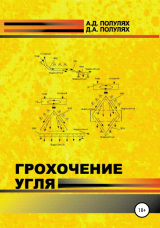
Текст книги "Грохочение угля"
Автор книги: Данил Полулях
сообщить о нарушении
Текущая страница: 3 (всего у книги 6 страниц)
Сыпучий материал, состоящий из смеси частиц разных размеров, можно рассматривать, как некоторый статистический коллектив. Средний диаметр смеси частиц, как и всякое среднее, определяется по правилам математической статистики. Средний аргумент x, по рассматриваемому определяющему свойству, коллектива S называют одинаковое для всех членов коллектива значение аргумента x, которое им можно придать, не изменяя определяющего свойства коллектива.
Для отображения определяющего свойства в среднем диаметре необходимо, чтобы усредненный коллектив со средней величиной аргумента x=D1,D2…Dn в отношении этого свойства ничем не отличался от эмпирического x=d1,d2…dn. Если точно установлено определяющее свойство, которое необходимо сохранить при усреднении, то принципиально задача определения среднего диаметра частиц решается просто: выбранное определяющее свойство выражают функцией f(d) переменного от класса к классу диаметра частиц d и той же функцией f(D) искомого среднего диаметра частиц D, который является величиной, постоянной для всех классов.
Определяющее свойство при усреднении должно остаться неизменным, следовательно,

Решая это исходное уравнение относительно D, получаем надлежащую для данного конкретного случая формулу исчисления среднего диаметра.
Обозначим через: w – весовой выход класса, n – число частиц в классе, d – средний диаметр частиц класса, D – средний диаметр частиц всей смеси. Если диапазон изменения крупности частиц в пределах класса достаточно узкий и модуль классификации не превышает 1,414, то с достаточной точностью можно принять

где d1 и d2 – диаметры частиц, ограничивающих класс. Примем для простоты вычислений, что все частицы имеют правильную кубическую форму и одинаковую плотность, тогда

где δ – плотность частиц (постоянная по всем классам при мономинеральном материале).
Рассмотрим на примерах вывод формул среднего диаметра с сохранением определяющего свойства при усреднении.
а) По числовому распределению частиц. Объем коллектива – число всех частиц Σn. Предположим, что определяющим свойством является поверхность всех частиц:
для реальной смеси

для усредненной смеси

Должно существовать равенство

Откуда средний диаметр, обеспечивающий сохранение при усреднении поверхности всех частиц будет исчисляться по формуле

т. е. как среднее квадратичное, взвешенное по числу частиц.
б) По весовому распределению частиц. Объем коллектива – вес всех частиц Σw. Определяющее свойство остается то же самое – поверхность всех частиц:
для реальной смеси

для усредненной смеси

Должно существовать равенство

откуда

т. е. средний диаметр исчисляется как среднее гармоничное, взвешенное по весовым выходам классов.
1.3.8. Порозность материала и его гранпараметрПористостью материала называется отношение объема твердой части частицы материала к объему, занимаемому частицей [2].
Пористость является физической характеристикой твердого тела.
Порозностью материала называется отношение объема пустот между частицами материала к объему, занимаемому материалом [6].
Порозность является характеристикой сыпучего материала, указывает на степень удаления частиц друг от друга и зависит от гранулометрического состава материала и способа укладки частиц.
Порозность определяется по уравнению [6]

где m – порозность в долях единицы; α,γ – углы пространственного элемента (рис. 1.15).
На рис. 1.15 показаны виды укладки частиц шарообразной формы, а в табл. 1.8 приведена их характеристика [7].
Формула (1.64) показывает, что порозность материала, состоящая из частиц одинакового размера, не зависит от диаметра последних, а зависит лишь от вида укладки и может изменяться от 0,259 до 0,476.
Таблица 1.8
Характеристика видов укладки шарообразных частиц


Рис. 1.15. Типы укладок слоя шаров:
а – кубическая; б – ромбическая; в – биромбическая; г – тетраоктаэдрическая; д – тетраоктаэдрической укладки; е – октаэдрическая укладка.
В табл. 1.9 приведены результаты определения порозности моноклассов различных материалов по данным [6].
В практике наиболее простым и достоверным [11] методом определения порозности является метод, при котором порозность определяется через насыпную массу виброуплотненного материала, и плотность частиц материала по формуле

где γн – насыпная масса материала в виброуплотненном состоянии, кг/м3; δ – плотность частиц материала, кг/м3.
Естественно, наиболее устойчивая форма укладки октаэдрическая, для которой порозность равна 0,259. При этой геометрии шары имеют наибольшее количество точек соприкосновения, обеспечивающих их поддержку со всех сторон. В то же время кубическая и все промежуточные формы укладок менее устойчивы. Очевидно, что при любом сотрясении частицы будут стремиться занять наиболее устойчивую форму укладки, при которой порозность будет наименьшей. Однако при размещении большого количества частиц потребуется высокое совершенство укладки отдельных единиц, чего нельзя получить в естественных условиях. В естественных условиях следует ожидать образование групп, в которых размещение частиц будет беспорядочным и, где порозность будет иметь величину большую, чем 0,259.
Таблица 1.9
Значения порозности материалов после их виброуплотнения

Для моноклассов различных зернистых материалов следует ожидать, что их порозность будет находиться между теоретическими значениями 0,26 и 0,48.
Полидисперсные материалы обладают меньшей порозностью, чем отдельные классы этого материала. Это объясняется тем, что меньшие по размеру частицы заполняют пространство между большими, тем самым уменьшают объем межчастичных пустот.
Из формулы (1.65) следует, что насыпная масса материала тем больше, чем меньше его порозность. Этим и определяется важность изучения порозности материалов при подготовке шихты к коксованию, при подготовке заполнителей бетона, для асфальтодорожного покрытия.
Данные табл. 1.8 показывают, что порозность различных моноклассов одного и того же материала не зависит от диаметра частиц и практически одинакова. При этом полученные величины порозности находятся в пределах теоретических значений. Различие в порозности между различными материалами – углем, породой, песком – объясняются различной формой частиц (коэффициент формы соответственно равен 0,57; 0,55 и 0,74. Моноклассы материалов, частицы которых более округлы, например, песка, укладываются наиболее плотно, в результате чего величина порозности таких материалов ниже, чем у материалов с угловатыми формами частиц.
Таким образом, для многих отраслей промышленности ставится задача минимизации порозности при составлении искусственных смесей зернистых материалов.
Определим количественное соотношение классов в двойной смеси угля для достижения минимальной порозности (двойная смесь – это смесь из двух моноклассов материала).
Объем, занимаемый первым (крупным) классом

где G1 – масса первого класса, кг; H1 – порозность первого класса.
Объем пустот в первом классе

Объем, занимаемый вторым (мелким) классом

где G2 – масса второго класса, кг; H2 – порозность второго класса.
Для достижения минимальной порозности объем второго класса должен быть равен объему пустот первого класса, т. е.

откуда при одинаковой плотности и порозности частиц

т. е. для получения минимальной порозности двойной смеси количество (мелкого) класса должно быть равно произведению массы первого (крупного) класса на порозность класса.
Выход классов в двойной смеси равен

где H=0,46 – порозность монокласса угля по табл. 1.8.
При добавлении к двойной смеси третьего класса, к тройной смеси четвертого класса и т. д. минимум порозности достается при добавлении последнего класса в том же количестве, что и второго класса в двойной смеси, при этом выход первого класса определяется как

а выхода остальных классов по формуле

где a– выхода классов в долях единицы; n – число классов в смеси; k – порядковый номер класса.
Анализ показывает, что любой угольный материал может быть разделен на две части, из которых первая (крупная) часть является скелетом, с выходом, определяемым по уравнению (1.71), а вторая (мелкая) часть является заполнителем, с выходом, определяемым по формуле (1.72).
Гранулометрическим параметром (гранпараметором) называется отношение средних диаметров скелета и заполнителя, выход которых равен, соответственно, 0,685 и 0,315 [8].

где dc, dз – средневзвешенный диаметр частиц, соответственно, скелета и заполнителя.
Гранулометрический параметр отражает распределение частиц по крупности и связан с коэффициентом распределения – b в уравнении Розина-Раммлера зависимостью, приведенной на рис. 1.16.
Авторами [9] установлена взаимосвязь порозности угольных смесей с их гранпараметром в виде

Гранулометрический параметр является критерием подобия зернистых смесей по плотности укладки их частиц. Все зернистые смеси в сложенном состоянии независимо от их средней крупности, имеющие одинаковый гранулометрический параметр, подобны и имеют одинаковую порозность.

Рис. 1.16. Связь гранпараметра с коэффициентом (-в) в уравнении Розина-Раммлера
1.3.9. Классификация углей по крупностиКласс – это совокупность частиц, крупность которых ограничена размерами отверстий двух смежнорасположенных сит, связанных между собой модулем шкалы классификации.
Сорт – это совокупность частиц, крупность которых ограничена размерами отверстий двух смежнорасположенных сит, связанных или на связанных между собой модулем шкалы классификации, и соответствует техническим условиям на товарную продукцию.
В нашей стране принята следующая классификация сортового угольного топлива [10]:

Машинный класс – это совокупность частиц, крупность которых ограничена размерами двух смежнорасположенных сит, не связанных между собой модулем шкалы классификации, и соответствует технической характеристике обогатительного аппарата.
Предлагается следующая классификация угля по крупности частиц для машинных классов [11]:

1.4. Процесс грохочения
1.4.1. Последовательность выделения классов при грохоченииПри грохочении сыпучего материала с выделением более двух классов последовательность выделения их определяется расположением сит.
Различают следующие схемы выделения классов: от крупного класса к мелкому; от мелкого класса к крупному; смешанную или комбинированную.
При грохочении от крупного класса к мелкому сита располагают одно под другим (рис. 1.17, а). Верхнее сито имеет наибольшие отверстия, а книзу размеры отверстий сит уменьшаются. Эта последовательность выделения классов имеет следующие преимущества.

Рис. 1.17. Схемы выделения классов при грохочении:
а, б – от крупного к мелкому; в – от мелкого к крупному; г – смешанная
1. Меньший износ сит, потому что вся масса материала и наибольшие куски поступают на рабочую поверхность с крупными отверстиями, которая обычно собирается из стальных решет и защищает поверхности с мелкими отверстиями из проволочных сеток.
2. Более высокая эффективность грохочения мелких классов, так как на сита с мелкими отверстиями поступает меньшее количество материала.
3. Меньшее крошение крупных кусков при грохочении, так как они быстрее выводятся из процесса. Последнее имеет большое значение для углей.
4. Компактность установки грохочения по занимаемой площади вследствие многоярусного расположения сит.
Из недостатков этой схемы следует отметить неудобства в наблюдении за состоянием нижних сит, затруднения в их замене и скученность разгрузки классов в одном конце грохота. Расположение сит по схеме рис. 1.17, б позволяет рассредоточить места вывода классов. При таком расположении также несколько увеличивается эффективность грохочения на нижнем сите, так как наличие поддона под верхним ситом позволяет направить материал в начало нижнего сита.
При грохочении от мелкого класса к крупному сита располагают последовательно в порядке возрастания величины их отверстий (рис. 1.17, в). Достоинства такой последовательности выделения классов заключаются в удобстве смены сит и наблюдения за их состоянием. Помимо того, разгрузка классов рассредоточена по всей длине сит. Недостатки этой схемы, однако, весьма существенны.
1. Быстрый износ сит и пониженная эффективность грохочения, так как вся масса материала загружается на сито с самыми мелкими отверстиями.
2. Возможность крошения крупных кусков хрупкого материала.
При комбинированной схеме выделения классов сита располагаются частично от крупного к мелкому и частично – от мелкого к крупному (рис. 1.17, г).
В практике чаще применяются схемы выделения классов от крупного к мелкому и комбинированные. При необходимости выделения сухого отсева из рядового угля перед его обогащением применяется схема выделения классов от мелкого к крупному.
1.4.2. Баланс материала при грохоченииНа рис. 1.18 приведена схема грохочения и обозначение продуктов.

Рис. 1.18. Схема грохочения
Рассмотрим баланс материала при грохочении

Также имеем

И, Н, П – масса, соответственно, исходного, надрешетного и подрешетного продуктов;
α, β, ϴ – содержание класса меньше крупности разделения, соответственно, в исходном, надрешетном и подрешетном продуктах, %.
Выходом продукта называется отношение его массы к массе исходного продукта (выраженное в процентах). Тогда

Баланс продуктов по выходу

Баланс продуктов по классу меньше крупности разделения

или, разделив на массу исходного продукта,

Пользуясь определением выхода, получим

Баланс продуктов по классу больше крупности разделения

или, разделив на массу исходного продукта,

Пользуясь определением выхода, получим

Извлечением называется отношение массы класса заданной крупности находящегося в продукте разделения к массе этого класса, содержащегося в исходном материале, выраженное в процентах.
Извлечение класса меньше крупности разделения в подрешетный продукт

Подставляя в выражение (1.79) значение γн из выражения (1.78) и преобразуя относительно γп, получим

Подставляя γп из (1.82) в выражение (1.81) окончательно получим

Извлечение класса меньше крупности разделения в надрешетный продукт

Подставляя в выражение (1.79) значение γп из выражения (1.78) и преобразуя относительно γн, получим

Подставляя γн из (1.85) в выражение (1.84) окончательно получим

Извлечение класса больше крупности разделения в надрешетный продукт

или, используя выражение (1.85)

Извлечение класса больше крупности разделения в подрешетный продукт

или, используя выражение (1.82)

Баланс класса меньше крупности разделения по извлечению

Баланс класса больше крупности разделения по извлечению

Для количественной оценки полноты отделения мелкого материала от крупного при грохочении введено понятие эффективности грохочения.
Эффективностью грохочения называется выраженное в процентах или в долях единицы отношение массы подрешетного продукта к массе нижнего класса в исходном материале.

При отсутствии в подрешетном продукте классов больше крупности разделения, т. е. ϴ=100 %, выражение (1.93) приобретает следующий вид

Рассматривая грохочение как операцию разделения на два продукта, для оценки процесса используют критерии эффективности грохочения (которые ошибочно называют также эффективностью грохочения).
В основу этих критериев положено извлечение соответствующих классов в соответствующие продукты.
Критерий эффективности грохочения по извлечению классов в подрешетный продукт

При ϴ=100 %, выражение (1.95) преобразовывается в уравнение (1.94).
Критерий эффективности грохочения по извлечению соответствующих классов в соответствующие продукты

При ϴ=100 %, выражение (1.96) также преобразовывается в уравнение (1.94).
Критерий эффективности по гранпараметру продуктов разделения [9]


Эффективность грохочения и критерии эффективности грохочения определяются по гранулометрическому составу продуктов разделения.
1.4.4. «Легкие», «трудные» и «затрудняющие» частицыПросеивание частиц нижнего класса сыпучего материала сквозь сито можно рассматривать состоящим из двух стадий:
1) частицы нижнего класса должны пройти сквозь слой частиц верхнего класса, чтобы достигнуть поверхности сита;
2) частицы нижнего класса должны пройти через отверстия сита.
Осуществлению обеих стадий помогает соответствующий характер движения короба грохота, приводящий слой частиц на сите в разрыхленное состояние и освобождающий сито от частиц, застрявших в его отверстиях.
При встряхивании короба в слое частиц, лежащем на сите, происходит их сегрегация (расслоение по крупности), причем наиболее крупные частицы оказываются в верхнем слое, а наиболее мелкие – на поверхности сита. Последние легко достигают поверхности сита и проходят через его отверстия. Но зерна, близкие по величине к размеру отверстий сита, с трудом проходят в промежутках между более крупными частицами нижнего слоя материала, лежащего на сите, а также и через отверстия сита.
Практика грохочения показала, что частицы, диаметр которых меньше, чем три четверти величины отверстий сита, легко проходят в промежутках между крупными частицами материала на сите и по достижении ими поверхности сита немедленно проваливаются через отверстия. Такие частицы, в отношении их грохотимости, называют «легкими». Частицы крупнее трех четвертей величины отверстий сита проходят с трудом в промежутках между крупными частицами и через отверстия сита. И эта трудность прохождения прогрессивно возрастает по мере приближения диаметра частиц к величине отверстий сита. Такие частицы называют «трудными» [5].
Частицы, диаметр которых больше полуторной величины отверстий сита, не оказывают существенного влияния на перемещение «легких» и «трудных» частиц к поверхности сита. Но нижний слой материала на сите, состоящий из частиц диаметром меньше полуторной величины отверстий сита, затрудняет проникновение к его поверхности близких к ним по величине «трудных» частиц. Кроме того, частицы, близкие по диаметру к величине отверстий сита, но больше их, легко застревают в отверстиях и «заслепляют» сито. Такие частицы, по размеру большие отверстий сита, но меньшие полуторной величины их, называют «затрудняющими».
Чем меньше в исходном материале «трудных» и «затрудняющих» частиц, тем легче его грохочение и тем выше, при прочих равных условиях, эффективность грохочения.
Характеристики крупности легко– и трудногрохотимого материалов на ситах с размером отверстий l показаны на рис. 1.19.
Эффективность грохочения по «трудным» частицам определяется по общей формуле (1.93), где α, β, ϴ – содержания «трудных» частиц соответственно в исходном материале, надрешетном и подрешетном продуктах.

Рис. 1.19. Характеристики крупности:
а – легкогрохотимого материала; б – трудногрохотимого материала
1.4.5. Вероятность прохождения частиц через отверстия сита
Рассмотрим условия прохождения отдельной частицы через отверстия сита. Вероятность р какого-либо события равна отношению числа случаев m, благоприятствующих наступлению данного события, к числу всех возможных случаев n, при которых данное событие может произойти. Причем все случаи должны быть равновозможными и несовместимыми. Следовательно, величина вероятности измеряется отношением

При m=0 имеем p=0 – невозможность, когда ни один случай не благоприятствует наступлению события, при m=n имеем p=1 – достоверность, когда каждый случай благоприятствует событию.
Величина N, обратная вероятности p, определяет вероятное число случаев, при котором данное событие может иметь место

Предположим, что мы имеем сито из бесконечно тонкой проволоки с квадратными отверстиями величиной l. Допустим также, что шарообразные частицы диаметром d при грохочении падают перпендикулярно к плоскости сита. Будем считать, что зерна проходят через отверстия беспрепятственно, если не касаются проволоки, т. е. центр частицы при падении проектируется на заштрихованную площадь (l-d)2 (рис. 1.20, а).
Можно считать, что число случаев, благоприятствующих прохождению зерна через отверстие, пропорционально заштрихованной площади (l-d)2, а число всех возможных случаев падения частицы на отверстие пропорционального его площади l2. Вероятность прохождения зерна через отверстие определится отношением площадей

Тогда величина N, обратная вероятности p, определит вероятное число отверстий, которое необходимо встретить частице, чтобы в одно из них пройти сквозь сито.

Рис. 1.20. Схема прохождения частицы через отверстие сита
Значения величин p и N для различных отношений d/l приведены в табл. 1.10, по данным которой построен график (рис. 1.21). Из графика видно, что небольшое увеличение диаметра частицы сверх 0,75l вызывает значительное возрастание числа отверстий для прохождения частицы сквозь сито.
Таблица 1.10
Вероятность прохождения зерна через отверстие в зависимости от его относительного размера

Следовательно, теория вероятностей подтверждает принятое практикой деление частиц на «легкие» (d<0,75l) и «трудные» (d>0,75l).
Если учесть толщину проволок сита (рис. 1.20, б), то, рассуждая аналогично предыдущему, получим следующее выражение для вероятности прохождения частицы сквозь сито:

Первый член этого выражения – коэффициент живого сечения сита. Отсюда видно, что вероятность прохождения частицы прямо пропорциональна живому сечению сита.
На основе рассмотренного определения вероятности прохождения частиц сквозь сито можно установить эффективность грохочения частиц диаметром x=d/l (весьма узкого класса).
Согласно формуле (1.101) имеем

где L – коэффициент живого сечения сита в долях единицы.

Рис. 1.21. Вероятность прохождения частицы сквозь сито в зависимости от относительного его размера
Число отверстий N, которое надо встретить частицам, составляющим рассматриваемый узкий класс, для полного прохождения сквозь сито, равно

Встреча с этим числом отверстий обеспечивается при определенной продолжительности грохочения t. Если время грохочения t1 меньше t, то частицы просеваемого узкого класса встретят число отверстий N1, меньшее N, и пройдут сквозь сито не полностью. Извлечение этого узкого класса в подрешетный продукт (эффективность грохочения по данному классу)

где C – постоянный для данного грохота коэффициент пропорциональности.
Для приближенных подсчетов можно пользоваться эмпирической формулой

где a – параметр, являющийся некоторой функцией времени грохочения.