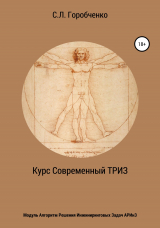
Текст книги "Курс «Современный ТРИЗ». Модуль «Алгоритм решения инжиниринговых задач АРИнЗ»"
Автор книги: Станислав Горобченко
сообщить о нарушении
Текущая страница: 4 (всего у книги 7 страниц)
Множество разработок комплексных и сложных технико-коммерческих предложений начинается с получения обычного запроса на предложение. Иногда даже не прилагается опросных листов. Как правило, специалисты равняются на известные им решения и вообще-то проверяют этим, а знаешь ли ты таковые решения. Конечно, есть и другой вариант «послушать, как у них там за бугром делается».
Часто советником является проектный институт, однако, он не является знатоком многих участков использования арматуры, и мы можем сказать, что проектные институты в свою очередь равняются на решения, разработанные еще в советские времена уже не существующими НИИ. За последнее время опыт применения арматуры уже во многом переместился в инжиниринговые и арматурные компании. С учетом растущей конкуренции инженерных решений, предлагаемых разными фирмами, и накопления опыта их внедрения, старые разработки институтов не могут быть и вовсе применены.
Тем не менее, на этом первом этапе уже ставится задача «как есть», и с этого момента начинается работа по проведению инженерно-экономического анализа с целью разработки наиболее конкурентного предложения (подробнее см. Горобченко С. Л. Практический маркетинг. Применение комплексного инженерно-экономического анализа для маркетинговых целей ТПА – экспресс, 12013). Ниже мы приводим пример разработки сложного коммерческого предложения, проведенного специалистами компании Метсо для одного из предприятий содовой промышленности.
После опроса специалистов немного кристаллизовались первые задачи.
ИСХОДНЫЕ ДАННЫЕ
Проект, включает в себя следующие задачи:
1. реконструкция цеха абсорбции и дистилляции по регулирующей арматуре
2. приведение в соответствие с требованиями Ростехнадзора по безопасности
3. замена запорной арматуры.
4. установка интеллектуальных позиционеров
Двигателем прогресса стали требования Ростехнадзора – не часто встретишь…
В рамках действующей реконструкции ставятся следующие задачи:
1. выполнение предписаний Ростехнадзора по повышению уровня безопасности.
2. установка современной системы АСУТП.
3. установка приборов КИП и А в рамках действующих проектов реконструкции.
4. снижение выбросов в т.ч. и по арматуре.
Важно, что в комплексе с КИП и А и вместе с системой АСУТП. Из этого следует, что требования к качеству регулирования и исполнительным механизмам будут на уровне.
Требования к запрашиваемой арматуре:
1. подготовка исполнения арматуры в соответствии с опросными листами (для бюджетного предложения).
2. применение современной арматуры
3. работоспособность в современных системах автоматизации управления и контроля техпроцессов.
4. смарт клапаны с интеллектуальными контроллерами, работающими на сигнале 4–20mA на основе HART-протокола.
5. V класс герметичности для 80% отсечных клапанов.
6. фланцевое исполнение.
Ключевое для нас слово смарт клапаны с интеллектуальными контроллерами прозвучало. Хотя и жаль, что «на основе HART протокола»…
Дополнительные положения, принятые во внимание.
1. Высокая экспортоориентированность (80% продукции идет на экспорт).
2. Сложность, непрерывность и взаимозависимость производств между собой.
3. Необходимость снижения потерь сырья и химикатов за счет повышения точности регулирования.
4. Необходимость уменьшения объема обслуживания арматуры и КИП.
5. Перспективность освоения современной смарт арматуры для дальнейших новых проектов.
Экспортоориентированность – первый признак того, что предприятие – серьезное. За рубежом не любят брака. Следовательно, и требования к качеству регулирования будут, по всей видимости, немаленькие…
На первом этапе нами была проведена большая информационно-аналитическая работа по поиску основных тенденций и типовых решений и цифр, отражающих современное состояние производств содовой промышленности. Для этих целей были привлечены консультанты КЦ Промконсалт ВШТЭ СПбГУПТД Санкт-Петербург. Выдержка из отчета приведена ниже.
Особенности содового производства
Производство кальцинированной соды по аммиачному способу включает в себя восемь основных переделов (отделений):
1. Получение карбонатного сырья на ГОКах.
2. Переработка карбонатного сырья: обжиг, охлаждение и очистка диоксида углерода, гашение извести с получением известковой суспензии.
3. Очистка рассола: взаимодействие сырого рассола с реагентами в реакторах и отстой рассола.
4. Абсорбция: отмывка в промывателях газов, выделяющихся на других стадиях от аммиака, двухстадийное насыщение раствора хлорида натрия (рассола) аммиаком и частично диоксидом углерода, поступающим со стадии дистилляции, охлаждение аммонизированного рассола.
5. Карбонизация: отмывка от аммиака газа, покидающего стадию карбонизации (сопровождается улавливанием небольших количеств диоксида углерода), предварительная карбонизация; карбонизация с выделением гидрокарбоната натрия в осадительных колоннах, компримирование перед подачей в карбонизационные колонны, диоксида углерода, поступающего со стадий переработки карбонатного сырья и кальцинации.
6. Фильтрация отделение гидрокарбоната натрия на фильтрах и отсос воздуха вакуум насосами.
7. Кальцинация: обезвоживание и разложение гидрокарбоната натрия в содовых печах, охлаждение и очистка диоксида углерода после содовых печей.
8. Регенерация аммиака (дистилляция) предварительный подогрев и диссоциация содержащихся в фильтровой жидкости карбонатов и гидрокарбонатов аммония в конденсаторе и теплообменнике дистилляции, смешение и взаимодействие нагретой жидкости с известковой суспензией в смесителе и отгонка аммиака.

Рис. 1. Технологическая схема производства кальцинированной соды
Что ж, специализация по химии в полном объеме. Нас ждет масса регулирующих и отсечных клапанов, способных работать в полупериодическом режиме и кристаллизующихся средах…
Технико-экономические показатели процесса получения соды.
Экономические показатели производства кальцинированной соды характеризуются следующими данными (данные по литературным источникам):
1. На 1 т продукта расходуется:

Начнем считать. В первую очередь по массовым технологическим потокам. Выделим, что в своем большинстве среда – рассольная и с наличием извести, а также наверняка и с абразивными шламами.
2. Энергетические затраты.

Как следует из описания – самый дорогой процесс – кальцинация. Здесь и будут лежать источники окупаемости клапанов и энергосбережения.
3. Фондоемкость производства соды

Надежда на энергетику не оправдается. Затраты не велики. Основная эффективность будет лежать в собственно регулировании параметров технологического процесса.
4. Сумма капитальных затрат по объектам основного производственного назначения распределяется следующим образом:

Основные капитальные затраты также лежат в собственно технологических линиях, а не вспомогательных, добычных или транспортных процессах. На таких предприятиях Технологи «правят бал».
5. Структура себестоимости соды кальцинированной характеризуется следующими данными, %:

Примерно также распределится и эффективность от работы арматурного хозяйства в целом. С учетом того, что «технология превыше всего», то задачей для арматуры будет не снижение расходов на содержание и ТО, а на снижение потерь в технологии (графа «сырье и материалы»).
6. Общая сумма затрат на 1 т соды распределяется по стадиям производства следующим образом, %:

Основные процессы – адсорбция, карбонизация, дистилляция и кальцинация занимают все эксплуатационные затраты на производство. И еще раз мы правы в том, что основное внимание при подготовке предложения нужно будет направлять на технологические эффекты и сверхэффекты.
7. Использование тепла в основных отделениях производства соды составляет в долях от общего теплопотребления, %

Если отдельно заняться клапанами для обеспечения подачи технологического пара и газа, то нас ждут обжиговые печи, кальцинация и регенерация аммиака и диоксида углерода. Остальные не интересны. Хотя в последнее время и охлаждающей водой можно заниматься, особенно там, где переводят охлаждение на испарительное охлаждение. Экономия воды – в 40 раз!
8. Определение технико-экономических показателей (ТЭП) в содопоташном производстве.
Выделяются до 100 технико-экономических показателей. Выделим наиболее существенные. Сопоставление отдельных видов технологических затрат для различных аппаратов показало, что при выпаривании стоимость пара составляет 81–87% от суммы технологических затрат на переработку растворов; при сушке 81–87% затрат приходится на долю мазута, при вакуум кристаллизации основной статьей расхода является стоимость воды (71–76%).
Эти данные можно использовать для выделения контуров, обслуживающих именно наиболее ресурсопотребляющие потоки и начинать работу именно с них.
Распределение переменной части технологических затрат на переработку содопоташных растворов показано в табл.1.
Табл. 1. Распределение переменной части технологических затрат

Затраты на пар – основные. Пар и ближе к технологии, чем вода и мазут. При этом все сосредоточено вокруг производства соды. Очень хорошо. Можно будет поискать специализированные решения из прошлого опыта проектирования.
9. Уровень автоматизации как часть ТЭП.
Уровень автоматизации достигает 75–76%, в т.ч. основных процессов (кальцинация, дистилляция) – 90–95%, уровень механизации в основных цехах достигает 71–72%.
Отрасль уже хорошо знакома с автоматизацией. Это важно. Более будет понятно, когда будем говорить о протоколах, нечувствительности, диагностике и пр. Это уже наша сфера и посмотрим на нее попристальнее.
Особенности систем автоматизации и регулирования содового производства
Производство соды относится к сложным объектам химической промышленности, эффективность работы которых может быть повышена путем установки эффективных автоматических регулирующих исполнительных устройств в АСУ ТП.
Характерными особенностями содового производства являются непрерывность и крупнотоннажность технологических процессов, значительное количество основных и вспомогательных отделений, отличающихся сильной взаимозависимостью. На каждое из них воздействует большое число разнородных возмущений. Характеристики самих технологических аппаратов являются нестационарными как по статическим, так и динамическим характеристикам, что требует постоянной корректировки технологических режимов и большего внимания к динамическому регулированию. Особенно важно отметить, самой характерной средой содового производства являются агрессивные, кристаллизующиеся и абразивные среды. В схемах работы имеются рециклы, связывающие режимы основных отделений, поэтому нарушение режима в одном из них приводит к нарушению нормального хода всего производства.
С точки зрения контуров регулирования и управления содовые производства имеют следующие особенности:
– Последовательная технологическая структура, при которой выход из строя или даже временная разгрузка одной из стадий приводит к резкому изменению работы всего агрегата.
– Значительное число параллельно включенных аппаратов в основных отделениях – абсорбции, фильтрации, дистилляции и карбонизации. Например, отделение карбонизации типового многоэлементного завода содержит три серии карбонизационных колонн. В свою очередь каждая серия состоит из 4 или 5 карбонизационных колонн, одна из которых работает в режиме предкарбонизации.
– Отсутствие промежуточных емкостей и жесткие связи между отдельными стадиями.
– Достаточно большие мощности агрегатов, определяющие необходимость длительного цикла непрерывной работы.
– Большое число точек контроля параметров технологического процесса, составляющее часто до 1000 позиций.
– Жесткие требования к качеству регулирования, поскольку нарушение технологического режима распространяются на смежные отделения и в конечном итоге могут приводить к нарушению режима производства в целом или значительным потерям.
1.1. Особенности производства кальцинированной соды.
Производство кальцинированной соды состоит из следующих этапов:
– абсорбции и очистки рассола
– карбонизации
– фильтрации
– кальцинации
– дистилляции
– гашения
– обжига.
Перейдем к клапанам.
Регулирующие клапаны для основного оборудования содового производства.
ИЗВЕСТКОВЫЕ ПЕЧИ
Состав исходных продуктов:
Мел CaCO3, на сухое вещество не менее 96%
SiO2 и нерастворимые в HCl примеси не более 2%
Топливо – кокс не более 82%
Зольность -10,5%
влага – 5%
Летучие – 2,0
Сера 0,5%
Известковые печи
Температура в кожухе – не выше 70оС
Давление – 200–350 мм вод ст.
Вверху печи – 2–10.
Печной газ
Температура – не выше 150оС
Содержание на абсолютно сухой газ
СО2 -33–35%
О2 0,5–1,5%
СО 0,5–2,0%
Пыли гм3, не более 2,0
Газ после электрофильтра
Температура, оС:
– На входе 30–35
– На выходе 20–25
Разрежение, кПа (70–100)
Содержание СО2–32–34
Пыли не более 10гм3
Участки регулирования
– Регулирование известково-обжигательных печей предусматривает поддержание стабильной нагрузки печей с учетом потребности в негашеной извести и поддержание оптимальных параметров процесса.
– Регулирование состоит из следующих подсистем:
– Расход воздуха
– Температура газа
– Давление газа в верхней части печи и выброс диоксида серы в атмосферу посредством дроссельных заслонок, степень открытия которых изменяется с помощью регуляторов давления.
– Регулирование подачи топлива.
– Регулирование на участках дутьевых вентиляторов, электрофильтра, промывателей и пр.
С учетом сказанного на этом участке сосредоточимся на стабилизации процесса. Они работают в стационарном режиме и, как правило, относятся к медленным процессам.
ПРИГОТОВЛЕНИЕ ИЗВЕСТКОВОГО МОЛОКА
Получение известкового молока включает стадии гашения извести горячей водой и очистку известкового молока от крупных кусков необожженного карбонатного сырья, мелких зерен недопала, перекала и др. нерастворимых примесей.
При регулировании решаются задачи соответствия нагрузки в отделении гашения потребности в дистилляции в известковом молоке, а также поддержание постоянной концентрации гидроксида кальция в известковом молоке.
Участки регулирования:
– Регулирование расхода нагретой промывочной воды (слабое известковое молочко) для гашения
– Регулирование на участках промывки после сортировочного барабана
– Регулирование конденсатора
– Регулирование классификатора
– Вспомогательные контуры регулирования на мешалках, шаровых мельницах очистки от шлама, отбросной жидкости дистиллера, пара, дистиллерной жидкости, пробоотборники и пр.
Вот и пришли к сложным участкам. Известковое молочко – один из весьма сложных видов среды для регулирования.
Основными проблемами являются колебания титра молока, т.к. они усложняют дозирование молока в отделении дистилляции и увеличивают потери извести и аммиака с отбросной жидкостью дистиллера. В последней содержание свободного СаО может колебаться в очень узких пределах (1–2 н.д), т.е. в пределах одного нормального деления. В аппаратах отделения дистилляции известковое молоко разбавляется примерно 4 раза. Отсюда следует, что колебания титра молока, поступающего на дистилляцию, не должны превышать 4 н.д.
Титр молока регулируют расходом воды, подаваемой на гашение. Концентрация Са(ОН)2 измеряется каждые 30 мин.
Конечная температура молока (85–95%) в значительной степени зависит от температуры, поступающей на гашение воды, которая подогревается за счет тепла конденсации водяных паров, выходящих из гасителя. Для гашения используют подогретую воду из холодильников газа содовых печей или газа дистилляции.
Сложности для арматуры.
– Налипание и кристаллизация осадка.
– Сложная среда с большим количеством хлор-ионов, вызывающих значительную коррозию даже при высокой щелочности среды (рН 8–11,4).
– Истирание затворов и значительные трудности при страгивании затвора.
– Зарастание трубопроводов и, как следствие, уменьшение проходного сечения, что приводит к изменению пропускной способности и возможной потере линейности регулирования. Желательна регулирующая арматура с более широким диапазоном регулирования.
ПРЕДВАРИТЕЛЬНАЯ ОЧИСТКА СЫРОГО РАССОЛА
Технологическая схема очистки основана на осаждении с предварительной каустификацией содового раствора. Основной задачей регулирования является поддержание стабильности нагрузки по очищенному рассолу. Необходимая степень очистки рассола достигается стабилизацией концентрации рассола и дозирования осадительных реагентов в зависимости от нагрузки и постоянства температурного режима.
Участки регулирования
– Регулирование подачи содового раствора из декарбонизатора
– Разбавление очищенным рассолом известкового молока
– Регулирование подачи содового раствора и известкового молока в каустификатор.
– Регулирование узла отвода шлама
– Регулирование подачи реагентов и сырого рассола
Сложности работы арматуры:
– Инкрустация поверхностей при кристаллизации Ca(CO)3 и Mg (OH)2.
АММОНИЗАЦИЯ (АБСОРБЦИЯ) ОЧИЩЕННОГО РАССОЛА
Технологическая схема процесса абсорбции состоит из участка напора (напорный бак), промывателя воздуха фильтров, промывателя газов колонн, промывателей газа абсорбции, собственно абсорберов, холодильника газов дистилляции, холодильника аммонизированного рассола, сборника конденсата и сборника аммонизированного рассола.
Опыт эксплуатации показывает, что более 50% возмущений режима отделения карбонизации является следствием изменения качества аммонизированного рассола.
Задачами развития технологической схемы участка абсорбции являются повышение уровня регулирования процесса, в частности, за счет реализации схем воздействия на расход рассола, т.к. продолжительность и амплитуды переходных процессов в такой схеме значительно меньше по сравнению со схемой, в которой производится воздействие на нагрузку дистилляции.
Поскольку отделения аммиачного цикла в содовом производстве взаимосвязаны, то важно, чтобы нагрузки были согласованы в динамическом режиме регулирования.
Регулирование процесса
Задачей регулирования является получение аммонизированного рассола постоянного заданного состава путем поглощения всего поступившего на абсорбцию аммиака.
Участки регулирования
– Узел регулирования очистки отходящих газов от аммиака, включая промывку газов свежим рассолом, получения рассола с минимальным содержанием аммиака, охлаждения и отвода тепла при растворении NH3 и СО2 в рассоле и конденсации водяных паров.
– Регулирование температуры рассола на выходе из абсорбера
– Регулирование температуры рассола на входе в абсорбционную колонну
– Регулирование температуры на выходе из промывателя газа
– Регулирование вспомогательных контуров
– Регулирование давления и температуры для стабилизации состава парогазовой смеси, поступающей из отделения дистилляции на абсорбцию через регулирование подачи охлаждающей воды, и степень открытия заслонки на газопроводе, отводящем газ к вакуум насосам.
– Регуляторы температуры рассола
– Регуляторы температуры воды в холодильники
– Регулятор уровня рассола в напорном баке
Какое разнообразие!
КАРБОНИЗАЦИЯ
Является ведущим отделением содового производства. Технологическая схема состоит из колонны предварительной карбонизации, промывателя газа колонн, осадительной карбонизационной колонны, холодильника, трубопровода подачи смешанного газа, подачи газа известковых печей.
Ведущим потоком отделения карбонизации принимается поток диоксида углерода, поступающего из отделения кальцинации.
Регулирование
Решаются задачи поддержания стабильных и оптимальных параметров технологического процесса. Обеспечивается соответствие между количествами подаваемого диоксида углерода и аммонизированного рассола.
Узлы регулирования
– Регулирование постоянного уровня жидкости в колонне
– Регулирование расхода и давления, температуры жидкости на входе, газа на входе,
– Регулирование расхода, давления и температуры жидкости на выходе, газа на выходе
– Регулирование подачи охлаждающей воды и воды на выходе из холодильников.
– Регулирование разбавления и поддержания стабильной концентрации ионов Cl-.
– Регулирование выдуваемого аммиака
– Регулирование параметров вакуум фильтров
– Регулирование уровня
– Регулирование вспомогательных участков
Клапаны систем выпуска газов в атмосферу в связи с наличием экспанзерного газа, содержащего H2, H2S, CO.
Сложности при регулировании
– Множество взаимосвязанных узлов.
– Барботажные узлы, приводящие к повышенной вибрации.
Сложности для арматуры
Основной проблемой является кристаллизация и инкрустация поверхностей гидрокарбонатом натрия, кристаллизующегося из раствора с образованием отложений кристаллической массы. В процессе рабочего пробега колонны происходит зарастание ее внутренней поверхности и поверхностей холодильных трубок отложениями бикарбоната натрия, что приводит к изменению условий пребывания жидкости в колонне, условий охлаждения и, как следствие, условий абсорбции СО2 жидкостью. Карбонизационные колонны каждой серии последовательно, по мере окончания рабочего цикла переключаются на промывку.
Таким образом, частые остановы с целью промывки отложений и повышенная цикличность работы арматуры является особенностью процесса. Так без промывки колонна работает не более 3х-4х суток. Промывка может длиться 16–20 ч. Количество колонн для обеспечения непрерывности процесса составляет не менее 4-х ед.
При расчете арматуры необходимо использовать данные по цикличности работы арматуры в связи с частыми отключениями каскада колонн для промывки.
КАЛЬЦИНАЦИЯ
Технологическая схема процесса кальцинации состоит из следующих узлов: смесителя, питателя, вакуум-фильтра, скребкового транспортера, бункера, шнековых транспортеров, транспортных труб, циклона, коллектора газа содовых печей, холодильника газов содовых печей, промывателя газов содовых печей, сборника слабой жидкости, элеватора, выгружного шнека, газоходов, содовой печи и топки.
Критичной является работа вакуум-фильтра.
Регулирование.
Задачами регулирования являются стабильная работа вакуум-фильтров, и регулирование важных параметров, например, уровня суспензии в корытах вакуум-фильтров, давления воздуха на продувку фильтрующего сукна, уровень промывной воды в напорном баке, расход воды на промывку NaHCO3, поддержание уровня вакуума, стабилизация уровня на линии подачи суспензии.
Узлы регулирования.
В содовых печах
– Регулирование топлива мазута и природного газа
– Регулирование подачи воздуха
– Отвода отходящих газов.
Паровой кальцинатор (как альтернатива содовым печам)
– Регулирование подачи пара
– Регулирование отвода конденсата.
Вакуум-фильтр
– Подача NaHCO3.
– Регулирование расхода промывной воды
Циклон
– регулирование подачи газа с известковых печей
Холодильник газа содовых печей
– Регулирование расхода охлаждающей воды
– Регулирование подачи газа из коллектора газа содовых печей
– Регулирование подачи воздуха в аппараты охлаждения соды с кипящим слоем.
Вспомогательные контуры
– Пневмотранспорт
УЧАСТОК ДИСТИЛЛЯЦИИ
На участке происходит регенерация аммиака из фильтровой и других жидкостей содового производства. Технологическая схема включает дистиллер, теплообменник дистилляции, узел внешнего перелива жидкости, конденсатор дистилляции, напорный бак, мешалку известкового молока, смеситель, испарители, пескоуловитель.
Регулирование
Задачей регулирования является оптимизация и поддержание стабильных параметров отгонки NH3 и СО2. Обеспечивается регулированием расходов фильтровальной жидкости, пара и известкового молока, а также регуляторами давления пара в общем паровом коллекторе и уровня фильтровой жидкости в напорном резервуаре.
Узлы регулирования
Конденсатор дистилляции
– Регулирование подачи парогазовой смеси, фильтровальной жидкости и охлаждающей жидкости
Теплообменник дистилляции
– Регулирование нагревания жидкости и подачи парогазовой смеси
– Регулирование уровня
Дистиллер
– Регулирование отгонки аммиака из жидкой фазы
– Регулирование подачи парогазовой смеси
Смеситель
– Регулирование расхода фильтровальной жидкости и известкового молока
Сложности работы арматуры
Образование гипсовых отложений на рабочих поверхностях арматуры. Необходимость шабрирования как седел, так и поворотного затвора. Избегание подпружиненных седел. Большее внимание к эрозионно-коррозионному износу поверхностей. Вероятность заклинивания, как по седлу, так и по поворотному затвору из-за образования отложений.
Влияние изменений в производительности и маневренности производства
Учитывая как рост производительности, так и ее частое изменение в зависимости от рыночных условий, часто задаются требования частого изменения нагрузки.
Применительно к клапанам это означает требование расширения диапазона регулирования. Это, в свою очередь, приводит к росту использования специализированных клапанов с расширенными расходными характеристиками.
Требования к устойчивости поддержания процесса
Большое значение начинает иметь также и поддержание устойчивых характеристик регулирования с ростом срока эксплуатации. Так, на основе анализа до 500 смен было выявлено, что среднемесячные потери по выпуску кальцинированной соды на одном из заводов составляли до 8% из-за отклонений технологического режима.
Многие из них можно было бы предотвратить, если реализовывать систему технической диагностики, в т.ч. и клапанов. Потери также значительно уменьшатся как за счет сокращения времени на поиск и ликвидацию, так и за счет предотвращения наступления отклонений. Для этого нужны смарт клапаны с развитой диагностикой.
Ужесточение экологических требований
Резкое ужесточение экологических требований привели к тому, что для опасных производств могут применяться клапаны с экологическими сертификатами, сертифицированными на отсутствие выбросов. Для примера, такие клапаны могут быть установлены на участках аммиака и подачи аммиачных рассолов, экспанзерного газа и др., имеющих высокую опасность для персонала. В частности, кратность воздухообмена, требуемая по нормам и СНиП должна составлять не менее 8–10.
Действительно так. Принятие обязательств по снижению экологического риска часто обязывает компании выделять в опасных производствах зоны и системы безопасности, где диагностика клапана должна проводиться на основании специализированных диагностических комплексов без нахождения оператора в опасной зоне.
Подходы к арматуре на основе высокого уровня автоматизации
Спецификой технологических схем содового производства является многоэлементность и, соответственно, как объект управления перед АСУ ТП, оно ставит задачи распределения и согласования нагрузок элементов технологического процесса и отделений.
Дальнейшее совершенствование АСУ ТП связано с расширением функциональных возможностей. Появляются аппараты большой единичной мощности, усложняется технология, создаются замкнутые оборотные циклы производства с целью достичь по возможности полной безотходности производства. Существенное значение в последнее время стали иметь вопросы энергосбережения и энергоэффективности, повышения уровня промышленной безопасности.
С необходимостью совершенствования АСУ ТП связано и появление децентрализованных систем управления. Функции в них значительно перераспределены. Первичная обработка информации осуществляется в автономных процессорах, а центральный процессор берет на себя решение только наиболее сложных задач. Клапан с насыщенной интеллектуальной частью также выполняет ряд диагностических и других задач, которые ранее выполнялись только системой автоматизации.
К слову сказать, если будет принята концепция распределенных систем управления с большой степенью ответственности полевого уровня автоматизации, то система диагностики FIELD CARE легко впишется в такую АСУ ТП.
Учитывая эти факторы, появились новые подходы на основе цифровых сигналов, реализуемых полевыми шинами для лучшего контроля за технологическими процессами. Они с успехом заменяют традиционные щитовые способы представления информации с большим числом операторов, отвечающих только за работу отдельного производственного участка. Это не обеспечивает требуемой согласованности и оперативности в управлении крупнотоннажными агрегатами. Большое число параметров, которые должны контролироваться и диагностироваться, привели к внедрению исполнительных устройств и средств автоматизации на основе возможностей современных АСУ ТП, построенных на высоком уровне обработке информации.
Таким образом, небольшой конфликт уже налицо. Современные распределенные системы автоматизации требуют и цифровых исполнительных устройств, а не достаточно устаревшего HART протокола…
Изменения в связи с ростом степени автоматизации
Благодаря появлению в системах автоматизации дополнительных функций, насыщенность технологических схем исполнительными и регулирующими органами значительно возросла. Количество регулирующих клапанов и функционально связанной с ними запорной арматуры также резко возросло, в связи, с чем актуальным становится вопрос использования клапанов и арматуры, имеющих значительно большую способность к интеграции в системы АСУ ТП, но и желательно, обладающих одновременно и регулирующей и отсечной способностью. Такие решения уже есть, например, у компании Jamesbury.

Рис. 2. Клапаны с конструктивными элементами, предназначенный для интеграции в системы автоматизации.
Изменения в арматурном хозяйстве предприятий
За последние 10–15 лет произошли существенные изменения в арматурном хозяйстве предприятий химической отрасли. Наблюдается устойчивая постоянная тенденция к замене клапанов возвратно-поступательного действия поворотной арматурой. Это особенно выражено в регулирующей арматуре. Возросла роль автоматизации в диагностировании массы однотипного оборудования в т.ч. и (арматуры), постоянно осуществляется перевод систем на цифровую обработку сигналов.
Наверное, можно сказать, что вторая по приоритетности задача будет – уменьшение затрат на обслуживание через полное применение автоматизации диагностики клапанов.
Широкое применение поворотной арматуры и замена седельных клапанов и задвижек
Если в старых решениях в основном применялись вентили, шиберные и клиновые задвижки и только мембранные и поршневые приводы и аналоговые позиционеры, в независимости от типа контура, то в настоящее время выделяются критические контуры регулирования, где необходимость снижения колебательности процесса наиболее высока. Это особенно связано с ростом использования в схемах автоматических анализаторов, а также увеличением числа измерительных контуров в целом. Для таких контуров регулирования все больше применяются специализированные мембранные приводы (для четвертьоборотных клапанов) и интеллектуальные цифровые позиционеры с применением системы диагностики.