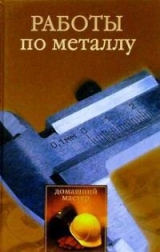
Текст книги "Работы по металлу"
Автор книги: Наталья Коршевер
Жанр:
Технические науки
сообщить о нарушении
Текущая страница: 8 (всего у книги 20 страниц) [доступный отрывок для чтения: 8 страниц]
Механические передачи, работающие на принципе зацепления, могут быть зубчатыми и червячными.
Зубчатые передачи, в свою очередь, подразделяются на цилиндрические и конические. Но и это не последняя классификация зубчатых передач.
В зависимости от расположения зубьев относительно оси цилиндрических колес различают:
– цилиндрические прямозубые передачи, самые простые по конструкции и, соответственно, в изготовлении, они не создают осевых нагрузок на валы, следовательно, не нуждаются в специальных упорных подшипниках, что значительно упрощает сборку. Такие передачи используются в механизмах с небольшой рабочей скоростью вращения вала. Недостатком прямозубых цилиндрических передач является большой шум во время работы механизма, особенно если колеса передачи недостаточно точно обработаны;
– цилиндрические косозубые передачи, их зубья расположены по винтовым линиям на делительном цилиндре. Так как зубья таких передач входят в зацепление плавно, постепенно, то снижается уровень шума и повышается нагрузочная способность. Однако из-за наклонного расположения зубьев осевая сила стремится сдвинуть колесо с валом вдоль оси, поэтому при сборке косозубых передач требуется осевая фиксация вала;
– цилиндрическая шевронная передача представляет собой колесо, венец которого состоит из чередующихся участков левых и правых зубьев. При таком их расположении осевая сила отсутствует, что обеспечивает передачу очень больших мощностей;
– цилиндрическая передача внутреннего зацепления. Поверхности зубчатых колес этой передачи расположены одна внутри другой, при этом колеса вращаются в одном направлении.
Перед установкой колес цилиндрических зубчатых передач проверяют их биение, то есть концентричность профиля зубьев относительно посадочного диаметра. Для этого зубчатое колесо устанавливают на жестко закрепленную оправку, между зубьями устанавливают цилиндрический калибр, на который помещают ножку индикатора, и записывают его показания. Поворачивают оправку, перекладывают калибр через два-три зуба и вновь записывают показания, продолжают таким образом до полного оборота оправки, затем из всех показаний выбирают наибольшее и наименьшее. Если полученные отклонения не превышают разрешенных (по техническим данным для конкретного механизма), то колесо допускают к сборке.
Сборка цилиндрических зубчатых передач состоит из следующих технологических операций:
– подготовка и проверка собираемых единиц. Зубчатые кольца передач должны быть обработаны, проверены на биение, промыты, просушены, на них не должно быть дефектов в виде забоин, задиров, заусенцев;
– сборка зубчатых колес, конечно же, если колеса разборные. Они обычно состоят из ступицы, которая выполнена из стали или чугуна, и венца зубьев (высококачественная сталь или текстолит). Венец напрессовывают на диск ступицы и фиксируют либо сваркой, либо с помощью стопоров, которые ввинчивают в специально просверленные отверстия с резьбой на венце и диске ступицы;
– установка и крепление зубчатых колес на валах. Зубчатые колеса надеваются на вал, и их положение фиксируется шпонками, шлицами или болтами;
– установка валов с зубчатыми колесами в подшипники корпуса;
– регулировка зацепления зубьев у отдельной пары колес и у передачи в целом. Для регулировки проверяют качество зубчатого зацепления на краску. Зубья меньшего по диаметру колеса покрывают тонким слоем краски и прокручивают пару передачи на один оборот и обратно. При правильном зацеплении пятна краски на парном колесе должны быть расположены на средней части боковой поверхности зубьев и занимать не менее 50–60 % поверхности зуба по высоте и не менее 70–90 % по длине. Если пятна смещены по длине поверхности, то налицо перекос осей валов. Смещение пятен по высоте ближе к ножке зубьев свидетельствует об уменьшении межцентрового расстояния валов, а ближе к головке зубьев – об увеличении межцентрового расстояния.
Конические зубчатые колеса являются составной частью передач, в которых оси валов пересекаются под определенным углом (самые распространенные – 90°). Форма зубьев конических колес может быть прямой, косой и круглой. Колеса с косыми и круглыми зубьями используются в передачах, испытывающих большие нагрузки и большие скорости вращения валов (например, при передаче вращения от коробки скоростей на задний мост автомобиля).
Приемы установки и закрепления колес в конических передачах аналогичны приемам установки и закрепления цилиндрических зубчатых передач. Но при сборке конических передач следует помнить, что зацепление колес правильное тогда, когда оба колеса будут установлены в такое положение, при котором образующие начальных конусов (I–I и II–II) совместятся, а предполагаемые центры конусов (О и О1) совпадут (рис. 63).

Рис. 63. Коническая зубчатая передача.
Прежде чем установить валы с коническими колесами, проверяют правильность взаимного расположения осей их посадочных мест, для чего на посадочные места устанавливают две оправки, центрирующиеся в отверстиях: если в зазор между ними щуп входит свободно, значит, расположение осей правильное.
Нормальная работа конической передачи возможна лишь при наличии бокового зазора между зубьями сопрягаемых колес.
Величина зазора разная для каждого вида механизмов и находится в пределах 0,08–0,20 мм. Измерить величину бокового зазора можно щупом, если к колесам имеется свободный доступ. Но более распространен контроль с помощью свинцовых пластинок: между зубьями сопрягаемых колес пропускают свинцовую пластинку и колеса проворачивают. Повторяют операцию в нескольких равномерно расположенных по окружности местах, каждый раз используя новую пластину.
Микрометром (см. рис. 1, б) измеряют толщину каждой из деформированных пластин; величину зазора определяют как среднеарифметическое полученных измерений.
При несоответствии фактического зазора необходимому его величину регулируют, для чего одно из колес перемещают либо по направлению к предполагаемой вершине конуса для уменьшения зазора, либо от нее для его увеличения. А чтобы зафиксировать новое положение конических колес, под их опорные поверхности устанавливают прокладки.
Собранную зубчатую коническую передачу проверяют на качество зацепления (проверка на краску аналогично проверке цилиндрических передач), на уровень шума (при его высоком уровне передачи прирабатывают в медленном режиме), на трение (если смазочный материал не перегревается, значит, трение в сопряжениях нормальное).
Червячные передачи используются в том случае, если геометрические оси валов перекрещиваются между собой, как правило под углом 90°.
Червячная передача состоит из червяка и червячного колеса. При этом червяк может быть прямым – цилиндрическим (в зацепление с ним одновременно входят 1–2 зуба червячного колеса) – или глобоидным – вогнутым (здесь одновременно в зацеплении находится 5–6 зубьев, в результате чего они значительно опережают цилиндрические червячные передачи по передаваемой мощности и КПД). При сборке червячных передач сначала в корпус механизма устанавливают подшипники скольжения, а уже в них – валы, на которых установлены червяк и червячное колесо.
Перед окончательным креплением передачи проверяют правильность зацепления зубьев на краску: в данном случае тонким слоем краски покрывают винтовую поверхность червяка, затем его медленно поворачивают (рис. 64).

Рис. 64. Контроль правильности зацепления червячной передачи.
При правильном зацеплении краска должна покрыть боковую поверхность зубьев червячного колеса по длине и высоте не менее чем на 50–60 % (в средней части).
Отрегулировать зацепление червячной передачи можно с помощью подбора соответствующей толщины правой или левой прокладки под фланец червячного колеса (для удобства они сделаны в форме полуколец, поэтому их установка не требует разборки узла, достаточно лишь ослабить установочные винты). Во многих передачах такого типа подшипниковые стаканы, в которые устанавливаются червяки, снабжены резьбой, поэтому регулировку зацепления можно производить поворотом гаек, перемещая их вместе с зубчатыми колесами вдоль оси.
Ремонт зубчатых передач и уход за нимиДля того чтобы зубчатая передача работала исправно и не приводила к сбою в работе всего механизма в целом, за ней нужно организовать правильный уход. Что это значит?
При попадании в передачу грязи, абразивной и металлической пыли, при отсутствии или недостаточном количестве смазки зубья колес быстро изнашиваются, на их поверхностях образуются шероховатости, которые могут привести к заклиниванию передачи. Поэтому открытые передачи, которые не имеют защитного кожуха, периодически смазывают кистью или масленкой, одновременно очищая их от пыли и грязи. Закрытые передачи в смазке нуждаются реже, их погружают в масляную ванну или смазывают струей масла, подаваемого под давлением в зону сопряжения зубьев.
В ходе эксплуатации зубья передач периодически осматривают на предмет обнаружения износа: если износ зубьев превышает допустимый, значит, колеса подлежат замене (при этом заменяются оба колеса пары).
Если колеса разборные, то можно ограничиться заменой венца, для чего старый венец срезают, на его место напрессовывают и стопорят новый. Если зубья работают с одной стороны, то колеса можно просто перевернуть, подрезав несимметричную ступицу с одной стороны, а с другой приварив кольцо.
Одной из частых причин выхода из строя передачи является поломка зуба. Отремонтировать «беззубое» колесо (правда, только цилиндрическое) можно заливкой нового зуба по профильному шаблону: на колесе в месте излома на планках и шпильках крепят профильный шаблон, выемку заливают расплавленным металлом, после его остывания профиль зуба обрабатывают, сверяясь с шаблоном (рис. 65).

Рис. 65. Восстановление зубьев цилиндрических колес с помощью профильного шаблона: 1 – зуб цилиндрического колеса; 2 – планка; 3 – новый зуб; 4 – профильный шаблон.
Зуб можно также приварить (наплавить) газовой или электросваркой электродами Э-42 с толстой обмазкой ОММ-5. После наплавки зуб обрабатывают и закаливают.
Сборка цепных передачО цепных передачах разговор особый, ибо и сами они не совсем обычны: с одной стороны, цепная передача относится к разряду гибких, где цепь представляет собой своеобразный ремень, но, с другой стороны, передача вращающего момента осуществляется не за счет силы трения, а за счет зацепления звеньев цепи за зубья зубчатых колес (звездочек), следовательно, цепная передача является одновременно зубчатой.
Поэтому она обладает достоинствами и у нее отсутствуют недостатки как гибкой, так и зубчатой передач: во-первых, с ее помощью можно передавать вращающие моменты между валами, находящимися на значительном удалении друг от друга – до 8 м (как при ременной передаче); во-вторых, она сохраняет постоянство передаточного числа, то есть отсутствует проскальзывание (как в зубчатых передачах); в-третьих, цепь этой передачи не требует большого натяжения (в отличие от ремня); в-четвертых, она может передавать большие крутящие моменты; в-пятых, КПД цепной передачи достигает 0,98.
Классификация цепных передач производится по двум признакам: по назначению (грузовые – для поднятия грузов, тяговые – для перемещения грузов, приводные – для передачи движения от двигателя к исполнительному механизму) и по конструкции приводных цепей (роликовые, втулочные, зубчатые и т. д.).
Приводная роликовая цепь состоит из переходных (валик с напрессованными наружными пластинами) и соединительных (втулка с насаженным на нее роликом и напрессованными внутренними пластинами) звеньев (рис. 66).

Рис. 66. Цепная передача: а – роликовая цепь.

Рис. 66 (продолжение). Цепная передача: б – втулочная; в – зубчатая цепь; г – узел цепной передачи: 1 – ведущий вал со звездочкой; 2 – ведомый вал со звездочкой; 3 – цепь; 4 – регулировочное приспособление для натягивания цепи со звездочкой.
Ролик в соединительных звеньях насажен на втулку с некоторым зазором, что обеспечивает создание между зубьями звездочек и цепью трения качения. Применяются такие передачи в механизмах, где окружные скорости не превышают 15 м/с.
Роликовые цепи могут быть одно– (ПР) и двухрядные (2ПР) – для передачи небольших мощностей, а также трех– (3ПР), четырехрядные (4ПР) цепи с изогнутыми пластинами (ПРИ) и цепи тяжелого типа (ПРТ, 2ПРТ, 3ПРТ, 4ПРТ и 6ПРТ) – для передачи больших мощностей. Многорядные цепи собираются из обычных звеньев с применением удлиненных валиков. Промышленностью выпускаются цепи с шагом определенной величины (соответственно под них выпускаются и звездочки): 8, 9,525, 12,7, 15,875, 19,05, 25,4, 31,75, 38,1, 44,45, 50,8, 63,5 и 76,2 мм.
Приводные втулочные цепи представляют собой подобие роликовых, но ролики не имеют (рис. 66, б). Вследствие этого они значительно легче и ощутимо дешевле роликовых цепей. Однако они больше подвержены износу, поэтому применяются только для передачи малых мощностей в тихоходных механизмах.
Маркировка и роликовых, и втулочных цепей одинакова: на первом месте указывается количество рядов (при маркировке однорядных цепей 1 не указывается), далее идут заглавные буквы, обозначающие тип цепи (ПР – роликовая, ПРИ – роликовая изогнутая, ПРТ – роликовая тяжелая, ПВ – втулочная), следующее число говорит о величине шага звеньев цепи, последнее числовое значение указывает предельно допустимую силу нагрузки.
Конструкция приводной зубчатой цепи состоит из рабочих пластин, соединенных между собой вкладышами качения, и направляющих пластин, которые фиксируют цепь в осевом направлении.
Цепи могут быть однопарными и многопарными в зависимости от назначения. Шаг звеньев цепей 12,7, 15,875, 19,05, 25,4 и 31,75 мм. Такие цепи используют в механизмах, имеющих большие окружные скорости (до 30 м/с) и испытывающих неравномерную загрузку.
Как уже было сказано, цепная передача движения осуществляется за счет зацепления цепи за зубья звездочек. Звездочки изготавливаются из стали, число зубьев может быть от 9 до 22 и 25 (28), 32 (36), 40 (45), 50 (56), 63 (71), 80. Они бывают как цельные, так и разборные (ступица из чугуна или стали, а венец стальной, при этом венец напрессовывается на ступицу и закрепляется болтами или винтами).
Сборка узла цепной передачи состоит из следующих операций:
– звездочки устанавливаются на взаимодействующие валы методом напрессовки прессами или винтовыми приспособлениями и фиксируются во избежание осевого смещения;
– производится проверка их расположения (они должны находиться в одной плоскости) и радиального и торцевого биения (с помощью индикатора);
– подбирается отрезок цепи необходимой длины (при ремонте – по старой цепи, при первичной сборке – согласно техническим условиям на конкретный механизм), надевается на звездочки и натягивается специальным приспособлением;
– замыкается цепь в кольцо. Если цепь состоит из четного количества звеньев, то ее концы соединяются обычным звеном, если число звеньев нечетное, то переходным звеном.
Для нормальной и долговечной работы цепной передачи необходимы два условия:
– во-первых, соблюдение натяжения цепи. Поскольку при работе механизма цепь испытывает постоянные нагрузки на вытягивание, то провисание цепи может увеличиться, цепь начнет болтаться, износ элементов передачи будет ощутимее. Поэтому при вытягивании цепи ее подтягивают либо натяжной звездочкой, если она предусмотрена конструкцией механизма, либо путем удаления звеньев, если это допустимо по техническим условиям, если натяжение откорректировать этими способами нельзя, то устанавливается новая цепь;
– во-вторых, постоянное присутствие смазочного материала.
Если для смазывания сопрягаемых элементов передачи используется пластичный смазочный материал, то цепь перед очередной процедурой смазки промывают в керосине, просушивают, а смазывают ее путем погружения в расплавленную смазку.
Если используется жидкая смазка, то необходимо своевременно пополнять масленки.
Сборка передач, основанных на силе тренияМеханические передачи, работа которых основана на силе трения, можно разделить на две группы: ременные – используются в том случае, если взаимодействующие валы находятся на некотором удалении друг от друга, и фрикционные – если валы расположены в непосредственной близости.
В ременных передачах движение передается посредством гибкого, замкнутого в кольцо, ремня, надетого на два шкива. Ремни могут быть плоскими, клиновыми и круглыми.
Плоские ремни изготавливаются из кожи, прорезиненных или хлопчатобумажных тканей, шерсти или шелка. Перед установкой такие ремни подвергают растягиванию в течение 3–5 суток, затем концы ремней соединяют склеиванием, сшиванием или с помощью металлических прижимов. Самый лучший способ соединения – склеивание (кожаные – косым швом, прорезиненные – ступенчатым). Для склеивания кожаных ремней используют мездровый, желатиновый, целлюлозный, рыбный клеи, для прорезиненных – резиновые тиуратовые клеи 1-го и 2-го сортов в равных долях. Концы кожаных ремней перед склеиванием тщательно зачищают, наносят два слоя клея с интервалом в 5–6 минут и накладывают ремни друг на друга. Затем клееный шов зажимают между двумя дощечками, которые стягивают болтами, и выдерживают в течение 5–8 часов.
Концы прорезиненных ремней зачищают ножом, затем напильником делают ступенчатые уступы и обезжиривают бензином, наносят 3–4 слоя клея (перед нанесением последующего слоя предыдущий просушивают), после нанесения последнего слоя (без просушки) концы соединяют, зажимают струбцинами между двумя дощечками и выдерживают при температуре 16–20 °C 24 часа (или при температуре 100 °C – 3–4 часа). Используют плоские ремни в передачах со скоростью вращения до 30 м/с.
Клиновые ремни могут быть кордтканевые или кордшнуровые, с гладким и зубчатым профилем, угол трапецеидальной формы – 40°.
Обладая достаточной гибкостью и большей, по сравнению с плоскими ремнями, прочностью, клиновые ремни используются для передачи мощностей от 0,3 до 75 кВт (в зависимости от профиля и длины ремня). Шкивы для клиноременных передач на ободе имеют канавки клиновидной формы, с углом профиля 34–40°.
Ремни круглого профиля бывают кожаными, хлопчатобумажными, капроновыми или прорезиненными, диаметром от 2 до 20 мм. Область применения та же, что и у плоских ремней. Профиль канавки шкива круглоременной передачи полукруглый, с радиусом, равным радиусу ремня.
Технологический процесс сборки ременной передачи состоит из следующих этапов:
– балансировка шкивов, то есть устранение их неуравновешенности. Она достигается либо путем высверливания части металла из шкива, либо путем нагружения его специальными грузиками;
– установка шкивов на валы. Их напрессовывают и закрепляют шпонкой или шлицем (следует учесть, что для напрессовки шкива на вал нельзя пользоваться ударными инструментами, поэтому ее осуществляют с помощью специальных приспособлений);
– регулирование передачи заключается в создании определенного усилия натяжения ремня. Натяжение проверяют динамометром или гирями, подвешенными за скобу (при воздействии определенной силы от 50 до 100 Н или при определенном весе гирь должен быть такой же прогиб ремня, который задается техническими условиями для каждого конкретного механизма). При слабом натяжении ремень проскальзывает при работе механизма или «бьет» (хлопает), нагревается, что приводит к его быстрому износу; чрезмерное натяжение ремня создает излишнюю нагрузку на подшипники, а также ведет к быстрому износу шеек вала и шкивов. Регулировка натяжения производится перемещением натяжного ролика.
Работоспособность ременной механической передачи характеризуется величиной углов обхвата (угол, образуемый лучами, выходящими из центра шкива и проходящими через крайние точки сопряжения шкива с ремнем). Определяющим является угол обхвата меньшего шкива, он должен быть не менее 120°. Это условие выполняется, если отношение величины диаметра ведущего шкива к величине диаметра ведомого находится в пределах от 1/3 до 3, а межосевое расстояние не меньше удвоенной суммы величин диаметров обоих шкивов. Фрикционные передачи (рис. 67) передают вращательные движения между валами с помощью силы трения.

Рис. 67. Вариант фрикционной передачи: 1 – конический барабан; 2 – винт; 3 – фрикционное колесо; 4 – гайка; 5 – маховик.
Самые распространенные механизмы, в которых используются фрикционные передачи, – фрикционные муфты и тормоза.
Фрикционные муфты, в зависимости от назначения, могут быть сцепными (находящимися в постоянном сцеплении, но при необходимости разъединяющимися), например муфта сцепления в автомобиле, или предохранительными – они предохраняют привод от поломок во время перегрузок.
Название тормоза говорит само за себя: это устройство для уменьшения скорости, вплоть до полной остановки машины. Тормоз любого механизма характеризуется двумя показателями: временем торможения и скоростью, при которой начинается торможение.
Время торможения зависит от контакта тормозной колодки или ленты с вращающимися элементами тормоза, поэтому важно плотное прилегание фрикционного материала к колодке или ленте (без складок, выпучиваний и выступаний головок заклепок), а площадь его контакта с поверхностью торможения должна быть не менее 80 %.
Во время работы механизма, то есть при бездействии тормоза, фрикционный материал не должен соприкасаться с вращающимися деталями, для чего предусмотрен определенный зазор.
Однако если зазор будет очень мал, то это неизбежно приведет к нагреванию поверхностей трущихся пар и быстрому их износу.
Основной деталью фрикционной передачи является фрикционное колесо, которое и передает вращательные движения с одного вала на другой (оно может быть текстолитовым, фибровым, кожаным, деревянным или резиновым). Величина передаваемого крутящего момента зависит от коэффициента трения фрикционных пар, а также от усилия прижима друг к другу отдельных единиц фрикционной передачи. Технологический процесс сборки фрикционных передач аналогичен сборке зубчатых колес.