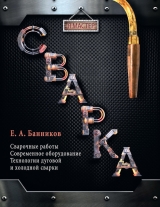
Текст книги "Сварка"
Автор книги: Евгений Банников
Жанры:
Хобби и ремесла
,сообщить о нарушении
Текущая страница: 6 (всего у книги 23 страниц) [доступный отрывок для чтения: 9 страниц]
• удельное усилие сжатия – Р (МПа);
• плотность тока – i (А/мм2);
• время протекания тока – t (с).
Шовная (роликовая) контактная электросварка
Шовная (роликовая) сварка – разновидность контактной сварки, при которой заготовки соединяют прочно-плотным сварным швом, состоящим из ряда точек, перекрывающих друг друга. Электроды имеют вид роликов (дисков) диаметром – 400 мм. Форму рабочей поверхности выбирают в зависимости от толщины, формы и материала свариваемых заготовок. Ролики для сварки делают из токопроводящих материалов, с высокой теплопроводностью, например из меди или специальных сплавов.
Схема шовной сварки изображена на рисунке 32.
В процессе шовной сварки (рис. 32) листовые заготовки 1 соединяют внахлестку, зажимают между роликами-электродами 2 и пропускают ток сварки от трансформатора 3. При движении роликов по заготовкам образуются перекрывающие друг друга точки, в результате чего образуется сплошной герметичный шов. Шовную сварку, так же как и точечную, можно получить при одностороннем и двухстороннем расположении электродов.
Циклограмма процесса шовной сварки бывает с прерывистым или с непрерывным включением тока.

Рис. 32.
Схема шовной сварки и разрез сварного шва:
1 – заготовки; 2 – ролики;
3 – сварочный трансформатор;
Р – усилие сжатия
Толщины свариваемых листов металла составляют – 0,3 мм. Шовной сваркой выполняют те же типы сварных соединений, что и точечной сваркой, но используют для получения герметичных швов.
Шовную сварку применяют в массовом производстве для изготовления различных сосудов, баков и т. п.
Диффузная сварка
Диффузией называется явление самопроизвольного проникновения и перемешивания частиц двух соприкасающихся газов, жидкостей или твердых тел. Происхождение слова от латинского diffusio означает распространение, растекание, рассеивание. С точки зрения физики это неравновесный процесс, вызываемый молекулярным тепловым движением и приводящий к установлению равновесного распределения концентраций внутри фаз. В результате диффузии происходит выравнивание химических потенциалов компонентов смеси.
Микроскопическая теория диффузии атомов, основанная на механизме перескоков атомов по вакансиям (свободным местам), была развита Я. И. Френкелем.
Замещение атомов кристаллической структуры вакансиями связано с возможностью перехода их через потенциальный барьер. Предполагается, что после перехода атома на свободное место (вакансию) он, благодаря сильному взаимодействию его с соседними атомами, успевает отдать часть энергии, прежде чем вернется на свое место.
Процесс диффузии в твердых телах может осуществляться несколькими способами:
• обмен местами атомов кристаллической структуры с ее вакансиями;
• перемещение атомов по междоузлиям;
• одновременное циклическое перемещение нескольких атомов;
• обмен местами двух соседних атомов.
При образовании твердых растворов замещения преобладает обмен местами атомов и вакансий. Диффузию принято выражать через коэффициент диффузии D:
D = a2/t × exp (—W/k × T),
где: D – коэффициент диффузии;
a – постоянная решетки;
t – время периода колебаний атомов решетки (t=10–13c)
W – энергия активации;
Т – температура.
Из формулы видно, что для твердых тел характерна экспоненциальная зависимость диффузии от температуры. Например, коэффициент диффузии для цинка в медь возрастает в 1014 раз при повышении температуры от 30 °C до 300 °C.
Все эти физические явления положены в основу диффузной сварки материалов и различных металлов и их сплавов. При диффузной сварке соединение образуется в результате взаимной диффузии (проникновения) атомов в поверхностных слоях контактируемых материалов, находящихся в твердом состоянии.
Температура нагрева при сварке несколько выше или ниже 0,5–0,9 Тплавл) температуры рекристаллизации более легкоплавкого материала. Процесс сварки в большинстве случаев выполняют в вакууме, примерно (1,33 × (10–2–10–5) Па. Однако возможна и сварка в атмосфере инертных защитных или восстановительных газов.
Защитная среда способствует удалению пленок поверхностных окислов. В вакууме происходит их разложение (диссоциация) и испарение или восстановление окисных пленок до основного металла в среде восстановительного газа.
На рисунке 33 изображена принципиальная схема диффузной сварки.
Процесс диффузной сварки выполняют следующим образом (рис. 33): свариваемые заготовки 4 центрируют в оправках 3, 6, устанавливают в рабочую камеру 2, в которой создают вакуум или заполняют ее защитным газом. После этого нагревают заготовки до температуры рекристаллизации более легкоплавкого материала и прикладывают давление с помощью, например пневмо, гидро– или механических устройств 1.
Давление создают порядка 1–20 МПа в течение 5–20 минут. После охлаждения деталей образуется сварное соединение. Нагрев осуществляют при помощи внешнего либо внутреннего нагревателя. Используют нагрев электрическим током, при помощи индуктора ТВЧ (токами высокой частоты), при помощи электронного луча в вакууме. Время выдержки зависит от свойств материала и его размеров.

Рис. 33.
Схема диффузной сварки:
1 – механизм создания давления; 2 – рабочая камера; 3, 6 – оправки; 4 – свариваемые детали; 5 – нагреватель
Основные технологические параметры диффузной сварки:• давление на свариваемые детали;
• температура нагрева заготовок;
• степень разрежения в вакуумной камере;
• время нагрева и время сжатия деталей.
Процесс сварки с помощью диффузного соединения условно разделяют на две стадии:• 1-я стадия – нагрев материала и приложение давления, что вызывает пластическое течение микровыступов, разрушение и удаление различных пленок на поверхностях контакта. Образуются многочисленные участки с непосредственной связью материалов;
• 2-я стадия – ликвидация микровыступов и образование объемной зоны соединения.
Оборудование для диффузной сварки:• вакуумная установка с системами для подъема и опускания камеры;
• системы для создания регулируемого давления на заготовки;
• устройства нагрева заготовок (индукторы ТВЧ, электроннолучевые нагреватели);
• системы управления установкой и контроля.
Преимущества диффузной сварки:• отсутствие загрязнений в соединении (нет припоев, флюсов, электродов);
• возможность соединений в различных сочетаниях металлов, сплавов, различных материалов независимо от их твердости, взаимного смачивания;
• возможность сваривать биметаллические, триметаллические и тетраметаллические детали;
• получение высокопрочных соединений без изменения физико-химических свойств свариваемых материалов;
• отсутствие какой-либо механической обработки после сварки;
• возможность соединений материалов различных толщин;
• высокая степень автоматизации процесса сварки;
• относительно низкие энергозатраты при высокой рентабельности сварки.
Недостатки диффузной сварки:• относительная сложность оборудования требует подготовки кадров.
Диффузную сварку широко применяют в ракетно-космической технике, в самолетостроении, приборостроении, пищевой и медицинской промышленностях и других отраслях. Этот способ применяют для сварки ответственных деталей турбин, при изготовлении металлокерамики, узлов вакуумных приборов, высокотемпературных нагревателей, при производстве инструмента и т. д.
Выпускаются установки диффузной сварки для единичного производства (с ручным управлением) и для серийного производства (с полуавтоматическим и автоматическим программным управлением).
Газопрессовая сварка
При газопрессовой сварке используют традиционный источник тепловой энергии, характерный для сварки плавлением, – газовое пламя. Одновременно с положительным воздействием нагрева и давления защитная атмосфера в зоне сварки интенсифицирует образование качественного соединения.
Схема газопрессовой сварки показана на рисунке 34.
При сварке газопрессовым способом детали 2, 4 фиксируют в зажимах 1, 5 и прогревают с поверхности стыка или с торца до температуры пластического состояния, а затем, прикладывая давление, обеспечивают образование сварного соединения. Регулируя состав газов, можно получать как окислительную, так и восстановительную атмосферу в газовом факеле. Этим можно оказывать определенное положительное воздействие на процесс образования сварочного соединения. Газопрессовая сварка достаточно широко применяется, например, при производстве электровакуумных приборов и в других сферах производства, благодаря простоте процесса сварки, доступности оборудования и низкой квалификации персонала.

Рис. 34.
Схема газопрессовой сварки:
а – положение деталей перед сваркой; б – положение деталей после сварки;
1, 5 – зажимы заготовок; 2, 4 – свариваемые изделия; 3 – горелка кольцевая
Дугопрессовая сварка
Дугопрессовая сварка используется для присоединения деталей типа шпилька к пластине или к массивной плите. В качестве электрода выступает сама деталь. Для получения теплоты используется энергия электрической сварочной дуги.
Схема процесса дугопрессовой сварки показана на рисунке 35.
При отводе детали 2 от пластины 3 включают электрическую цепь, при этом возбуждаемая электрическая дуга расплавляет материал шпильки и пластины. После этого отключают электрическую цепь и ударом шпильки о пластину производят соединение деталей.
Поверхностные окислы и загрязнения при этом выдавливаются из зоны сварки вместе с жидким металлом, и образуется соединение высокого качества. Для повышения качества соединения сварка может производиться в защитной среде, например в среде азота, углекислого газа.
Процесс дугопрессовой сварки может быть легко механизирован. При производстве дугопрессовой сварки используется аппаратура для обычной электродуговой сварки.
Дугопрессовую сварку можно применять при производстве строительных элементов, например для сварки арматурных стержней с закладными деталями.
Сварка аккумулированной энергией
Сущность процесса сварки аккумулированной энергией заключается в том, что кратковременные сварочные процессы осуществляются за счет энергии, запасенной в соответствующем приемнике, непрерывно заряжающем и периодически разряжающемся на свариваемые детали.
Существуют четыре разновидности сварки аккумулированной энергией:
• конденсаторная сварка;
• инерционная сварка;
• электромагнитная сварка;
• аккумуляторная сварка.
Накопление энергии соответственно происходит в конденсаторной батарее, во вращающихся частях генератора, в магнитном поле специального сварочного трансформатора и в аккумуляторной батарее.
Наиболее широкое промышленное применение получила конденсаторная сварка. Этот способ сварки по характеру протекания процессов близок к дугопрессовой сварке.
Энергия в конденсаторах накапливается при их зарядке от источника постоянного тока (генератора или выпрямителя). Затем в процессе разрядки запасенная энергия мгновенно подается в зону сварки. Накопленную в конденсаторе электрическую энергию можно регулировать, изменяя емкость конденсаторной батареи и напряжение ее зарядки.

Рис. 35.
Схема дугопрессовой сварки (стрелка показывает направление сжатия);
а – положение деталей перед сваркой; б – разогрев свариваемых кромок; в – соединение деталей. 1 – выключатель тока; 2 – шпилька (электрод); 3 – пластина; 4 – дуговой разряд
Энергию заряда конденсатора можно определить по формуле:
A = C × U2/2,
где А – энергия заряда (Дж);
С – емкость конденсатора (Ф);
U – напряжение зарядки конденсатора (В).
При конденсаторной сварке возможна точная регулировка и дозировка количества энергии зарядки, не зависящая от внешних условий, в частности от нестабильности питающей сети.
В настоящее время используются две схемы конденсаторной сварки (рис. 36):
• бестрансформаторная конденсаторная сварка;
• трансформаторная конденсаторная сварка.
В обеих схемах запасенная в виде емкостного заряда энергия разряжается за короткое время (10–3 –10–4 с) на электроды, сжимающие заготовки. Высокая плотность тока способствует мгновенному разогреву места сварки, что обеспечивает небольшую зону термического влияния при скоростном процессе.
При бестрансформаторной (рис. 36а) сварке концы обкладок конденсатора подключены непосредственно к свариваемым деталям 2, 3. При этом один из выводов жестко закреплен, а другой может перемещаться в направляющих. При освобождении защелки 6 под действием сжатой пружины 5 деталь быстро переместится по направлению к неподвижной заготовке. Перед соударением, в промежутке 1–3 мм, между деталями возникает мощный дуговой разряд энергии, накопленной в конденсаторе С. Этот искровой пробой, переходящий в дуговой разряд, успевает частично оплавить торцы обеих заготовок 2, 3, которые после соударения свариваются между собой под действием усилия осадки. При ударном сжатии деталей поверхностная прослойка жидкого металла вытесняется из зоны сварки, что способствует образованию качественного сварного соединения.
Способом бестрансформаторной конденсаторной сварки можно сваривать встык проволоку и тонкие стержни разной толщины из разнородных материалов: вольфрам-никель, медь-константан, молибден-никель и т. п.
Трансформаторная конденсаторная сварка (рис. 36б) отличается тем, что конденсатор разряжается на обмотку сварочного трансформатора Т2.
При этом способе сварки сжимают заготовки между электродами, заряжают конденсатор, который разряжают на первичную обмотку сварочного трансформатора. В результате во вторичной обмотке сварочного трансформатора индуцируется ток большой величины, с энергией, достаточной для сплавления деталей.

Рис. 36.
Схемы конденсаторной сварки:
а – бестрансформаторная конденсаторная сварка; б – трансформаторная конденсаторная сварка. Т1 – трансформатор повышающий; Т2 – трансформатор сварочный; С – конденсаторная батарея; В – выпрямитель переменного тока; П – переключатель; 1, 4 – электроды; 2, 3 – свариваемые заготовки; 5 – пружина; 6 – защелка
Преимущества конденсаторной сварки:• точная дозировка запасенной энергии;
• независимость от колебаний питающей сети;
• малое время протекания тока (10–3–10–4 с);
• небольшая зона термического влияния;
• низкая потребляемая мощность (0,2–2 кВА);
• высокая степень автоматизации процесса;
• возможность сваривать материалы малых толщин (до нескольких микрон).
Конденсаторная сварка широко применяется в производстве приборов для точной механики (авиационные, часовые, прецизионные), в производстве радиоэлементов и т. п.
Глава 4
Металлы и сплавы. Основные свойства и понятия
Сварщик работает с металлами и их сплавами. Для понимания процессов, происходящих при сварке, необходимо владеть основными понятиями, знать основные свойства металлов и сплавов.
Что такое металлы? Более 200 лет назад великий русский ученый М. В. Ломоносов (1711–1765) в своем знаменитом труде «Первые основания металлургии или рудных дел», написанном в 1763 году, дал металлам такое определение: «металлы суть ковкие светлые тела». Для того времени краткая формулировка была достаточно верной и точной. Ломоносов назвал шесть основных металлов: золото, серебро, медь, железо, свинец и олово.
Позже Мейер (1897) в своем энциклопедическом словаре дал уже расширенное определение металлам: «элементы, которые являются хорошими проводниками тепла и электричества, обладают характерным сильным блеском, непрозрачны (в не слишком тонком слое) и образуют с кислородом соединения преимущественно основного типа».
С развитием науки происходили открытия все новых элементов. Открытые элементы необходимо было классифицировать какими-то другими определениями.
К чему причислять новые элементы?
Выход из тупика нашел знаменитый русский ученый Д. И. Менделеев (1834–1907). Его таблица и периодическая система элементов получили всемирное признание. Одновременно с Д. И. Менделеевым и независимо от него подобную систему разработал немецкий химик Лотар Мейер (1830–1895). Права на открытия принадлежат обоим ученым. Однако Менделеев предсказал по своей таблице свойства еще не открытых элементов и определил их свойства теоретически. Это были элементы галлий и германий. В то время было известно 63 элемента, из них около 50 – металлы.
Дальнейшие исследования свойств металлов с помощью оптического микроскопа (увеличение до 1500 раз), а затем при помощи электронного микроскопа (увеличение 20–100 000 крат) позволили заглянуть внутрь металла.
Русский ученый П. П. Аносов в 1831 году впервые в мировой практике применил оптический микроскоп для исследования микроструктуры металлов, став основоположником изучения металлов методом микро– и макроанализа. Кроме того, он первым в мировой практике обратил внимание, что свойства стали зависят не только от ее химического состава, но и от структуры.
Исследование при помощи оптики показало строение металлов как кристаллических веществ. Электронная металлография позволила наблюдать дефекты в кристаллах в виде различных дислокаций-смещений, перестановок.
Итак, что нам сегодня известно о металлах?
Металлы обладают различными свойствами. Общими свойствами металлов является характер зависимости электропроводности от температуры. Свойства металлов объясняются их строением: распределением и характером движения электронов в атомах; расположением атомов, ионов и молекул в пространстве; размерами, формой и характером кристаллических образований.
Электронное строение металлов определяется периодической системой Д. И. Менделеева. В полном соответствии со сходством в электронном строении элементы одной группы имеют и сходные свойства.
К таким периодически изменяющимся свойствам металлов относятся: твердость, абсолютная температура плавления, средний коэффициент теплового расширения, атомный объем и др.
В природе металлы, за исключением золота, серебра, платины и меди, существуют в составе химических соединений – окислов, сульфатов и прочих, образующих руды. Из руды различными металлургическими способами извлекают металлы: дроблением руды, обогащением и сепарацией и далее выплавкой соответственно чугуна или слитков цветных металлов. Чугун используется собственно и как чугун, как материал для выплавки сталей.
Стальные слитки и слитки цветных металлов в дальнейшем перерабатываются для сортового проката в виде рельсов, балок, прутков, полос, листов, уголков, швеллеров, проволоки и т. п. Соответственно, выпуском чугуна и сталей занимается черная металлургия, а производством цветных металлов – цветная металлургия.
Технически чистые металлы характеризуются низкой прочностью и высокой пластичностью, поэтому в технике применяют различные металлические сплавы. Сплав – вещество, полученное сплавлением двух или более элементов.
Элементами сплавов могут быть металлы и неметаллы. Эти элементы называются компонентами сплава. В сплавах, кроме основных элементов, могут содержаться примеси. Примеси могут быть полезными, если они улучшают свойства сплава, или вредными, если они ухудшают свойства сплава. Примеси можно выделить как специальные, которые ввели в сплав для придания ему требуемых свойств, так и случайные, попавшие в сплав случайно при его приготовлении.
Сплавы делятся по следующим признакам:
• черные сплавы на основе железа – это стали и чугуны;
• легкие цветные сплавы с малой плотностью на основе алюминия, магния, титана, бериллия;
• тяжелые цветные сплавы с высокой плотностью на основе меди, свинца, олова и др.;
• легкоплавкие цветные сплавы на основе цинка, кадмия, олова, и др.;
• тугоплавкие цветные сплавы на основе молибдена, ниобия, циркония, вольфрама, ванадия и пр.
Кристаллическое строение металлов
Все металлы в твердом состоянии имеют кристаллическое строение. Атомы в твердом металле расположены упорядоченно и образуют кристаллические решетки. Расстояние между атомами называют параметрами кристаллической решетки и измеряют в нанометрах. Типы кристаллических решеток изображены на рисунке 37.
Свойства металлов таковы, что при повышении температуры или давления параметры решеток могут изменяться. Некоторые металлы в твердом состоянии при различных температурах изменяют строение своих кристаллических решеток, что всегда приводит к изменению физико-химических свойств металлов.
Существование одного и того же металла в нескольких кристаллических формах носит название аллотропии, или полиморфизма. Температура при этих фазовых превращениях называется критической, а перестройка кристаллических форм – полиморфными превращениями.
Основоположником изучения термических превращений в сталях (сплавах «железо-углерод») был русский ученый Д. К. Чернов. Им было открыто, что при нагреве твердой стали до определенных температур, зависящих от ее состава, в ней происходят внутренние превращения, приводящие к изменению свойств. Открытие Д. К. Чернова, получившее всемирное признание в 1868 году, показало связь между составом, строением и свойствами стали. Работы Чернова легли в основу учения о термообработке стали. Им были открыты дендритные кристаллы, критические точки термических превращений и теория литья стали и сплавов, изучены процессы кристаллизации слитков металла.

Рис. 37.
Кристаллические решетки металлов:
1 – объемно-центрированного куба (ОЦК); 2 – гранецентрированного куба (ГЦК);
3 – гексагональная плотно упакованная решетка (ГПР)