трудно обнаружить.
Одно из самых древних изделий из железа найдено в Египте: это ожерелье из прокованных полосок метеоритного железа. Оно датировано IV тысячелетием до н. э. Примерно к тому же периоду относится и кинжал из метеоритного железа, найденный на юге Месопотамии (современный Ирак).
Но метеоритное железо встречается довольно редко, поэтому перед людьми встала задача научиться получать его из руд. Для восстановления железа из его окислов окисью углерода требуется температура около 700 °C. Однако железо, получаемое таким путем, представляет собой запеченную массу из металла, его карбидов, окислов и силикатов. При ковке она рассыпается.
Первые опыты с окислами железа скорее всего проводили древние гончары, стремившиеся использовать их как красящее вещество. Они применяли флюс вместе с костной смесью (СаО, Р 2O 5). При этом также получались железные крицы, удобные для ковки. При температурах 1075 °C и выше для получения крицы флюсы не требовались. Таких температур достигали, складывая руду и древесный уголь слоями в яму или каменный горн. Уголь поджигали и через эти слои продували «сырой» (неподогретый воздух). Вначале мастера осуществляли продувку при помощи своих легких, вдувая воздух через отверстия внизу горна. Позже стали применять мехи, сшитые из шкур животных.
Сгорая в потоке воздуха, уголь нагревал руду и частично восстанавливал ее до состояния железа. Оставшаяся часть окислов железа вместе с окислами других примесей плавилась и образовывала жидкий шлак. На дне горна получали крицу – комок пористого, тестообразного, пропитанного жидким шлаком металла. Многократной проковкой крицы в горячем состоянии шлак «выжимали» и получали железную поковку, представлявшую собой сварочное ковкое железо, или мягкую сталь. Содержание углерода в такой стали – 0,12–0,26 %; серы, фосфора и других примесей очень мало.
Следует отметить, что железо всегда содержит примеси. Фосфор и сера относятся к вредным примесям, так как повышают хрупкость металла. Техническим железом называют сплав железа и углерода, содержащий 99,8–99,9 % железа, 0,1–0,2 % примесей и 0,02 % углерода. Но такой материал мягкий, поэтому практически не находит применения. Уникальность железа заключается в том, что в соединении с углеродом резко повышается его прочность и твердость. Таким образом, процесс получения железа из руды одновременно повышает механические свойства железа. Все соединения железа с углеродом можно разделить на две группы: стали и чугуны. Стали содержат до 2 % углерода, чугуны – свыше 2 %. Вначале люди использовали только сталь. Чугун, который образовывался при сильном науглероживании железа, не применялся, поскольку был хрупким и не поддавался ковке.
Долгое время для производства стали использовался сыродувный процесс. Но еще в древности металлурги применяли тигльный способ выплавки железа, меди, бронзы. Добытый металл переплавлялся в небольших огнеупорных сосудах – тиглях. Таким образом металл очищался от нежелательных примесей, его структура улучшалась. Тигльная сталь применялась для изготовления холодного оружия – мечей, сабель, кинжалов, отличавшихся необычайной остротой и упругостью. Именно из тигльной стали делали знаменитые дамасские клинки.
На процесс изготовления железа влияет режим термообработки. Уже первые кузнецы заметили, что если нагретый докрасна слиток металла опустить в холодную воду или иную охлажденную жидкость, его твердость резко возрастет. Этот процесс назвали закалкой. В некоторых старых металлургических трудах упоминается «закалка скотинным рогом с солью». По сути, это азотирование – насыщение поверхностного слоя азотом.
Потребность в стали постоянно росла. Увеличивались размеры горнов, совершенствовалась их форма, повышалась мощность дутья. Высота печей достигала нескольких метров, воздуходувные трубы приводились в движение специальными водяными трубами и огромными водяными колесами. Температура в печах повысилась до 1250–1350 °C, что привело к увеличению количества чугуна, получаемого при плавке. В то время свойства чугуна не позволяли применять его для промышленных нужд. Но в XIII–XIV веках был открыт «кричный передел». Его суть заключалась в том, что чугун загружали в печь вместе с рудой. В результате происходило окисление примесей, в первую очередь углерода. Переплав чугуна позволял получать сталь хорошего качества и в больших количествах. Двухстадийный способ получения стали из руды сохранился и по сей день, являясь основой современных схем производства стали (за исключением бездоменной металлургии).
Технический переворот в металлургии произошел в конце XVIII – начале XIX века с изобретением паровой машины. И как следствие – рост промышленного производства и увеличение числа машин. Это вызвало повышенную потребность в металле и послужило толчком к развитию металлургии. Развитию же препятствовало отсутствие заменителя древесного угля. Он был дорог, запасы древесины для его производства – ограничены. Еще в 1558 г. английская королева Елизавета запретила производить уголь из древесины. Поэтому в качестве топлива стали использовать каменный уголь. Первые попытки использования угля были неудачными: проблемой стала высокая температура его воспламенения. Кроме того, чугун, выплавленный на каменном угле, содержал много серы и фосфора, поэтому для передела в сталь не годился. В 1619 г. англичанин Додлей получил патент на производство чугунного литья или брусков путем применения каменного угля в печах с раздувательными мехами. Но внедрить в практику это изобретение ему не удалось, и свой секрет он унес в могилу.
В 1713 г. Абрахам Дерби-старший нашел способ очистки каменного угля от примесей путем его обжига. Такой способ назвали коксованием. Но Дерби-старший применял кокс в доменной плавке лишь частично (из-за отсутствия техники для мощного воздушного дутья). В 1735 г. его сын Абрахам использовал для доменного дутья паровую машину. Качество выплавленного чугуна было высоким, а производительность из-за значительного увеличения температуры резко возросла. Дерби-сын заменил деревянные рельсы, по которым подавали вагонетки с рудой, на чугунные. Так появилась первая железная дорога. В 1779 г. Абрахам Дерби-внук построил первый в мире мост из литых чугунных деталей.
Применение каменного угля сдерживалось высоким содержанием серы в нем. Это придавало чугуну повышенную хрупкость. Проблему помогли решить пудлинговые печи. В них металл не соприкасался с коксом, а нагревался теплом, отраженным от свода. Для более равномерного выгорания углерода металл постоянно перемешивали, что и дало название процессу («puddle» по-английски – перемешивать).
Следующим шагом в развитии доменного процесса стал нагрев воздуха, подаваемого в печь. Эта идея, предложенная шотландцем Нильсоном, первоначально была встречена в штыки. Тогда полагали, что чем холоднее воздух, тем лучше идет плавка. Внедрение этого изобретения позволило сократить расход кокса на треть, а выплавку чугуна увеличить в полтора раза. Идею Нильсона развил английский инженер Каупер. В 1857 г. он предложил оригинальную конструкцию доменного воздухонагревателя (каупера), позволявшего нагревать воздух до 600–700 °C. Современные кауперы позволяют нагреть воздух перед подачей в печь до 1200 °C.
К середине XIX века существовавшие тогда пудлинговый процесс и кричный передел не удовлетворяли требования металлургов из-за продолжительности, трудоемкости и низкого качества металла, а тигльный способ, позволявший получать хорошую сталь, был дорогим и применялся мало.
В то время даже лучшие мастера руководствовались в своей работе исключительно опытом предшественников и своим собственным. О процессах, происходящих в металле при плавке и обработке, они практически ничего не знали, поэтому сознательно управлять ими не могли. Это не позволяло совершенствовать железоделательное производство.
Великий русский ученый-металлург Павел Петрович Аносов задался целью превратить металлургию железа из ремесла в науку. После окончания в 1817 г. Горного корпуса в Петербурге он получил назначение на заводы Златоустовского горного округа на Урале. Экспериментируя с различными процессами получения стали, Аносов сумел получить сталь высокого качества, сократив продолжительность выплавки в несколько раз. Ему удалось получать сталь непосредственно из чугуна. Заветной мечтой русского металлурга была разгадка тайны булата. На пути к ее раскрытию Павел Петрович провел тысячи опытов с различными добавками: кремнием, марганцем, алюминием, титаном, даже с золотом и платиной. В конце концов молодой инженер пришел к выводу, что булат – это только железо и углерод. А опыты с добавками других металлов в железо положили начало металлургии легированных сталей.
Для исследования структуры металла Аносов впервые в мировой практике применил микроскоп, заложив основы металлографического анализа. В 1833 г. был выкован первый булатный клинок, перерубавший и гвозди, и тончайший газовый платок. Итог своим многолетним трудам Аносов подвел в своей монографии «О булатах».
Переворот в производстве литой стали призошел во второй половине XIX века. В 1856 г. Генри Бессемер взял патент на изобретение – конвертер, в котором осуществлялась продувка воздухом расплавленного чугуна, что позволяло превращать чугун в сталь без дополнительного нагрева.
В 1864 г. француз Пьер Мартен разработал новый способ выплавки стали, названный затем в его честь. Несмотря на то, что мартеновский процесс был более продолжительным, чем бессемеровский, он обеспечивал более высокое качество стали. Причем сырьем для него могли служить металлолом и отходы конвертерного производства. Плавка в мартене легко контролировалась, и ею можно было управлять. К началу XX в. мартеновский способ по объемам производства превзошел бессемеровский.
Большой вклад в исследование процессов, происходящих в стали, внес русский ученый Д. К. Чернов. Он исследовал нагрев и охлаждение стали, пытаясь найти оптимальный режим термообработки для различных ее сортов. Опыты Чернова помогли разработать способ получения требуемой структуры стали и положили начало новой науке – металловедению.
В начале XIX в. русский ученый Петров выдвинул идею выплавки железа в электропечи. В 1853 г. во Франции был получен первый патент на электропечь. В 1879 г. Вильгельм Сименс построил первую электропечь. Но получаемый в ней металл содержал большое количество примесей. В 1891 г. Н. Г. Славянов осуществил первую плавку стали в тигльной печи, снабженной электродами. В 1892 г. Анри Муассан создал лабораторную электропечь, температура в которой достигала 4000 °C. Благодаря производству дешевой электроэнергии на гидроэлектростанциях были построены электропечи в Швейцарии, Швеции, Германии, США. Высокая температура (до 5000 °C), а также восстановительная атмосфера позволяли получить полностью очищенную от примесей сталь. Именно появление электропечей дало возможность производить сталь с добавками других элементов – хрома, ванадия, вольфрама, титана и др. – легированную сталь.
В XX веке идет работа над заменой доменного процесса. Это связано с удорожанием производства кокса и повышением требований к охране окружающей среды. Еще Д. К. Чернов предложил конструкцию печи, выплавлявшей не чугун, а железо и сталь. В 60-е годы XX века появились комбинаты, сырьем для которых служат окатыши – небольшие «орешки» из железорудного концентрата. В установках прямого восстановления, работающих на природном газе, из окатышей извлекают кислород. На второй стадии в мощных дуговых печах выплавляется высококачественная электросталь, очищенная от примесей. Эта технология позволяет обходиться без кокса, не загрязнять окружающую среду отходами производства.
Передовой технологией является и непрерывная разливка стали. На смену сложной многоступенчатой схеме получения стальных слитков и превращения их в прокатную заготовку пришла единственная операция. Она позволяет превратить расплавленный металл в полуфабрикат для проката. Непрерывная разливка стали намного упростила технологию, что позволило снизить производственные затраты. При этом сократились потери металла, повысилось качество стали. Кроме того, улучшились условия труда и повысилась возможность автоматизации процесса разливки.
В киевском Институте электросварки им. Патона в 1952 г. был разработан способ электрошлакового переплава металлов. Он позволяет получить слитки больших размеров и сложной конфигурации.
Еще одним эффективным методом получения металлических изделий является порошковая металлургия. Она позволяет получать изделия путем прессования и спекания металлических порошков.
Постоянное развитие технологий производства сплавов на основе железа позволяет получать материалы, соответствующие современным требованиям промышленности. Поэтому можно с уверенностью сказать, что железный век человечества продолжается.
Интегральная микросхема
Около полувека в радиотехнике царили электронные лампы. Они были хрупкими, большими, ненадежными, потребляли много энергии и выделяли массу тепла. Появившиеся в 1948 г. транзисторы были надежнее, долговечнее, потребляли меньше энергии, выделяли меньше тепла. Они дали возможность разрабатывать и создавать сложные электронные схемы из тысяч составляющих: транзисторов, диодов, конденсаторов, резисторов. Но это усложнение породило проблему, заключавшуюся в дороговизне ручной пайки многочисленных соединений. Это занимало много времени и снижало общую надежность устройств. Требовался более надежный и рентабельный способ соединения электронных компонентов схем.
Кроме того, работу большинства полупроводниковых приборов обеспечивает тонкий поверхностный слой толщиной в несколько микрометров. Остальная часть кристалла играет роль основания (подложки), необходимого для прочности транзистора или диода.
При изготовлении транзисторов в них размещали три тонких слоя с р– и n-проводимостью, создав в нужных местах пленочные металлизированные контакты для соединения с внешними элементами схемы и диэлектрические пленки, изолирующие каждый контакт. Технология нанесения полупроводниковых металлизированных и диэлектрических пленок послужила основой создания пленочных интегральных микросхем.
Одним из решений проблемы уменьшения количества соединений в электронных схемах стало создание микромодульной технологии. Она поддерживалась Министерством обороны США. Идея состояла в том, что все компоненты должны иметь одинаковые размеры и форму и содержать выводные контакты для межэлементных соединений. При создании схем модули объединялись в сложные объемные структуры с меньшим количеством проводных соединений.
Среди компаний, занимавшихся созданием микромодульных схем, была «Texas Instruments». Один из ее сотрудников, Дж. Килби, считал, что микромодуль не сможет решить проблему уменьшения числа соединений в сложных схемах. Он начал искать другое решение и пришел к выводу, что основу схемы должен составлять полупроводниковый материал. Пассивные элементы схемы (резисторы и конденсаторы) могли быть сделаны из того же материала, что и активные (транзисторы). Если все компоненты сделаны из одного материала, их можно соединить между собой, формируя законченную схему.
В июле 1958 г. Килби начал работать над созданием микросхемы, а 12 сентября того же года он продемонстрировал руководству компании рабочую интегральную схему, сформированную в кусочке германия, наклеенного на стеклянную пластинку.
Промышленники скептически восприняли появление микросхемы. Только военное ведомство США, и в частности воздушные силы, проявили определенный интерес к новому изобретению.
В феврале 1960 г. фирма «Fairchild» выпустила семейство монолитных транзисторных логических элементов с несколькими биполярными транзисторами на одном кристалле кремния. Оно получило название «микрологика». Фундамент развития интегральных микросхем был заложен планарной технологией Хорни и монолитной технологией Нойса в 1960 году. Сначала микросхемы основывались на биполярных транзисторах, а затем на полевых транзисторах и комбинациях обоих видов.
Интегральная схема сначала отвоевала место на рынке военных изделий, благодаря программе создания первого компьютера на полупроводниковых кристаллах для Министерства Воздушных сил в 1961 году и производству ракет «Минитмен» в 1962-м.
Интегральные схемы, содержавшие до 100 элементов, называются микросхемами с малой степенью интеграции, до 1000 – микросхемами со средней степенью интеграции, до 10 000 – большими интегральными схемами.
В 1967 г. был выпущен первый электронный карманный калькулятор. Его размеры были следующими: 108×156×27 мм. Он был создан на основе большой интегральной микросхемы БИС, выполнявшей основные математические действия (сложение, вычитание, умножение и деление). Ее создателями были Дж. Килби, Дж. Мерриман и Джеймс Ван Тассел.
Рассмотрим процесс изготовления интегральной микросхемы, основой которой служит пластина чистого кремния, обладающая р-проводимостью. Ее тщательно обрабатывают: шлифуют, полируют. После этого проводится окисление пластины в атмосфере сухого кислорода. В результате на ее поверхности возникает слой двуокиси кремния SiO 2. Он обладает большой прочностью и высокой химической стойкостью.
Затем проводится фотолитография: на пластину наносится светочувствительный слой (фоторезист). На следующем этапе на фоторезист накладывается фотошаблон. На нем фотографическим способом изготовлен рисунок всех элементов, которые необходимо закрепить на подложке. Фоторезист облучается ультрафиолетовым светом, проявляется, полимеризуется и сохраняется в тех местах, где фотошаблон имеет прозрачные окна. Там, где ультрафиолетовый свет не проник через шаблон, фоторезист удаляется химической обработкой. Оставшийся фоторезист служит контактной маской, защищающей те области пленки металла, которые должны быть сохранены от химического воздействия.
Поверхность схемы подвергается химическому травлению, удаляющему пленку металла с поверхности, кроме мест, защищенных фоторезистом.
Применяемый в описанной схеме фоторезист называется негативным. Применяется также позитивный фоторезист, который не закрепляется, а разрушается ультрафиолетовым светом. При его использовании окна на фотошаблоне соответствуют пустым промежуткам на будущей микросхеме.
На участки поверхности подложки, свободные от фоторезиста, вносятся примеси путем легирования – диффузии необходимых примесей внутрь подложки. Такими примесями могут быть сурьма или мышьяк, которые обладают n-проводимостью. Другим способом получения участков с n-проводимостью является планарная технология. Она заключается в том, что перед легированием проводится эпитаксия – постепенное наращивание слоя, по структуре повторяющего кристаллическую структуру подложки, но имеющего отличные от нее физические свойства. Так, методом эпитаксии на подложку с p-проводимостью наносится слой с n-проводимостью. Используя соответствующие маски, в нужные области эпитаксиального слоя вводятся примеси, обеспечивающие p-проводимость.
Все зоны и их контакты создаются в одной плоскости, отсюда и термин «планарная технология».
Для нанесения пленок, легирования подложек применяются вакуумные камеры, в которых могут располагаться электронные пушки, магнетроны, источники рентгеновских или ионных лучей.
После эпитаксии или легирования поверхность вновь покрывают слоем оксида, проводят фотолитографию, травление, открытие новых «окон» кремния, после чего проходит легирование бором, обладающим p-проводимостью. Так создаются базовые области транзисторов, p-n переходы и области резисторов.
При следующей диффузии – диффузии фосфора – формируются эмиттерные области транзисторов. Затем вскрываются «окна» под контакты с областями коллектора, эмиттера и базы транзисторов, p– и n-областями диодов и с резисторами.
Затем создаются внутрисхемные соединения путем напыления пленки алюминия, которая после этого селективно травится путем фотолитографии. Сохраненные участки алюминия образуют электроды элементов, соединительные дорожки и контактные площадки для подсоединения структуры интегральной схемы к выводам корпуса.
Всю поверхность полупроводникового кристалла покрывают защитным слоем, который после этого удаляют с контактных площадок.
Готовые микросхемы подвергают тщательному контролю для выявления дефектных изделий.
Применение микросхем позволило значительно уменьшить размеры радиотехнических приборов, электронно-вычислительных машин, увеличить их быстродействие.