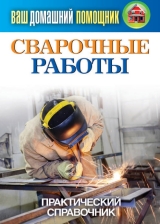
Текст книги "Сварочные работы. Практический справочник"
Автор книги: Сергей Кашин
Жанр:
Хобби и ремесла
сообщить о нарушении
Текущая страница: 4 (всего у книги 11 страниц) [доступный отрывок для чтения: 5 страниц]
Особенности сварки различных материалов
Газовая сварка может быть применена для сваривания различных материалов.
1. Сварка легированной стали. В ее состав входят титан, молибден, хром, никель и др. От присутствия тех или иных легирующих компонентов зависят особенности газовой сварки этого материала.
Горючим газом для хромоникелевой стали является ацетилен (заменитель использовать нельзя). Сварка осуществляется с обязательным применением специальных флюсов. Толщина изделий может быть не более 2 мм.
Готовое изделие следует подвергнуть термической обработке.
Поскольку хромистая сталь подвержена закалке на воздухе, что чревато образованием трещин, при сварке необходимо замедлить остывание сварного шва, для чего готовое изделие продолжают нагревать после завершения сварки.
Высокохромистую сталь не рекомендуют сваривать газовой сваркой, поскольку из-за содержания хрома (более 15 %) усиливается зернистость сварного шва.
Сталь, содержащую молибден, как и хромистую, советуют нагревать перед сваркой (до 300 °C) и после ее окончания.
Особенности газовой сварки легированной стали представлены в табл. 8.
2. Сварка углеродистой стали имеет свои особенности, в частности высокоуглеродистую сталь газовой сварке не подвергают.
Таблица 8
Рекомендации по газовой сварке легированной стали

При сварке среднеуглеродистой стали важно в точности придерживаться температурного режима, а в качестве горючего газа используется только ацетилен. Для газовой сварки низкоуглеродистой стали толщиной до 5 мм флюсы не применяют; используют смесь ацетилена с кислородом; готовое изделие проковывают и постепенно охлаждают; содержание углерода в применяемых присадках должно быть меньше, чем в основном металле.
Режимы газовой сварки данного материала наглядно представлены в табл. 9.
Таблица 9
Примерные режимы для газовой сварки углеродистых сталей

3. Сварка чугуна. Есть несколько разновидностей чугуна, которые в той или иной степени поддаются газовой сварке (белый варится плохо, ковкий – хорошо). Газовая сварка чугуна представлена тремя разновидностями:
✓ с латунным припоем, для осуществления которой требуется доведение температуры материала до 700 °C. При этом применяют ацетилен или пропан-бута-новую смесь;
✓ высокотемпературной, которая предполагает фиксацию детали и предварительный ее подогрев (за 5 минут до сварки) до 400 или 700 °C в зависимости от размера. Применение флюсов является обязательным. Рекомендуется накладывать нижние швы. Сварку ведут нормальным пламенем мощностью примерно 100 л/ч на 1 мм толщины изделия. После сварки металл нагревают с расстояния 50 мм в течение 1 минуты, а потом постепенно охлаждают, накрыв асбестом;
✓ холодной, при которой кромки подготавливают механическим или термическим способом. Топливо – смесь ацетилена с кислородом или заменители ацетилена. При сварке поддерживают нормальное пламя.
Номера и состав флюсов, используемых при сварке чугуна:
№ 1 – плавленая бура (100 %);
№ 2 – прокаленная бура (100 %);
№ 3 – техническая бура (100 %);
№ 4 – прокаленная бура (56 %), углекислый калий и углекислый натрий (по 22 %);
№ 5 – углекислый натрий (50 %), техническая бура (50 %);
№ 6 – натриевая селитра (50 %), углекислый натрий (27 %), плавленая бура (23 %).
4. Сварка меди. Медь при сваривании склонна к сильному окислению, что делает шов недостаточно прочным. Это диктует применение при газовой сварке флюсов, которые предотвращают образование различных дефектов. Состав некоторых флюсов:
№ 1 – прокаленная бура (100 %);
№ 2 – борная кислота (100 %);
№ 3 – прокаленная бура (50 %), борная кислота (50 %);
№ 4 – прокаленная бура (75 %), борная кислота (25 %);
№ 5 – прокаленная бура (50 %), борная кислота (35 %), фосфорный калий (15 %) и др.
При газовой сварке меди необходимо соблюдать следующие условия:
✓ придерживаться определенного порядка при осуществлении технических операций (зачистить кромки, собрать детали под углом в 10° к горизонтали), зафиксировать элементы конструкции, выполнить прихватки;
✓ накладывать однослойные швы; ✓ ограничиваться угловыми и стыковыми соединениями (при сваривании деталей) и в кромку (при ремонте);
✓ готовый шов подвергать проварке;
✓ осуществлять сварку на высокой скорости, чтобы уменьшить время контакта пламени и меди;
✓ применять наконечник на 1–2 размера больше, чем при сварке стали.
5. Сварка бронзы. Газовая сварка применима только к оловянной бронзе (БрАМ, БрОЦ, БрОЦС). Перед сваркой кромки очищают металлической щеткой, после чего V-образно разделывают их под углом в 70–90°. Сварку предпочтительнее вести в нижнем положении. В качестве топлива подходят ацетилен, пропан, бутан и пропан-бутановая смесь. При сварке обязательны обработка кромок и присадки флюсом (БрОЦ, БрОФ).
Температуру детали доводят до 300 °C. Горелку держат под прямым углом к поверхности металла, расплавляя кромки и присадку. Пламя горелки размещают на расстоянии 10 мм от жидкого металла сварочной ванны, которую перемешивают присадочным прутком и вводят флюс. По окончании сварки проводят термообработку изделия.
Технология кислородной резки
Суть кислородной резки заключается в сгорании разрезаемого металла под воздействием струи кислорода и удалении из разреза шлаков, образованием которых неизбежно сопровождается этот процесс (рис. 21).
Углеродистые, а также низколегированные стали режут с помощью исключительно чистого кислорода, а высоколегированные стали, чугун и сплавы меди, помимо кислорода, требуют применения специальных флюсов.

Рис. 21. Схема выполнения газовой резки: 1 – рез; 2 – газовая смесь; 3 – внутренний мундштук; 4 – наружный мундштук; 5 – струя режущего кислорода; 6 – грат (излишек металла)
Резка осуществляется вручную или машинным способом. При этом необходимо обеспечить соблюдение определенных условий:
✓ температура плавления металла должна быть выше температуры, при которой он воспламеняется в кислороде. При нарушении этого условия металл будет расплавляться еще до того, как он начнет гореть в струе кислорода. Низко-и среднеуглеродистые стали удовлетворяют данному условию, поскольку имеют температуру плавления 1500 °C, а для горения в кислороде достаточно довести их до 1300–1350 °C. Повышенное содержание углерода в стали снижает температуру ее плавления и затрудняет резку. То же самое относится к сталям, в которых имеются такие трудно окисляющиеся легирующие элементы, как хром и никель;
✓ температура плавления шлаков должна быть ниже температуры горения металла в кислороде. Кроме того, шлаки должны быть жидкотекучими и без проблем удаляться при воздействии на них давления режущей струи;
✓ в процессе сгорания металла выделяющейся теплоты должно быть достаточно для поддержания горения металла в кислороде;
✓ теплопроводность металла не должна быть чересчур высокой, чтобы не препятствовать поддержанию высокой температуры на кромке разреза.
Перечисленным условиям соответствуют стали, в которых содержание углерода не превышает 0,5 %, хрома – 5 %, марганца – 4 %. Что касается остальных примесей, они не оказывают существенного влияния на процесс резки.
До начала резки сталь нагревают до температуры ее воспламенения в кислороде. От общего количества тепла, необходимого для выполнения резки, приблизительно 54 % идет на доведение температуры стали до температуры воспламенения; 22 % – на нагрев шлака; 24 % – на покрытие потерь.
Для осуществления резки требуется кислород, причем максимально возможной чистоты, поскольку от этого зависит его расход: чем качественнее газ, тем меньше его потребуется. Как правило, для резки используют кислород чистотой 98,5–99,5 %. При снижении этого показателя даже на 1 % падает скорость резки и возрастает расход кислорода.
Кислородная резка бывает двух типов (рис. 22):

Рис. 22. Схема выполнения различных видов резки: а – разделительной; б – поверхностной
✓ разделительная, посредством которой вырезают различные заготовки, раскраивают листовой металл и осуществляют разделку кромок под сварку. Собственно процесс резки состоит в том, что материал вдоль линии предполагаемого реза доводят до температуры его воспламенения в кислороде. Металл сгорает в режущей струе, которая одновременно вытесняет из зоны разреза образующиеся оксиды.
✓ поверхностная. Для этого предназначаются специальные резаки, с помощью которых с металла снимают поверхностный слой. При небольшом угле наклона резака к металлу (15–20°) его поверхностный слой сгорает в кислородной струе, оставляя после себя углубление овального сечения. Для выполнения такой резки скорость истечения кислорода должна быть меньше, а скорость перемещения резака выше, чем при осуществлении разделительной резки. Этот вариант резки используют для удаления трещин, различных пороков сварных швов, литья и проч. Например, резак РАП-62 делает канавку шириной 6–20 мм и глубиной 2–6 мм со скоростью 1–6 пог. м/мин.
При резке изделие подогревается горючими газами – заменителями ацетилена. Обычно это природный, коксовый, нефтяной, пиролизный газ, пропан или пары керосина.
Резка невозможна без специального инструмента – универсального инжекторного резака (рис. 23), основные технические характеристики которого представлены в таб. 9.
Таблица 9
Параметры универсального резака


Рис. 23. Схема устройства инжекторного резака: 1 – головка; 2 – трубка; 3, 4 – вентиль; 5 – кислородный ниппель; 6 – ацетиленовый ниппель; 7 – наружный мундштук; 8 – внутренний мундштук; 9 – инжектор; 10 – кислород; 11 – ацетилен; 12 – горючая смесь; 13 – режущий кислород
В отличие от инжекторной горелки в резаке имеется дополнительная трубка с вентилем, через которую подается режущий кислород.

Рис. 24. Схема устройства мундштуков для кислородной резки: а – щелевой; б – многосопловый; 1 – внутренний; 2 – наружный
Мундштуки резаков бывают двух типов (рис. 24):
✓ щелевыми, состоящими из наружного и внутреннего мундштуков, при смене которых можно регулировать расход газов и мощность подогревающего пламени. В промежуток между ними поступает смесь газов подогревающего металл пламени, а режущий кислород проходит по центральному каналу.
✓ многосопловыми, в которых выход отверстий подогревательного пламени не параллельный, а фокусируется в точке, которая находится примерно в 12 мм от торца. При этом пламя всех выходов ориентировано на одну зону, благодаря чему скорость резки возрастает.
Мундштук – самая главная деталь резака. Для качественной резки необходимо заботиться о герметичности соединений и не допускать прилипания к нему металлических брызг. В связи с этим лучшим материалом для изготовления мундштуков является бронза БрХ0,5. Наличие в ней хрома препятствует оседанию капель металла на поверхности мундштука.
При необходимости переходить от сварки к резке, что нередко требуется при монтажных или ремонтных работах, применяют вставные резаки. По своей конструкции они однотипны, основное отличие заключается в устройстве мундштуков. Вставные резаки подключают к стволу газовой горелки, предварительно сняв сменный наконечник. Вставной универсальный инжекторный резак РГС-70 массой 600 г используют для ручной раздельной резки стали толщиной от 3 до 70 мм.
Резаки бывают малой, средней, а также большой мощности, которые предназначаются для резки металла толщиной 3–100, 100–200 и 200–300 мм соответственно. Последние используют исключительно газы – заменители ацетилена, поскольку имеют большие проходные каналы для них. К каждому резаку прилагается набор мундштуков с номерами от 0 до 6.
При отсутствии горючего газа для кислородной резки применяют пары керосина, и такие устройства называются керосинорезами (рис. 25). В комплект к нему входит бачок для керосина, работающий по тому же принципу, что и садовый опрыскиватель

Рис. 25. Устройство керосинореза РК-71: 1 – гайка крепления головки; 2 – асбестовая набивка; 3 – гайка; 4 – кожух-экран; 5 – трубка-испаритель; 6 – инжекторная трубка; 7 – вентиль
При работе с резаками необходимо соблюдать несколько правил:
1. Перед использованием резака, следует внимательно прочитать прилагающуюся инструкцию.
2. Проверить исправность инструмента, правильность подсоединения всех шлангов, инжекцию в каналах горючих газов и герметичность соединений (при необходимости подтянуть их).
3. Установить рабочее давление ацетилена и кислорода согласно инструкции.
4. Зажечь резак, для чего на четверть оборота открутить кислородный вентиль и создать разряжение в газовых каналах, после чего открыть вентиль подачи газа и зажечь горючую смесь.
5. Прогреть металл (он должен окраситься в соломенный цвет), открыть кислородный вентиль и выполнить рез.
6. В процессе работы надо поддерживать нормальное подогревающее пламя. Для охлаждения мундштука можно использовать воду, при этом следует закрыть только газовый вентиль (кислородный должен быть открыт).
7. Чтобы прекратить резку, надо перекрыть сначала вентиль горючего газа, а потом кислородный.
То, насколько качественным получится рез, зависит от положения резака. При резке стали толщиной 50 мм действуют следующим образом:
1. Разогревают кромку до температуры плавления, направив на нее подогревающее пламя горелки.
2. Держат мундштук строго под прямым углом к поверхности металла, чтобы подогревающее пламя, а потом и струя режущего кислорода были направлены вдоль вертикальной оси листа. Только прогрев металл, открывают кислородную струю.
3. Прорезав металл сначала на всю толщину, резак перемещают вдоль линии реза. При этом угол наклона устройства изменяют на 30° (10–15°, если режут сталь толщиной 100–200 мм) в сторону, противоположную направлению движения, а скорость движения уменьшают.
При резке важно выдерживать ширину разреза, что также свидетельствует о качестве работы. Каждой толщине металла соответствует определенная ширина реза: 5–50 мм – 3–5 мм; 50– 100 мм – 5–6 мм; 100–200 мм – 6–8 мм; 200–300 мм – 8–10 мм.
Если требуется разрезать несколько листов, прибегают к пакетированию (рис. 26), уложив их таким образом, чтобы кромки располагались под углом.

Рис. 26. Газовая резка пакетированных листов стали
Техника безопасности при газовой сварке и резке
Газовая сварка и резка связаны с определенным риском, поэтому при их осуществлении необходимо строго соблюдать правила техники безопасности:
1. До проведения работ надо внимательно прочитать инструкцию по применению оборудования.
2. Эксплуатировать газосварочное и газорезательное оборудование исключительно в течение гарантийного срока, после чего требуется контроль наладчика.
3. Не производить работы рядом с легковоспламеняющимися и огнеопасными материалами.
4. Не оставлять оборудование без присмотра и не передвигать заряженный генератор.
5. Мобильные генераторы ацетилена переставлять, удерживая их в вертикальном положении.
6. Соблюдать грануляцию карбида кальция, рекомендованную инструкцией.
7. По завершении работы сливать воду из ацетиленового генератора.
8. Не применять открытое пламя для отогревания замерзшего ацетиленового генератора.
9. Извлекать остатки карбида только после его полного разложения.
10. Следить за исправностью водяного затвора ацетиленового генератора.
11. Хранить карбид в герметичном виде в емкостях, предназначенных специально для этого.
12. Устанавливать редуктор на газовый баллон осторожно, но плотно.
13. При подаче кислорода вентиль поворачивать медленно.
14. Не снижать давление кислорода на входе в газовую горелку ниже уровня давления горючей смеси.
15. Не работать газовой горелкой без предохранительного клапана.
16. В случае возникновения обратного удара прекратить работу.
17. При осуществлении сварки внутри емкости сварщик должен быть одет соответствующим образом, а также иметь индивидуальные средства защиты и страховочный канат.
Сварочные материалы и оборудование для дуговой сварки
Сварочная проволока
Чтобы заполнить зазор между свариваемыми частями, применяют присадочный материал, который имеет вид прутка или проволоки и вводится в зону сварочной дуги.
Если осуществляется ручная дуговая сварка, то используют плавящиеся электроды, которые представляют собой прутки или стержни с нанесенным на них специальным покрытием (обмазкой). При механизированном процессе электрод имеет вид проволоки, которая намотана на кассету (катушку). Для плавящихся электродов и наплавочных работ применяются различные марки проволоки (табл. 10).
Таблица 10
Марки проволоки, предназначенной для сварки плавящимися электродами и наплавочных работ

Для маркировки сварочной проволоки существует специальное обозначение – индекс «Св», после которого идут цифры и буквы. За каждой из них стоит определенное значение:
✓ индекс «Св» обозначает «сварочная»;
✓ две цифры после индекса – среднее содержание в материале углерода, составляющее сотые доли процента;
✓ буквы – легирующие химические элементы: азот (А), который встречается исключительно в высоколегированной проволоке, марганец (Г), кремний (С), хром (Х), никель (Н), титан (Т), алюминий (Ю), молибден (М), ниобий (Б), цирконий (Ц), бор (Р), вольфрам (В), ванадий (Ф), медь (Д), кобальт (К);
✓ цифры после букв – содержание указанного элемента, составляющее проценты; отсутствие цифры после букв показывает, что содержание данного элемента составляет менее 1 %;
✓ буква А, завершающая маркировку низкоуглеродистой и легированной проволоки, свидетельствует о повышенной чистоте материала по содержанию серы и фосфора; удвоенная буква А в проволоке марки Св-08 АА – о пониженном содержании серы и фосфора относительно проволоки марки Св-08 А.
Например, проволока, имеющая маркировку Св-08 ХГ2 С, расшифровывается так: в состав сварочной проволоки входят углерод (0,08 %), хром (менее 1 %), марганец (до 2 %), кремний (менее 1 %); Св-02 Х19 Н9 – углерод (не более 0,02 %), хром (19 %), никель (9 %).
При всех видах сварки плавлением и для электродов используется стальная сварочная проволока различного диаметра – 0,3, 0,5, 0,8, 1, 1,2, 1,6 2, 2,5, 3, 4, 5, 6, 8, 10 или 12 мм, причем для изготовления электродов для ручной дуговой сварки применяется проволока диаметром 2–6 мм; для автоматизированной и механизированной сварки в среде защитных газов и под флюсом – 0,8–5 мм; для наплавочных работ – от 5 мм.
Стальная наплавочная проволока диаметром 0,3–8 мм изготавливается из стали различных марок – углеродистой (Нп-25, Нп-40 и т. д.); легированной (Нп-40 Г, Нп-30 ХГСА и др.); высоколегированной (Нп-30 Х13 и др.).
Стальная и алюминиевая сварочная проволока отличается от обычной товарной тем, что должна отвечать специальным требованиям, которые изложены в ГОСТах и касаются следующего:
1. Химический состав. По этому признаку марки стальной проволоки подразделяются на три основные группы:
✓ углеродистые. Они используются для сварки низко-, среднеуглеродистых и некоторых низколегированных сталей, например Св-08; Св-08 А; Св-08 АА и др.;
✓ легированные такими элементами, как хром, никель, марганец, титан и др. Допускается 2,5– 10 %-ное данных компонентов. Они предназначаются для сварки низколегированных сталей. В эту группу входит проволока марок Св-08 ГС; Св-08 Г2 С и др.;
✓ высоколегированные (содержание легирующих элементов составляет более 10 %), например Св-06 Х14; Св-02 Х19 Н9 и др.
Всего ГОСТ 2246–70 предусматривает применение 77 марок стальной сварочной проволоки, химический состав некоторых из них представлен в табл. 11.
Таблица 11
Химический состав сварочной проволоки некоторых марок по госту 2246–70


2. Способ и точность изготовления.
3. Упаковка.
4. Транспортировка.
5. Хранение. Проволока реализуется в виде мотков, внутренний диаметр которых составляет 150–750 мм, а масса – 1,5– 40 кг, и бухт, имеющих бирку с указанием выходных данных, в частности завода-изготовителя, маркировки, номера партии, клейма техконтроля. Кроме того, прилагается так называемый сертификат соответствия.
В последние годы для сварки и наплавки стали шире применять порошковую проволоку, имеющую вид свернутой из стальной ленты (20 × 0,2 мм) трубки (для этого используется лента из низкоуглеродистой стали марки 08 КП холодного проката мягкая или особо мягкая), в которую засыпана шихта (порошок) из газо– и шлакообразующих компонентов, благодаря которым значительно улучшаются сварочный процесс и его результат. Сварной шов отличается высокими механическим свойствами, визуально выглядит более аккуратно. Кроме того, снижаются деформации, возрастает глубина проплавления и устраняется разбрызгивание металла при сварке.
Для придания проволоке необходимой жесткости и защиты от смятия подающими роликами при наплавке ее сечение специально делают сложным (рис. 27).
Шихта может иметь различный состав, в частности:
✓ рутиловый;
✓ рутилово-целлюлозный;
✓ рутилово-флюоритный;
✓ карбонатно-флюоритный;
✓ флюоритный (флюорит – это плавиковый шпат CaF2, о котором упоминалось выше).

Рис. 27. Сечение оболочек порошковой проволоки: а – трубчатое; б – трубчатое с нахлестом; в, г – с загибом в оболочке; д – двухслойное
Но при этом она должна быть такой, чтобы сплав, который получится после расплавления оболочки проволоки и порошка и их затвердения, имел бы химический состав и характеристики, требуемые от металла шва.
Порошковая проволока находит применение в следующих случаях:
✓ для сварки открытой дугой;
✓ для сварки под флюсом;
✓ для сварки в защитных газах (в углекислом, инертных);
✓ для наплавки с целью образования твердосплавного слоя.
В строительно-монтажных работах используется порошковая проволока марок ПП-АН1, ПП-АН2 и др.
Порошковая проволока различается диаметром, который может составлять 2,3, 2,5 или 3,2 мм. Как и сварочная проволока, она имеет специальную маркировку, которая расшифровывается следующим образом:
✓ тип проволоки обозначается буквами ПГ (нуждающаяся в дополнительной защите) или ПС (самозащитная);
✓ цифры, следующие за буквами, указывают характеристику прочности металла шва или сварного соединения по гарантируемому пределу прочности;
✓ буквы Н, В, Вх, Ву, Т обозначают допускаемое пространственное положение при выполнении сварки (нижнее и горизонтальное на вертикальной поверхности; вертикальное, нижнее и горизонтальное; горизонтальные швы; вертикальные швы; любые положения, в том числе и кольцевые швы без вращения);
✓ последние цифры указывают на критическую температуру перехода к хрупкому состоянию металла шва, характеризующемуся значениями ударной вязкости менее 35 Дж/см2: 0 – +20 °C; 1–0 °C; 2 —20 °C; 3 —30 °C; 4 —40 °C; <5 —50 °C;
✓ буква Д, присутствующая в обозначении, говорит о том, что требования по температуре не регламентированы, т. е. применение проволоки ограничено исключительно сваркой наиболее неответственных изделий и конструкций, которые предполагается эксплуатировать при положительной температуре окружающего воздуха.
Например, маркировку порошковой проволоки ПС-50-Н2 следует понимать так:
✓ ПС – «проволока самозащитная»;
✓ 50 – минимально гарантируемый предел прочности металла шва или сварного соединения составляет 50 кгс/мм2;
✓ Н – проволока используется для сварки в нижнем положении;
✓ критическая температура —20 °C.
Порошковая проволока должна соответствовать определенным требованиям:
✓ обеспечивать легкое возбуждение сварочной дуги и ее стабильное горение;
✓ плавиться равномерно, с минимальным разбрызгиванием;
✓ образовывать шлак, равномерно покрывающий сварочную ванну и не создающий проблем при отделении его после охлаждения сварного шва;
✓ формировать качественный и прочный сварной шов, т. е. такой, который не имеет пор, трещин и других повреждений и дефектов.
Порошковую проволоку используют при сварке конструкций из углеродистых и низколегированных сталей, которые рассчитаны на средние и тяжелые режимы эксплуатации.