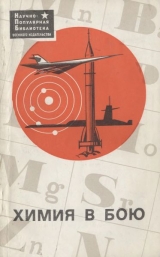
Текст книги "Химия в бою"
Автор книги: авторов Коллектив
Жанры:
Технические науки
,сообщить о нарушении
Текущая страница: 7 (всего у книги 10 страниц)
НОВЫЙ ЧЕМПИОН – КОМПОЗИЦИОННЫЕ МАТЕРИАЛЫ
Инженер-подполковник Г. НЕСТЕРЕНКО, кандидат технических наук
Во все времена материалы, используемые в технике, были одним из главных условий ее развития. Через деревянную соху, каменный топор, а затем железные орудия труда пролегал путь человечества к вершинам современной цивилизации. Стекло, сталь, алюминий, пластмассы– вот материалы, из которых строились последующие ступени научно-технического прогресса. Однако возможности подобных материалов небезграничны. Не случайно, когда речь заходит о реализации новых технических проектов, нередко указывают на то, что почти все эти возможности исчерпаны, нужны новые материалы. Но вот в середине шестидесятых годов на страницах научных журналов стали встречаться необычные термины: «монокристаллические нити», «композиционные материалы». Специалисты заговорили о новых перспективах развития авиационной, космической, ракетной и другой техники.
Композиционные, или, как их иногда еще называют, «композитные», – это значит составные, неоднородные, сборные, как бы специально конструируемые материалы. Их нет в природе. Они составляются искусственным путем из элементов, изготовляемых из различных материалов, и имеют упорядоченную, построенную по определенному замыслу внутреннюю структуру.
Простейшие композиционные материалы давно всем известны. Это прежде всего железобетон, состоящий из бетонной массы и скрепляющей ее стальной арматуры. Еще – текстолит, внутренняя структура которого представляет собой слои прочной ткани, скрепленные затвердевшей смолой. В последние годы, благодаря успехам химии, широко стал применяться «стеклопластик» – тоже составной, композиционный материал. Из «стекловолокна»– неорганического соперника нейлона и других высокопрочных синтетических волокон – методом «намотки» с последующей пропиткой полимеризуемыми, затвердевающими смолами изготавливаются сейчас даже крупные, высоконагруженные конструкции – корпуса ракет, катеров, части самолетов, вертолетов. В печати сообщалось, например, о первом полете экспериментального самолета, конструкция которого почти целиком выполнена из стеклопластиков. Однако особый, повышенный интерес специалистов вызывают не эти композиционные материалы, а другие. Они строятся на принципиально новой основе.
На пути к идеалу
Наукой установлено, что применяемые в современной практике конструкционные материалы обеспечивают лишь 10–15 процентов своей идеальной, то есть теоретически достижимой прочности, твердости и других важных характеристик. Происходит это потому, что внутреннее строение этих материалов представляет собой неупорядоченную, хаотически сросшуюся при остывании расплава смесь кристаллических зерен. Таким структурам, содержащим к тому же примеси, присущи различного рода микродефекты. Если же материал подвергнуть тщательной очистке, а внутреннее строение образца «выправить», построив атомы металла в такую же строгую кристаллическую решетку, как, например, у драгоценных камней, то прочность его и другие свойства станут близкими к идеальным.
Однако получать целиком детали или их заготовки в виде монолитных кристаллов пока не удается. Чистые монокристаллы получают сейчас в ряде стран посредством весьма сложной технологии лишь в виде тончайших нитей, диаметром до 0,1 миллиметра и длиной до нескольких сантиметров. Зато прочность таких монокристаллических нитей на разрыв может достигать 1400 кг/мм2, что примерно в десять раз больше, чем у большинства конструкционных сталей. Идея создания новых композиционных материалов именно в том и состоит, чтобы использовать сверхпрочные монокристаллические нити в качестве арматуры применяемых сегодня конструкционных материалов, «укрепить» их нитями так же, как железная арматура укрепляет бетон. При этом матрицей, то есть связующей основой, служат различные металлы, керамика и другие материалы.
Конечно, прочностные характеристики созданных таким образом материалов оказываются ниже, чем у идеальных монокристаллов, но зато они могут быть значительно, при некоторых сочетаниях в несколько раз, выше, чем у обычных, исходных конструкционных материалов. Так, упрочение алюминиевых сплавов нитевидными кристаллами сапфира позволяет увеличить их прочность в 2–3 раза. С точки зрения ювелиров, сапфир – драгоценный камень, а для химика – это окись алюминия, из которой получаются нитевидные кристаллы высокой прочности. В лабораторных условиях, как указывает печать, удается получать также монокристаллы химически чистого алюминия, железа, окиси кремния, карбида бора и многих других элементов и их соединений.
В отличие от известных ранее волокнистых материалов нитевидные кристаллы в принципе могут обладать близкой к идеальной прочностью, поскольку у них отсутствуют ослабляющие микротрещины, резкие переходы в структуре и другие «дефекты». Поэтому-то специалисты четко разграничивают монокристаллические нити и прочие материалы, используемые ныне в качестве арматуры – стекловолокно, проволока.
Чистые нитевидные кристаллы получают в настоящее время различными способами «выращивания» при процессах кристаллизации из жидких, паровых и газообразных фаз. Изготовить длинные монокристаллические нити в виде непрерывного волокна, которые можно было бы использовать для изготовления конструкций методом намотки, как из стекловолокна, сообщает печать, пока не удается. С увеличением длины и диаметра монокристаллических нитей уменьшается их прочность, так как повышается вероятность появления микротрещин и других дефектов структуры.
Установлено, что близкая к идеальной структура возможна лишь в тонких кристаллических нитях диаметром менее 0,1 мм. Длина таких нитей составляет, как правило, от нескольких миллиметров до двух-трех сантиметров. Однако разрабатываются методы получения все более длинных нитевидных кристаллов. В печати сообщалось, что одной из английских фирм удалось получить нити из графита длиной до 90 см. Специалисты этой фирмы надеются в недалеком будущем получить нити длиною до 4,8 километра, то есть практически непрерывное графитовое волокно.
Сообщалось, что использование монокристаллических нитей и металлических матриц позволяет уже сейчас получать конструкционные материалы с пределом прочности до 500 кг/мм2 и более. Кроме того, многие композиционные материалы сохраняют высокие значения своих характеристик в условиях работы при очень большой температуре. Так, образцы, изготовленные из композиционного материала на основе серебряной матрицы, армированной нитевидными кристаллами сапфира, сохраняют свои механические характеристики при температуре, близкой к точке плавления серебра. По сообщениям зарубежной печати, сейчас ведутся исследования, связанные с получением нитевидных кристаллов специально из жаропрочных материалов – вольфрама, молибдена, тантала.
От нити к материалу
Технология производства деталей и конструкций из композиционных материалов имеет ряд специфических особенностей и представляет значительную сложность. Кроме правильного подбора матриц и армирующих нитей по соображениям прочности, температурным характеристикам и т. д. необходимо принимать в расчет возможность химического взаимодействия материалов матрицы и арматуры, растворимость нитей в расплавленной матрице, смачиваемость нитей арматуры материалом матрицы. В некоторых случаях, отмечалось в печати, приходится покрывать монокристаллические нити специальными изолирующими или связующими покрытиями для получения нужных условий на границах арматуры и матрицы.
При изготовлении листов, профилей, различных деталей и конструкций из композиционных материалов на основе металлических и керамических матриц в настоящее время применяются различные методы: отливка, жидкая инфильтрация (пропитка), порошковая металлургия, диффузионное склеивание. Некоторые методы предусматривают предварительное покрытие монокристаллических нитей материалом, предназначаемым в качестве матрицы, с последующей формовкой, прессованием и спеканием заготовки или сразу готовой детали, не требующей механической обработки. Однако технологические процессы производства конструкций из композиционных материалов, и особенно процессы выращивания нитевидных кристаллов, остаются пока что мало освоенными и весьма дорогими.
Однако трудности эти, как полагают, со временем будут преодолены.
Замечательным свойством композиционных материалов на основе монокристаллических нитей оказывается то, что они обеспечивают получение более прочных деталей при значительно меньшем весе. Снижение веса достигается не только путем уменьшения объема используемого материала ввиду его большой прочности, но и за счет того, что композиционный материал, как правило, имеет меньший удельный вес, чем те обычные конструкционные материалы, которые он заменяет. В печати сообщалось, что армирование волокнами сапфира в 20–25 раз повышает удельную прочность серебра, в 12–15 раз – чистого алюминия, в 7–9 раз – эпоксидной смолы, в 3–4 раза – никеля.
Еще более существенно повышается при армировании нитевидными кристаллами предел текучести материалов, то есть нагрузка, при которой материал образца получает существенные остаточные деформации. Так, предел текучести алюминия и серебра, армированного нитями сапфира, повышается примерно в 30 раз при комнатной температуре и еще больше при повышенной. Материал, имеющий в своей структуре нитевидные кристаллы, менее чувствителен также к «усталости». Он более устойчив при вибрациях и опасных колебаниях авиационных конструкций типа флаттер. Причина такой повышенной устойчивости состоит в том, что каждое из тысяч волокон композиционного материала в конструкции несет свою нагрузку независимо, так что разрыв одного или нескольких волокон не снижает прочности остальных. Именно поэтому композиционный материал менее чувствителен к появлению и развитию «усталостных» трещин.
Исследования, интенсивно ведущиеся в лабораториях многих стран мира, направлены сейчас в основном на разрешение проблем, связанных с получением и обработкой монокристаллических нитей, выбором наилучших методов их размещения в матрицах, оптимизацией количества и ориентацией нитей в зависимости от величины и направления действия нагрузок и т. д. Характерно, что во многих случаях эти исследования производятся с помощью моделирования на электронных вычислительных машинах.
За стенами лабораторий
В настоящее время имеется немало примеров практического применения новых композиционных материалов в конструкциях авиационных и ракетных двигателей, самолетов и вертолетов. По сообщениям зарубежной печати, в 1967–1968 годах началось освоение промышленного производства деталей самолетов и ракет из бороволокна, графитового волокна и других композиционных материалов. Кроме лопастей роторов вертолетов и лопаток для газотурбинных двигателей из них уже изготавливаются и проходят испытания такие высоконагруженные элементы авиационных конструкций, как самолетные шасси, обшивка и силовой набор крыльев, фюзеляжей и оперения самолетов. Проведенные зарубежными специалистами расчеты показывают, что переход к композиционным материалам позволяет уменьшить вес этих элементов конструкций от 20 до 50 процентов, то есть примерно в полтора-два раза.
Как сообщал журнал «Эркрафт», английская фирма «Роллс-Ройс» уже несколько лет применяет стеклопластик и другие композиционные материалы в конструкциях воздушно-реактивных двигателей. В последнее время фирма осваивает композиционный материал «хай-фил» на основе графитового волокна. Рабочие лопатки вентиляторов и компрессоров реактивных двигателей, выполненных из хайфила, оказываются значительно легче, долговечней и даже дешевле, чем металлические,
Зарубежная печать сообщает о применении монокристаллов и композиционных материалов на новых американских самолетах F-5A, F-111, С-5А, а также в приборостроении, реакторостроении и других областях техники. Композиционные материалы предполагают еще более широко использовать на проектируемых в США самолетах, таких, как F-14, F-15 и «AMSA». Как сообщал недавно журнал «Металл инженирииг куотерли», американские специалисты подсчитали, что применение композиционных материалов позволит уменьшить вес конструкции разрабатываемого сверхзвукового бомбардировщика «AMSA», которому недавно дано обозначение «В-1A», на 25–32 процента.
Однако промышленное производство композиционных материалов на основе монокристаллических нитей все же находится за рубежом еще в стадии становления. Получение многих типов монокристаллов доступно пока только в лабораторных масштабах, а стоимость некоторых из них называют баснословной – до 40 тысяч долларов за килограмм. Правда, зарубежные специалисты считают, что уже в ближайшие годы, по мере внедрения в промышленность, стоимость монокристаллических нитей и композиционных материалов будет быстро снижаться.
Обращают внимание и на то, что одно из существенных преимуществ композиционных материалов составляет возможность изготовления конструкций без механической обработки или с очень незначительной обработкой. Поэтому окончательная стоимость деталей и конструкций из композиционных материалов может оказываться даже меньше, чем из обычных металлов и сплавов.
На проходивших в последние годы крупных международных конференциях и симпозиумах по проблемам композиционных материалов отмечалось быстрое развитие теории, технологии производства и практического применения нитевидных кристаллов и композиционных материалов на их основе. Начал издаваться специальный журнал по проблемам композиционных материалов. Им посвящается также много страниц других изданий.
Предполагают, что в ближайшие 3–5 лет практически будут использоваться армирующие материалы с прочностью на растяжение до 700 кг/мм2, а в последующие 5—10 лет такая прочность может быть получена не только у армирующих, но и у самих композиционных материалов, из которых будут изготавливаться реальные конструкции. Многие специалисты рассматривают композиционные материалы как основу дальнейшего прогресса авиационной, космической и многих других видов техники.
Но, как это было уже не раз, к новому достижению науки тотчас потянулись военные круги империалистических государств. Выше приводились примеры использования композиционных материалов в конструкциях военных самолетов. В США такое применение важного технического новшества считается первоочередным. Это еще раз свидетельствует о том, что империализм стремится использовать достижения человеческого разума, талант ученых и инженеров не на пользу человечеству, не для улучшения жизни на земле, а для осуществления своих агрессивных реакционных целей.
Однако монополии на технический прогресс не существует. Разработка новых композиционных материалов доступна всем высоко развитым в научном и техническом отношении странам. А в каких именно направлениях эти материалы будут применяться и в каких масштабах – покажет время.
ГОРЮЧЕЕ ДЛЯ ВОЙСК: ПРОБЛЕМЫ И ПОИСКИ
Инженер-полковник А. ЧОЧИА
Скорости двадцатого века… За какие-нибудь полстолетия человечество прошло путь от первых автомобилей, с трудом одолевавших за час десяток километров, до сверхзвуковых самолетов и космических кораблей. В этом стремительном покорении пространства и времени, ставшем олицетворением технического прогресса наших дней, химии принадлежит ведущая роль. Она дала главное – энергию топлива. С той поры вместе с развитием конструкций двигателей внутреннего сгорания непрерывно совершенствуются возможности топлива, появляются новые виды горюче-смазочных материалов.
Чем это вызвано? Какие проблемы стоят здесь перед специалистами?
Основным фактором, определяющим ценность горючего, считается количество теплоты, выделяемое при сгорании единицы массы или объема топлива, то есть его теплотворная способность. Из всех широко распространенных видов ископаемого топлива наибольшей теплотворной способностью обладает нефть, точнее, продукты ее переработки: бензин, керосин, дизельное топливо, мазут и другие. Это оказалось решающим в установлении гегемонии нефти среди остальных видов топлива, которую пока не удалось поколебать другим, в том числе и нехимическим источникам энергии.
Может, однако, возникнуть впечатление, что продукты переработки нефти представляют собой чуть ли не идеальное горючее. Нет, это далеко не так. Углеводородное топливо имеет гораздо больше недостатков, чем хотелось бы конструкторам двигателей современных машин. Назовем некоторые, наиболее характерные из них.
Даже при самой тщательной очистке в топливе остаются посторонние примеси. Наибольшую опасность из них представляет влага. Кроме того, неполное сгорание топлива, наличие в его составе негорючих веществ, так называемой золы, приводят к появлению нагара, загрязнению рабочих частей двигателя.
Пытаясь устранить эти недостатки, специалисты-химики предложили добавлять в топливо небольшие количества особых химических соединений, получивших название присадок. Так, к бензину стали добавлять антинагарные, моющие присадки для предотвращения загрязнения карбюратора углеродистыми отложениями. Появились многофункциональные присадки, улучшающие одновременно несколько эксплуатационных свойств топлива. К ним относится, например, изодецилортофосфат никеля, снижающий износ и ржавление деталей автомобильных двигателей, способствующий лучшему сгоранию бензина и устраняющий обледенение карбюратора. В качестве антиобледенительной присадки к реактивным топливам за рубежом используют монометиловый эфир этиленгликоля с добавкой небольшого количества глицерина. Эта присадка одновременно препятствует росту микроорганизмов в топливных системах самолетов – приходится считаться и с таким явлением.
Но особенно сложным дёлом оказалось устранить органически присущую топливу опасность пожара. Экипаж любой машины в этом смысле «сидит на бочке с порохом». Повреждение топливных баков или магистралей, будь то в бою или при аварии, чревато опасностью воспламенения паров топлива и взрыва. Возникает задача уменьшить летучесть топлива. Как сообщается в печати, зарубежные специалисты разрабатывают для этого способы загущения топлива, превращения его в студенистую эмульсию.
С помощью особых веществ – эмульгаторов рассчитывают уменьшить распыление горючего при ударе, снизить его способность интенсивно растекаться в случае повреждения баков. В журнале «Интеравиа эйр леттр» указывалось, например, что один из видов эмульгированного горючего для реактивных самолетов при температуре плюс 25 градусов не загорается во время контакта с огнем в течение часа, тогда как обычное топливо воспламеняется практически мгновенно. Однако достигается все это довольно дорогой ценой. У вязкого топлива ухудшается эффективность сгорания, его труднее перекачивать по обычным топливным системам.
Многим, вероятно, известно, что вещества, плохо проводящие электрический ток (диэлектрики), обладают свойством накапливать заряды статического электричества. Если учесть, что углеводородные топлива – типичные диэлектрики, то становится понятным, как опасно соседство горючих паров топлива с искрой от разряда накопленного статического электричества. Даже очень тщательное заземление резервуаров, цистерн, трубопроводов и заправочного оборудования полностью не устраняет накопления зарядов. Специалистам пришлось и здесь обратиться к так называемым антистатическим присадкам. Благодаря их применению удалось значительно уменьшить пожарную опасность топлива.
Основательно поработала химия над совершенствованием нефтяных горюче-смазочных материалов. В гигантских масштабах выросло и продолжает расти потребление нефтепродуктов во всем мире. Для вооруженных сил, подчеркивает зарубежная печать, эта проблема приобретает особую остроту: миллионы тонн разнообразного топлива, необходимого боевым машинам, авиации и кораблям, чрезвычайно усложнили задачу снабжения войск горючим. Подсчеты иностранных специалистов показали, что среднесуточный расход материальных средств пехотной дивизии, например, увеличился по сравнению с периодом второй мировой войны приблизительно в три раза и может составить 1200 тонн, причем около 65 процентов объема тыловых перевозок падает на горюче-смазочные материалы.
В последние годы за рубежом прилагают большие усилия для устранения трудностей в снабжении войск горючим. Этим, в частности, объясняется появление многотопливных двигателей, способных работать с одинаковым успехом на бензине, реактивном и дизельном топливах, с другой стороны, предпринимаются попытки разработать некое универсальное топливо, годное для двигателей разных типов. Однако, даже если удастся создать практически пригодные многотопливные двигатели и многодвигательное топливо, отмечают специалисты, это не снимает главной проблемы – как сократить объем перевозок при снабжении войск горючим.
Прежде всего обратили внимание на громоздкость, неудобство и малую эффективность средств транспортировки и хранения горючего. Ведь основным материалом для изготовления резервуаров, цистерн, бочек и другой тары служит сталь. Замена ее легкими синтетическими материалами из арсеналов достижений современной химии открыла реальные возможности приостановить непрерывное «утяжеление» тыла войск. Наибольшее распространение, указывается в зарубежной печати, синтетические изделия получили в войсковом звене. Это – мягкие резервуары, перекатывающиеся контейнеры, эластичные буксируемые баржи, гибкие трубопроводы.
Мягкие резервуары не только снизили вес тары, но и упростили процесс транспортировки и хранения горюче-смазочных материалов. С их помощью, по существу, любой транспорт: железнодорожные вагоны и платформы, грузовые автомобили и бронетранспортеры, сухогрузные суда и баржи, самолеты и вертолеты – все может быть использовано для доставки топлива. Мягкие резервуары удобны при организации подвижных складов горючего, позволяют хранить топливо под водой. При этом хранилища большой емкости сооружаются легко и быстро, что особенно важно в боевых условиях.
Вот, например, как выглядит мягкий резервуар емкостью 1600 кубометров, изготовленный из нейлоновой ткани с покрытием из синтетической резины. Длина его – 49,4 метра, ширина—14,9 метра, вес оболочки – 1043 килограмма. В скатанном виде это – рулон шириной 4 метра и диаметром 0,9 метра. В рабочем положении резервуар устанавливается в яме глубиной 3,7 метра, которая подготавливается обычными землеройными машинами. Его установка, пишет журнал «Арми информейшн дайджест», требует 200 человеко-часов рабочего времени. Для сравнения можно указать, что сборно-разборный стальной резервуар такой же емкости весит около 38 тонн, в 37 раз больше, и для его установки необходимо в 10 раз больше времени (рис. 15).

Рис. 15. Так выглядят в сопоставлении стальной сборно-разборный резервуар для горючего и мягкий такой же емкости (последний в скатанном виде грузят на автомашину)
Во многих странах для доставки топлива по воде применяют мягкие буксируемые баржи. Их емкость достигает 10 000 кубометров. В отличие от танкеров они обладают очень малой осадкой и поэтому по воде могут быть отбуксированы к необорудованному побережью. В порожнем состоянии они свертываются и доступны для перевозки любым видом транспорта. Существуют буксируемые и по суше резервуары – перекатывающиеся контейнеры. Некоторые зарубежные специалисты указывают, что в ряде случаев для их буксировки можно использовать и боевые машины. Например, танк будет в состоянии сам перевозить дополнительную заправку горючего.
Внедрение синтетики, как видно, в состоянии существенно уменьшить объем перевозок горючего в войсках. Но это, подчеркивают специалисты, тоже не радикальное средство. Вот почему в различных странах все настойчивее ищут способы обеспечить боевые машины более эффективным топливом, занимающим меньший объем и вес, чем существующее, или таким, которое можно получать из дешевого местного сырья.
Одним из направлений этого поиска следует считать попытки использовать в качестве топлива простейшие углеводороды, содержащиеся в нефтяных или природных газах, такие, как метан и пропан. Американские специалисты, например, исследуют возможности применения жидкого метана в качестве топлива для сверхзвуковых самолетов. Главное преимущество жидкого метана по сравнению с обычным реактивным топливом – в его более высокой теплоте сгорания и теплоемкости. Только за счет этого, как полагают, полезная нагрузка транспортного сверхзвукового самолета может быть увеличена почти вдвое. Правда, при этом отмечается, что сжиженный метан значительно дороже керосина, возрастает вес топливной системы самолета, усложняется заправка.
Другой путь поисков – производство углеводородов из заменителей нефтяного сырья: угля, горючих сланцев, битуминозных или нефтяных песков, или синтезом на базе окиси углерода и водорода. Производство такого искусственного жидкого топлива имеет довольно большую историю. Известно, что в фашистской Германии из-за недостатка нефти было освоено промышленное производство бензина методами гидрогенизации угля, а также синтеза на базе окиси углерода и водорода. В Японии времен второй мировой войны получали авиационный бензин из корней сосны. Как говорили в то время японцы, «корней 200 сосновых деревьев достаточно, чтобы самолет мог продержаться в воздухе в течение часа». В июне 1945 года путем переработки корней сосны вырабатывалось около девяти тысяч тонн бензина.
Однако искусственное жидкое топливо из ненефтяного сырья обходилось значительно дороже нефтяного. Поэтому в послевоенные годы в капиталистических странах его производство было сведено до минимума, хотя исследования в этой области не прекращались. В настоящее время, указывает печать, положение изменилось. Достижения химии создали возможность снизить стоимость искусственных жидких углеводородных топлив. Теперь они в состоянии конкурировать по стоимости с нефтяными топливами. Предполагают, что к 1980 году потребление искусственных жидких топлив, получаемых на базе угля, сланцев и битуминозных песков, только в США и Канаде может составить миллионы тонн в год.
Особые надежды возлагают зарубежные специалисты на поиск неуглеводородных видов топлива. Оказалось, что некоторые вещества, например аммиак, обеспечивают при сгорании более полное использование воздуха. Благодаря этому мощность, скажем, танкового дизельного двигателя на аммиаке возрастает на треть. Кроме того, подчеркивается в печати, аммиак можно получать из воздуха и воды непосредственно в районе военных действий.
Однако прежде чем аммиак удастся сделать моторным топливом, предстоит преодолеть немало трудностей. Дело в том, что аммиак – летучее и ядовитое вещество. Чтобы сохранить его в жидком виде при нормальной температуре, необходимо в резервуарах поддерживать давление 14 атмосфер. Большая летучесть аммиака требует специальных дозирующих и впрыскивающих устройств, иначе горючее начнет интенсивно испаряться в системе питания. В довершение ко всему аммиак несовместим со сплавами меди и цинка, многими другими металлами.
Таковы некоторые направления, по которым химия «наступает» на гегемонию нефти среди источников энергии для боевых машин. Как видно, «черному золоту» пока не угрожает серьезная конкуренция, однако бурный прогресс науки и техники наших дней уже не раз вносил существенные поправки в самые, казалось бы, незыблемые представления и Оценки. Не составляют исключения и вопросы обеспечения войск горючим.
Наш рассказ о топливе для войск был бы, однако, неполным, если бы мы ничего не сказали о ракетном топливе. Вести же о нем разговор заставляет то обстоятельство, что топливо это особое. Посмотрим прежде всего, чем оно отличается от привычных для нас видов горючего?
Мы обычно не задумываемся над тем, что для сгорания килограмма горючего в двигателе автомобиля, танка или самолета необходимо почти три килограмма окислителя – кислорода. Силовые установки машин черпают его из окружающей атмосферы. Строго говоря, бензин, керосин, дрова, уголь – это горючие материалы, а не топливо. Топливом они становятся лишь в смеси с кислородом. Вот почему говорят об их зависимости от окружающей среды. Но ведь ракета должна летать и в безвоздушном пространстве, лишенном кислорода. Значит, ей необходимо «возить» с собой и горючее и окислитель. Только вместе они могут служить источником энергии для движения ракеты – стать ракетным топливом. И тогда оно не будет зависеть от окружающей среды, получит способность «гореть» в любых условиях– в атмосфере, в космосе, под водой. Такова первая обязанность ракетного топлива.
С другой стороны, обратим внимание на то, что реактивные самолеты, ракеты не имеют движителя такого, скажем, как колеса у автомобиля, гусеницы у танка или воздушный винт у самолетов и вертолетов. Роль движителя у ракет выполняет реактивная струя выбрасываемых из двигателя газов – продуктов сгорания или разложения топлива. Создание в реактивном или ракетном двигателе струи газов, с большой скоростью вытекающих наружу и образующих необходимую силу тяги, – вторая особенность ракетного топлива.
Таким образом, в отличие от обычных видов горючего ракетное топливо не только источник энергии, но и генератор так называемого рабочего тела, то есть газовой смеси, при помощи которой преобразуется тепловая энергия в механическую. Отсюда и основные требования к ракетному топливу. Оно должно обладать повышенным содержанием энергии, чтобы обеспечивать образование большого количества газов, нагретых до высокой температуры. Чем больше будет выбрасываться газов из сопла ракетного двигателя, чем выше будет их скорость, тем быстрее будет двигаться ракета, тем эффективнее топливо. Существуют ли в природе вещества, отвечающие подобным требованиям?
Вообще говоря, ассортимент материалов для ракетного горючего очень широк. Теоретически применимы почти все элементы периодической системы и их многообразные соединения. Несколько ограниченнее выбор окислителя: кислород, фтор, кислородсодержащие и галоидные соединения, наиболее активные из которых соединения фтора. Одним словом, если число видов ракетного горючего, которые уже испытаны в разных странах, близко к сотне, то число видов окислителя не превышает полутора – двух десятков.
По своему физическому состоянию компоненты ракетных топлив могут быть в нормальных условиях твердыми, жидкими и газообразными. Правда, газообразные компоненты для сокращения занимаемого ими объема сжижаются. Так что их тоже относят к жидким. Твердые окислитель и горючее образуют твердое ракетное топливо, а жидкие – соответственно жидкое. Но существуют и такие варианты, когда окислитель – жидкий, а горючее – твердое, или наоборот. В этом случае ракетное топливо называют гибридным или смешанным. Чем же объяснить такое разнообразие ракетных топлив?