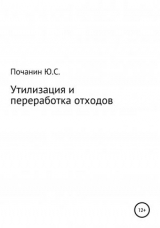
Текст книги "Утилизация и переработка отходов"
Автор книги: Юрий Почанин
Жанр:
Научпоп
сообщить о нарушении
Текущая страница: 3 (всего у книги 4 страниц)
Глава 3. Методы обезвреживания и утилизации токсичных отходов
Все опасные отходы производства характеризуются такими признаками, как: содержание в своем составе вредных для здоровья человека, животных и жизнеспособности растений веществ. Основные источники опасных отходов представлен на рис.3.1.

Рис. 3.1. Основные источники опасных отходов
В России на свалки поступают отходы, в составе которых имеются особенно опасные для здоровья населения: мышьяк, никель, свинец, жидкая или в твердом виде ртуть, а также хром, отходы калия и натрия, и ряд других химически активных веществ. Кроме того, к токсичным отходам также могут отнести лекарственные и фармацевтические препараты, отходы, образуюшие при нефтепереработке, разведке, добыче, хранении, транспортировке нефти и нефтепродуктов, а также при чистке резервуаров, обезвреживании сточных вод, авариях. Значительную токсичность имеют промывочные жидкости, содержащие твердую фазу, дизельное топливо и нефтепродукты, а также поверхностно-активные вещества (ПАВ).
Основными токсическими выбросами и стоками являются:
–соединения фосфора и ртути;
–металлоорганические компоненты;
–сернистые соединения (сероуглерод, сероводород, диоксид серы);
–фториды;
–циановодород;
–оксиды азота;
–производные хлора и непосредственно хлор;
–альдегиды;
–щелочи;
–амины;
–минеральные кислоты;
–органические растворители.
Особенно опасными токсинами являются соединения соли и тяжелых металлов: кадмия, свинца, ртути, хрома и др.
Наиболее экологически опасным канцерогеном является оксид CrO3, содержащий шестивалентный Cr6+, переходящий при нагревании в наиболее устойчивый Cr2O3, содержащий трехвалентный Cr3+. Шестивалентный хром Cr6+ содержится в исходных материалах для производства теплоупоров (природные хромиты, плавленый периклазохромит), в самих шпинелидных теплоупорах, а также в портландцементе, в который Cr6+ диффундирует из шпинелидных футеровок вращающихся цементообжигательных печей.
Выделяют коэффициенты геотоксичности (Тл) химических элементов по геохимическим группам. К супертоксичным (Тл = 15) относят Hg, Cd, Tl, Be, U, Rn, радионуклиды Sr и др.
Высокотоксичными (Тл = 10) являются Pb, Se, Te, As, Sb, B, F, Th, V, Co, Ni, Ru. Опасными (Тл = 5) считаются Cu, Zn, S, Bi, Ag, Ba, Mo, Os, Pt, Yn, Ge, Sr, W, Al, Li, Mn и др. В группу общетоксичных (Тл = 1) входят литофильные элементы Ti, Na, K, Ta, Rb, Ca, Si, Nb. Литофильные элементы– химические элементы, составляющие около 93% массы земной коры и около 97% массы солевого состава океанической воды.
Экологические проблемы решаются двухэтапно:
I этап – ликвидация токсичности отходов и превращение их в безопасные материалы;
II этап – применение множества обычных существующих технологий производства из полученных материалов ценной продукции с широкой областью применения и высокой эффективностью.
Комплекс работ по утилизации отходов представлен на рис.3.2. Все отходы, которые не задействованы в дальнейшей переработке, подлежат утилизации на специально предназначенных для такой цели полигонах огромных площадей, технически оборудованных сооружениями, предотвращающими загрязнение окружающей среды.
Обезвреживание – один из возможных этапов перед утилизацией, если отходы представляют опасность и можно снизить уровень негативного воздействия для окружающей среды.
Рис. 3.2. Комплекс работ по утилизации отходов
Существует несколько способов обезвреживания токсичных промышленных отходов в зависимости от их агрегатного состояния и химического состава.
В качестве обеззараживания отходов перед их утилизацией их подвергают переработке методами, которые можно разделить на следующие группы:
–термические—сжигание в печах различных типов,
–химические—экстрагирование с помощью растворителей, отвердение с применением добавок;
–физические и физико-химические – менять физическую структуру отходов с помощью силового поля, применение специально подобранных реагентов, изменяющих физико-химические свойства, с последующей обработкой на специальном оборудовании;
–биологические – микробиологическое разложение в почве непосредственно в местах хранения, биотермическое разложение.
3.1. Термические методы
Сущность термообработки заключается в сжигании горючих отходов или огневой обработке негорючих отходов высокотемпературными (более 1000°С) продуктами сгорания топлива. Эффективными считаются термические методы, при которых основным является тепловое воздействие (нагревание или окисление):
–термообработка отходов;
–уничтожение с помощью ИК-нагрева;
–уничтожение в высокоэффективном электрическом реакторе (fluid wall destruction);
–сжигание в кипящем слое (fluidized bed system);
–пиролиз;
–окисление суперкритической водой.
Аппараты для огневого обезвреживания и переработки отходов включают в себя: слоевые топки, барабанные вращающиеся печи, многоподовые печи, камерные печи, шахтные печи, топки котельных агрегатов, реакторы с псевдоожиженном (кипящим) слоем, пенно-барботажные реакторы рис.3.3.

Рис. 3.3. Некоторое оборудование для сжигания твердых отходов
В зависимости от типа отходов и способа обезвреживания огневой метод подразделяют на три типа: сжигание отходов, огневой окислительный метод, огневой восстановительный метод.
Сжигание отходов, способных гореть самостоятельно (горючих отходов), – наиболее простой и надежный метод их обезвреживания. Для обеспечения устойчивого процесса горения сжигание отходов проводится при температуре отходящих газов 1200-1300°С. Данный метод обеспечивает получение ценной продукции: отбеливающая земля, активированный уголь, известь, сода и др. Химический состав промышленных отходов определяет содержание дымовых газов (SOХ, P, N2, H2SO4, HC1), соли щелочных и щелочноземельных элементов плюс инертные газы.
Огневой окислительный метод обезвреживания негорючих отходов заключается в том, что их вводят в поток высокотемпературных продуктов сгорания топлива. При смешении газообразного отхода с дымовыми газами происходит его нагрев и окисление горючих компонентов за счет кислорода дымовых газов или кислорода, содержащегося в отходах. Токсичные компоненты подвергаются окислению, термическому разложения и другим химическим превращениям с образованием безвредных газов (С02, Н20, N2) и твердых остатков (оксидов металлов, солей).
Огневой восстановительный метод отличается от огневого окислительного проведением процесса обезвреживания (или только стадии огневой обработки) происходит в восстановительной среде (при отсутствии свободного кислорода в печной атмосфере). Данный метод используется для уничтожения токсичных отходов без получения каких-либо побочных продуктов, пригодных для дальнейшего использования в качестве сырья или товарных продуктов. В результате образуются безвредные дымовые газы и стерильный шлак, сбрасываемый в отвал. Так можно обезвреживать газообразные и твердые выбросы, бытовые отходы и некоторые другие.
Чтобы достичь хорошей степени разложения промышленных отходов, особенно галоидосодержащих, печь, предназначенная для сжигания продуктов, должна обеспечивать необходимое время их нахождения в зоне горения, хорошее перемешивание реагентов с кислородом при определенной температуре. Количество кислорода регулируется, чтобы не образовывались галогены, а полностью переходили в галогеноводороды, необходимо избыточное количество воды и как можно меньше кислорода, чтобы образовывалось меньше сажи.
Недостаток метода заключается в необходимости предварительной сортировки отходов. Они не должны содержать в своем составе соединения фосфора, галогенов и серы. В противном случае в процессе горения, а также в результате неполного сгорания будут образовываться высокотоксичные канцерогенные газовые выбросы, содержащие диоксины и фураны.
Диоксины и фураны-две структурно близкие группы полихлор органических веществ. Среди них выделяют 7 диоксинов, обладающих особенно высокой токсичностью и 10 фуранов, свойства которых близки диоксинам. Эти вещества относят к стойким органическим загрязнителям, обладают высокой стабильностью и длительным периодом полураспада, для диоксинов он составляет 7-11 лет.
Для образования диоксинов необходимо сочетание трех условий: наличие органического углерода, наличие хлорорганических соединений и температура выше 450°С.
При нагревании хлор– и бромсодержащих органических веществ диоксины образуются в интервале температур 500-1200°С, причем максимум их образования приходится на 600-800°С.
Из общего количества хлора, который имеется в ТКО, около 50% содержится в пластмассе, до 25% в целлюлозно-бумажной продукции, а остальное в резине и других материалах.
Основным мероприятием для подавления выделения диоксинов является уменьшение выбросов органического углерода, то есть обеспечение полного его выгорания, а также контроль уровня СО как основного показателя полноты сжигания и остаточной концентрации диоксинов.
Диоксины обладают высокой термостойкостью. Эффективное разложение этих веществ происходит только при температурах выше 1250°С и выдержке в зоне обработки более 2с. Их терморазложение при меньших температурах является обратимым процессом. При охлаждении дымовых газов до 200-450°С они синтезируются вновь. В целях предотвращения образования вторичных диоксинов в зоне охлаждения отходящих газов установок по сжиганию время пребывания в интервале температур 200-450°С должно быть не более 1 с.
Эффективным является сжигание отходов в стационарной и передвижной вращающейся печи. Печи вращаются со скоростью от 0,05 до 2 об/мин. Со стороны загрузки подают отходы, воздух и топливо, а шлак и золу выгружают с противоположного конца печи. В первой части печи отходы подсушивают, обычно при температуре 400°С, после чего происходят их газификация и последующее сжигание при температуре 900–1000°С.
Следует уделить несколько слов методу газификации, используемому для переработки отходов. Цель данного метода: получение горючего газа, смолы, шлака. Газификация представляет собой термохимический процесс, осуществляемый при высоких температурах. При данном процессе органическая масса взаимодействует с газифицирующими агентами, превращая при этом органические продукты в горючие газы. Газифицирующими агентами являются воздух, кислород, водяной пар, диоксид углерода, их смеси. Процесс газификации проходит в механизированных газогенераторах шахтного типа. При этом применяется дутьё: воздушное, паровоздушное и парокислородное. Преимущества газификации перед сжиганием состоят в следующем:
–использование образовавшихся горючих газов как топливо;
–использование образовавшихся смол в качестве топлива или химического сырья;
–снижаются уровни выбросов золы и сернистых соединений в воздух.
Недостатки газификации:
–при использовании воздушного и паровоздушного дутья образуется генераторный газ с низкой характеристикой теплоты сгорания, непригодный для транспортировки;
–невозможна переработка отходов крупных размеров пастообразного типа, перерабатываются только отходы дробленые и сыпучие с газопроницаемыми характеристиками.
При использовании парокислородной газификации образуется газ с хорошей характеристикой по теплоте сгорания, что дает возможность транспортировать его на большие расстояния.
В инсинераторе, действующем по принципу термической обработки в кипящем слое твердых, жидких и газообразных вредных отходов, происходит высокотемпературное окисление органических веществ струей воздуха в контролируемых условиях. Кипящий слой обеспечивается прокачиванием воздуха через твердый материал на днище первичной камеры – песок, алюминий, карбонат натрия, известь, оксиды железа, почву, специальные катализаторы и т.д. Технически опробовано несколько модификаций установки, в том числе в двухкамерном и циркуляционном вариантах. Температура обычно от 450 до 980°С и более, время пребывания в зоне обработки составляет 2 с для газов, 12-14 с для жидких и до 30 мин – для твердых отходов. Предусматривается тщательная очистка отходящих газов.
В реакторах, имеющих внутренний обогрев (вертикальные шахтного типа, с псевдоожиженным слоем, барабанные вращающегося типа), в качестве теплоносителя применяют газы, но после их нагрева до 600—900°С. Эти газы не вступают в химическую реакцию с отходами (инертные и горючие газы без кислорода). Лучше всего, если при этом газ циркулирующий.
Недостатком данного оборудования считается то, что в реакторе, имеющем внутренний обогрев, в связи с применением газообразных теплоносителей увеличивается запыленность газа. Однако, внутренний обогрев конвекцией делает процесс интенсивным, позволяет уменьшить габариты реакторов в сравнении с реакторами, имеющими внешний обогрев.
В инсинераторе, действующем по принципу жидкостной инжекции (liquid injection), подача токсичных отходов в первичную камеру сгорания осуществляется с помощью насоса. Поэтому его применяют при обеззараживании жидких и не очень вязких отходов, а также некоторых взвесей. Температура в первичной камере может изменяться от 650 до 1750°С, в зависимости от характера уничтожаемых отходов, а время обработки – от 0,5 до 2 с. Производительность установок составляет обычно 7-10 т/ч. Установка была разработана фирмой «Дженерал Электрик» («General Electric») для уничтожения ПХБ, и эффективность обеззараживания в этом процессе достигает 99,9999%. Инсинератор, действующий по принципу жидкостной инжекции, неоднократно использовался также для уничтожения диоксинсодержащих отходов.
Способ разрушения органических веществ расплавами, главным образом карбонатами натрия и калия, с одновременной продувкой воздухом известен с 1969 г. и использовался первоначально для газификации угля. Соответствующая установка для термохимической обработки высокотоксичных отходов создана фирмой «Рокуэлл» («Rockwell International Corporation, США). Быстрота разрушения обеспечивается высокой скоростью теплопередачи от расплавленной соли к отходам. Углеводороды окисляются до углекислого газа и воды. Атомы хлора хлорорганических веществ поглощаются расплавом. Преимущество процесса – сравнительно низкая температура (порядка 800-1000°С) и отсутствие в выбросах оксидов азота. Обрабатываться могут как твердые, так и жидкие отходы с низким содержанием воды и золы. Эффективность разрушения продемонстрирована на отравляющих веществах и гербицидах. Примеси высокотоксичного диоксина разрушаются на 99,96-99,98%.
Фирма НУКЕМ (NUKEM GmbH, Германия) разработала процесс дехлорирования в атмосфере инертного газа при 600-800°С с использованием оксида кальция, фиксированного на силикагеле. Процесс происходит в электрическом реакторе с механическим перемешиванием. Время удержания хлор ароматических соединений в реакторе от 10 до 20 с. ОХДД и ОХДФ разрушаются больше чем на 99,99%.
В установке фирмы «Detox International» (США) для термической обработки газов от нагрева отходов, содержащих ПХБ, ПХДД и ПХДФ (диоксины и фураны), использован реактор с циркулирующим расплавленным алюминием (730°С). Отходы нагреваются в печи в атмосфере азота. Экзотермическая реакция токсичных газов и алюминия поддерживает температуру реактора постоянной и приводит к образованию солей и оксидов (AlCl3, Al2O3 и т.д.). Последние поднимаются на поверхность расплава и удаляются из реактора. Поскольку органические отходы не сжигаются, а химически преобразуются, метод менее энергоемок по сравнению с чисто термическим.
Фирмой «Ширко» (США) создана передвижная установка для обеззараживания отходов с помощью ИК-нагрева. Процесс предусматривает двукратную обработку. Вначале отходы поступают в первичную камеру сжигания, выполненную из углеродистой стали и выложенную несколькими слоями керамического покрытия. Они подвергаются мощному ИК-облучению электрически нагретых нагревательных элементов из карбида кремния, смонтированных над конвейером (температура от 500 до 1050°С). Отходы перемешивают, а время их тепловой обработки составляет от 10 до 120 мин, в зависимости от характера уничтожаемых отходов. Улетучивающиеся органические вещества дожигаются с помощью повторного ИК-нагрева до 1260°С, комбинированного со сжиганием в пропановом пламени (время удержания <2,2 с). Выделяющиеся газы пропускаются через влажный скруббер для отделения твердых частиц. Сконструировано несколько вариантов установки, в том числе мобильный, смонтированный на 5 трайлерах (производительность до 680 кг/ч). В газовых выбросах установки диоксины не обнаружены (эффективность обеззараживания – 99,9999%).
Следующий метод термического обезвреживания промышленных отходов – пиролиз. Схема работы пиролизной установки представлена на рис.3.4.

Рис.3.4. Схема работы пиролизной установки
Существует два различных процесса пиролиза промышленных отходов: окислительный и сухой пиролиз.
Окислительный пиролиз является процессом термического распада отходов промышленности, при котором они частично сжигаются или непосредственно контактируют с продуктами сгорания топлива. Этот способ термического обезвреживания применяется для многих отходов, «неудобных» для сжигания или газификации. Это отходы вязкого или пастообразного состояния, влажные осадки, пластмассы, шламы с большим количеством золы, земля с большим количеством примеси мазута, масла и других соединений, отходы, которые сильно пылят.
Сухой пиролиз представляет собой также процесс термического разложения отходов, но без доступа кислорода. Вследствие данного процесса образуется пиролизный газ, имеющий высокую теплоту сгорания, продукт в жидком виде и углеродистый остаток в твердом состоянии. Данный способ термической обработки отходов высокоэффективно обезвреживает их и позволяет применять как топливо и химическое сырьё. Это способствует развитию малоотходных и безотходных технологий, рациональному применению природных ресурсов.
Способ обработки отходов методом сухого пиролиза приобретает все большее распространение. Сегодня это чуть ли не самый перспективный способ утилизации твердых отходов органического содержания, для которого характерно выделение ценных компонентов из данных отходов.
Различают низкотемпературный (450-550°С), среднетемпературный (макс. 800°С) и высокотемпературный пиролиз (900°С– 1050°С) в зависимости от температуры, при которой протекает процесс.
Процесс пиролиза отходов осуществляется в реакторах, имеющих внешний и внутренний обогрев. Внешний тип обогрева применяют в реакторах, имеющих исполнение в виде вертикальных реторт, или в барабанных реакторах вращающегося типа. В реакторах пиролизные газы не разбавляются теплоносителями, сохраняя за счет этого высокую характеристику теплоты сгорания. Газ, получаемый в реакторе с внешним типом обогрева, содержит минимум пыли, ибо он не перемешивается с газовым теплоносителем, что является положительным моментом данного оборудования. Обычно теплоноситель пропускается через слой отходов с содержанием мелкодисперсных частиц.
Разрушение органических компонент высокотоксичных отходов, достигаемое вместо окисления электрическим пиролизом, заложено, в частности, в конструкцию усовершенствованного электрического реактора фирмы «Хубер» (США). Реактор представляет собой вертикальную электрическую камеру из пористого графита, вокруг которой установлены стержневые электронагреватели, а вся система термоизолирована. Энергия излучается электрически нагретыми угольными электродами и передается на обрабатываемые отходы через пористый каркас реактора. Для предотвращения контакта обрабатываемых отходов со стенками реактора в него через поры графита непрерывно подается инертный газ (азот). Температура в зоне термообработки поддерживается на уровне 2200-2500°С, время обработки – миллисекунды. Отходы из первой камеры направляются в две последовательно размещенные камеры дожигания (температуры 1370 и 540°С соответственно), после чего твердые отходы поступают в контейнер, а газы – на дополнительную очистку в циклоне и в адсорбере с активированным углем. Разработаны стационарный и подвижный варианты установки производительностью 20-50 тыс. т в год по ПХБ-содержащим отходам. ПХБ -полихлорированные бифенилы–класс химических ароматических соединений, содержащих в молекуле от одного до десяти атомов хлора. Основные продукты, образующиеся при обработке почв, зараженных диоксинами, – водород, хлор и HCl. В установке могут обрабатываться только материалы, однородные по фазе (не шламы). Эффективность обеззараживания от: ПХБ – 99,9999%; диоксинов —>99,999%.
Следующее направление, основанное на применении низкотемпературной плазмы, используется при утилизации опасных отходов. Плазмотермическая технология предназначена для обезвреживания твердых промышленных и бытовых отходов любой степени опасности.
Принцип работы плазмотрона и его конструкция довольно просты и состоят в следующем: сам процесс с применяемой технологией происходит в камере с двумя электродами: катодом и анодом. Они, как правило, изготавливаются из меди, иногда бывают полые. При определенном давлении в камеру загружаются отходы, кислород и топливо в заранее установленных объёмах. Добавляют водяной пар. Можно применять катализаторы. Давление и температура в камере постоянные. Общий принцип плазменной обработки отходов заключается в термическом разложении с неполным окислением под воздействием водяного пара, кислорода воздуха и давления. Чтобы исходное сырье не сгорало, нужно контролировать поступление окислителя – воздуха. На выходе из установки образуется смесь водорода, монооксида углерода с примесями других горючих газов. Получаемый синтез газ служит топливом для электростанций, сырьем для получения метанола и высших спиртов, аммиака, азотных удобрений, синтетического моторного масла и горючего, рис.3.5.

Рис.3.5. Продукты плазменной переработки отходов
Плазменная переработка отходов с электродуговым плазмотроном представлена на рис. 3.6.
Рис.3.6. Схема с электродуговым плазмотроном
Твердые бытовые отходы при этой технологии обрабатываются потоком плазмы с температурой 1200ºС и выше. При такой температуре смолы не образуются, а токсичные отходы разрушаются.
Перед началом плазменной переработки бытовые отходы предварительно готовятся и измельчаются, после чего загружаются в приемный бункер. Оттуда сырье посредством шнекового загрузочного устройства поступает в непосредственно в реактор. Там отходы движутся сверху вниз, поочередно проходя этапы сушки и пиролиза. Необходимая температура протекания процесса поддерживается за счет работы плазмотрона, который получает питание от электрической сети. Энергия электрической дуги плазмотрона превращает газ в плазму с высокой теплопроводностью и теплоемкостью. Проходя через плазму, органические соединения распадаются на углекислый газ, водяной пар, азот, водород, моноксид углерода и водяной пар. Образовавшаяся газовая смесь поступает в верхнюю часть реактора, где отдает свое тепло твердым отходам. За счет этого и происходит их термодеструкция. Для накапливания шлака предназначена нижняя часть реактора. Обычно там он находится в виде расплава и должен периодически удаляться специальным устройством.
Обезвреживание отходов плазменным методом может выполняться двумя путями:
–посредством ликвидации особо опасных высокой токсичности отходов плазмохимическим методом;
–переработка отходов плазмохимическим методом, чтобы получить товарный продукт.
Разложения в плазмотроне вредных продуктов (полихлорбифенилов, метил бромидов, фенилртутьацетатов, хлор-и фторсодержащих пестицидов, поли ароматических красителей) происходит почти полностью. В результате разложения образовываются CO2, H2O, HC1, HF, P4O10 по следующим технологиям:
–конверсия отходов в воздушной среде,
–конверсия отходов в водной среде,
–конверсия отходов в паровоздушной среде,
–пиролиз отходов при малых концентрациях.
В зависимости от способа переработки отходов можно оптимизировать работу плазмотрона для отходов с разным химическим составом. При использовании плазменного метода для переработки отходов в восстановительной среде получают ценную товарную продукцию:
–из жидких органических хлорсодержащих отходов получают ацетилен, этилен, HC1 и продукты на их основе;
–в плазмотроне с водородом при обработке органических хлор– и фторсодержащих отходов получают газы с содержанием 95 – 98% по массе HC1 и HF.
В целях удобства применяют брикетирование отходов в твердом виде и нагрев пастообразных отходов, чтобы перевести последние в жидкую фазу.
Создано несколько эффективных технологий обеззараживания высокотоксичных жидких отходов методом высокотемпературного пиролиза в пироплазме. В методе, разработанном фирмой «Вестингауз» (Westinghouse Electric Corporation, США), обрабатываемые отходы вводятся непосредственно в плазменную дугу (> 5000°С). Жидкие отходы поступают прямо в плазму. При этом сложные органические молекулы распадаются до атомов (время пребывания в зоне атомизатора порядка 500 мкс), рекомбинирующих в дальнейшем в простейшие молекулы – H2, N2, CO, CO2, HCl, этилен, ацетилен и т.д. (время – около 1 с, температура 900-1200°С). С помощью этой технологии удается обрабатывать не только жидкие отходы, но и 40%-ные тонкие суспензии твердых веществ.