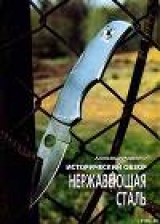
Текст книги "Исторический обзор. Нержавеющая сталь"
Автор книги: Прорез Журнал
Соавторы: Александр Марьянко
Жанр:
Хобби и ремесла
сообщить о нарушении
Текущая страница: 1 (всего у книги 1 страниц)
Александр Марьянко
ИСТОРИЧЕСКИЙ ОБЗОР. НЕРЖАВЕЮЩАЯ СТАЛЬ
Окончательный переход к железу нашими далекими пращурами был, вероятно, омрачен необходимостью изыскания средств борьбы с вездесущей коррозией. Поиски способа создать нержавеющую сталь уходят корнями а глубину веков, но практически до начала XIX-го века человечеству приходилось довольствоваться уходом за сталью, полировкой поверхности и созданием разнообразных защитных слоев и покрытий. Только в 1819 году в ходе экспериментов английских ученых Фарадея и Стодарта был получен первый сплав железа с хромом (феррохром) и была продемонстрирована его повышенная сопротивляемость коррозии. Добавив в фарадеевский феррохром углеродистую сталь, французский ученый Бертье получил первый образец коррозионностойкой стали из которой было отковано несколько клинков. Они выделялись хорошей стойкостью режущей кромки, но не отличались особой антикоррозионной стойкостью в кислотной среде и даже в морской воде. Позже удалось установить, что содержание хрома в тех ножах было менее 3%.
Юлиус Баур запатентовал в Нью-Йорке в 1865 году хромистый сплав, высокие прочностные свойства которого предлагалось использовать на решетках и сейфах. Ножовщики Фредерик Адольф Уилл и Юлиус Финк из Сан-Франциско попытались использовать этот сплав для клинков своих ножей, но они быстро темнели и страдали от питтинговой коррозии. Оказалось, что этот сплав имел 5–7% хрома. В таком количестве хром без легирования никелем вместо замедления коррозии служил катализатором процесса окисления железа. После того, как это было доказано английским металлургом Робертом Хадфилдом в 1892 г., эксперименты с химическим составом нержавеющей стали на некоторое время приостановились.
Эстафету приняли немецкие ученые, которым в начале 20-го века удалось, наконец, получить коррозионностойкую сталь. Независимыми путями шли английский ученый из Шеффилда Гарри Бреали и американец Элвуд Хайнс, чье имя связано с изобретением кобальто-вольфрамового сплава, известного под названием "Стеллит".
Оба установили, что увеличение количества хрома до 11 % в углеродистой стали, даже без никеля, обеспечивало хорошую коррозионную стойкость в ограниченно агрессивной среде. При этом на чистой металлической поверхности возникает характерное для хромистых сплавов пассивное состояние. Это химическое состояние поверхности, наблюдаемое также на благородных металлах, связано с образованием на ней субмикроскопического оксидного слоя, состоящего на нержавеющих сталях из оксида хрома, который и обеспечивает им химическую стойкость. В то же время такую сталь можно было закаливать как обычную, высокоуглеродистую. Это было очень важно, так как более стойкая к воздействию коррозии хромоникелевая сталь закалку не воспринимала. Было установлено, что для достижения требуемых свойств ножевых сталей важны химический состав и термическая обработка. В зависимости от требуемых свойств содержание хрома варьируется и дополняется введением марганца, молибдена и других легирующих элементов.
В 20-х годах нержавеющая сталь заняла доминирующее место на североамериканском и европейском рынке кухонных ножей и столовых приборов. Ножи из нее производились в 30-х годах и в Златоусте. Тем не менее, качество ширпотреба было крайне далеко от того, которое достигалось в лабораториях. Причиной этого был остаточный аустенит – сравнительно мягкая структура, которая в больших количествах образуется в ножах при закалке и сильно отличается от твердого мартенсита, который обеспечивает высокие режущие свойства клинка. В высокохромистых сталях (типа 440C) количество остаточного аустенита после закалки может доходить до 60 % и даже 80 %. Превращать остаточный аустенит в мартенсит научились только в 50-х годах, но за этот срок репутации ножевой нержавеющей стали был надолго нанесен непоправимый ущерб. Решение проблемы было найдено Эмерсоном Кейзом (Case), президентом Robeson Cutlery Co. (Rochester, New York). Ему помогла серия научных работ конца 40-х – начала 50-х годов по исследованию влияния низкотемпературного воздействия на свойства коррозионностойких сталей, используемых в авиации, полярных регионах, в холодильной и химической промышленности.
В результате на свет появился процесс криогенного охлаждения «Frozen Heat» («Замороженое Тепло»). Клинки помещаются в лотки и нагреваются до температуры, незначительно превышающей обычную температуру закалки. После этого они помещают в ванну с закалочной средой (маслом) с температурой 60 °C, где и выдерживаются до того момента, пока не достигнут температуры закалочной среды. Затем клинки очищаются, помещаются плотно в обжимки для исключения коробления и переносятся в охлаждающую камеру, где выдерживаются в твердой углекислоте (-78 °C), либо в жидком азоте (-196 °C), После этого происходит нагрев для снятия остаточных напряжений и охлаждение до комнатной температуры.
В настоящее время этот процесс является обязательной процедурой для всех качественных высокоуглеродистых ножевых сталей, за исключением ширпотреба самого низкого разбора.
Достаточно долго производители использовали, в основном, низкоуглеродистую коррозионностойкую сталь, которая удовлетворяла нуждам домохозяек, но по стойкости режущей кромки не очень устраивала прочие категории пользователей.
Ареной экспериментов сразу стала высокоуглеродистая подшипниковая хромистая сталь 440 класса. Первыми с новым материалом с разным успехом стали работать индивидуалы. К началу 70-х за этой сталью уже прочно закрепилась репутация hi-tech в ножевой индустрии. Фирма Gerber использовала 440C на известной модели ножа Mark II, поставляемой по частным заказам военных во Вьетнам, заменив ею обладающую низкой коррозионной стойкостью сталь L6. Результат эксперимента был, по меньшей мере неоднозначен – не обладая высокой коррозионной стойкостью 440C обладала худшими эксплуатационными качествами в сравнении с L6, что вызвало много нареканий в адрес производителя. В то же время фирма, возглавляемая W. D. «So» Randall, стала активно использовать на клинки 440В.
В 70-х годах поиск новых материалов продолжался. Известным ножовщик Bob Loveless начал активно пропагандировать 154СМ компании Crucible Steel – материал для подшипников, втулок и клапанов двигателей. Совместно с Cold Steel ему удалось даже выпустить серийные ножи элитного класса из этой стали. Позже он представил общественности полный аналог этой стали – более доступную японскую марку ATS-34 от Hitachi.
Именно эти стали – 154CM, ATS-34, 440А, 440В и 440C, – практически до середины 90-х определяли лицо американского ножевого рынка среди малосерийных производителей и частников. С конца 80-х – начала 90-х за широкое применение этих сталей взялись и серийные производители. Ножи среднего класса предлагались в 440А и 440В, а также в их немецких и японских подобиях. Ширпотреб изготавливался из дешевой дальневосточной стали 420J2. Европейский рынок несколько отставал от американского потому, что широкое применение высокоуглеродистых коррозионностойких ножевых сталей началось только в первой половине 90-х. Этот рынок между собой поделили немцы, французы и шведы, причем весьма своеобразно: например, финская компания Marttiini покупает нержавеющую сталь у немцев и французов, а французская Opinel – у шведов из компании Sandvik.
В конце 80-х – начале 90-х годов японские нержавеющие стали окончательно утвердились на североамериканском рынке. Молодые компании, стремительно вторгнувшиеся на ножевой рынок, такие как AIMar Knives, Cold Steel, Spyderco и Benchmade, сделали ставку на ножи именно из них – ATS-34 от Hitachi, G-2 (Gin-1) от Gingami, AUS-6 и AUS-8. И, возможно, не только из-за их эксплуатационных свойств и цен: японский капитал стал играть все более возрастающую роль в развитии ножевой индустрии США. Сегодня модели таких производителей как Beretta (США) и Fallkniven (Швеция) производятся практически полностью из японских коррозионностойких сталей.
Одновременно состоялось и «второе пришествие» 154СМ – производителям ножей предлагается улучшенная версия этой стали в виде удобного для раскроя листового проката. Американская компания Latrobe Steel (Latrobe, PA) вышла на рынок с новой подшипниковой сталью Lescalloy BG42, которую интенсивно пропагандирует модный производитель Крис Рив (Chris Reeve).
Сегодня большинство серийных производителей работают с уже опробованными марками сталей, а новый сортамент, появившийся в последние годы (AUS-10, ATS-55, VG-10, MRS-30 (Япония) и BG-42 (США)), фактически повторяет с теми или иными незначительными улучшениями уже известную ATS-34. Примечательно и то, что такие марки сталей как ATS-55 и VG10 уже не имеют «двойного назначения» – они разрабатывались японскими производителями именно в качестве ножевых. В настоящее время четко прослеживается тенденция на задание более жестких рамок по химическому составу сталей используемых для ножей. Если 440C допускает серьезный разброс элементов по процентному содержанию (например углерода в 0.25 %: от 0,95 % до 1.20 %), то новые стали типа ATS-34, ATS-55, VG10 и пр. за счет использования новых технологий имеют более жесткие рамки нормирования процентного состава – от 0.05 % до 0.1 %. Это позволяет не только подобрать оптимальный режим термообработки, но и гарантирует высокую стабильность конечного результата.
Серьезная разница в свойствах клинков из сталей близкого химического состава у различных производителей объясняется отличием технологических процессов, использованных для их изготовления и окончательной термообработкой клинков.
Наиболее распространенным способом производства сталей являются плавки в электропечах методом кислородного дутья с завершающей обработкой в ковше и вакуумной обработкой. Этим достигается хорошая степень очистки от оксидов, как на популярной отечественной стали 95Х18Ш.
Дальнейшею улучшения свойств удается добиться диффузионным отжигом при высоких температурах, за счет переплава и ряда специальных мер: снижением окончательной температуры прокатки и дополнительными затратами на быстрое охлаждение проката. Так на сталях 154СМ используется метод повышенной очистки от примесей АКД (аргонокислородная декарбюризация), на BG-42 – технологический процесс VIM-VAR – вакуумно-индукционная плавка – вакуумно-дуговая переплавка.
Большое влияние на свойства клинков имеет и распределение карбидов внутри матрицы – неравномерное насыщение матрицы карбидами, также как и карбидная неоднородность (различие размеров карбидов) вызывает неравномерный износ режущей кромки и снижение ее стойкости.
Ячеистость и сетчатость остаются нежелательными неоднородностями, но их полностью избежать нельзя в рамках традиционных способов получения сталей. По этой причине с 70-х годов начал активно развиваться альтернативный способ их получения, призванный решить эту проблему. Он получил название Crucible Particle Metallurgy Processing (CPM). В России материалы, полученные этим способом, известны как аморфные металлические сплавы или металлическое стекло. В ходе него вместо обычного литья в виде болванок, которые далее медленно остывают, расплавленный легированный металл охлаждается на сверхвысоких скоростях, в результате чего вырабатывается быстроостывающий порошок, представляющий собой твердую переохлажденную жидкость. Далее этим порошком заполняют стальной контейнер, который вакуумируется, запечатывается и подвергается горячей изостатической прессовке (HIP) на температурах близких к ковочным для достижения 100 % плотности спекаемого содержимого. Таким образом, удается избежать присущего литым технологиям охрупчивания. Для улучшения механических характеристик аморфных сплавов могут применяться и традиционные методы обработки, такие как ковка и прокат. Высокоуглеродистые нержавеющие с аморфными металлическими сплавами CPM(T)440V (S90V) и CPM420V (S60V) с содержанием углерода свыше 2 % стремительно завоевывают популярность у производителей и потребителей. Однако не только в США работают над перспективными материалами. Аморфные металлические сплавы, имеющие хорошие перспективы в ножевой отрасли, производят в Германии, Швеции, России и, конечно, в Японии. Наиболее перспективными считают японские Cowry X (RT-6) и ZDP-189 с содержанием углерода около 3 %, Cowry Y (СР-4) – 1.2 % углерода и немецкую UHB Elmax с 1.7 % углерода. Развитие технологии вакуумной диффузионной сварки позволило разработать способы изготовления сварочных пакетов из нержавеющих сталей. Фирмы Helle (Норвегия) и Cold Steel (США-Япония) предлагают трехслойные клинки, где на режущую кромку выходит высокоуглеродистая коррозионностойкая сталь с обкладками из высокопрочной низкоуглеродистой нержавеющей стали. Такие производители как Damasteel AB (Швеция) на основе технологии СРМ предлагают коррозионностойкий многослойный пакет – нержавеющую дамасскую сталь.
Тем не менее, и определенное распределение карбидов и даже дендритная ликвация может играть на руку производителю клинков. Американцем Дэвидом Бае производятся клинки из «дендритной стали 440C» путем литья и постепенного остывания заготовки. При этом удается получить кристаллическую хром-карбидную древовидную структуру, близкую по свойствам к легендарным булатам: стойкость режущей кромки клинка резко возрастает – в 3-10 раз в сравнении с аналогичной 440C, полученной традиционным способом. Сходный материал производят в Златоусте под коммерческим названием «Нержавеющий булат». Наиболее популярные марки нержавеющих сталей, используемых для производства клинков. В связи с этим, в практике используют стали с переменным содержанием углерода и хрома: чем выше в стали содержание углерода, тем больше требуется хрома для обеспечения необходимой коррозионной стойкости. Так, если при 0,15 % С необходимо 12…14 % Сr, то при 0,2… 0,4 % С -13…15 % Сr, при 0,6…1,0 % С 14.. 16 % Cr и т. д. В вопросе систематизации всего многообразия ныне применяемых для ножей сталей, целесообразно взять за основу количество углерода и хрома. За основу при этом стоит взять американскую систему стандартов AISL как наиболее представительную.
Следует выделить несколько основных групп:
1. 420:0,15 % С и 12–14 % Cr;
2. 420/425 modified: 0,4–0,5 % С и 13–15 % Cr;
3. 440А: 0.65-0.75 % С и 16.00–18.00 % Cr.
4. 440В: 0.75-0.95 % С и 16.00–18.00 % Cr;
5. 440C: 0.95-1.10 % С и 16.00–18.00 %Cr;
5а.154СМ/АТS-34:1.00-1.05 % С и 14 % Cr;
6. СРМ(Т) 440V: 2.0–2.2 % С и 17.00–18.00 %Cr.
Приближенный транслятор наиболее распространенных в ножевой индустрии марок коррозионностойких сталей.
(см. http: //www. rusknife.newmail.ru/info/5tainls/5nls3.htm)
420
Плохо воспринимают закалку. Стали этой группы отличаются хорошей прочностью и коррозионной стойкостью. Очень легко перетачиваются. Стойкость режущей кромки – слабая.
Традиционно используется на столовые приборы, дешевые кухонные и складные ножи. Производителя прельщает дешевизна и простота в обработке материала.
420/425 modified
(известна также как 420НС – High Carbon)
Закалка на твердость 53-55HRC. Наиболее распространенный материал на кухонные ножи, ножи водолазов, рыбаков и поклонников водного/морского туризма, складные модели среднего класса. Хорошая коррозионная стойкость. Легко перетачивается. Неплохие прочностные свойства. Стойкость режущей кромки – удовлетворительная.
440А
Закалка на твердость 54-57HRC. Очень похожа по свойствам на 425 modified, но обладает лучшей стойкостью режущей кромки. Как правило, материал для нескладных ножей большого и среднего размера, боевых и охотничьих, а также крупных складных.
440В
Закалка на твердость 55-58HRC. Лучшая в сравнении с 440А стойкость режущей кромки. Несколько ухудшенная в сравнении с 440А ударная вязкость. Материал для средних и небольших разделочных, нескладных и складных многофункциональных моделей среднего класса.
440C
Закалка на твердость 56-60HRC Хорошая стойкость режущей кромки в сравнении с прочими сталями 440-го класса, коррозионная стойкость – удовлетворительная, примерно в 2 2.5 раза ниже, чем у 440А. При закалке на HRC60 более склонна к «охрупчиванию» и щерблению. Высокая износостойкость и вызванная этим сложность с переточкой. Материал для дорогих моделей складных и обычных ножей, переживший пик популярности в первой половине 90-х.
154СМ
Закалка на твердость 57-61HRC. Фактически это одна из разновидностей сталей типа 440C с более жестко нормированным химическим составом за счет технологии AOD (аргоно-кислородная декарбюризация). В связи со спросом в настоящее время этот тип нержавеющих сталей выделился в отдельную группу, претендуя на статус самых модных «ножевых» марок в классе сталей на дорогие модели ножей. Достаточно хорошее сочетание режущих и прочностных свойств, удовлетворительная коррозионная стойкость и способность к переточке.
СРМ(Т) 440V
(коммерческое название – S60V)
Закалка на твердость 56-58HRC. Аморфные металлические сплавы (или т. н. металлическое стекло) – сравнительно молодой класс материалов. Сочетание хорошей коррозионной стойкости и удовлетворительных прочностных свойств по сравнению с нержавеющими сталями типа 440C, выработанными по традиционной схеме. Очень хорошие режущие свойства, однако повышенная хрупкость. Удовлетворительная возможность переточки.
Заключение.
Таким образом, можно убедиться, что качество нержавеющей стали, применяемой на клинки, это сложный комплексный параметр. Выбор подходящей марки стали своего рода компромисс, где для достижения ряда высоких свойств всегда приходится чем то жертвовать.
Какие можно дать в связи с этим рекомендации пользователю?
1. Оценивать не только уровень изготовления изделия и марку стали, но и самого производителя, в т. ч. и уровень его технологической оснащенности. Например, испанцы из Nieto, несмотря на перевооружение своей металлургической отрасли в первой половине 80-х, производят клинки из 440C, которые по режущим свойствам и коррозионной стойкости уступают не только аналогам из США и Германии, но даже стали 440А, применяемой SOG (США), которые достигли весьма недурных результатов в работе с ней.
2. Проявлять разумный консерватизм. Многие производители в рекламных целях выходят на рынок с новым продуктом, не дове денным до ума – лишь бы сорвать куш с первых продаж ножей из новой, «эксклюзивной» стали. Причем с рекламациями на качество стали дело обстоит не всегда хорошо, а принимая во внимание специфику России, когда замена брака практически невозможна, лучше 7 раз подумать, прежде чем брать «сырой» продукт.
3. Проявлять стойкость. Схема продаж ножей из новых сталей достаточно хорошо отработана: публикации в периодике о новом ножевом материале (которому может быть уже не первый десяток лет), раскрутка у модного мастера индивидуала, представление на выставке или шоу, preproduction run, и, наконец, появление в продаже за неприличную цену. Если вы не коллекционер, подождите пока ажиотаж спадет, а цены не станут разумными.
4. Не покупать дешевого ширпотреба. 10 дрянных ножей из скверной нержавейки так и останутся 10 скверными ножами – на вашем веку их цена вряд ли возрастет. Уж лучше подкопить и проявив немного терпения приобрести один нож чуть дороже, которым будет удобно работать.
5. Не гнаться за заоблачными значениями твердости. Особенно если у вас проблемы с точкой ножей. Вам же этот нож потом придется перетачивать самому или просить знакомых. А вот отдавать на точку в среднестатистический металлоремонт не рекомендуется – угробят. Даже копеечный китайский.
6. Не требовать от нержавеющей стали тех свойств, которые достижимы только на углеродистых сталях. Она сопротивляется коррозии – это ее плюс. Минусы – хладноломкость, падение вязкости при низких температурах, хорошая режущая способность, как правило, сочетается с хрупкостью и склонностью к трещинообразованию. Это очень капризный материал и с точки зрения ковки и закалки. «Хамон» на нем практически невозможен. Пробовать делать из нее сабли и мечи тоже не стоит.
7. Понимать ограниченность термина «нержавеющая сталь». Проржаветь может все, а особенно – дорогой нож из высокоуглеродистой хромистой стали. Проявите о нем минимум заботы, и он вам послужит верой и правдой долгие годы.
Последние годы ознаменовались интенсивными поисками в области альтернативных материалов, которые бы сохраняли главное достоинство нержавеющей стали – коррозионную стойкость, но были бы лишены ее недостатков, В первую очередь следует отметить кобальтовые и титановые сплавы, гибридную керамику, пластиковые композиты. Однако можно с уверенностью предположить, что в ближайшие десятилетия вряд ли появится материал, который сможет успешно конкурировать с нержавеющей сталью по свойствам и цене.
