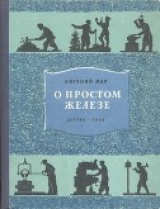
Текст книги "О простом железе"
Автор книги: Евгений Мар
сообщить о нарушении
Текущая страница: 3 (всего у книги 4 страниц)
Он теперь долго и верно будет служить человеку.
Бывает, во время плавки случается непредвиденное.
Грозная огненная стихия бушует внутри домны. Многие опасности подстерегают мастера: он может снизить температуру и «заморозить» металл, тогда-то и образуется «козел» – застывшая масса чугуна; мастер может передержать металл и не заметить, как он поднимется выше дозволенной отметки.
Вот почему плавка порой напоминает битву, исход которой до конца еще неизвестен.
Но вот один из чугуновозов уже везет чугун к конвейерной разливочной машине.
Пойдем же скорей «по следам» этого металла.
Ковш уже стоит у разливочной машины. Медленно движется ее стальная лента с ячейками-формами. Сюда-то и направляется из ковша жидкий чугун.
Чтобы металл быстрее остывал, в ячейках разливочной машины его поливают водой. Остуженные потоками воды слитки чугуна – чушки все одинакового размера и веса – опрокидываются на доставленную сюда же, в цех, железнодорожную платформу. Они как бы сами сходят на нее.
Металл готов. Поезд доставит его для переработки на другие заводы страны.
Но если мы пойдем по пути чугуновоза, принявшего металл из второй домны, то можем оказаться в соседнем с доменным – мартеновском цехе.
Этот чугун пойдет в переплавку. Он получит здесь вторую огненную очистку.
Рабочие мартеновского цеха должны изготовить из него отличную сталь.
Если ты вместе с товарищами задумаешь создать в школе небольшой музей металла, то первым экспонатом его должен стать, конечно, кусок железной руды. Рядом с ним займут свое законное место чугунок, утюг, чугунная деталь машины.
Образец стали, которая была получена из чугуна, ты сумеешь добыть, не выходя из класса. Им может стать перышко или даже стальная скрепка от старой тетрадки – скромные, но достойные представители многих известных тебе стальных вещей.
Как варят сталь
Сталь. Стальной…
Прочтешь эти слова – и сразу поймешь, что дело идет о металле большой прочности.
Мост легко выдерживает груз сотен автомашин, тяжесть целого железнодорожного состава. Этот мост сделан из стали. Самолет, который летит с огромной скоростью, легко преодолевая сильное сопротивление воздуха, тоже стальной. Стальной вал – деталь электродвигателя – совершает десять-пятнадцать тысяч оборотов в минуту. Посмотришь на него – все сливается перед глазами. А сталь выдерживает и такую нагрузку.
Для исследования морского дна строят стальной шар. Он опускается на глубину в несколько километров. Сверху на него давит огромный пласт воды. Казалось, такое давление может превратить шар в лепешку. Но ученые спокойно трудятся в своем круглом подводном домике – ведь и он изготовлен из стали.
В порту идет разгрузка большого парохода. Вот подъемный кран перенес на своем стальном крюке автомобиль, трактор или даже паровоз. Матросы, грузчики на пароходе и в порту знают: стальной крюк не подведет – он сделан из прочного металла.
Листы бронированной стали всегда служили нашим танкистам и артиллеристам верной защитой в бою.
Стальной броне не страшны ни пули, ни снаряды.
Но каким образом такой сверхпрочный металл получился из чугуна, который и удара молотка не выдержит?
Ответ на этот вопрос мы получили в лаборатории металлургического завода. Здесь быстро исследуют для нас кусочек чугуна и точно такой же кусочек стали.
По своему составу оба металла, оказывается, очень схожи. Основу и чугуна и стали составляет железо. Но в кусочках чугуна и стали обнаружены частицы и некоторых других веществ. Они хотя и составляют ничтожные доли, но все же определяют многое. Это, прежде всего, углерод. Он попал в чугун из кокса во время плавки в домне. Это также сера и фосфор. Они были в железной руде и еще остались в небольшом количестве и в нашем металле.
В чугуне различных примесей больше, чем в стали. Этим и объясняется, между прочим, его хрупкость; сталь чище.

Для того чтобы превратить чугун в сталь, надо освободить его от излишка углерода и других примесей, вроде фосфора и серы. Чугун только тогда станет сталью и получит ее чудесную силу, когда переплавится в новой, уже сталеплавильной печи.
Древние кузнецы, когда впервые выплавили, по их мнению, негодный «свиной металл», никак не могли объяснить свою неудачу: ведь в маленькой домнице они получали отличную сталь, которой были довольны самые требовательные заказчики.
А произошло все это потому, что угля и железа стало в большой домнице куда больше, температура выше, чем в маленькой. Плавка стала продолжаться дольше. Уголь начал действовать на металл – щедро насыщать его углеродом. Долгое время кузнецам приходилось выжигать углерод из чугуна в особых горнах и таким сложным и медленным способом получать сталь.
Чугунную чушку они обычно со всех сторон обкладывали раскаленным углем. Подручный кузнеца приводил в действие мехи – и жидкий чугун обдувался сильным потоком ветра. Пламя разгоралось. На самом дне горна образовывался ком мягкого, ковкого металла. Теперь-то кузнец брался за молот и с силой ударял по железному кому, выбивая из него куски шлака.
Это был очень медленный способ. Многое ли мог сделать кузнец с его ручным молотом и маленьким горном?
Люди долгие годы бились над тем, чтобы найти новые, более совершенные способы получения стали из чугуна. Ведь спрос на сталь с каждым годом рос. Но для этого надо было построить печь, которая была бы куда жарче домны. Началась настоящая погоня за градусами – вернее, за новыми сотнями градусов тепла.
Строились самые различные сталеплавильные печи.
Одна из них существует и сейчас. Она называется по имени своего изобретателя – конвертером Бессемера. После того как в него наливают из ковша жидкий чугун, проходит всего около пятнадцати минут – за это время и суп на плите не успевает свариться, – а сталь готова.

Конвертер Бессемера. Показан его внешний вид. Плавка стали продолжается здесь всего около пятнадцати минут. За это время и суп на плите не поспеет.
Кроме того, Бессемер так устроил свой конвертер, что он автоматически наклоняется, и из него можно легко вылить сталь.
Но вот беда: оказывается, в таком конвертере можно варить сталь лишь немногих и притом низких сортов. Куда лучше электроплавильные печи, чудесное изобретение замечательного русского ученого – профессора Петрова. Профессор Петров разработал проект такой печи еще в начале XIX века. Электропечи, значительно усовершенствованные, с той поры широко используются во всем мире.
Сталь получается в этих печах самого высокого качества, очищенная от многих вредных примесей.

Внешний вид современной электропечи. Здесь выплавляется высококачественная сталь.
Однако и электрическую печь не везде можно применить: она требует очень много электроэнергии и в электропечах варят только высшие сорта стали.
Больше всего стали самых разных сортов дают промышленности существующие повсюду мартеновские печи.
Первые мартеновские печи были построены во второй половине XIX века. Они работают на газе или на жидком топливе – мазуте – отходе нефти, который остается после изготовления из нее бензина и керосина.

В мартеновском, как и в доменном, цехе многие тяжелые работы по завалке печей сейчас выполняют машины. Завалочная машина ловко, словно кастрюли ухватом, подхватывает короба с рудой, металлическим ломом, известняком и сует по очереди в печь. Она сама их опрокидывает и уже пустыми возвращает обратно.
Следит за работой мартеновской печи сталевар. Он здесь первый человек, как и мастер у домны.
Чтобы суметь изготовить отличную сталь, необходимы большие знания и опыт. Имена лучших сталеваров, как и имена лучших доменщиков, известны всей стране. Многие из них награждены орденами и медалями, удостоены Сталинской премии.

Внешний вид и чертеж внутреннего устройства мартеновской печи. По каналам 1, 2 подаются в печь нагретый воздух и газ.
Сталевар то и дело поглядывает в оконце мартеновской печи, следит за ходом плавки. Пламя там такое яркое, что невооруженным глазом и глядеть больно. Но к кепке сталевара прикреплены синие очки. Он смотрит через них и, словно в уменьшительные стекла бинокля, видит огненное море. На его поверхности то и дело вздымаются вверх какие-то фонтанчики.
Это кипит сталь. Непосвященному такая картина мало что скажет, а сталевар быстро определит по цвету пламени, по величине искры, как идет плавка стали, скоро ли поспеет металл.
Было время, когда и за ходом плавки в мартеновской печи наблюдали только вот так, поглядывая на пламя через синие очки.
Теперь сталевару, как и мастеру домны, следить за варкой стали помогает наука.

В мартеновском цеху.
В его распоряжении – установленные на мартене многочисленные контрольные приборы. Кроме того, сталевар постоянно связан с находящейся здесь же, в цехе, экспресс-лабораторией. Она называется так потому, что делает анализы стали с необыкновенной быстротой.
…Вот пришло время, и подручный сталевара длинной металлической ложкой зачерпывает в печи немного жидкой стали. Через минуту проба уже в лаборатории. А пройдет еще несколько минут – и лаборант скажет точно, сколько оказалось в стали углерода, серы, марганца, фосфора… Сталевар будет знать, как ему действовать дальше, какую температуру держать, чего добавить в печь.
Сталевару каждая минута дорога. Раньше плавка стали длилась по десяти часов и даже больше. А советские сталевары-скоростники успевают иногда выдать плавку за шесть часов: страна получает сотни тонн металла дополнительно.

…Лаборатория дала последний анализ. Его тут же заносят в плавильный журнал. Металл готов.
Диспетчер по радио дает команду сталевару выпустить сталь. Все приходит в движение.
С помощью мощных кранов к печи подали вместительные ковши. Отверстие для стока стали открыто.
Сталь устремилась по длинному желобу прямо в ковш, и весь цех словно осветился заревом.
Стоят наготове металлические формы – изложницы. Сюда пойдет из ковша жидкий металл.
Наступает горячая пора для рабочих, занятых разливкой стали. Медленно движется ковш над изложницами, наполняя их жидким металлом.

Медленно движется ковш над изложницами.
Ковш ушел, а над каждой изложницей еще долго горит пламя, словно факел.
Уже не один мощный, подобный зареву, отсвет, а десятки веселых огней освещают теперь цех. Пока сталь, разлитая по изложницам, еще не успела затвердеть, рабочий быстро вставляет в каждую изложницу небольшие металлические ушки. На них обозначен номер плавки и марка, или сорт, стали.
Номер плавки и марку стали можно будет увидеть и на стальной балке и на станине станка, которые будут изготовлены из этого металла.
Номер будет жить теперь со стальным изделием, станет как бы его вторым именем.
Если изделия из стали будут служить хорошо, заказчики поблагодарят сталеваров, сваривших отличную сталь, и попросят в следующий раз изготовить точно такую же. Если сталь окажется плохого качества, нетрудно будет установить, кто и где совершил ошибку, чтобы не повторить ее более.
Когда остынет сталь, ушки с номером плавки накрепко приварятся к каждому слитку. Кран вытащит слитки за эти самые ушки из изложниц и аккуратно уложит вдоль литейной канавы. Затем придет паровоз и отвезет слитки в прокатные цехи. Там-то и изготовят из стальных слитков листы кровельного железа, строительные балки, железнодорожные рельсы, проволоку и многие другие вещи.
Вот как это произойдет.
Огонь и сила
Для того чтобы стальной слиток весом в несколько тонн превратить в мягкие и гибкие листы кровельного железа, или в прочные железнодорожные рельсы, или в километры тонкой проволоки, надо прежде всего раскалить этот слиток. Огонь сделает сталь мягкой, податливой.
Помните, как обрадовался первый кузнец древности своей победе над диковинным камнем, таким послушным в огне костра.
Все кузнецы обязательно кладут полосу металла в огонь. Так было в старину, так делается и теперь, когда металл куют уже не ручным, а механическим молотом.
«Куй железо, пока горячо», – говорит старая мудрая пословица.
Жар огня и сила удара – вот что позволяет кузнецу отковать из слитка стали все, что ему нужно.
И в прокатных цехах металлургического завода, куда были доставлены из мартеновского цеха стальные слитки, огонь и сила сделают свое дело.
Стальной слиток начнет свое путешествие из нагревательной печи, куда его положат, пока он не нагреется докрасна. Затем сталь направят на первый и самый крупный из прокатных станов – блюминг.
Блюминг должен превратить большой, многотонный слиток в квадратные заготовки, из которых другие прокатные станы, поменьше, изготовят листы, рельсы, стальные балки для строек.
Блюминг является самой большой машиной из всех существующих на свете, да и к тому же, пожалуй, самой сильной. Это машина-великан. Ее вес – шесть с половиной тысяч тонн. В разобранном виде блюминг занимает четыре железнодорожных состава. Так и везут его на завод, где должны установить. Эта гигантская машина потребляет такое количество электрической энергии, что ее хватило бы на освещение поселка, где живет несколько тысяч человек.

Зато машина-гигант многое умеет делать. Она сама подкатывает слиток к огромным валам, которые его сразу же крепко схватывают. Валы блюминга обжимают слиток со всех сторон, придают ему квадратную форму. А работой блюминга руководит всего-навсего один оператор, который обязан следить за его многочисленными механизмами. Здесь и тележка-опрокидыватель, подающая раскаленный слиток, и поворотное устройство, и огромные ножницы, которые, когда режут металл, давят на него с силой в сотни тонн. В год такой блюминг успевает прокатать несколько миллионов тонн металла.
Но это только первый из многочисленных прокатных станов, стоящий на пути стали, а их много в цехе, широком и длинном, как улица.
Ты, наверно, видел когда-нибудь, как домашние хозяйки ловко раскатывают тесто самыми обыкновенными деревянными скалками. Был большой ком, а превратился в тонкий листик. Собственно говоря, нечто похожее проделывает и наш прокатный стан. Только скалки-валки вертятся на месте, а раскаленный металл по многу раз прогоняется между ними взад и вперед. Машина-силач удивительно легко поворачивает тяжелые слитки – вновь и вновь пропускает их между валами, пока они не примут нужных размеров.

Раскаленный металл проходит между верхним и нижним валами прокатного стана.
Удивительное дело: в прокатном цехе даже пол работает!
Крутятся вставленные в пол ролики и подталкивают заготовку от большого стана к стану с валками меньшего размера. Так стальная заготовка, проходя через многие прокатные станы, становится все тоньше и тоньше. Иной слиток на своем длинном пути похудеет в шестьдесят, а то и в сто раз, зато вытянется, будто вырастет.
Металл, перед тем как его отправить на очередной прокатный стан, вновь раскаляют в нагревательных печах.
Сталь остывает постепенно и все время меняет свой цвет: становится то яркожелтой, то багрово-красной, то синей.
Красивое это зрелище!
В домнах всё скрывают от человеческого глаза толстые стены из огнеупорного кирпича. За плавкой металла можно наблюдать там лишь через небольшое окошечко – глазок. А в прокатном цехе металлургического завода картина превращения металла в изделие раскрывается перед тобой во всех подробностях.
Сталь проходит через разные прокатные станы. Один выпускает готовое кровельное железо – хоть сейчас крой им крыши. Другой прокатывает узенькие стальные полоски. Из третьего стана выходят железнодорожные рельсы.
А вот еще один необычный прокатный стан. Он выпускает толстую стальную проволоку – катанку. Проволока извивается, словно огненная змея. Она долго остывает на открытом воздухе близ цеха, свернутая в большие круги.
Каким же образом стальная заготовка становится рельсом, строительной балкой или вот такой проволокой-катанкой?
Оказывается, в валках каждого прокатного стана имеются особые углубления. Одни точно повторяют форму и размеры железнодорожного рельса, другие – строительной балки, третьи – узкой стальной ленты.
Попадает в такое углубление мягкая раскаленная заготовка, уже прошедшая через несколько станов и ставшая квадратной или круглой, по нескольку раз прокатывается между валами и сама становится рельсом, балкой, узкой стальной лентой или толстой проволокой.
Для того чтобы затем превратиться в трубу, лента-заготовка должна пройти еще немалый путь. Ее будут обрабатывать различные станки: один размотает ленту, второй выпрямит ее, третий крепко приварит одну ленту к другой, четвертый свернет узенькую, но длинную теперь ленту в трубу, пятый ловко сварит каждый поворот ленты так, чтобы не было между ними просвета. Вот и вышла готовая стальная труба!

В прокатном цехе много механизмов.
Один из них рубит прокатанную сталь на ровные стальные пластины – сутунки, на других – заготовки распиливаются механической пилой, на третьих – у заготовок обрезают неровные края. Прежде чем направить для дальнейшей обработки, заготовки тщательно очищают.
Прокатный цех так же, как доменный и мартеновский, называют горячим цехом. Пышут жаром нагревательные печи, валки, полосы раскаленной стали. Вокруг летят искры. А рабочие прокатного цеха спокойно делают свое дело. Водяная завеса ограждает прокатчика от раскаленного слитка. У каждого рабочего места установлены мощные вентиляторы, распыляющие воду. Этот искусственный дождик из мельчайшей водяной пыли удивительно освежает.
А на некоторых наших металлургических заводах работают установки, подающие в горячие цехи искусственно охлажденный воздух.
От искр прокатчиков надежно защищают металлические сетки, похожие на стальные забрала. Ими воины в старину прикрывали лицо в бою. И на ногах у прокатчиков специальная обувь, предохраняющая от огня.
Рабочие прокатных цехов очень любят свою профессию, требующую много знаний, смекалки, сноровки. Нелегко иметь дело с раскаленным металлом, но зато какое удовлетворение получаешь, когда видишь, как металл покорился тебе и из стального слитка вышло готовое изделие, которое уже ждут на других заводах и стройках!
Прокатчики встречаются со своими изделиями буквально повсюду.
Вот мчится по асфальтированному шоссе новенький автомобиль: кузов его сделан из стальных листов, побывавших в прокатном цехе металлургического завода.
Перед тем как выпустить автомобиль, его подвергли различным испытаниям. Много часов простояла машина в особой камере под искусственным дождем: сталь выдержала, не подвела. Прокатчик может этим гордиться. А доведется ему сесть в дальний поезд – он и там увидит плоды своего труда: и поезд и рельсы сделаны из прокатанной стали.
У нас много прославленных прокатчиков, которых знает народ.
Мастер прокатного стана Московского металлургического завода «Серп и молот» Иван Ильич Туртанов принимал участие еще в строительстве того цеха, где сейчас трудится. Туртанов поступил на завод чернорабочим, а после того как новый прокатный цех был построен, попросил направить его работать на стан.
Сменил Иван Ильич много специальностей: был резальщиком металла, крючочником – направлял и подталкивал крюком раскаленный металл, был вальцовщиком, помощником мастера, стал мастером, начальником прокатного стана. Его прокатный стан – один из лучших в стране.
За многолетнюю и безупречную работу на заводе Туртанов награжден орденом Ленина.
На больших металлургических заводах существует несколько прокатных цехов. В одних прокатывают листовое железо, в других – стальную ленту. Из стальной ленты уже на других заводах делают вещи, которые ты встречаешь повсюду: ложки, ножи, твое школьное перышко.
А в сталепроволочном цехе из толстой проволоки – катанки – изготовляется проволока самой различной толщины, в том числе и та, которую рубят затем на гвозди, и та, из которой плетутся морские канаты необыкновенной прочности.
Проволока не прокатывается между валами. Она протягивается, волочится на волочильных станах.
В каждом таком стане есть отверстие – глазок, – через которое и пропускается катанка. Оно чуть уже, чем сама катанка. Когда проволоку с силой тянут через такой глазок, она становится тоньше и в то же время длиннее: волочится, вытягивается.
Волочильные станы следуют на пути катанки один за другим, словно прокатные станы на пути стальной заготовки. И глазки этих станов всякий раз становятся все меньше и меньше, а проволока выходит все тоньше и тоньше, пока, пройдя последний стан, не достигнет нужного размера.

Перед волочением проволока, чтобы уменьшить трение, тщательно смазывается.
Уже готовая, она сматывается в круги, упаковываемся и отправляется по назначению.
На деревянной дощечке, привязанной к проволоке, написан адрес заказчика.

Посмотри на этот рисунок – и ты лучше поймешь, как толстая катанка превращается в тонкую проволоку. Слева – волочильный стан. На чертеже справа показана его работа: толстая катанка (1) протягивается через узкий глазок стана и делается тоньше (2, 3).
Но и проволока выпускается самая различная.
В сталепроволочном цехе можно увидеть, например, необыкновенную проволоку, у которой сердцевина стальная, а оболочка медная. Сталь придает ей прочность, а медь хорошо проводит электрический ток.
А вот проволока-пруток изготовляется из высококачественного металла и сверкает будто серебро. Пруток идет на машиностроительные заводы. Там из него изготовят велосипедные спицы, детали для часов или готовален, медицинские инструменты и многие другие предметы.
Перед нами лежит обычная продукция большого металлургического завода. Вот тщательно упакованные листы автомобильной стали. Из них будут построены кузова автомашин. Рядом – связки стального прутка, похожие на снопы, мотки проволоки, рельсы, балки, тяжелые стальные плиты.
Много изменений претерпел слиток после того, как его не раз пропустили через прокатные или волочильные станы. Сталь нагревалась, а затем охлаждалась. Валки многих станов сдавливали ее с огромной силой. Что же стало теперь с металлом?
Конечно, сталь уже не та, что была в начале своего пути, после выхода из мартеновской печи. Она изменилась.
Обрабатывая металл, прокатывая его, люди придали стали новые качества, какими она раньше и не обладала.

Самый большой прокатный стан – блуминг.
Сталь, из которой изготовят затем инструменты, должна быть твердой – ведь ею будут резать металл, а рессорная сталь, наоборот, – упругой.
Металл, из которого изготовляют клинки кавалерийских сабель, прочен и в то же время упруг. Хороший клинок перережет на лету тонкий волос и не искрошится от удара другого, такого же стального клинка.
Как же придаются металлу все эти удивительные качества?
Уже давно известно, что сталь, нагретая до определенной температуры и охлажденная, становится прочной, закаляется.
Мастера древнего Востока отлично знали тайны воздействия на сталь и огнем и холодом. Там существовали многочисленные способы закалки стали.
Иногда, например, кузнец вынимал клинок из горящего горна, садился на коня и мчался с раскаленной саблей в руках до тех пор, пока ветер не остудит металла. И клинок после этого становился особенно прочным.
Но умерли мастера древнего Дамаска – города, который славился своей сталью на весь мир, – и с собой в могилу унесли секрет создания знаменитого дамасского булата.
Он был раскрыт лишь в середине XIX века в уральском городе Златоусте.
Честь его раскрытия принадлежит работавшему там русскому инженеру Павлу Петровичу Аносову.
Аносов исследовал сотни старинных сабельных клинков. В поисках тайны булатной стали он добавлял в плавку драгоценные металлы – золото и платину. Аносов проверял действие на металл слоновой кости, алмаза, сажи и наконец первым из ученых-металлургов обратился для изучения стали к микроскопу. С помощью микроскопа Аносов исследовал внутреннее строение стали. Так им были окончательно раскрыты секреты булата и создана Златоустовская сталь, ни в чем не уступающая дамасской.

Другому русскому ученому-металлургу, Дмитрию Константиновичу Чернову, умершему глубоким стариком в 1921 году, удалось установить, при какой температуре происходят различные изменения во внутреннем строении стали. После этого открытия, нагревая и охлаждая сталь до определенного градуса, люди стали придавать ей всякий раз различные свойства.
В наше время на каждом большом металлургическом заводе обязательно есть отлично оборудованные лаборатории с микроскопами и даже рентгеновскими аппаратами.
Сталь, изготавливаемая для каких-нибудь особенно ответственных деталей, например для лопаток гидротурбин, которые должны выдержать большую нагрузку, обязательно просматривается с помощью рентгеновских лучей, словно сердце и легкие человека.
Присоединенные к микроскопам фотоаппараты позволяют заснять строение металла.
Рабочие Московского металлургического завода «Серп и молот» называют свою центральную лабораторию «заводской академией наук». Эта великолепная лаборатория занимает шестьдесят комнат большого четырехэтажного здания. Здесь работают более двухсот инженеров-исследователей.
Вся жизнь стали – от ее рождения в мартене или электропечи до проката или литья – тщательно изучается работниками заводской лаборатории. Они проверяют качество всех подсобных материалов: например, мазута, которым топятся мартеновские печи, или бумаги, в которую пакуются изделия.
Кроме того, в лаборатории изготовляют новые сорта стали.
Это как бы маленький опытный завод, у печей и станов которого стоят пытливые исследователи.
В одном из отделов центральной лаборатории установлена небольшая электрическая печь. Ковш, в который выливается сваренная в этой опытной печи сталь, так мал, что его можно поднять руками. А возле этого маленького ковша, в котором проводятся опытные плавки, не раз часами стояли, волнуясь, и работники заводской лаборатории и многие прославленные ученые-металлурги.
Когда на «Серпе и молоте» впервые осваивалось производство стальных лент для радиоламп, пришлось произвести свыше шестисот различных опытов.
В нижнем этаже центральной лаборатории завода «Серп и молот» расположены испытательные мастерские. Там сталь испытывается на прочность, гибкость, упругость. Металл мнут, растягивают, подвергают ударам. На стальной канат подвешивают груз и придирчиво проверяют прочность каната.
Еще на заводе металл должен пройти самые серьезные испытания, подобные тем, с которыми ему придется встретиться, когда он станет частью станка, машины, фермой моста, железнодорожным рельсом или корабельным канатом.
Металл выдержит проверку и пойдет на службу людям.