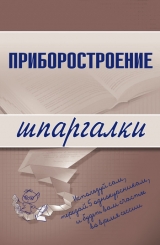
Текст книги "Приборостроение"
Автор книги: Маариф Бабаев
Жанр:
Технические науки
сообщить о нарушении
Текущая страница: 2 (всего у книги 6 страниц) [доступный отрывок для чтения: 2 страниц]
13. Классификация взаимозаменяемости
По степени сопряжения различается:
1. Полная взаимозаменяемость (когда степень сопрягаемости очень высокая) – прочие физические параметры узлов точно соответствуют заданному, а это диктует их соответствие определенной задан-ности, которая ограничена минимальными и максимальными значениями, а последние следуют из эксплуатационных требований, сама граница допуска рассчитывается по теоретико-вероятностному методу, который изложен в предыдущей главе.
Когда взаимозаменяемость полная, то упрощается сборка, растет масштабность кооперации, повышается степень специализации и обеспечения запчастями, а также эффективность производства, в силу более рационального расхода времени, высокого темпа работы.
В итоге становятся возможными конвейерное производство, организация цехов автоматизированных заводов. Все вышеуказанные достоинства этого вида взаимозаменяемости были бы невозможны без соблюдения довольно жестких требований к точности параметров.
2. Исходя из геометрических параметров и учитывая, насколько присоединяемы узлы различают внешнюю взаимозаменяемость, когда речь идет о сравнении наружных и внутренних размеров, и внутреннюю взаимозаменяемость, когда речь идет о том же самом, однако рассматриваются внутренние части узлов и деталей.
3. Функциональная взаимозаменяемость. Имеется в виду взаимозаменяемость узлов, когда, несмотря на различие между ними по некоторым параметрам, это различие не сказывается на выполнении функций, для которых они предназначены.
Само собой разумеется, что задать теоретически границы допуска при функциональной взаимозаменяемости невозможно, это делается эмпирически.
После анализа полученных результатов (степени их влияния на работу установок и механизмов, на эксплу-тационные методы) устанавливают оптимальные допуски на исследуемые параметры. Сами параметры называют функциональными параметрами. Насколько высока роль принципа взаимозаменяемости в производстве изделий машиностроения (приборостроения), говорит срок их службы, т. е. повышая степень взаимозаменяемости, можно увеличить срок службы механизмов и приборов.
Конструктивные требования больше опираются на функциональные параметры, поскольку при этом расходы, а следовательно, и стоимость изделий наименьшие.
Уровень взаимозаменяемости в производстве тех или других узлов зависит от того, насколько трудоемки:
1) изготовление узлов и деталей;
2) изготовление механизмов из этих узлов.
Если взять отношение характеристик трудоемкости и ввести коэффициент взаимозаменяемости КВ, равный этому отношению, KB < 1, поскольку производство узлов и деталей менее трудоемки, чем сборка из них механизмов.
Кв → 1 говорит о высокой рентабельности и эффективности производства, о наименьших потерях в производстве узлов и деталей, а значит, и самих приборов.
14. Взаимозаменяемость по геометрическим и механическим параметрам
Применительно к практике геометрическиепараме-тры называют номинальными. Действительные результаты отличаются от номинальных. В достижении заданной шероховатости поверхности или длины, ширины, высоты, радиуса, может получиться деталь формы совсем другого геометрического тела: в последнем случае называют макроотклонениями поверхности. Эти отклонения характеризуются волнистостью, при этом расстояния между соседними возвышениями, впадинами оказываются больше, чем высота или глубина.
Если эти расстояния меньше, чем высота или глубина, то дефект называют микроотклонениями.
Необходимость повышения качества в производстве предполагает уменьшение отклонения всех порядков. Исходя из этого, требования к обеспечению взаимозаменяемости устанавливают обязательность соблюдения точности по линейным и угловым размерам, геометрической форме поверхности, взаимному расположению поверхностей друг к другу или к осям, волнистости и шероховатости поверхности.
Директивными документами для достижения уменьшения отклонений служат рабочие чертежи, ГОСТы, рекомендации ПСО (международная организация по стандартизации).
Взаимозаменяемость характеризуется и по многим другим параметрам, кроме геометрических, например, по механическим, физическим, пневматическим, гидравлическим, электрическим и другим. Эти виды взаимозаменяемости объединяет то, что они функциональны. Следовательно, требуется однородность изделий, которая предполагает однородность самих исходных материалов и полуфабрикатов.
Механические параметры взаимозаменяемости – это характеристики упругости элементов, которые, в свою очередь, зависят от физико-механических свойств исходного материала, а также от технологии производства этих элементов.
В качестве упругих свойств элементов рассматривается реакция этих элементов на прогиб и раскрутку, последние, как известно из теоретической механики, характеризуются модулем упругости Е и коэффициентом Пуассона М. Допуск на них определяется количеством уравнений, характеризующих систему.
В общем же случае для достижения полной взаимозаменяемости требуется обеспечение наименьшего разброса: любой плавности прогиба или раскрутки упругого элемента к приложенным усилиям; любых приемлемых значений этой плавности; любой остаточной деформации после снятия усилий; гистерезиса: любое несовпадение характеристик при погружении и разгружении упругого элемента и др.
При рассмотрении взаимозаменяемости по другим параметрам, требования примерно такие же.
Небольшим характерным отличием обладает взаимозаменяемость по магнитно-электрическим параметрам. Специфика этих элементов такова, что требуемой величины можно достичь путем различного сочетания тех же магнитно-электрических элементов.
15. Допуски и посадки: их классификация. Допуски и посадки типовых узлов и деталей в приборостроении
Характеристики допуска и посадки – понятия, характеризующие процесс соединения узлов (деталей), т. е. степень приемлемости рассматриваемых узлов для сборки определенного механизма (прибора).
«Посадка»: это разность между линейными размерами отверстия и вала. Когда соединяют два узла цилиндрической формы, то внутренняя поверхность «одеваемого» цилиндра называют охватывающей поверхностью, внешнюю поверхность другого называют охватываемой поверхностью, если поверхность охватывающая, то ее называют отверстием, в противоположном случае – валом. Если, диаметр отверстия больше, чем диаметр вала, то разность диаметров называют зазором. Если же диаметр вала больше – натягом.
В каких пределах возможен зазор и натяг – это определяет допуск, который и обеспечивает требуемую посадку. Допуск – это разность между отклонениями зазора или натяга. Номинальное, то есть расчетное (или заданное) значение зазора находится между этими пограничными значениями. Разность между верхним пределом и номинальным значением называют верхним предельным отклонением, разность с нижним пределом – нижним предельным отклонением. Если взять разность между отклонениями, то получим допуск размера. Именно системой допуска и посадки определяется (устанавливается) класс точности узлов.
Если в расчетах или графически совместить соответствующие границы отверстия и вала, то между верхним и нижним пределами обнаруживается зона, кото-! рую называют полем допуска.
Линия, соответствующая номинальному значению зазора, будет находиться в поле допуска, она называется нулевой линией. Основные типы допусков и посадок:
1. Посадки с полем допуска отверстия находятся над полем допуска вала, может случиться, что нижняя граница поля допуска отверстия совмещается с верхней (скользящие посадки). В этом случае говорят о посадках с зазором, причем зазор обеспечен в режиме соединения.
2. Поле допуска вала находится над полем допуска отверстия. В таком случае говорят о посадке с натягом в соединении.
3. Когда поля допусков отверстия и вала чередуются, то есть имеют место ситуации (1) и (2). В этом случае говорят о переходных посадках.
Допуски и посадки характеризуются предельными зазорами (натягами), когда зазоры (или натяги) в соединяемых деталях не одинаковы, имеет место их разброс между предельными зазорами (натягами). Существуют понятия – наибольший зазор (натяг). Соответственно, наименьший – наименьший зазор (натяг). Разница между предельными значениями зазоров (или натягов) называется допуском посадки.
Не входящие в рассматриваемую систему системы отверстий принимаются равными нулю. Эти нулевые отверстия называются основными отверстиями. Совокупность изменений предельных отклонений при некотором номинальном значении размеров вала составляют содержание класса точности. Причем верхние отклонения валов нулевые, они называются основными валами.
Следует отметить, что все стандарты устанавливаются для эксплуатации КИП при комнатной температуре, то есть при 20 о С.
16.Основные понятия. Теории точности механизмов. Причины ошибок
Движущийся узел некоторого механизма, который приводит в движение другой узел, называют ведущим звеном. Тот узел, который ведущий приводится в движение, называют ведомым звеном.
Точность любого механизма определяется тем, насколько точно соответствуют параметры узлов заданным (или расчетным). Этими и другими вопросами, такими как выявление погрешностей звеньев, влияющих на точность механизмов в целом, занимается теория точности механизмов.
Современная теория точности механизмов состоит из теории механизмов и машин, технологии, метрологии, теории ошибок.
Здесь излагается теория ошибок, ее задачей является: определить пути повышения точности механизмов, суммируя частные погрешности (т. е. погрешности узлов). Теория точности механизмов занята решением двух задач.
1. Прямая задача – трудно решаемая задача. Ее суть состоит в определении соответствия параметров каждого узла техническим требованиям. Эта работа требует согласования большого числа параметров.
2. Обратная задача. При решении этой задачи, главным является соответствие механизма конечному результату.
Характерные ошибки: 1) ошибка положения механизмов. Имеется в виду следующее: если взять два механизма, которые должны совершить некоторое согласованное действие, то несмотря на полное соответствие параметров ведущих звеньев, обнаруживается разница; эта разница и есть искомая ошибка. Эти механизмы можно себе представить как механизм действительный и его теоретический прототип, то есть под ошибкой имеется в виду несоответствие образца теоретическому прототипу;
2) ошибка перемещения механизмов: речь идет о несоответствии параметров ведомых узлов при тех же параметрах ведущих. Только теперь разница в перемещении, а не в положении ведомых узлов;
3) ошибка положения ведомого звена – имеется в виду та же ошибка, что и в (1), только теперь ее причина в неточности ведущих звеньев, последние часто являются последствиями неправильных вводных данных;
4) ошибка перемещения ведомого звена: то же самое, что и ошибка (2), только теперь причина в ведущих звеньях, но по той же причине, что и в (3);
5) ошибка передаточного отношения (имеется в виду разность между действительным ig (у образца) и теоретическим im передаточными отношениями):
6) ошибка линейного передаточного отношения. Аналогично предыдущей ошибке, речь идет о разности между действительным i'g и теоретическим i'm линейными передаточными отношениями
Δi =i'g – i'm
17. Факторы, порождающие ошибки в приборостроении
Классификация факторов:
1) причины, связанные со схемой погрешностей, которые появляются при изготовлении механизмов (т. е. при применении схемы);
2) технологические причины, которые по линейным, т. е. геометрическим размерам разделяются на:
а) ошибки размера – отклонения размеров элементов у образца и теоретического прототипа от номинальной величины, а также ошибки между элементами, которые появляются при перемещении узлов, составляющих пару (кинематические пары);
б) ошибки формы у рабочих поверхностей тех же пар;
в) ошибки во взаимном расположении рабочих поверхностей узлов;
г) отклонения в шероховатости и волнистости от номинальных;
3) ошибки, вызванные силами в самом механизме (это силы деформации, трения, вибрации и прочие, а также воздействие динамических факторов (например, ударно-колебательное движение));
4) ошибки, связанные с нарушением температурного режима эксплуатации механизма, из-за изменения сопротивлений и линейных размеров в узлах;
5) ошибки, связанные с износом механизмов, в этом случае могут появиться любая из предыдущих ошибок или все вместе.
Передаточное отношение – это отношение мгновенных угловых скоростей, что одно и то же с мгновенными угловыми перемещениями звеньев ведомого и ведущего. Пусть угол поворота ведомого звена есть φ1, причем φ2 зависит от угла поворота ведущего звена φ1.Тогда передаточное отношение:

Линейное передаточное отношение: речь идет об отношении мгновенных линейных скоростей (что одно и то же с мгновенными линейными перемещениями) ведомого и ведущего звеньев в механизме. Если эти перемещения соответственно обозначить как V2, V1, то эти отношения:

r1, r2 – радиусы ведущего и ведомого звеньев.
Получили уравнение, связывающее угловое и линейное передаточные отношения.
18. Первичные ошибки механизмов
После разработки конструкторских чертежей начинается реализация этих чертежей. Производитель очень часто отклоняется от чертежа: для него становится важным получение функционального результата.
На поверку «появляется» несоответствие механизма конструкторскому замыслу («теоретическая» ошибка): это несоответствие («теоретическую» ошибку) называют ошибкой схемы.
Методы обнаружения ошибок.
1. Аналитический метод – самый общий и распространенный метод обнаружения ошибок.
Сопоставляются уравнения движения уже имеющегося механизма и его теоретического прототипа. Цель: получить зависимость, которая выражала бы разность движений ведомых узлов в этих механизмах, в зависимости от движения ведущего звена уже произведенного механизма.
Полученная зависимость, являясь функцией от движения ведущего звена, как правило, соответствует искомой ошибке схемы ΔScx:
ΔScx =Sd– Sm,
где Sd Sm – параметры движения ведомых узлов механизма (теоретического и действующего).
В итоге получается функция от ошибок схемы.
Значение погрешности получают, разделив линейное перемещение нарушенного Д Sm ведомого звена на чувствительность измерительного устройства R, и находят ошибку схемы, выраженную в:

2. Экспериментальный метод применяют в том случае, когда использование предыдущего метода становится проблематичным из-за ряда причин, например, из-за плохого знания прибора, или же когда в приборах имеются упругие узлы, не позволяющие установить линейную зависимость между искомыми величинами. В случае обнаружения дефектов подвергают исследованию группы одинаковых приборов (механизмов).
После определения ряда одинаковых параметров, для которых характерны общие по роду отклонения (для этого каждая единица прибора (механизма) исследуется многократно; в одних и тех же точках, где наблюдались отклонения, определяются средние значения параметров для каждой единицы) находят среднее значение для всей исследуемой партии.
После обработки полученных данных удается определить функцию от ошибки схемы прибора (механизма). Достоинством этого метода является следующее: функцию от ошибок схемы находят, например, методом наименьших квадратов, что значит уменьшение влияния ошибок каждого механизма на общую ошибку для всей группы. Если построить кривую для рядов найденных ошибок, то она будет отражать не только искомые ошибки схемы, но и систематические, которые были допущены при изготовлении или сборке приборов.
19. Методы определения первичныхошибок
Первичной ошибкой является неточность геометрической формы рабочих поверхностей узлов (звеньев). Подобными ошибками могут считаться отклонения разного рода: геометрические параметры, связанные с формой и поверхностью узлов, а также с их взаимным расположением.
Кинематическая пара или звено механизма – это два или более элементов механизма, например, ведущий и ведомый узлы. Для их согласованной работы выбираются конкретные параметры, число которых известно из чертежа. При изготовлении узла каждый из этих параметров может получиться несоответствующим данным чертежа, поэтому число первичных ошибок целесообразно взять равным количеству параметров. Учитываются только рабочие, т. е. взаимодействующие поверхности узлов.
Число скалярных первичных ошибок должно быть столько, сколько количество координат.
Рассмотрим примеры.
1. Элемент кинематической пары, оформлен как точка. В системе координат XYZ положение точки характеризуется тремя координатами, по каждой из которых может быть допущено отклонение. Следовательно, число первичных ошибок три уже в скалярной форме.
2. Элемент кинематической пары имеет форму линии, это значит, что число координат в системе XYZ четыре. Число первичных ошибок четыре.
3. Элемент кинематической пары имеет форму плоскости: в этом случае число первичных ошибок не растет и равно трем.
19б В этом случае в числе параметров могут быть и направляющие углы, но общее число первичных ошибок остается неизменным.
Если плоскостей несколько, то число первичных ошибок будет кратно трем: 3n, где n – количество плоскостей.
4. В случае, когда элемент кинематической пары имеет форму сферы, отклонения могут иметь радиус сферы по трем координатам в декартовой (XYZ) системе координат плюс радиус сферы по длине. Число первичных ошибок равно четырем, т. е. равно количеству параметров с возможными отклонениями.
5. Число первичных ошибок может дойти до 11, например элемент кинематической пары, состоящий из цилиндра и двух плоскостей. Поскольку для цилиндра (кругового) число первичных ошибок равно пяти.
6. Если цилиндр не круговой, то число первичных ошибок – шесть.
7. Если взять круговой конус, то число первичных ошибок – семь, для некругового – восемь. В случае усеченного кругового конуса также восемь.
Числа первичных ошибок элемента кинематической пары, суммируясь для каждого звена, в итоге составляют суммарное число первичных ошибок для всего механизма.
20. Исследование точности механизмов
В процессе исследования механизмов анализируются: причины возникновения ошибок, предполагаемые (ожидаемые) величины этих ошибок, методы контроля ошибок и поверки приборов. Все эти вопросы принадлежат метрологии, как неотъемлемой части производства и эксплуатации изделий в «Приборостроении».
Метрология. Основные понятия.
1. Действующая ошибка кинематической пары – так называют результирующая ошибка в формах, размерах элемента кинематической пары, которая проявляется непосредственно в процессе работы, ее невозможно фиксировать как постоянную величину, поскольку механизм работает непрерывно. Например, соприкасающиеся поверхности узлов заменяются другими, имеющими свои возможные отклонения от заданных, перемещение ведущего звена f(ц) является аргументом для функций закона распределения ошибок.
ΔF = f(φ).
2. Линия действия – так называют линию, которая является общей нормалью к соприкасающимся рабочим поверхностям, нормаль проходит через точку касания поверхностей. Из-за отклонения параметров у элемента кинематической пары практическая линия действия отличается от теоретической (заданной), что является нередким явлением.
Взаимодействуя друг с другом в процессе эксплуатации, отдельные ошибки порождают комплексную ошибку, которая не подчиняется закону простого суммирования. Первичные ошибки рассматривают как частные случаи комплексной: при анализе комплексной (функциональной) ошибки ее раскладывают в ряд, состоящий из первичных ошибок. Этот метод помогает увидеть ошибки, допущенные в самом технологическом процессе, в разных его стадиях.
Производимые расчеты исходят от функциональной (т. е. практически существующей) ошибки узлов.
Методы анализа ошибок:
1) дифференциальный метод;
2) метод преобразованного механизма;
3) геометрический метод;
4) метод планов малых перемещений;
5) метод относительных ошибок;
6) метод плеча и линии действия.
Первые пять методов служат для анализа первичных ошибок.
Последний метод применяется для исследования функциональных действующих (т. е. комплексных) ошибок, причем является достаточно надежным.
Для перехода от комплексных ошибок к частным и наоборот существует специальная функция, которую называют передаточным отношением ошибок (ее нередко называют еще коэффициентом влияния).
21. Метод плеч и линия действия
Метод плеч и линий действия позволяет выявить все погрешности, приводящие к кинематической неточности прибора.
Погрешности делят на следующие группы:
1. ΔFr – так выделяют те избыточные приращения в общем плече, которые возникают из-за отклонений в подвижных звеньях механизма.
2. ΔFл.д. – так обозначают погрешности, которые возникают из-за ошибок на линии действий или на параллельных ей линиях.
3. ΔFн.э. – приращения (погрешности), являющиеся следствием ошибок у неподвижных звеньев механизма.
Общее приращение ΔFΣ, как нетрудно себе представить, является суммой вышеперечисленных групп, то есть
ΔFΣ =ΔFr + ΔFл.д. + ΔFн.э. Формула для расчета передачи ошибок:

где ΔF2,ΔF1 – действия соответственно ведомого и ведущего звеньев,
i– линейное передаточное отношение между узлами,
r2, r1 – соответственно, радиусы точек, находящихся на рассматриваемых узлах. Не всегда совпадают линии движения ведомого звена и действия: они могут образовать некоторый угол б. В таком случае приращение на линии движения

где ΔFΣ – общее избыточное приращение по линии действия;

– антипроекция AF на линии действия.
Ошибка для линейного углового положения звена:

где ΔFΣ – общее избыточное давление;
Δφ2, r02– изменение угла между двумя положениями и радиус точки у ведомого звена.
Ошибка линейного перемещения
ΔSnep = ΔSk – ΔSH.
Для скорости:
