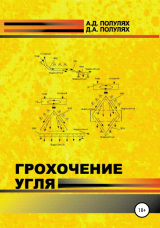
Текст книги "Грохочение угля"
Автор книги: Данил Полулях
сообщить о нарушении
Текущая страница: 1 (всего у книги 6 страниц)
Введение
Все твердые полезные ископаемые в той или иной мере подвергаются классификации по крупности. Из всех способов классификации зернистых материалов, грохочение, как способ разделения частиц по крупности, на просеивающей поверхности занимает важнейшее место в угольной горно-металлургической, строительной, химической и других отраслях промышленности.
Важнейшее место среди подготовительных процессов занимает грохочение в угольной отрасли и, особенно, при обогащении угля. Это связано не только с увеличением пропускной способности углеобогатительных фабрик, но и с внедрением новых обогатительных технологий, для которых выделение и качественная подготовка машинных классов в узких диапазонах крупности является определяющим фактором для эффективной работы этих технологий.
Разработка и использование новых типов грохотов, применение их для классификации шламовых продуктов, особенности оптимизации параметров процессов грохочения в разветвленных схемах углеобогатительных фабрик предопределяет необходимость обобщения результатов работы грохотов и формулировки рекомендаций по их применению.
В данной монографии обобщен опыт применения грохотов для сухого грохочения угля, мокрого грохочения на подвижных грохотах, гидрогрохочения на неподвижной просеивающей поверхности, агрегатной установки гидрогрохотов с инерционными грохотами, гидромеханических грохотах, высокочастотных грохотах и т. д.
Монография может быть полезна для научных работников и специалистов, рабтающих в углеобогатительной отрясли, а также студентов и аспирантов горных вузов, обучающихся по специальности «Обогащение полезных ископаемых».
Глава 1. Общие сведения о грохочении полезных ископаемых
1.1. Назначение и классификация процессов
1.1.1. Основные определенияГорный энциклопедический словарь [1] дает следующее определение процессу грохочения: грохочение – это процесс разделения сыпучего материала по крупности на просеивающих поверхностях.
Устройство для механического разделения (сортирования) сыпучих материалов по крупности кусков (частиц, зерен) путем их грохочения через просеивающую поверхность называется грохотом.
В соответствии с [2] просеивающая поверхность (сито) – это рабочая поверхность грохота, имеющая отверстия (ячейки) конкретного размера и формы. Для круглых отверстий определяющим размером является диаметр, для квадратных – сторона квадрата, для прямоугольных – меньшая сторона прямоугольника, для щелевых – ширина щели.
Материал, поступающий на грохочение, называется исходным, остающийся на просеивающей поверхности – надрешетным (надситным) продуктом, а прошедший через отверстия просеивающей поверхности – подрешетным (подситным) продуктом.
Материал, прошедший через сито с отверстиями d1отв и оставшийся на сите с отверстиями d2отв (d2отв <d1отв), называется классом крупности.
Выход классов крупности (γ) в процентах рассчитывается по формуле

Просеивание сыпучего материала на грохотах осуществляется по т. н. граничной крупности разделения. Под граничной крупностью разделения подразумевается средний диаметр узкого класса крупности, содержание которого в подрешетном и надрешетном продуктах одинаково. Величина граничной крупности разделения может быть больше или меньше характерных размеров отверстий просеивающей поверхности грохота. Она зависит от многих факторов: размера отверстий сита, угла наклона просеивающей поверхности, режимных параметров грохота, гранулометрического состава сыпучего материала, его влажности, формы зерен и т. д.
Граничная крупность разделения определяется по сепарационной характеристике грохота, построенной по данным ситового анализа продуктов грохочения. Исходные данные для построения (в качестве примера) сепарационной характеристики процесса грохочения приведены в табл. 1.1, а определение граничной крупности разделения дано на рис. 1.1.
Таблица 1.1
Исходные данные для построения сепарационной характеристики процесса грохочения


Рис. 1.1. Определение граничной крупности разделения
Построение сепарационной характеристики процесса грохочения осуществляется по извлечению классов крупности в подрешетный продукт (ε(-)) и надрешетный (ε(+)). Проекция точки пересечения этих сепарационных характеристик на ось абсцисс дает значение граничной крупности разделения. В нашем случае ее величина составляет 13,7 мм.
Классы угля, совместно направляемые на обогащение в один аппарат, называют машинным классом.
Классы угля, являющиеся готовыми товарными продуктами, называются сортами.
Шкала грохочения – отношение максимального размера частицы к ее минимальному размеру в каждом классе грохочения, которая может иметь постоянный и непостоянный модули.
Модуль – отношение размеров отверстий смежных решет, сит. В угольной промышленности для стандартных решет (сит) принят модуль

Промышленная шкала грохочения устанавливается в зависимости от обогатимости угля, принятой технологической схемы обогащения, требований потребителей и, как правило, она имеет непостоянный модуль.
При последовательном грохочении материала на п ситах получают п + 1 продукт. В этом случае один из продуктов предыдущего просеивания служит исходным материалом для последующего просеивания.
Размер d наибольших зерен (кусков) подрешетного продукта так же, как и размер наименьших кусков надрешетного продукта, условно принимают равным размеру отверстий сита l, через которое просеивается материал, т. е. d = l. Соответственно обозначают: подрешетный продукт – l (минус l) или – d (минус d); надрешетный продукт + l (плюс l) или +d (плюс d).
Материал, прошедший через сито с отверстиями l1 и оставшийся на сите с отверстиями l2, причем l2< l1, и называется классом крупности. Крупность класса обозначают следующими тремя способами: – l1 +l2 (минус l1, плюс l2) или – d +d; l1-l2 или d1-d2; l2< l1 или d2-d1. Например, классы -25 + 10; 25–10 и 10–25 мм. Из приведенных способов обозначения крупности классов наиболее широко применяют первый и третий, обязательный для использования при грохочении углей (ГОСТ 2093-82) и щебня.
В получаемых при грохочении классах размер наибольших кусков материала d1 всегда меньше размера отверстий сита l1, а размер наименьших кусков d2 – больше отверстий l2. Обозначения крупности классов – d1 +d2 или d1-d2 указывают лишь на то, что данный класс был получен последовательным просеиванием материала на двух ситах с отверстиями размером d1= l1 и d2 = l2.
Извлечение (ε) определяется как отношение количества классов меньше граничной крупности разделения, содержащегося в подрешетном продукте, к его количеству в исходном материале, выраженное в процентах, т. е.

Грохочение зернистых материалов бывает сухим, мокрым и в водной среде.
Сухое грохочение осуществляется без добавления воды. В углеобогащении применяется для предварительного и подготовительного грохочения угля, а также для выделения из рядового угля сухого отсева крупностью 0–6 мм.
Мокрое грохочение осуществляется с добавлением воды. В углеобогащении применяется для подготовительного и тонкого грохочения, соответственно, угля и угольных шламов.
Грохочение в водной среде осуществляется помещением просеивающей поверхности под зеркало воды. В углеобогащении не применяется.
Основным фактором, определяющим применение сухого и мокрого способа подготовки машинных классов, является влажность. Так, по данным ИОТТ, на каждый процент повышения влажности исходного угля сверх 5,5 эффективность грохочения снижается при размере отверстий сит 13 и 6 мм соответственно на 10 и 24 % [19]. Исследованиями ИОТТ установлено, что сухое грохочение мелких классов антрацита по граничному зерну 6 мм при влажности исходного 7–7,5 % невозможно, так как сита при этом полностью залипают.
Таблица 1.2
Динамика изменения влажности углей

В сложившихся условиях, когда влажность антрацита достигает 7–8% (влажность классов 0-13 мм – 9-10 %), а влажность каменных углей приближается к этому значению (табл. 1.2, [11]), необходима разработка эффективных средств интенсификации процессов грохочения.
Трудности, возникающие при грохочении влажного угля, обусловлены проявлениями капиллярного сцепления между отдельными угольными зернами, покрытыми пленкой воды. Под действием сил поверхностного натяжения между пленками воды происходит комкование влажного материала, а в результате действия этих же сил между частицами угля и увлаженной поверхностью сита – залипание сит.
Как показали исследования [27], приведенные на рис. 1.2, влияние сил поверхностного натяжения может быть устранено либо удалением влаги при сушке, либо наполнением промежуточных объемов жидкостью (мокрое грохочение).

Рис. 1.2. Зависимость эффективности грохочения углей (Е) от их влажности (W):
AB – сухое грохочение; BC – грохочение влажного угля; CD – отсутствие грохочения; DF – мокрое грохочение
Силы поверхностного натяжения могут быть уменьшены путей применения поверхностно-активных веществ и увеличения уровня ускорения грохотов.
При сухом грохочении влажных углей увеличение вил разделения достигается путем подбора оптимальных динамических режимов работы грохота и специальных материалов для рабочих поверхности, установкой струнных, консольно-каскадных н других сит, применением центробежных сил, созданием специальных устройств для разрыхления материала. С этой же целью применяются различные устройства и механизмы для очистки рабочей поверхности в вида щеток, самоочищающихся колосников, резиновых шаров и т. п. Однако, несмотря на подобное многообразие средств интенсификация улучшения способов разделения, проблема сухого грохочения влажных углей на современных обогатительных фабриках остается до сих пор не решенной. Во многом это объясняется тем, что при применении электрообогрева сит и средств интенсификации режимов разделения на грохоте, работающем в режиме сухого грохочения, силы, интенсифирующие разделение, действуют, в основном, на просеивающую поверхность, грохота, а не на грохотимый материал, в результате чего не устраняется явление комкования.
В связи в тем, что способы газо– и электрообогрева, а также аэродинамического воздействия на грохотимый материал до этого времени не дали удовлетворительных результатов, наиболее приемлемым методом улучшения классификации углей для условий углеобогатительных фабрик с мокрыми методами обогащения и глубиной до 0 мм, оказалось применение метода мокрого грохочения.
Эффективность указанного способа грохочения объясняется тем обстоятельством, что ликвидация сил капиллярного сцепления между частицами и просеивающей поверхностью грохота осуществляется с помощью внешних импульсов в виде струй воды, одновременно действуя как на грохотимый материал, так и на поверхность грохота.
При влажности материала, превышающей предельное значение (точка D), подвижность зерен возрастает и наступают условия для мокрого грохочения.
При прямом грохочении, когда исходный материал подается на сито, надситный продукт представляет собой частицы не прошедшие через отверстия просеивающей поверхности и обозначается знаком + (плюс), а подситный продукт – частицы, прошедшие через отверстия просеивающей поверхности – обозначается знаком – (минус).
При обратном грохочении, когда исходный материал подается под сито, надситный продукт представляет собой частицы прошедшие через отверстия просеивающей поверхности и обозначается знаком – (минус), а подситный продукт – частицы не прошедшие через отверстия просеивающей поверхности – обозначается со знаком + (плюс).
Просеивание называется сухое дискретное грохочение зернистых материалов, при котором основным интенсифицирующим усилием разделения является сила тяжести. Грохоты, предназначенные для этой операции имеют множество названий, целесообразно их классифицировать как устройство для сухого грохочения.
Гидравлическим грохочением называется мокрое грохочение зернистых материалов, при котором основным интенсифицирующим усилием разделения является сила тяжести. Грохоты, предназначенные для этой операции имеют множество названий, целесообразно их классифицировать как устройства для гидравлического грохочения.
Виброгрохочением называется сухое или мокрое грохочение зернистых материалов, при котором основным интенсифицирующим усилием разделения является сила инерции. Грохоты, предназначенные для этих операций, называются вибрационными грохотами или просто грохотами.
Гидрогрохочением называется мокрое грохочение зернистых материалов в виде пульпы, при котором основным интенсифицирующим усилием разделения является гидродинамическая сила струй воды, вытекающих из сопел. Грохоты, предназначенные для этой операции, называются гидрогрохотами.
Пневмогрохочением называется сухое грохочение зернистых материалов, при котором основным интенсифицирующим усилием разделения является аэродинамическая сила струй воздуха, вытекающих из сопел. Грохоты, предназначенные для этой операции, называются пневмогрохотами.
Пневмогидрогрохочением называется мокрое грохочение зернистых материалов в виде пульпы, при котором основным интенсифицирующим усилием разделения является аэродинамическая сила струй воздуха, вытекающих из сопел. Грохоты, предназначенные для этой операции, называются пневмогидрогрохотами.
Прямоточным грохочением называется грохочение, когда движение надситного продукта совпадает с направлением интенсифицирующего усилия разделения.
Противоточным грохочением называется грохочение. когда движение надситного продукта противоположно направлению интенсифицирующего усилия разделения.
1.1.2. Виды грохоченияПредварительное – для отделения от исходного угля крупных кусков с целью выборки из них породы и других предметов и последующего дробления.
Подготовительное – для получения отдельных (машинных) классов угля, пригодных для раздельного их обогащения или других видов обработки.
Самостоятельное – для выделения сортов сухого отсева.
Контрольное – для контроля крупности готового продукта.
Обесшламливающее – для удаления шлама из машинных классов и продуктов разделения при мокром обогащении.
Обеспыливающее – для удаления шлама из машинных классов и продуктов разделения при сухом обогащении.
Обезвоживающее – для удаления воды от продуктов мокрого обогащения.
Вспомогательное – для выделения мелочи из отдельных сортов.
Избирательное – для получения классов угля, отличающихся не только по крупности, но и качеству.
В практике обогащения углей грохочение осуществляется от крупных кусков к мелким. Верхнее сито имеет отверстия наибольшего, нижнее – наименьшего размера.
1.2. Теоретические основы грохочения
Просеивание зерен нижнего класса сыпучего материала сквозь сито можно рассматривать как операцию, состоящую из двух стадий: зерна нижнего класса должны пройти сквозь слой зерен верхнего класса, чтобы достигнуть поверхности сита; зерна нижнего класса должны пройти через отверстия сита. Осуществлению обеих стадий помогает соответствующий характер движения короба грохота, приводящий слой зерен на сите в разрыхленное состояние и освобождающий сито от зерен, застрявших в его отверстиях.
При встряхивании короба в слое зерен, лежащем на сите, происходит их сегрегация (расслоение по крупности), причем наиболее крупные зерна оказываются в верхнем слое, а наиболее мелкие – на поверхности сита. Последние легко достигают поверхности сита и проходят через его отверстия.

Рис. 1.3. Схема прохождения зерна через квадратное отверстие сита
Зерна проходят через отверстия беспрепятственно, если они не касаются проволоки, т. е. когда центр зерна при падении проектируется на заштрихованную площадь (l – d)2 (рис. 1.3).
Можно считать, что число случаев, благоприятствующих прохождению зерна через отверстие, пропорционально заштрихованной площади (l – d)2, а число всех возможных случаев падения зерна на отверстие пропорционально его площади l2. Вероятность прохождения зерна через отверстие определится отношением площадей:

С учетом толщины проволок сита получено следующее выражение для вероятности прохождения зерна сквозь сито:


Рис. 1.4. Вероятность прохождения зерен через сито в зависимости от их относительного размера
Первый член этого выражения представляет коэффициент живого сечения сита. Следовательно, вероятность прохождения зерна прямо пропорциональна живому сечению сита.
Зерна размером до 0,75l имеют большую вероятность их прохождения через отверстия сита и называются легкогрохотимыми. Небольшое увеличение размера зерен сверх 0,75l предопределяет резкое снижение вероятности прохождения. Поэтому зерна крупностью в пределах от 0,75l до l называются трудногрохотимыми. Зерна диаметром от l до 1,5l называются «затрудняющими», так как они затрудняют просеивание «трудных» зерен. Зерна крупностью более 1,5l существенно не влияют на перемещение «легких» и «трудных» зерен по поверхности сита (рис. 1.4).
Чем больше скорость движения материала по грохоту, тем меньше вероятность просеивания, при прочих равных условиях, и тем больше производительность грохота по исходному материалу.
Сферическое зерно диаметром d (рис. 1.5), движущееся по ситу со скоростью v, пройдет через отверстие при условии, что траектория движения центра его тяжести пересечет верхнюю плоскость сита не дальше точки 01. Если траектория движения зерна пройдет выше, то возможность прохождения его через отверстие маловероятна.
Координаты точки 01

где v – скорость движения зерна, м/с; t – время движения, с; g – ускорение свободного падения, м/с2.

Рис. 1.5. Схема влияния скорости движения зерна на прохождение его через отверстие сита
Из рис. 1.5 следует, что

Из формулы (1.6) видно, что

Подставив в формулу (1.6) значения x1 и t1, получим

Скорость v, при которой обеспечивается прохождение зерна через отверстие,

Для «трудного» зерна размером, приближающимся к размеру отверстия d≈l, получено

где d – размер зерна, м.

Рис. 1.6. Схема влияния наклона и толщины решета на размер зерна, проходящего в отверстие сита
По формуле (1.10) можно вычислить максимальную скорость сферического тела d≈l, при которой обеспечивается беспрепятственное прохождение его через отверстие.
Предельная скорость движения материала (скорость подачи) по формуле (1.10) получена без учета подбрасывания.
При режиме с подбрасыванием скорость движения зерен повышается в 2–3 раза. Оптимальную подачу устанавливают экспериментально в зависимости от производительности и необходимой эффективности грохочения.
Существенное влияние оказывают на процесс грохочения угол наклона и толщина просеивающей поверхности (рис. 1.6). Если грохочение осуществляется на наклонной под углом α плоскости толщиной h, мм, то для определения размера зерна, проходящего через отверстия, получено выражение

Чтобы получить подрешетный продукт одинаковой крупности при α = 20° и, α = 25° размер отверстий наклонного сита должен быть в 1,15 и 1,25 раза больше отверстий горизонтального сита.
В начальный период грохочения эффективность его увеличивается быстро, а затем замедляется. Это объясняется тем, что скорость грохочения зависит от количества зерен, которые должны пройти сквозь отверстия сита. В первые моменты проходят в основном легкогрохотимые зерна, и процесс грохочения протекает быстро. Затем с течением времени количество их становится все меньше и меньше.
Трудногрохотимые же зерна требуют для своего просеивания значительно больше времени. Поэтому и эффективность просеивания с течением времени замедляется.
С увеличением производительности грохота Q, при прочих равных условиях, эффективность грохочения Е понижается.
Таким образом, на эффективность грохочения влияют, в основном, два фактора: гранулометрический состав грохотимого материала и отверстия просеивающей поверхности грохота. На вероятность прохождения частицы через отверстие оказывают влияние технологические, конструктивные, динамические и гидродинамические факторы.
1.3. Гранулометрический состав
1.3.1. Крупность частицПри дроблении, измельчении и грохочении приходится иметь дело с рыхлыми смесями частиц материалов (породы) различного размера – от максимальных кусков, измеряемых сотнями миллиметров, до мельчайших частиц величиной в несколько микронов.
Куски обычно имеют неправильную форму и их величина может быть охарактеризована лишь несколькими размерами. Для практических целей желательно характеризовать величину отдельного куска одним размером. Этот размер обычно называют «диаметр» куска. Диаметром кусков сферической формы будет диаметр шара. Для кусков кубической формы за диаметр принимают длину ребра куба; для кусков неправильной формы диаметр определяют по главным измерениям – длине l, ширине b и толщине t параллелепипеда, в который вписывается змеряемый кусок. При этом используют все размеры или только некоторые из них. За диаметр d куска принимают:

Перечисленные способы определения диаметра куска неправильной формы используются при изучении отдельных кусков. Формула для вычисления выбирается в зависимости от способа измерений и целей, для которых подсчитывается диаметр куска. С помощью сит можно получить один размер куска. В этом случае приходится пользоваться формулой (а). С помощью микроскопа определяется два размера и можно пользоваться формулами (б) и (г). Для крупных кусков можно получить все три размера и применить формулы (в), (д), (е) и (ж), если надо характеризовать линейный размер, объем, поверхность или удельную поверхность соответственно.
При грохочении, для массовых определений размера зерен, за диаметр зерна принимают размер наименьшего квадратного отверстия, через которое это зерно может проходить.
Крупность всей массы сыпучего материала оценивают по содержанию в ней классов определенной крупности, т. е. по ее гранулометрическому составу. Гранулометрический состав материала определяют посредством анализов:
1) ситового – путем рассева на ситах на классы крупности, для материалов крупнее 0,04 мм;
2) седиментационного – путем разделения материала на фракции по скоростям падения частиц в жидкой среде, для материалов крупностью от 50 до 5 мк;
3) микроскопического – путем измерения частиц под микроскопом и классификации их на группы в узких границах определенных размеров для материалов крупностью менее 50 до десятых долей микрона.
Гранулометрический состав материалов для контроля процессов грохочения, дробления и измельчения на обогатительных фабриках определяют чаще всего посредством ситового анализа.
Средний диаметр частиц определенного класса крупности находится по формуле

Для нескольких классов или всей смеси частиц средний диаметр определяется как среднединамический диаметр по формуле

Выход отдельных классов определяется в процентах. Размер крупных и мелких частиц выражается в миллиметрах, а тонких – в микронах.
Номинальным называют размер квадратной ячейки контрольного сита, через которое проходит 95 % пробы материала. Для оценки номинального диаметра помимо прямых измерений используется поведение частицы в некоторых специфических условиях, например осаждение в воде. Некоторые из наиболее известных номинальных диаметров [3] приведены в табл. 1.3.
Очевидно, что полученный диаметр для частицы неправильной формы будет зависеть от используемой методики измерения. Например, диаметр Стокса dСт определяется при ламинарных условиях потока и не применим при турбулентных потоках, так как в последнем случае частица ориентируется так, чтобы обеспечить максимальное торможение, в то время как в первом случае она ориентируется случайным образом. Поэтому всякий раз при упоминании крупности частиц следует указывать, какой номинальный диаметр используется.
Крупность всей массы сыпучего материала оценивают по содержанию в ней классов определенной крупности, т. е. по ее гранулометрическому составу. Гранулометрический состав материала в зависимости от крупности определяют одним из следующих способов, мК [3]:

Таблица 1.3
Номинальные диаметры

Наиболее часто для контроля процессов грохочения, дробления и измельчения на обогатительных фабриках применяют ситовый анализ.
Для оперативного контроля гранулометрического состава материалов на потоке используют различные конструкции автоматических гранулометров [4]. По принципу действия гранулометры разделяют на ситовые, седиментационные, ультразвуковые, лазерные, оптические и т. д. Гранулометры осуществляют контроль одного (определяющего) либо нескольких классов крупности.