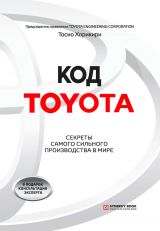
Текст книги "Код Toyota. Секреты самого сильного производства в мире"
Автор книги: Тосио Хорикири
Жанр:
Деловая литература
сообщить о нарушении
Текущая страница: 1 (всего у книги 2 страниц)
Тосио Хорикири
Код Toyota. Секреты самого сильного производства в мире
© Перевод на русский язык. АНО «Центр «Кайдзэн», 2016.
© Издание на русском языке. Университет «Синергия», 2018.
Предисловие
Собранный в 1978 году исполнительным вице-президентом компании Toyota Motor Т. Оно опыт в виде книги «Производственная система Toyota» (Toyota Production System, TPS) получил распространение в 1980-х годах в США под названием Lean Production (бережливое производство). Затем система стала известна в Европе, а после и в России.
Со времени знакомства Запада с TPS прошло 30 лет. За это время она была значительно усовершенствована и, пройдя многие этапы, преобразовалась в финальную версию – Всеобщую производственную систему Toyota (Total Toyota Production System, T-TPS).
Согласно T-TPS, кайдзен-работа в компании стартует на начальной стадии производства – с этапа разработки и проектирования новой продукции. Для этого необходимо проводить активизацию всего персонала и всех рабочих мест (АПРМ). С другой стороны, благодаря кайдзен-работе и происходит данная активизация.
Если компания слаба в экономическом и производственном плане, то ей не выиграть в конкурентной борьбе. Компания – это организация людей, которых необходимо активизировать с целью повышения экономичности и производительности. Однако если руководство будет просто насаждать свой курс по принципу сверху вниз, то никто не поймет его устремлений и не будет действовать сообразно им. Очень важно добиться того, чтобы каждый человек в компании действовал – выполнял работу, имеющую конкретную ценность.
Кайдзен по принципам T-TPS позволяет этого достичь.
Сегодня российские компании отстают в сфере управления, но пытаются сократить дистанцию с лучшими мировыми практиками. Для этого им необходимо активно внедрять T-TPS, особенно главный ее принцип – АПРМ.
Надеюсь, что важные моменты совершенствования производства, отраженные в этой книге, будут применены вами на практике.
Хорикири Тосио, председатель правления Toyota Engineering Corporation
Глава 1
О Всеобщей производственной системе Toyota (Total Toyota Production System, T-TPS)
1.1. Проблемы прежней модели TPS (Toyota Production System, производственная система Toyota)
1.1.1. Проблемы, с которыми сталкиваются руководители и собственники компаний при внедрении TPSTPS (производственная система Toyota) – известная и распространенная система, о которой издано большое количество книг. Многие, прочитав их, полагают, что получили полную информацию, пытаются применить систему в своей компании, но зачастую сталкиваются с проблемами внедрения. Другие, полагая, что поняли суть системы, не получают ожидаемых результатов от внедрения. Даже те, кто для внедрения системы TPS обращаются в консалтинговые фирмы и нанимают экспертов, тоже не получают желаемые результаты.
Консультанты по TPS, как правило, выбирают пилотный участок, руководят выявлением проблем и работой по улучшению производственных процессов, достигают определенных результатов, но кайдзен-деятельность не распространяется на всю компанию. Удается достигнуть лишь некоторых локальных улучшений на ряде участков, а с уходом консультантов процесс совершенствования останавливается, и со временем от него не остается и следа. В большинстве компаний проблемы возвращаются, так как совершенствование процессов не продолжается либо ведется неэффективно.
Почему же принципы TPS трудно реализовать на практике? Ведь в книгах собрано так много полезной информации и описана идеальная модель…
Занимаясь процессом совершенствования в различных компаниях, методом проб и ошибок, обдумывая принципы и разрабатывая способы кайдзен-работы, автор задавался следующими вопросами:
– что позволило добиться успешного внедрения?
– что повлияло на неудачный ход внедрения?
– нет ли более понятного для всех способа развертывания принципов TPS?
– что надо сделать, чтобы все активно участвовали в кайдзен-работе?
Ответы на данные вопросы будут даны ниже, а сейчас рассмотрим примеры попыток внедрения TPS.
1.1.2. Типичные ситуацииЗдесь я хотел бы представить несколько примеров внедрения прежней модели TPS. Рассмотрев их, давайте подумаем, как меняются производственные подразделения, какие проблемы возникают в процессе внедрения. Обнаружив и осознав проблемы, появится способ их решить, найдется кайдзен-решение.
1.1.3. Основные проблемы TPS до появления T-TPS (Total-TPS)Пример 1: Предприятия, изучающие TPS по книгам
Ко мне обратился за советом директор предприятия, выпускающего производственное оборудование. Он прочитал 20 книг по TPS и задался следующими вопросами: «Я думал, что понял, как работает система. Но когда попытался ее реализовать, не имел никакого представления, с чего начать. В каком состоянии находится наша компания? Какова цель внедрения TPS? Я вновь перечитал книги и еще раз попробовал применить полученные знания, но ничего не вышло. Реализовать TPS – сложная задача». Пришлось ответить ему так: «Это естественно. Только прочитав книги, непонятно, что делать. Но когда специалист Toyota увидит вашу компанию, то сразу определит ее состояние».
На тот момент я мог дать только такой ответ. Но спустя время многое было переосмыслено, и я пришел к выводу, что компаниям (за исключением Toyota) нужен более понятный и легкий способ внедрения TPS. Обычным компаниям трудно понять, как функционирует TPS в ежедневном режиме, так как очень многие важные моменты недостаточно объяснены в специализированной литературе. Кроме того, даже специалисты по TPS, имеющие практический опыт работы в Toyota, при внедрении TPS в других компаниях используют разные способы и подходы в консультативной деятельности. Подходы к консультированию не определены, а значит, нет единой технологии внедрения.
Пример 2: Компания, имеющая небольшой практический опыт внедрения TPS
Специалист по кайдзен (такие специалисты могут работать в данной компании или быть экспертами консалтинговой компании) начал процесс совершенствования в следующей последовательности:
1) определение пилотного участка;
2) начало кайдзен-работы;
3) начало реализации работы по сокращению трудозатрат на выбранном участке;
4) наблюдение за движениями операторов на участке;
5) координация работы по сокращению потерь.
В процессе кайдзен-работы всегда возникает сопротивление рабочих и руководителей, которое носит как явный, так и скрытый характер. Когда специалисты сталкиваются с таким сопротивлением, они пытаются заставить сотрудников выполнять кайдзен-работу, иногда используя для этого административное давление со стороны их непосредственных руководителей. В процессе такого «принудительного» совершенствования возникают три типа сценария поведения сотрудников:
1) бойкот поручений;
2) частичное выполнение;
3) создание эффекта видимости выполнения.
В третьем случае, после завершения работы на пилотном участке, специалист предлагает самостоятельно внедрить полученный опыт на других участках, а сам переходит в другой цех или подразделение. Однако после его ухода в большинстве случаев деятельность по совершенствованию останавливается, подсознательно формируется отношение «наконец-то ушел этот зануда», и процесс внедрения вместо того, чтобы развиваться, сходит на нет.
Пример 3: Завод «Цуцуми» корпорации Toyota Motor
На протяжении всей своей работы в Toyota я применял на практике принципы TPS. Свой первый опыт внедрения системы я получил на заводе «Цуцуми». Тогда группа под руководством главного инспектора из Департамента исследования производства головной компании, отвечавшего за внедрение TPS, проводила кайдзен-работу на заводе. В то время я работал инженером в отделе технологии производства и участвовал в проектировании новой линии сборки автомобилей. Кайдзен-работа проводилась под руководством этого инспектора. Я участвовал в обучении по TPS, но как ее применяют на практике, не видел.
Оказалось, что инспектор и его подчиненные, пытаясь добиться желаемого, едва не крича, жестко требовали от сотрудников: «Сокращайте время переналадки прессов!», «Сокращайте расстояние между рабочими местами!» Подвергнутые такому прессингу, работники и начальник отдела буквально дрожали от страха.
Через год работы на «Цуцуми» я вернулся на завод «Мотомати», тоже в отдел технологии производства. И здесь тот же инспектор давал указания о проведении кайдзен-работы по TPS. Таким образом, мы стали заниматься данным направлением под руководством того же инспектора.
Вместе с кайдзен-группой в течение дня мы должны были проанализировать текущее состояние производственного процесса, выявить потери, составить планы по их устранению и реализовать их. Главным было устранить узкие места и потери, на которые указал инспектор.
На следующий день он проверял результат совершенствований. Если результат отсутствовал, лицо его краснело от злости, и он вскипал от ярости. Поэтому, чтобы не навлекать на себя гнев, мы отчаянно совершенствовали производственные процессы.
В то время завод работал в две смены (дневная и ночная). Совершенствование проводилось каждый день, между сменами в течение часа (20.00–21.00), когда производство останавливалось: улучшалось планирование участка, перераспределялись виды работ, сокращалась трудоемкость.
В течение дневной смены мы анализировали состояние рабочих мест и выявляли проблемы. Между сменами совершенствовали рабочие места. Но в начале ночной смены, после изменений, возникали различные проблемы. И только решив их, мы уходили с работы.
Деятельность в таком ключе продолжалась примерно год. Оглядываясь назад, мы с улыбкой вспоминаем, как усердно старались, чтобы не разозлить инспектора. Определенно, благодаря устранению потерь на рабочих местах произошли качественные перемены. Но справедливо и то, что такой результат достигался и благодаря более интенсивному труду рабочих. Часто руководители участков говорили мне: «Работа стала очень тяжелой, это предел человеческих сил», показывая при этом распухшие ноги операторов на сборочных линиях. В душе мы были согласны с ними и понимали, что так работать нельзя. Но, тем не менее, руководители участков, боясь попасть под горячую руку инспектора, не показывали своего несогласия и молча проводили намеченные им мероприятия.
По окончании программы инспектор и мы, члены кайдзен-группы, пришли с отчетом к вице-президенту головной компании Тайичи Оно (в то время курировал Департамент управления производством в рамках всей корпорации). Инспектор с гордостью доложил о проделанной работе: «Сокращено энное количество человек в цехе А, энное количество человек в цехе Б, энное количество человек в техническом отделе…». Этим и закончилось руководство инспектора по проведению кайдзен-работы на заводе «Мотомати». Правда, после этого он работал и на других заводах Toyota.
Этот опыт с большой пользой дал мне возможность познать практику TPS. Вместе с тем, я понял, что у рабочих возникало негативное отношение к людям, занимающимся кайдзен-работой, что создало натянутые отношения внутри коллектива. В результате проекта резко снизилось качество выпускаемой продукции, поэтому пришлось вернуть на производственные участки сокращенных сотрудников. При этом от результатов кайдзен-работы практически не осталось и следа, среди рабочих и линейных руководителей распространились беспомощность и апатия, были разрушены доверительные отношения между сотрудниками. Некоторые сетовали: «Для чего нужно было это совершенствование? Было ли это на самом деле улучшениями? Или это нужно только для получения заслуг инспектором, а мы просто жертвы?»
Понадобилось много времени, чтобы посредством внедрения уже T-TPS ситуация перешла в состояние «активизации персонала».
Пример 4: Компания-партнер Toyota по производству автокомпонентов
Компании-партнеры Toyota также вели деятельность по совершенствованию своих производственных процессов. Например, в одной компании внезапно появлялся сотрудник отдела исследования производства Toyota и, посмотрев на производственную линию, начинал тут же кричать: «Проблема тут! Проблема там! Совершенствуйте процессы!»
Люди, работающие на этой линии, недоумевали: «Что он хочет предпринять? Почему это считается проблемой?» Но пояснений не следовало, и им оставалось только подчиниться.
При насильно проводимом совершенствовании сотрудники не понимают, зачем оно нужно, и, естественно, эффективность такой методики низкая. К сожалению, таких случаев история внедрения TPS знает много.
Пример 5: Зарубежные заводы Toyota
Позже я перешел из Департамента технологии производства на должность ответственного за строительство, обучение персонала и руководство заводами Toyota за границей. Естественно, за рубежом другая культура.
Операторам тех заводов не только незнакомо мышление в духе Toyota – у них абсолютно отсутствуют знания по TPS! Тем не менее, я приступил к руководству с намерением сделать, к примеру, заводы в Индонезии или Таиланде такими же, как заводы в Японии, по уровню качества и производительности. Для этого туда были направлены несколько специалистов по TPS, которые руководили процессами совершенствования. Соответственно, после этого на отдельных рабочих участках на какое-то время ситуация улучшалась. Но после того как мы, закончив деятельность, уезжали домой, все опять возвращалось на круги своя. И так повторялось каждый раз.
Опыт показал, что во внедрении и применении TPS был ряд проблем:
– внедрение TPS не давало желаемых результатов;
– отсутствовала адаптированная методика для сотрудников компаний, не входящих в группу Toyota;
– трудность понимания TPS не позволяла закреплять результаты;
– низкая мотивация персонала, отрицательно относящегося к кайдзенработе.
Почему возникали данные проблемы? Почему ни в книгах Тайити Оно, ни в других книгах по TPS о них не написано?
Потому что сами руководители развертывания TPS не очень хорошо их понимают.
Иногда такие проблемы решаются – обычно с помощью личного опыта руководителей. Но поскольку у каждого из них свои знания и опыт, то и способы организации кайдзен-работы различны, и это тоже является проблемой.
Занимаясь совершенствованием по TPS в различных компаниях, мы внедряли TPS, также основываясь на собственных знаниях и опыте.
1.2. Уроки, извлеченные из примеров
1.2.1. Причины отсутствия энтузиазма на рабочих местахПри внедрении прежней модели возникала проблема отсутствия мотивации у персонала. В чем же причина? В процессе кайден-работы очень важна реакция сотрудников. Для этого нужно тщательно анализировать их реакцию.
На схеме 1-2-1 изображена организационная структура производственной компании. Данная структура является типичной для большинства предприятий. На заводе существуют различные подразделения (цеха), участки (отделы), бригады (секторы), общезаводские службы и т. д.
Совершенствование по TPS проводится в следующем порядке.
1. Для быстрого получения результата от внедрения определяют пилотный участок и назначают руководителя по совершенствованию (эксперт по кайдзен-работе).
2. Руководитель проекта (топ-менеджер) или эксперт по кайдзен-работе (специалист по TPS) ходит по подразделениям и определяет проблемные места, дает сотрудникам указания по их устранению. Обычно таким способом совершенствуются производственные процессы и логистика. Данный способ оказывает определенное влияние на подсознание сотрудников, но этого недостаточно для полного убеждения. В большинстве случаев, когда приходит руководитель по TPS, людям не остается ничего, кроме как подчиниться: «Сказали, значит, надо сделать». Некоторые сопротивляются или игнорируют – и это нормально. Есть те, кто догадываются о том, что должен прийти руководитель, и ловко ускользают в тот момент.
Если применять такой способ внедрения, то результат (уменьшение запасов, уменьшение численности персонала) достигается только на пилотном участке и на определенный момент времени, когда работает эксперт. После его ухода все возвращается к прежнему состоянию.

Схема 1-2-1. Организационная структура компании (завода)
По окончании пилотного проекта руководитель группы по развертыванию TPS обязательно говорит: «Необходимо распространять совершенствования, проведенные нами на пилотном участке, на другие участки, и тогда ситуация на заводе (в компании) улучшится».
Но после нескольких месяцев работы без эксперта совершенствования не распространяются дальше пилотного участка, а со временем и совсем затухают.
Вопрос: что с этим делать?
Когда Toyota строит завод за границей, мы поступаем следующим образом: с одного из заводов Toyota внутри Японии (система родительского завода, кода один японский завод курирует несколько зарубежных заводов Toyota) приезжают специалисты и внедряют TPS, корпоративную культуру и другие методики Toyota по принципу «количество переходит в качество». Бывает, что на один зарубежный завод отправляется несколько сотен руководителей (лидеров групп, мастеров, начальников участков и смен). Именно по этой системе Toyota создавала и развивала свои заводы и филиалы за границей. Конечно, хотелось бы управлять ими с помощью только нескольких экспертов, проживающих за рубежом, но, как было уже сказано, после небольшого периода нововведений все возвращается на прежний уровень. Поэтому Toyota и сегодня пользуется методом «количество-качество».
При запуске нового крупномасштабного завода за рубежом с численностью 1 тыс. чел. для обучения дается один эксперт на одного или пару сотрудников. Сегодня такие принципы применяются на всех заводах Toyota, запускающихся за границей.
Тем не менее, если таким образом внедрять TPS на предприятиях, не относящихся к Toyota, то потребуется огромное число экспертов, что очень затратно. Необходим более эффективный метод внедрения TPS, особенно, если мы хотим внедрить TPS на заводе, где работает тысяча человек. Я долгое время искал метод эффективного внедрения TPS в таких случаях.
Хочу отметить, что начало кайдзен-работы на пилотном участке, о чем мы говорили выше, является не самым плохим вариантом. Сотрудники более или менее помогали руководителям и выражали понимание. Обычно люди либо сопротивляются, либо игнорируют советы эксперта, либо просто поверхностно исполняют поручения. А поскольку в душе они не согласны, то дальше ничего и не развивают. Несмотря на то, что любое производство содержит большое количество важных проблем и задач, сотрудники выполняют только порученное и, как правило, никаким совершенствованием не занимаются. Впрочем, это можно считать нормальным, ведь даже если указания экспертов кайдзен сотрудники считают правильными, то в душе они с ними не согласны. А без искреннего согласия не появится желание улучшать! Поэтому эксперты и руководители вынуждены повышать голос, из-за чего возникает неприятная атмосфера, и желание совершенствовать(ся) становится еще меньше.
Итак, если работники определенного участка теряют интерес к совершенствованию, то виноваты в этом, прежде всего, линейные руководители и эксперты по кайдзен.
Несмотря на то, что персоналу правильно указывается на требующиеся улучшения, реакция сотрудников обязательно проходит следующие этапы:
1) понимание указанных экспертом проблем;
2) осознание логичности указаний;
3) внутреннее согласие провести совершенствования;
4) реализация совершенствований.
Такая последовательность является нормальной человеческой реакцией. Между моментом осознания проблемы и моментом ее решения должно пройти определенное время.
Первые два этапа осознания происходят на уровне разума – это логическое понимание.
Состояние согласия внедрять совершенствование (третий этап) – это убеждение, идущее из души, от эмоций (подсознательный уровень). Именно на этом этапе человек приступает к действиям. То есть человек начинает действовать только тогда, когда сформируется желание. Если желание что-либо делать отсутствует, то добиться эффективного результата невозможно даже приказами свыше. Это как с детьми, когда родители велят им что-либо сделать, а они не хотят. С другой стороны, когда они хотят попробовать сами, они с радостью делают.
Таким образом, очень важно сформировать у сотрудников желание совершенствования. Для того чтобы поднять уровень осознания проблемы до уровня желания ее ликвидировать, необходимо больше задумываться об уважении личности (о человеческой душе). В этом отношении в прежней модели TPS имеется ряд недостатков: отсутствие понимания важности уважения личности для повышения мотивации и заинтересованности сотрудников и нацеленности на решение вопросов, значимых для самого сотрудника и рабочего участка.
Также в TPS усиленно обращали внимание на деньги, готовые изделия, детали и оборудование. Персонал воспринимался как ресурс, за счет которого возможно сокращение расходов. Но на самом деле в TPS человеческая душа важнее всего. Следовательно, есть необходимость использовать ее по максимуму. Но как использовать, спросите вы, ведь она неосязаема! Тем не менее, Toyota разрабатывала различные пути решения этой задачи: почувствовав предел методов прежней модели TPS, компания сменила свои принципы 30-летней давности. Теперь используется так называемая система самостоятельных исследований (дзисюкэн). Мы переключились с прошлой принудительной модели TPS на новую – T-TPS, где один из главных принципов – «думаешь и совершенствуешься сам». Для того чтобы человек внутренне согласился и самостоятельно начал стремиться к совершенствованию, необходимо, чтобы он понимал суть изменений и сам их осуществлял. Об этом принципе поясним подробнее в разделе «История становления T-TPS».
Для того чтобы сотрудники приняли изменения и развивали их дальше, необходимо, чтобы они внутренне, душой ощутили желание заниматься кайдзен (состояние высокой степени желания). Система, повышающая степень желания персонала, называется «активизация персонала и рабочих мест» (АПРМ). Отметим, что это одно из ключевых понятий в кайдзен-работе. С помощью данной системы поднимается уровень осознания сотрудниками необходимости совершенствований и активизируется деятельность, например, по улучшению качества и сокращению себестоимости.
Именно кайдзен-деятельность стремительно повысила уровень TPS. Поэтому Total-TPS, используемая в настоящее время, сильно отличается от TPS, применявшейся 30 лет назад.
Интересно, что сама Toyota из своего опыта понимает ценность АПРМ, но не может четко и системно выразить ее, так как не проводила конкретные исследования по данной тематике. А такие исследования необходимы и с точки зрения нейропсихологии. Но об этом более подробно – в главе 4.