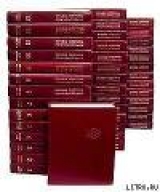
Текст книги "Большая Советская Энциклопедия (ТК)"
Автор книги: Большая Советская Энциклопедия
Жанр:
Энциклопедии
сообщить о нарушении
Текущая страница: 2 (всего у книги 3 страниц)
Ткань текстильная
Ткань тексти'льная, изделие, образованное в процессе ткацкого производства переплетением взаимно перпендикулярных нитей – продольных (основных) и поперечных (уточных). В некоторых случаях применяются дополнительные системы нитей, служащие для образования ворса, узоров и т.п. Наиболее распространённое текстильное изделие вырабатывается в виде полотен или штучных вещей (платки, скатерти и т.п.). Т. т. имеют малую толщину (обычно до 5 мм), значительную ширину (как правило, до 1,5 м, но иногда до 12 м), различную длину. Отрезки ткани, поступающие в торговлю и называемые кусками, обычно имеют длину 20—40 м. Узкие ткани (шириной менее 0,4 м) называют лентами.
Классификация Т. т. может быть выполнена по следующим признакам: волокнистому составу, назначению, а также способам выработки, отделки и расцветки.
Т. т. вырабатывают почти из всех видов волокон текстильных и нитей текстильных. В зависимости от отраслей текстильной промышленности и преобладающего волокнистого состава их подразделяют на хлопчатобумажные, льняные, шерстяные, шёлковые и др. К шёлковым относят Т. т. из волокон химических и натурального шёлка. Выделяют Т. т. однородные (из одного типа волокон или нитей либо с примесью не более 10% других видов); смешанные – из нитей, полученных из нескольких видов волокон; неоднородные – в которых чередуются различные нити. По назначению Т. т. классифицируют на бытовые и технические (см. Ткань техническая). Примерно от общего количества Т. т. составляют бытовые; они подразделяются на одёжные (бельевые, платьевые, костюмные, платки и т.д.), декоративные (мебельные, портьерные и т.д.) и влаговпитывающие (полотенечные и салфеточные). В торговле, кроме того, в отдельные группы выделяют Т. т., вырабатываемые в больших количествах, например ситец,сатин.
Основную массу бытовых Т. т. составляют хлопчатобумажные ткани. Следующими по объёму производства являются шёлковые и льняные. Шерстяные Т. т. подразделяются на камвольные (вырабатываются из тонкой и гладкой, так называемой гребенной пряжи) для пошива платьев, костюмов, пальто и т.п.; тонкосуконные (из более толстой, так называемой аппаратной пряжи) – для пальто и костюмов: грубосуконные (из самой грубой, толстой аппаратной пряжи) – для пальто, одеял и др.
Неотделанные ткани (снимаемые с ткацкого станка) называются суровьём. Из разноцветных нитей вырабатывают пестротканые ткани; из пряжи, полученной из смеси волокон разных цветов, – меланжевые ткани. Помимо гладкой поверхности, ткани могут иметь пушистый наружный слой (ворс). К ворсовым относят ткани с петельным или разрезным (получается при разрезании петель) ворсом, который образуется дополнительной системой нитей, а к ворсованным – ткани, у которых ворс начёсывается из уточных нитей. Сукнаотличаются войлокообразным застилом, закрывающим переплетение нитей. На поверхности ткани могут образовываться рубчики (с помощью утолщённых нитей), рельефные тканые рисунки (см. Жаккарда машина). Многослойные Т. т. вырабатываются из нескольких наложенных друг на друга основ, скрепленных общими уточными нитями.
До поступления к потребителю ткани подвергаются, как правило, отбеливанию,крашению или печатанию (см. Печатание тканей), а также различным видам заключительной отделок тканей. Гладкокрашеными называются ткани, окрашенные в один цвет; набивными – имеющие на лицевой поверхности печатный узор.
Отдельные виды тканей, отличающиеся от других хотя бы одним показателем заправочных данных (толщина нитей, число их на единицу длины и ширины, переплетение и т.д.), обозначаются условными номерами и называются артикулами. Общее число артикулов, вырабатываемых фабриками СССР, составляет около 4000.
Основные характеристики и свойства Т. т. Строение Т. т. характеризуют толщиной нитей [оценивается линейной плотностью, то есть массой (г) 1 км нити], видом переплетения нитей, плотностью ткани, соотношением изогнутости нитей основы и утка (так называемая фаза строения), структурой поверхности (гладкая, ворсовая) и т.п. Свойства и внешний вид Т. т. обусловливаются их строением, свойствами нитей и отделкой.
В СССР Т. т. аттестуют по 3 категориям качества: высшей, первой и второй. Т. т., которым присвоен Государственный знак качества, относят к высшей категории, а ткани, аттестованные второй категорией, подлежат снятию с производства. При аттестации учитывают оформление, структуру и заключительную отделку ткани. Кроме того, категория качества Т. т. определяется показателями качества: поверхностной плотностью (массой 1 м2), усадкой, устойчивостью окраски, степенью белизны, износостойкостью, пиллингуемостью, несминаемостью, механическими свойствами.
Поверхностная плотность характеризует материалоёмкость и косвенно толщину Т. т. Она колеблется от 30 г/м2 (шёлковый креп-шифон) до 1000 г/м2 (брезент, бельтинг и др.); плотность наиболее распространённых платьевых тканей (ситец, сатин и др.) 90—150 г/м2, а костюмных шерстяных – 250—400 г/м2. Усадка Т. т. показывает уменьшение размеров (выражается в % от их начального значения) после стирки, сушки, химчистки, хранения. Величина усадки по основе допускается в пределах 1,5—5%, по утку – 1,5—3,5%. Устойчивость окраски Т. т. проверяют к действию света, светопогоды (совместное действие света и атмосферных условий), стирки, трения и т.д. Её оценивают визуально сравнением испытанных образцов с эталонными. Высший балл оценки устойчивости окраски к действию света и светопогоды – 8, а к другим воздействиям – 5. Степень белизны Т. т. измеряют на специальном приборе (фотометре).
Износостойкость Т. т. к истиранию, стирке, химчистке, светопогоде и др. воздействиям определяют после опытной носки сшитой из тканей одежды, а также на приборах, имитирующих изнашивание при эксплуатации Т. т.; характеризуется уменьшением прочности, выносливости, массы, изменением вязкости раствора, полученного растворением вещества ткани (например, в щёлочи, кислоте), а также др. критериями. Стойкость к истиранию характеризуют числом циклов, вызывающих разрушение Т. т. При истирании на поверхности Т. т. могут образовываться из закатанных кончиков волокон мелкие шарики – пилли. Это свойство (так называемая пиллингуемость) особенно резко проявляется у Т. т., содержащих синтетические волокна. Коэффициент несминаемости определяют углом восстановления согнутого на 180° образца или по изменению размеров искусственно запрессованной складки.
Для оценки механических свойств Т. т. обычно измеряют прочность и удлинение при растяжении до разрыва, усталостные и др. характеристики. Разрывные нагрузки колеблются от 50 н (марля) до 3500 н на 50 мм (брезент, бельтинг); ситец имеет разрывные нагрузки 250—400 н, костюмные шерстяные ткани – 350—600 н. Удлинение выражается разницей между конечной и первоначальной длиной в %.
При оценке гигиеничности Т. т. определяют их способность поглощать водяные пары и воду, капиллярность, воздухо-, водо– и паропроницаемость, теплопроводность и реже электризуемость.
Лит.: Кукин Г. Н., Соловьев А. Н., Текстильное материаловедение, ч. 3, М., 1967; Лабораторный практикум по текстильному материаловедению, М., 1974; Пожидаев Н. Н., Симоненко Д. Ф., Савчук Н. Г., Материалы для одежды, М., 1975.
Г. Н. Кукин, А. Н. Соловьев.
Ткань техническая
Ткань техни'ческая, ткань текстильная, используемая для изготовления деталей машин, установок, сооружений, а также различных технических изделий. Вырабатывается почти из всех видов волокон текстильных и нитей текстильных. В качестве Т. т. могут использоваться и некоторые бытовые ткани (например, марля, миткаль, саржа) для изготовления кальки, прокладок, чехлов и т.п. К Т. т. обычно предъявляются повышенные требования по сравнению с бытовыми. Большинство Т. т. вырабатывают полотняным переплетением нитей (одно– и многослойным), так как оно обеспечивает наиболее прочную связь между основой и утком (см. Ткацкое производство). В некоторых отраслях промышленности Т. т. заменяются синтетическими плёнками. Наибольшее распространение получили кордные, ремнёвые, транспортёрные, рукавные, прессовые и фильтровальные ткани.
Кордная прорезиненная ткань используется для каркасов покрышек шин. Основные нити изготавливают из вискозных, полиамидных и полиэфирных комплексных нитей двойной крутки, в качестве утка применяется хлопчатобумажная пряжа. Плотность нитей по основе значительно больше (до 94 нитей на 100 мм), чем по утку (до 30 на 100 мм). Разрывная нагрузка от 120 до 250 н на 1 нить. Для защиты бортов покрышек от повреждения о закраины обода и для придания им жёсткости и прочности применяются ткани из хлопчатобумажной пряжи или мононитей.
Ремнёвые и транспортёрные ткани используются для изготовления лент конвейерных и ремнейприводных. Плотность этих тканей по основе значительно больше, чем по утку (см. Бельтинг).
Рукавные ткани применяют для передаточных устройств, работающих под давлением или разрежением (пожарные рукава и др.). Вырабатываются из льняных, хлопчатобумажных, комбинированных и синтетических нитей. Рукавные ткани образуют каркас рукава и обеспечивают прочность и стабильность размеров изделия. Изготавливаются на специальных круглых или плоских станках. Основные требование к рукавным тканям – равенство разрывных прочностей и удлинений по основе и по утку. Разрывная нагрузка этих тканей по основе и утку составляет от 1250 до 5000 н на 50 мм. Иногда для изготовления рукавов используют так называемые равнопрочные или кордные ткани.
Прессовые ткани применяют для обтяжки отжимных валов на машинах полиграфической, текстильной и других отраслей промышленности, для прокладок прессов в маслобойной промышленности, для брошюровочно-переплётного производства и т.д. Изготавливают главным образом из шерстяной (технического сукна) или хлопчатобумажной пряжи. Имеют высокую прочность на истирание, гладкую поверхность и нормированную водопроницаем ость.
Фильтровальные ткани служат для улавливания твёрдых частиц из жидкостей, газов и воздуха в химической, угольной, пищевой, целлюлозобумажной, медицинской и других отраслях промышленности. Изготовляются в основном из хлопка, шерсти, льна, асбеста, синтетических волокон и т.д. Разрывная нагрузка тканей должна соответствовать давлению фильтруемой жидкости или газа и поэтому колеблется в широких пределах (от 3 до 15 кн на 50 мм). Большое распространение получили фильтровальные ткани из синтетических волокон, которые обладают исключительной стойкостью к химическим реагентам (щелочам, кислотам, солям) и имеют большую разрывную нагрузку по сравнению с натуральными волокнами.
Помимо перечисленных областей применения, Т. т. используют также для парашютов, оболочек надувных сооружений, тентов (см. Брезент), для гибких ограждений агрегатов на воздушной подушке, в качестве заменителей кожи (см. Кирза), для изготовления сит и т.п.
Лит.: Технические ткани и их применение, М., 1965.
И. П. Хайневский.
Ткацкий станок
Тка'цкий стано'к, вырабатывает из нитей (основы и утка) различные виды тканей текстильных; основная машина ткацкого производства. Классификация Т. с. В зависимости от способа образования ткани станки бывают 2 типов: станки с прерывным образованием ткани (челночные и бесчелночные) и станки с непрерывным многоместным образованием ткани (многозевный Т. с.). По конструкции различают плоские станки и круглые (используют только для выработки специальных тканей, например рукавных). Наиболее распространены плоские челночные станки. В зависимости от используемой пряжи, вида и назначения ткани Т. с. предназначаются для выработки хлопчатобумажных, шёлковых, шерстяных, стеклянных, металлических и др. тканей. Станки могут быть узкими (вырабатывают ткань шириной до 100 см) и широкими, предназначаться для лёгких, средних и тяжёлых тканей. Для переработки утка различных видов (по цвету, крутке и т.д.) применяются многочелночные станки. В зависимости от устройства зевообразовательного механизма станки бывают эксцентриковые (для тканей простых переплетений), кареточные (для мелкоузорчатых тканей) и жаккардовые (для тканей с крупным, сложным узором; см. Жаккарда машина).
Принцип действия Т. с. показан на рис. 1. Основные рабочие органы станка – ремизка,челнок (прокладчик утка') и бёрдо. Нити основы, сматываемые с навоя, огибают направляющий валик (скало) и принимают горизонтальное или наклонное положение. Далее они проходят через отверстия ламелей (см. Ламельный прибор) и через глазки галев ремизок, перемещающих нити основы в вертикальном направлении для образования зева. В зев челноком или прокладчиком утка др. типа вводится уточная нить, которая продвигается (прибивается) к опушке ткани бёрдом, совершающим возвратно-поступательное движение вместе с батаном. У опушки ткани нити основы, переплетаясь с нитью утка, образуют ткань, которая огибает грудницу, вальян, направляющий валик и навивается на товарный валик. Порядок чередования перемещений ремизок обеспечивает изготовление тканей различного переплетения нитей. Число зубьев, приходящихся на единицу длины бёрда, и число нитей, проходящих через просветы между зубьями, обусловливают плотность ткани по основе, а перемещение (отвод) ткани, приходящееся на одну уточную нить, определяет плотность ткани по утку.
На челночных Т. с. уточная нить прокладывается в зеве челноком, который несёт в себе паковку (шпулю) с пряжей и совершает возвратно-поступательное движение со скоростью 10—18 м/сек (в зависимости от ширины станка). Смена шпуль производится автоматически. Масса челнока с уточной паковкой составляет от 0,25 до 5 кг. Переменная скорость движения челнока и его большая масса – основные причины малой производительности челночных Т. с.
Указанные недостатки устранены в бесчелночных Т. с., которые с середины 20 в. стали внедряться в ткацкое производство. На этих станках применяется уточная паковка больших размеров (бобина), которая размещается на станине станка; после каждого продвижения прокладчика утка нить обрезается. В зависимости от способа прокладывания уточной нити различают бесчелночные станки с малогабаритным прокладчиком утка, пневматические, гидравлические, рапирные и пневморапирные. Получили распространение Т. с. с малогабаритным прокладчиком утка. Прокладчик пружинным зажимом захватывает конец уточной нити. сходящей с бобины, и, перемещаясь в направляющей гребёнке, прокладывает нить в зеве со скоростью 23—25 м/сек. Масса прокладчика около 40 г. Производительность такого станка примерно в 2,5 раза выше по сравнению с челночным станком; на нём можно изготовлять ткани из всех видов волокон, а также их смесей; уток может быть 4 видов.
На пневматических и гидравлических Т. с. прокладывание уточной нити, сходящей с бобины, осуществляется струей сжатого воздуха или капельной струей воды. Сжатый воздух подаётся под давлением до 3×105н/м2 (3 кгс/см2); на гидравлических станках капельная струя воды выбрасывается из сопла под давлением 15×105н/м2 (15 кгс/см2). Скорость прокладывания уточной нити на этих станках достигает 35 м/сек. Пневматические станки применяются для изготовления хлопчатобумажных и шёлковых тканей, гидравлические – для изготовления тканей из синтетических нитей (они не смачиваются водой).
На рапирном Т. с. уточная нить вводится в зев захватами, укрепленными на концах стержней (рапир) или гибких металлических лент, которые совершают возвратно-поступательное движение с 2 сторон станка. Рапирные станки применяются в основном для изготовления суконных тканей и тканей с утком различного вида (цвета).
Выпускаются Т. с. с комбинированным (пневматическим и рапирным) способом прокладывания уточной нити в зеве (так называемые пневморапирные станки). На этих станках справа и слева вводятся в зев 2 полые рапиры, которые образуют воздушный канал. В правую рапиру сжатым воздухом под давлением около 0,4×105н/м2 (0,4 кгс/см2) вдувается уточная нить. Одновременно из левой рапиры воздух отсасывается, что обеспечивает большую надёжность продвижения нити в каналах рапир. После прокладывания утка (со скоростью 1820 м/сек) рапиры выходят из зева и бёрдо прибивает уточную нить к опушке ткани.
В многозевных Т. с. (опытные образцы имелись в 1974 в СССР и ЧССР) переплетение нитей выполняется челноками в нескольких участках по ширине основы, т.к. расстояние между челноками значительно меньше ширины ткани (рис. 2).
Ремизка станка состоит из отдельных секций шириной 2—4 см. Эти секции перемещаются независимо друг от друга с помощью кулачкового механизма, образуя так называемый волновой (или ступенчатый) зев. В каждой волне зева движется челнок с уточной нитью. Перемещение челноков происходит с помощью роликов цепного конвейера, расположенного под нитями основы. Прибой каждой уточной нити производится синхронно с движением челнока и может выполняться, например, с помощью дисков, установленных на валу. Между дисками имеются промежутки, в которых проходят нити основы. При вращении вала уточная нить захватывается дисками и прижимается к опушке ткани. Зарядка челноков осуществляется мотальными головками, которые после выхода челнока из работы наматывают на его катушку нить длиной на одну прокладку. Скорость движения челноков 2 м/сек.
Дальнейшее совершенствование Т. с. направлено в основном на повышение скорости прокладывания утка и, следовательно, скорости работы станка. Перспективно широкое использование многозевных Т. с.
Лит.: Сидоров Ю. П., Кокорев В. А., Пневматические П-105 и гидравлические Г-1055 ткацкие станки, М., 1962; Топилин А. П., Казуров А. А., Янпольский В. А., Высокопроизводительные автоматические ткацкие станки типа СТБ, М., 1969; Пневморапирные ткацкие станки, М., 1974.
В. Н. Полетаев.

Рис. 2. Многозевный ткацкий станок.

Рис. 1. Принципиальная схема образования ткани на ткацком станке: 1 – навой; 2 – нити основы; 3 – скало; 4 – ламели; 5 – вершник; 6 – бёрдо; 7 – челнок; 8 – грудница; 9 – направляющий валик; 10 – вальян; 11 – товарный валик; 12 – подбатанный вал; 13 – лопасть батана; 14 – ремизка; 15 – глазок галева; 16 – батан.
Ткацкое производство
Тка'цкое произво'дство, совокупность технологических процессов, необходимых для изготовления суровых (неотделанных) тканей текстильных. Иногда Т. п. называют ткачеством. В зависимости от вида перерабатываемого сырья (волокон, нитей) различают хлопко-, шерсто-, шёлко-, льноткачество и т.п.
Историческая справка. Ткачество, как и прядение, возникло в эпоху неолита и широко распространилось при первобытнообщинном строе. Ручной ткацкий станок с вертикальным расположением основы появился примерно за 5—6 тыс. лет до н. э. Изобретение ткацкого станка Ф. Энгельс считал одним из важнейших достижений человека на первой ступени его развития (см. К. Маркс и Ф. Энгельс, Соч., 2 изд., т. 21, с. 161). В феодальный период совершенствуется конструкция ткацкого станка, создаются приспособления для подготовки пряжи к ткачеству. Первые попытки механизации процесса ткачества относятся к 16—18 вв. Среди них наибольшее значение имело изобретение Дж. Кеем в 1733 так называемого самолётного челнока. В конце 18 в. в Великобритании Э. Картрайтом был изобретён механический ткацкий станок, в конструкцию которого в дальнейшем вносились различные усовершенствования (главным образом в Великобритании): приёмный товарный механизм (Р. Миллер, 1796), ремизо-подъёмные устройства (Дж. Тодд, 1803), механизм координации движения основного навоя и товарного валика (Р. Роберте, 1822) и др. В 1833 в Северной Америке была изобретена самодействующая шпарутка (устройство для растяжения ткани у опушки).
Существенный вклад в совершенствование конструкции ткацкого станка внесли и русские изобретатели: Д. С. Лепёшкин, запатентовавший в 1844 механический самоостанов при обрыве уточной нити; С. Петров, предложивший в 1853 наиболее совершенную систему боевого механизма для прокладки челнока, и др. В кон. 19 и начале 20 вв. были созданы станки с автоматической сменой челноков. Наиболее удачное решение проблемы автоматической смены уточной шпули в челноке принадлежит англичанину Дж. Нортропу (1890). Однако челночные ткацкие станки имеют существенные недостатки: малый размер уточной паковки; свободный, с большими ускорениями полёт челнока через зев; одновременная прокладка лишь одной уточной нити и др.
В начале 20 в. появилось несколько конструкций бесчелночных станков, в которых уточная нить сматывалась с больших неподвижных паковок и особыми механическими устройствами прокладывалась в зеве. Станки этого типа создали в 1926 Габлер (Германия), советский инженер В. Е. Леонтьев в 1936 и др. В 1927 С. А. Дынник (СССР) предложил конструкцию многозевного круглого ткацкого станка; в 1949 В. А. Прозоровым (СССР) был создан плоский многозевный станок.
Технология Т. п. В соответствии с технологическим процессом изготовления тканей Т. п. состоит из подготовительных операций, собственно ткачества и заключительных операций. К подготовительным операциям относятся перематывание нитей основы и утка, снование, шлихтование, пробирание основы и связывание концов нитей. Цель подготовительных операций – создание паковок нитей основы и утка, пригодных для работы на ткацком станке. Перематывание нитей основы обычно производится с прядильных початков на конические бобины крестовой намотки (реже на катушки), необходимые для следующей операции – снования. Перематывание осуществляется на мотальных машинах и мотальных автоматах. Если прядильные паковки удовлетворяют требованиям процесса снования, то перематывание исключают. При сновании нити с большого числа бобин или катушек (до 1000 нитей) навивают на сновальный валик. Процесс осуществляется на сновальных машинах. Шлихтование основы (пропитка клейким коллоидным раствором – шлихтой) повышает выносливость нитей и сопротивляемость истиранию и многократному растяжению их при ткачестве. Пробирание нитей основы в ламели необходимо для автоматического останова станка при обрыве нити; в глазки галев ремизок нити продеваются для образования зева на станке (пространство для движения челнока) и получения ткани заданного переплетения (см.Переплетение нитей). Пробирание нитей в зубья бёрда обеспечивает прибой уточной нити к опушке ткани и получение необходимой плотности ткани по основе.
Перематывание утка на шпули для челночных станков производится на уточно-перемоточных автоматах. Для бесчелночных ткацких станков используется бобина с мотальных или непосредственно с прядильных машин. Уточная пряжа часто подвергается дополнительной операции – увлажнению (либо эмульсированию, запариванию) для сматывания её без так называемых слётов (спадение с паковки нескольких витков).
Для ткачества основа и уток из приготовительного цеха поступают в ткацкий цех для выработки из них ткани. Нити основы в процессе ткачества испытывают большие воздействия рабочих органов станка, чем уточные, поэтому к ним предъявляются повышенные требования по прочности, выносливости и износостойкости. Основа, как правило, изготавливается из лучшего, чем уток, сырья, с более высокой круткой и дополнительно усиливается шлихтованием. Обрывность нитей, особенно основных, – главная причина останова ткацких станков, она ухудшает качество тканей и создаёт отходы пряжи.
Заключительные операции Т. п. – измерение длины ткани на мерильных машинах, чистка и стрижка её (см. Стрижка тканей), контроль качества на браковочных машинах и укладка на складальных машинах. Все заключит. операции осуществляются на поточных линиях, на которых суровая ткань движется непрерывным полотном, сшитым из отдельных кусков ткани. Пороки суровой ткани оцениваются по баллам (порочным единицам), число которых определяет сорт ткани.
Т. п. называют также совокупность ткацкого цеха (цехов), приготовит, цеха и браковочного отдела. Т. п. может быть самостоятельным (обычно называют фабрикой) или входить в состав текстильного комбината, состоящего из прядильного, крутильного, ткацкого и отделочного производств. Оптимальная мощность ткацких фабрик зависит от отрасли промышленности, например хлопчатобумажная фабрика обычно имеет 2—4 тыс. челночных станков или до 2 тыс. бесчелночных, шёлкоткацкая – до 3 тыс. пневматических, камвольно-суконная – до 800 бесчелночных.
Дальнейшее совершенствование Т. п. направлено на механизацию трудоёмких операций и автоматизацию производств. процессов; внедрение бесчелночных и мно-гозевных ткацких станков, разработку на их основе и освоение новых форм организации труда; агрегирование процессов и машин с целью сокращения переходов в подготовке пряжи к ткачеству. См. также Текстильная промышленность.
Лит.: Цейтлин Е. А., Очерки истории текстильной техники, М. – Л., 1940; Рыбаков Б. А., Ремесло древней Руси, [М.], 1948; Канарский Н. Я., Эфрос Б. Е., Будников В. И., Русские люди в развитии текстильной науки, М., 1950; Технология ткачества, т. 1—2, М., 1966—67: Гордеев В. А., Арефьев Г. И., Волков П. В., Ткачество, 3 изд., М., 1970; Проектирование ткацких фабрик, М., 1971.
И. Г. Иоффе, В. Н. Полетаев.