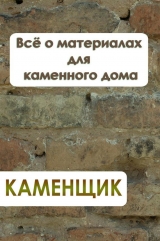
Текст книги "Всё о материалах для каменного дома"
Автор книги: Илья Мельников
Жанр:
Хобби и ремесла
сообщить о нарушении
Текущая страница: 2 (всего у книги 4 страниц) [доступный отрывок для чтения: 2 страниц]
ВЯЖУЩИЕ ВЕЩЕСТВА
Характеристика вяжущих материалов
Вяжущие вещества – это измельченные порошкообразные материалы, которые при смешивании с водой образуют пластичную массу, способную твердеть и превращаться в камневидное тело.
Различают известь, цементы, глину и гипсовые вяжущие вещества.
Минеральные (перечисленные) вяжущие вещества подразделяют на гидравлические и воздушные.
Гидравлические вяжущие вещества твердеют и повышают прочность не только на воздухе, но и в воде. К ним относят гидравлическую известь, цементы (кроме кислотоупорного), известково-шлаковые вяжущие. Воздушные вяжущие вещества твердеют и сохраняют прочность только на воздухе. К ним относят воздушную известь, кислотоупорный цемент, гипсовые и магнезиальные вяжущие, растворимое стекло и др.
Гидравлические свойства некоторых вяжущих веществ усиливают, смешивая их с природными и искусственными материалами, называемыми добавками. Добавки также снижают расход вяжущих веществ при изготовлении строительных деталей и конструкций, улучшают удобоукладываемость смеси, повышают морозостойкость и т. д.
Основной показатель качества вяжущих веществ – прочность. Прочность вяжущих веществ изменяется во времени, поэтому качество оценивают по прочности, набранной за определенное время твердения в условиях, установленных стандартом, т. е. маркой вяжущего.
Скорость твердения – это время, в течение которого вяжущее вещество набирает заданную прочность. Наибольшей скоростью твердения обладают гипсовые вяжущие вещества, медленно твердеет воздушная известь.
Схватывание – это процесс потери тестом пластичности. Схватывание характеризуется началом схватывания, т. е. временем в минутах от затворения вяжущего материала водой до начала потери им пластичности, и концом схватывания – временем от затворения до полной потери тестом пластичности. Наиболее короткими сроками схватывания обладают гипсовые вяжущие вещества (2-30 мин), более длительными – портландцемент (до 10ч).
Процесс твердения вяжущих материалов сопровождается выделением теплоты, усадкой или набуханием. Все операции по транспортированию и укладке смесей на основе вяжущих веществ должны заканчиваться до начала схватывания. Повторное перемешивание с добавлением воды для придания пластичности схватившейся растворной или бетонной смеси приводит к снижению прочности.
Известь
Строительную известь получают обжигом кальциевых и магнезиальных карбонатных пород.
О качестве извести свидетельствует высокое содержание в ней СаО и MgO. Содержание чистых оксидов CaO+MgO в общем количестве извести называют ее активностью. Недожог и пережог извести в печи снижают ее качество. Особенно опасен пережог: остеклованная известь медленно гасится и, увеличиваясь в объеме, может вызвать трещины в изделиях.
По условиям твердения строительную известь делят на воздушную, обеспечивающую твердение строительных растворов и сохранение ими прочности в воздушно-сухих условиях, и на гидравлическую, обеспечивающую твердение строительных растворов и сохранение ими прочности как на воздухе, так и в воде.
По составу известь делят на комовую и порошкообразную.
Воздушную известь в свою очередь делят на негашеную и гашеную или гидратную. В зависимости от содержания в ней оксидов кальция и магния воздушную известь разделяют на кальциевую (Mg0 не более 5 %), магнезиальную (Mg0 от 5 до 20 %) и доломитовую (MgO от 20 до 40%). В зависимости от активности и содержания непогасившихся зерен воздушную негашеную известь выпускают трех сортов, гашеную – двух.
Воздушная известь используется для приготовления известково-песчаных и смешанных строительных растворов.
Гашение извести происходит при обработке негашеной комовой кальциевой, магнезиальной или доломитовой извести водой. Этот процесс сопровождается выделением большого количества теплоты и интенсивным парообразованием. Негашеную комовую известь называют кипелкой. Для гашения извести применяют известегасительные барабаны или лопастные гидраторы.
В зависимости от времени гашения негашеную известь делят на быстрогасящуюся – не более 8 мин, среднегасящуюся – не более 25 мин и медленногасящуюся – более 25 мин.
В зависимости от количества воды, взятой для гашения, получают гидратную известь (пушонку), известковое тесто или известковое молоко.
Гидратную известь (пушонку) получают, когда для гашения берут 50-70% воды по массе извести. При этом 32 % воды участвует в химической реакции, а остальная испаряется в процессе гашения. В результате гашения объем полученной извести увеличивается в 2-3 раза по сравнению с исходным. Получившаяся гидратная известь представляет собой белый порошок, состоящий из мельчайших частиц гидрата оксида кальция. Средняя плотность в рыхлом состоянии – 400-450, в уплотненном – 500-700 кг/м3.
Для получения известкового теста для гашения 1 мас. ч. извести берут 3-4 мас. ч. воды. При этом объем получившегося известкового теста в 2-3,5 раза превышает объем исходной извести. Увеличение объема извести характеризуют выходом известкового теста, который равен объему теста в литрах, полученного гашением 1 кг извести. Известковое тесто представляет собой пластическую массу белого цвета средней плотностью 1400 кг/м3.
Погасившуюся известь, которая увеличилась в объеме не менее чем в 3 раза, называют жирной, а известь, увеличившуюся в объеме менее чем в 2,5 раза, – тощей. Выход известкового теста зависит от содержания в извести оксида кальция, количества посторонних примесей и качества обжига.
Для получения известкового молока для гашения 1 мас. ч. извести берут 8-10 мас. ч. воды. Известковое молоко можно применять без дополнительного выдерживания.
На специализированных предприятиях гашение извести ведут в известегасильных машинах. В некоторых машинах гашение извести совмещено с ее измельчением, что ускоряет гашение и сокращает количество отходов. Получающееся при этом известковое молоко сливают в металлические баки или специально оборудованные ямы, отстаивают, а затем перекачивают в автоцистерны, которые доставляют его к месту использования.
Гидравлическая известь является продуктом обжига при температуре 900-1100°С мергелистых известняков (содержание глины 8-20 %). Гидравлическую известь разделяют на слабогидравлическую и сильногидравлическую.
Применяют гидравлическую известь для приготовления растворных смесей, а также для бетонов низких классов, твердеющих как на воздухе, так и во влажных условиях.
Известесодержащие вяжущие гидравлического твердения – это группа низкомарочных местных вяжущих. В нее входят смешанные вяжущие (известково-пуццолановые и известково-шлаковые), а также гидравлическая известь.
Смешанные вяжущие – продукты совместного измельчения негашеной извести (10-30%), гидравлической добавки (85-70 %) и гипсового вяжущего (до 5 %). В качестве добавки используют горные породы, содержащие активный кремнезем – вулканический пепел, пемзу, туф, трепел и др. Такие вяжущие называют известково-пуццолановыми. Если в качестве добавки используют доменный гранулированный шлак, такие вяжущие называют известково-шлаковыми.
Известесодержащие вяжущие делят на марки 50; 100; 150; 200. Эти вяжущие применяют для приготовления растворов для подземной кладки и бетонов. Срок хранения вяжущих из-за наличия в них негашеной извести не более 30 сут. При хранении вяжущие необходимо предохранять от увлажнения.
Воздушную и гидравлическую известь хранят на складах в условиях, исключающих ее увлажнение. Негашеную комовую известь транспортируют в вагонах, контейнерах или в закрытых машинах; порошкообразную – в многослойных бумажных мешках, на которых указаны завод-изготовитель, вид и сорт извести, дата изготовления.
Сроки хранения с момента изготовления гидратной и порошкообразной извести в бумажных мешках не должны превышать 15 сут, так как поглощаемая влага из воздуха ухудшает качества извести (при длительном хранении образуются комки, уменьшается скорость схватывания). В герметичной таре срок хранения извести не ограничен.
Известковое тесто хранить больше суток нельзя, так как оно быстро твердеет.
Известь хранят и транспортируют раздельно по видам и сортам.
Гипс и глина
Гипсовые вяжущие, как уже отмечалось, обладают способностью быстро схватываться и твердеть. В зависимости от температуры тепловой обработки сырья их делят на две группы: низкообжиговые и высокообжиговые. К низкообжиговым гипсовым вяжущим относят формовочный строительный и высокопрочный гипс, а также гипсовые вяжущие вещества из гипсосодержащих материалов. К высокообжиговым – ангидритовое вяжущее (ангидритовый цемент) и высокообжиговый гипс (экстрихгипс).
По пределу прочности различают 12 марок гипсовых вяжущих. Марку вяжущего обозначают буквой "Г"с цифровым индексом, который обозначает минимальный предел прочности при сжатии. Например, марка Г-5 соответствует пределу прочности 5 МПа.
В зависимости от сроков схватывания гипсовые вяжущие разделяют на быстротвердеющие (А), нормальнотвердеющие (Б) и медленнотвердеющие (В). Сроки схватывания их – 2, 6, 20 мин соответственно, а конец схватывания – 15, 30 мин, для медленнотвердеющих не нормируется.
Гипсовые вяжущие добавляют в известково-песчаные растворы для увеличения их прочности и ускорения срока схватывания. Добавка гипсового вяжущего придает поверхности штукатурного слоя большую гладкость и белизну. Его применяют и как основное вяжущее вещество в мастиках.
Для изготовления строительных изделий используют в основном гипсовые вяжущие марок Г-2-7. При изготовлении гипсовых изделий гипсовые вяжущие затворяют водными растворами или дисперсиями полимеров, получая полимергипс. Он обладает большей плотностью, чем обычное гипсовое вяжущее, высокой механической прочностью (до 30 МПа), малой водопроницаемостью, постоянством объема, повышенным сопротивлением истиранию, а иногда (при использовании определенных типов смол) высокими электроизоляционными свойствами.
При длительном хранении даже в нормальных условиях активность гипсовых вяжущих снижается.
Глина – осадочная горная порода. В зависимости от содержания песка различают глину жирную, средней жирности и тощую. Глина обладает способностью во влажном состоянии образовывать пластичное тесто, легко принимающее заданную форму, которая сохраняется после испарения влаги. Используют глину в качестве вяжущего для приготовления печных и штукатурных растворов.
Цемент
Цемент применяют для приготовления бетонных смесей, строительных растворов, изготовления бетонных, железобетонных изделий и конструкций. Наиболее распространены портландцемент, шлакопортландцемент, глиноземистый цемент.
Цементы классифицируют по таким признакам: виду клинкера и составу, прочности при твердении, скорости твердения, срокам схватывания, специальным свойствам.
Портландцемент и его разновидности – основные вяжущие вещества, применяемые в строительстве. Портландцемент – гидравлическое вяжущее, получаемое тонким помолом портландцементного клинкера с гипсом, а иногда и со специальными добавками. Портландцементный клинкер – продукт обжига до спекания тонкодисперсной однородной сырьевой смеси, состоящей из известняка и глины или других материалов (мергеля, доменного шлака и пр.).
Для регулирования сроков схватывания портландцемента в клинкер при помоле вводят двуводный гипс в количестве 1,5-3,5% от массы цемента.
Различают портландцемент без добавок, портландцемент с минеральными добавками, шлакопортландцемент и др.
К основным свойствам портландцемента относятся средняя и насыпная плотность, тонкость помола, сроки схватывания, равномерность изменения объема при твердении и прочность затвердевшего цементного камня.
Средняя плотность портландцемента в зависимости от вида и количества добавок 2,9-3,2 г/см3, насыпная плотность в рыхлом состоянии 900-1100 кг/м3, в уплотненном – до 1700 кг/м3.
Тонкость помола характеризуется степенью измельчения, т. е. количеством цемента, проходящим через сито N 008 (размер отверстий 0,08 мм), и его удельной поверхностью. Через сито должно проходить не менее 85% пробы, а удельная поверхность (суммарная поверхность зерен, содержащихся в единице массы цемента) у обычного портландцемента должна быть 2000-3000 см2/г, у быстротвердеющего – 3500-5000 см2/г.
По ГОСТу сроки схватывания при температуре 20°С от момента затворения портландцемента должны быть следующими: начало – не ранее 45 мин, конец – не позднее 10 ч. Если цемент затворять горячей водой (более 40°С), схватывание значительно ускоряется.
Прочность портландцемента характеризуется маркой, которую определяют по пределу прочности при сжатии и изгибе образцов-балочек размером 40х40х160 мм, изготовленных из цементно-песчаного раствора состава 1:3 по массе при водоцементном отношении В/Ц = 0,4 и твердевших 28 сут в нормальных условиях (первые сутки в формах на воздухе и 27 сут в воде комнатной температуры). Портландцемент выпускают марок 400, 500, 550 и 600.
Твердение портландцемента сопровождается выделением теплоты. При использовании портландцемента для приготовления бетона смесь может разогреться до температуры 80°С, что приведет к образованию трещин в конструкции. Для предотвращения растрескивания забетонированную поверхность в жаркую и солнечную погоду накрывают влажными опилками или периодически поливают водой.
При твердении цементное тесто изменяется в объеме: усадка на воздухе – около 0,5-1 мм/м, в воде набухает до 0,5 мм/м. Изменение объема при твердении должно быть равномерным, что контролируют на лепешках из цементного теста – они не должны растрескиваться после твердения на воздухе в течение 24 ч и пропаривания в течение 3 ч.
Портландцемент с минеральными добавками получают, измельчая портландцементный клинкер, минеральные добавки и гипс. В качестве добавок вводят доменные гранулированные шлаки не более 20 % от массы цемента и 25 % активных минеральных добавок осадочного происхождения. Допускается вводить при помоле цемента пластифицирующие поверхностно-активные добавки не более 0,3 % от массы цемента. При помоле пластифицирующие добавки тончайшим слоем покрывают зерна цемента. Схватывание цемента протекает несколько медленнее. В ранние сроки твердения замедляется набор прочности. Выпускают портландцемент с минеральными добавками марок 400, 500, 550 и 600.
Быстротвердеющий портландцемент – это портландцемент с минеральными добавками, отличающимися повышенной прочностью через 3 сут твердения. Выпускают марок 400 и 500.
Шлакопортландцемент изготовляют путем совместного помола портландцементного клинкера с гранулированными доменными шлаками и гипсом. Выпускают марок 300, 400 и 500.
Быстротвердеющий шлакопортландцемент отличается повышенной прочностью через 3 сут твердения. Выпускают марки 400.
Глиноземистый цемент получают путем помола сплава, реже клинкера, полученного из сырья, состоящего из известняка и пород, богатых глиноземом (бокситами, состоящими в основном из гидрата оксида алюминия). Твердение глиноземистого цемента сопровождается интенсивным выделением теплоты. При этом 75-80 % всей выделяющейся при твердении теплоты приходится на первые сутки, что в 3-4 раза больше, чем за этот же период у портландцемента высоких марок. Выпускают марок 400, 500, 600.
Гипсоглиноземистый расширяющийся цемент получают путем смешивания тонкоизмельченных высокоглиноземистых доменных шлаков и природного двуводного гипса. Начало схватывания не ранее 10 мин, конец не позднее 4 ч от начала затворения. Предел прочности при сжатии образцов через 3 сут твердения должен быть не менее 28 МПа.
Белый портландцемент получают измельчением белого маложелезистого клинкера, минеральных добавок и гипса. Выпускают двух видов: белый портландцемент и белый портландцемент с минеральными добавками. Выпускают марок 400 и 500 с пределом прочности при сжатии соответственно 40 и 50, при изгибе 5,5 и 6 МПа. По степени белизны, которую определяют коэффициентом отражения в процентах абсолютной шкалы, белые портландцементы подразделяют на три сорта: первый – 80, второй – 75 и третий 68 %. Начало схватывания белого портландцемента должно наступать не ранее чем через 45 мин, конец схватывания не позднее чем через 12 ч после затворения. Тонкость помола белого портландцемента должна быть такой, чтобы при просеивании сквозь сито с сеткой N 008 проходило не менее 88 % массы пробы.
Цветной портландцемент изготовляют совместным тонким измельчением белого и цветного портландцементного клинкера, минеральных и органических красителей, гипса и минеральной добавки. Применяют для изготовления цветных бетонов и растворов, отделочных смесей и цементных красок. Выпускают красного, желтого, зеленого, голубого, коричневого и черного цветов марок 300, 400 и 500 с пределом прочности соответственно при изгибе 4,5; 5,5 и 6, при сжатии – 30, 40 и 50 МПа. Начало схватывания цемента должно наступать не ранее 45 мин, конец – не позднее 12 ч от начала затворения.
Тонкость помола цемента должна быть такой, чтобы при просеивании пробы сквозь сито с сеткой N 008 проходило не менее 90 % массы просеиваемой пробы.
Сульфатостойкие цементы выпускают четырех видов: сульфатостойкий портландцемент, сульфатостойкий портландцемент с минеральными добавками, сульфатостойкий шлакопортландцемент, пуццолановый портландцемент. При затворении и последующем твердении они образуют цементный камень, устойчивый к агрессивному действию сульфатной среды (например, морской воды). Марки сульфатостойких цементов – 300, 400 и 500.
Сульфатостойкий портландцемент получают измельчением портландцементного клинкера и гипса, добавляемого для регулирования сроков схватывания. В этом цементе не допускается наличие добавок.
Сульфатостойкий портландцемент – с активными минеральными добавками и гипсом.
В состав сульфатостойкого шлакопортландцемента вводят шлак (не менее 21-60 % от массы цемента) и гипс.
Пуццолановый портландцемент получают измельчением портландцементного клинкера и активных минеральных добавок осадочного происхождения (не менее 20-30 % от массы цемента). Пуццолановый портландцемент интенсивно набирает прочность только при твердении во влажных условиях или в воде, а также при тепловлажностной обработке (пропаривании). Пуццолановый портландцемент более водонепроницаем чем портландцемент, отличается пониженной морозостойкостью. Начало схватывания должно наступать не ранее 45 мин, а конец – не позднее 10 ч от начала затворения. Тонкость помола цемента должна быть такой, чтобы при просеивании через сито N 008 проходило не менее 85 % массы пробы.
Хранят цемент без упаковки в инвентарных металлических емкостях (силосах и бункерах) раздельно по видам и маркам, цемент в упаковке – в крытых сухих помещениях. Активность цемента, за исключением гидрофобных, при длительном хранении снижается примерно на 5 % в месяц.
Заполнители и добавки
Растворные и бетонные смеси приготовляют из вяжущего, воды и заполнителя (70-85 % от массы смеси). Вяжущие после затворения водой обволакивают частицы заполнителя и придают растворной или бетонной смеси подвижность. Заполнители, снижая расход вяжущих, уменьшают усадку растворов и бетонов при твердении.
Заполнители подразделяют на мелкие (песок) и крупные (гравий и щебень).
Пески характеризуются зерновым составом (крупный, средний, мелкий, очень мелкий) и модулем крупности.
Песок для строительных работ с размером зерен 0,14-5 мм применяют в растворах и бетонах. Количество пылевидных, глинистых и илистых частиц в песке не должно превышать 3 % по массе, в том числе глины не более 0,5 % по массе. В песке не должно быть засоряющих примесей.
Для приготовления растворов используют песок с модулем крупности менее 1,5, для приготовления бетона – крупные или средние пески не ниже модуля 2. Если пески не отвечают этому требованию, то их обогащают, т. е. создают необходимое соотношение фракций. Для легкого бетона используют пески из керамзита, шунгизита, пемзы, аглопорита и др.
Гравий для строительных работ бывает горным (овражным), речным и морским. Речной и морской гравий чище овражного, но имеет шлифованную поверхность, что ухудшает его сцепление с вяжущими веществами.
Щебень из природного камня для строительных работ – смесь, получаемая после дробления кусков горных пород или искусственных камней. Щебень имеет остроугольную форму и шероховатую поверхность, благодаря чему его сцепление с вяжущими более прочно, чем у гравия. В щебне меньше или отсутствуют органические примеси и пылевидные частицы, поэтому он является хорошим заполнителем для бетонов.
Качество крупного заполнителя (гравия и щебня) характеризуется крупностью и формой зерен, содержанием вредных примесей, прочностью и морозостойкостью.
Для бетонов используют следующие виды крупного заполнителя: щебень из природных каменных материалов, гравий и щебень из гравия, щебень из доменного шлака и из других побочных продуктов промышленности. Технические требования к заполнителю для тяжелых бетонов (кроме гидротехнического, дорожного и особо тяжелого) определены ГОСТом. Применяют следующие фракции крупного заполнителя: 5-10 (3-10), 10-20, 20-40 и 40-70 мм. В каждой фракции содержатся зерна промежуточных размеров. Размер крупного заполнителя не должен превышать 1/3 толщины ребра бетонируемой конструкции. Прочность заполнителей влияет на класс прочности бетона.
По морозостойкости гравий и щебень делят на марки Мрз 15, 25, 100, 150, 200 и 300.
Количество пылевидных, илистых и глинистых частиц в щебне, гравии и щебне из гравия определяют отмучиванием. Органические примеси снижают качество крупного заполнителя, поэтому их содержание устанавливают, как и для песка, калориметрическим методом.
Пористые неорганические заполнители для легких бетонов – природные или искусственные материалы с насыпной плотностью до 1000 кг/м3. Фракции пористых заполнителей 5-10, 10-20 и 20-40 мм.
Различают следующие марки пористых заполнителей по прочности: 25, 35, 50, 75, 100, 125, 150, 200, 250, 300 и 350.
В состав бетонов и растворов для улучшения их свойств (подвижности, удобоукладываемости, скорости твердения) вводят технические добавки. Введением добавок снижают расход вяжущих до 10-15 %, улучшают технологические свойства растворных и бетонных смесей (удобоукладываемость, однородность, нерасслаиваемость), регулируют степень подвижности бетонной смеси (скорость схватывания, твердения, тепловыделения), сокращают продолжительность тепловлажностной обработки до 40 %, ускоряют сроки загружения монолитных конструкций, повышают морозостойкость бетона в 2-3 раза, увеличивают стойкость бетона и железобетона к воздействию агрессивной среды.
При работе с добавками, особенно с нитритом натрия, необходимо строго соблюдать правила безопасности труда. Рабочие, имеющие повреждения кожи рук и лица, а также моложе 18 лет к этим работам не допускаются.
Различают пластификаторы, суперпластификаторы, воздухововлекающе-пластифицирующие, пластифицирующее-воздухоотвлекающие, гидрофобизирующие, газообразующие гидрофобизирующие и противоморозные добавки.
Пластификаторы увеличивают подвижность растворной и бетонной смесей, воздухоотвлекающие повышают морозостойкость, гидрофобизирующие повышают водостойкость и плотность, газообразующие повышают морозостойкость в агрессивных средах, противоморозные добавки обеспечивают твердение при отрицательных температурах. Комплексные добавки служат для придания подвижности, экономии цемента, обеспечения твердения при минусовых температурах.
Прочность раствора или бетона зависит от количества введенных добавок и водоцементного отношения. Наиболее распространен суперпластификатор С-3 – "разжижитель С-3" и НККС 40-03, а также суперпластифицирующие добавки на основе модифицированных лигносульфонатов: ЛТМ, МТС и др.