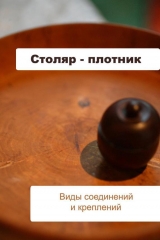
Текст книги "Столяр-плотник. Виды соединений и креплений"
Автор книги: Илья Мельников
Жанр:
Хобби и ремесла
сообщить о нарушении
Текущая страница: 1 (всего у книги 3 страниц) [доступный отрывок для чтения: 1 страниц]
Илья Мельников
Столяр-плотник. Виды соединений и креплений
ВИДЫ ПЛОТНИЧНЫХ СОЕДИНЕНИЙ
Для получения строительных элементов требуемых размеров лесоматериалы соединяют по длине, ширине, толщине и высоте посредством врубок. Врубки применяют при изготовлении балок, ферм, строительстве рубленых и брусчатых домов. Врубки выполняют по разметке вручную или с помощью ручного электрического инструмента.
Соединение отрезков древесины для получения деталей нужных размеров называется сращиванием. Сращивание производится вполдерева косым прирубом, прямым и косым накладными замками, прямым и косым натяжными замками, впритык. При сращивании вполдерева длина соединения должна быть равна 2-2, 5 толщинам бруса. Соединение скрепляют нагелями.
Соединение косым прирубом с подрезкой торца делают равным 2, 5-3 толщинам бруса и крепят также нагелями.
Соединение прямым или косым накладным замком используют в конструкциях, в которых возникают растягивающие усилия. Соединения в прямой накладной замок располагаются на опоре, а в косой накладной замок – у опор.
Соединения в прямой или косой натяжные замки являются прочными, однако их изготовление сложно, кроме того, при усыхании древесины ослабляются клинья, поэтому для ответственных деревянных конструкций применять натяжные замки не рекомендуется.
Сращивание впритык производится в тех случаях, когда два бруса своими концами ложатся на опору. Концы брусьев соединяют вплотную, а затем крепят скобами.
Угловые соединения. Брусья, бревна соединяют под углом при возведении брусковых и рубленых стен, устройстве верхней и нижней обвязок в каркасных домах и других деревянных конструкциях. Основными видами плотничных соединений являются соединения вполдерева, вполулапу, шиповое угловое сковороднем.
Врубку вполдерева выполняют путем вырубки или срезки половины толщины на концах соединяемых брусьев. После вырубки концы соединяют под прямым углом. Соединение вполулапу получается при зарезке на концах брусьев наклонных плоскостей. Обработанные концы брусьев плотно соединяют. Врубку угловым сковороднем выполняют так же, как и врубку вполдерева, но дополнительно в одном из брусьев выпиливают часть древесины.
Крестообразные соединения. Этот вид соединения брусьев применяют при строительстве мостов и изготовлении других деревянных конструкций. Такие соединения выполняют вполдерева, втреть и вчетверть дерева, а также с зарубкой одного бруса.
Соединения по высоте. Соединение элементов по высоте называется наращиванием. Этот вид соединения применяют при устройстве столбов, мачт и др. Наращивать бревна и брусья можно впритык с потайным шипом, впритык со сквозным гребнем, вполдерева с креплением болтами, вполдерева с креплением полосовой сталью, вполдерева с креплением хомутами, косым прирубом с креплением хомутами, применяемым в ответственных сооружениях, впритык с накладками и креплением болтами. Длину стыков делают обычно равной двум или трем толщинам соединяемых брусьев или двум или трем диаметрам соединяемых бревен.
ВИДЫ СТОЛЯРНЫХ СОЕДИНЕНИЙ
Бруски столярных изделий соединяют между собой шиповым соединением, состоящим из двух элементов – шипа и гнезда или проушины. Шип – выступ на торце бруска, входящий в соответствующее гнездо или проушину другого бруска. Шипы бывают одинарными, двойными, многократными.
Цельный шип – это шип, составляющий одно целое с бруском. Вставным шипом называют шип, выполненный отдельно от бруска. Шип с поперечным сечением в виде круга называется круглым.
Шип "ласточкин хвост" имеет профиль в виде равнобочной трапеции с большим основанием на торцовой грани шипа, односторонний шип "ласточкин хвост" – в виде прямоугольной трапеции с большим основанием на торцовой грани шипа.
Угловые концевые соединения брусков выполняют на шипы: открытый сквозной одинарный УК-1, открытый сквозной двойной УК-2, открытый сквозной тройной УК-3, несквозной с полупотемком УК-4, сквозной с полупотемком УК-5, несквозной с потемком УК-6, сквозной с потомком УК-7, несквозные и сквозные на круглые вставные шипы УК-8, на "ус" со вставным и несквозным круглым шипом УК-9, на "ус" со вставным несквозным плоским шипом УК-10, на "ус" со вставным сквозным плоским шипом УК-11.
Для столярных изделий угловые шиповые соединения делают концевыми – на сквозных прямых шипах; серединными вертикальными – на сквозных прямых шипах или шкантах; серединными горизонтальными – на несквозных прямых шипах или шкантах.
Шиповое соединение должно быть выполнено с величинами натягов и зазоров в пределах от -0, 1 до +0, 3 мм, т. е. практически плотным. Основными дефектами в шиповом соединении являются: не выдержаны размеры шипа по длине, толщине, непараллельность поверхности шипа или проушины, сколы, вырывы, неплотности в шиповом соединении и др.
При выработке шипов и проушин выполняют следующие операции: размечают шипы и проушины, запиливают, выпиливают заплечики и выдалбливают проушины.
Шипы и проушины можно размачать используя шаблоны, с помощью которых на торцы бруска наносят риски.
Запиливают шипы и проушины лучковой пилой очень тщательно, так как перекос шипа приведет к перекосу створки. Если шип толще проектного размера, то при посадке в проушину он может расколоть брусок, а если тоньше, то соединение получится непрочным.
При пилении следят за тем, чтобы пила проходила около риски, только в этом случае получится точный размер шипа или проушины. При выработке шипов пилят только с наружной стороны рисок, а при выработке проушин – с внутренней.
При начале пиления для быстрого углубления пилу ставят на ребро под углом 15-20° и, сделав несколько движений на себя, без нажима углубляют пилу, после чего пилят равномерно без нажима и рывков. После запила срезают заплечики. Проушину после запилов выдалбливают долотом с киянкой и зачищают стамеской.
Зубчатый шип имеет профиль в виде треугольника или трапеции, меньшее основание которого является торцовой гранью шипа, двукосый зубчатый шип – равнобедренного треугольника.
Одинарные и двойные шипы применяют при изготовлении окон, рамочных дверей, мебели; шип "ласточкин хвост" – при изготовлении ящиков, коробок; зубчатые шипы – при клеевом соединении деталей (сращивании) по длине.
Помимо этого применяют шипы круглые вставные при соединении делянок (заготовок) по ширине. Шипы впотемок и полупотемок используют при изготовлении рамок, мебели и др.
Шип впотемок делают не только при концевом соединении, но и в тех случаях, когда требуется, чтобы края гнезда были незаметны, так как получить ровные края гнезда не всегда удается. Чтобы скрыть этот дефект, у шипа вырезают потемок, т. е. снимают часть шипа по ширине с одной или обеих сторон.
ДОПОЛНИТЕЛЬНЫЕ КРЕПЛЕНИЯ СОЕДИНЕНИЙ
Деревянные конструкции в процессе эксплуатации деформируются, их соединения становятся непрочными. В таких случаях места соединения закрепляют деревянными нагелями, шипами, клиньями и шпонками из твердой и сухой древесины (влажность 4-6 %).
Деревянные гвозди (нагели) изготовляют из дуба, клена, ясеня или березы. До забивки нагеля просверливают отверстие (сквозное или несквозное) требуемого диаметра и округляют кромки нагеля. Это предохраняет древесину от растрескивания в местах соединения (в углах оконных и парниковых рам и др.).
Деревянные шипы (шканты), например, закрепляют соединения стропил на коньке крыши. Они бывают цилиндрические, прямоугольные и квадратные. Нижний конец шипа выполняют заостренным. До забивки шипа высверливают отверстие несколько меньшего диаметра, чем диаметр шипа.
Деревянные клинья изготовляют из древесины хвойных пород (сосна, ель), одно– или двусторонними. У односторонних клиньев косо обтесана одна широкая сторона, у двусторонних – обе стороны. Стороны имеют уклон 1:6, 1:7 и 1:8°. Такими клиньями укрепляют и натягивают деревянные конструкции, выравнивают лаги пола, поднимают осевшие части стен, крыши. Для заклинивания рукояток ручного инструмента (топоров и молотков) используют такие клинья, хотя следует отдать предпочтение металлическим.
Шпонки. Составные балки из двух-трех брусьев с деревянными шпонками. Скалывающие усилия между ними воспринимают шпонки. Элементы балки дополнительно стягивают между собой стальными болтами. Дубовые шпонки вставляют в гнезда между элементами составной балки. Гнезда для шпонок выбирают электродолбежником одновременно в двух брусьях, затем шпонки забивают в гнезда ударами деревянного молотка. Выступающие концы шпонок зачищают рубанком. Шпонки в середине пролета составных балок из-за слабой нагрузки не ставят.
Шпонки по отношению к соединяемым элементам различают: продольные, поперечные, косые продольные и шпонки с натяжкой. Поперечные шпонки (по сравнению с продольными) обеспечивают менее прочное соединение, так как древесина поперек волокон обладает меньшим сопротивлением, чем вдоль волокон.
Составные балки на шпонках изготовляют из хорошо высушенной древесины. Если шпонка установлена в гнезде с зазором, то она не будет воспринимать силы сдвига и передаваемая нагрузка будет передана на другие шпонки. Механизированное изготовление шпонок и гнезд гарантирует появление зазоров. Поперечное сечение составных балок не должно быть ослаблено гнездами более чем на 1/3 по высоте элемента. При симметричном расположении по противоположным сторонам гнезд их глубина не должна превышать более 1/6 части толщины элемента, но не менее 2 см. Для соединения брусьев применяют продольные шпонки и болты. Прочное и плотное соединение получают, применяя две клиновидные шпонки с натягом, действующие как клинья. Преимущества таких шпонок в том, что в процессе эксплуатации клиньями возможно восстанавливать натяг. Соединения на шпонках используют для усиления балок перекрытий.
МЕТАЛЛИЧЕСКИЕ КРЕПЛЕНИЯ СОЕДИНЕНИЙ
Шурупы, болты, гвозди, стальные хомутики, уголки, накладки и другие используют для крепления деревянных соединений.
Шурупы по сравнению с гвоздями обеспечивают более надежное соединение.
Длина шурупов 10-150 мм, головки – до 13 мм. Петли, ручки, замки окон и дверей, а также штапики, обкладки и т. д. закрепляют шурупами. Шуруп в соединяемую деталь ввинчивают отверткой, а не забивают молотком, чтобы не нарушить целостность древесины вокруг гнезда. Шурупы большего диаметра ввинчивают в предварительно просверленное отверстие, составляющее 0, 7-0, 8 диаметра и глубиной 1/3 длины шурупа. Для утопления головки шурупа заподлицо с поверхностью древесины предусматривают коническое расширение.
В соединениях встроенной мебели головки шурупа втапливают ниже поверхности с последующей шпатлевкой. Шурупы с овальной хромированной головкой скрепляют детали и придают соединению декоративный вид.
Шурупы используют для крепления гардинных штанг, картин, керамических изделий и т. д.
Гвозди изготовляют из проволоки круглого и квадратного сечения. Круглые гвозди меньше перерезают волокна древесины, чем квадратные, однако квадратные гвозди прочнее соединяют детали и больше сопротивляются выдергиванию. Диаметр гвоздя равен 1/20 части его длины. Для соединения детали из крупнослойной влажной древесины используют более толстые гвозди. Гвозди в замерзшую древесину забивают в предварительно просверленное отверстие диаметром, чуть меньшим гвоздя, и глубиной не менее 1/3 длины. Толстые гвозди в детали из твердых древесных пород забивают в заранее просверленные отверстия на глубину не менее 1/2 длины гвоздя. Это предупреждает искривление забиваемых гвоздей и растрескивание древесины.
Гвозди в стыках конструкции размещают по прямым параллельным линиям или под углом 45° относительно продольной оси детали. Расстояние (шаг) между гвоздями в направлении волокон не менее 15d (d – диаметр гвоздя) гарантирует от появления трещин в древесине. Расстояние между продольными рядами забитых гвоздей не менее 4d, при размещении в шахматном порядке – не менее 3d. От конца детали (доски, бруска) до крайнего поперечного ряда гвоздей расстояние не менее 15d, а от края детали до продольного ряда гвоздей – не менее 4d.
Отклонения от шага между гвоздями в узлах деревянной конструкции поперек волокон – не более диаметра гвоздя, вдоль волокон – двух диаметров.
Тонкие детали обычно прибивают к толстым. В противном случае выбирают гвозди по толщине и длине, соответствующие тонкому материалу. Длина гвоздей в 2, 5-3 раза превышает толщину прибиваемого материала. При наклонной (косой) забивке гвоздей прибитый элемент труднее оторвать от основного. Перекрестная косая забивка гвоздей надежнее параллельной косой.
При толщине соединяемых деталей меньше длины гвоздей, их выступающие концы загибают поперек волокон, что повышает на 25 % прочность соединения.
Прочность соединения гвоздями опиленного или обтесанного материала с круглым уменьшается на 30 %. Круглые элементы не соединяются между собой гвоздями из-за недостаточной силы трения. Поэтому при соединении в местах сопряжения круглых деталей выпиливают или обтесывают прямую накладку вполдерева, усиливая соединение установкой болтов.
Строительные скобы используют в соединениях деревянных конструкций.
В стыках несущих конструкций не используют гвозди, бывшие в употреблении, с затупленным концом, деформирующие древесину и снижающие прочность соединения.
В соответствии с разметкой сначала забивают гвозди крайних рядов, затем остальные. Гвозди, забитые вдоль волокон, имеют непрочное соединение.
Гвозди размещают одинаково по обе стороны действующей силы. Нарушение этого требования приведет к деформации стыка конструкции. Для разметки места забивки гвоздей применяют шаблон из фанеры.
Размером гвоздей соответствует минимальный шаг между ними, зависящий от направления действующей силы.
Болты используют для соединения бревен, брусьев, толстых досок. Их изготовляют из стали диаметром 10-28 мм. Болты отстоят от концов соединяемых деталей не менее чем на 15 см. Их забивают молотком в отверстия соединяемых деталей меньше диаметра болта (0, 7-0, 8d). Шайбы толщиной 4-6 мм с наружным диаметром в 3-3, 5 раза больше диаметра болта устанавливают с обеих сторон. В стыках несущих конструкций устанавливают не менее двух болтов диаметром до 12, 7 мм с шайбами толщиной 6 мм. Шайбы предотвращают вдавливание в древесину головки и гайки при затягивании болта и при работе под нагрузкой. Самовольное откручивание гайки предотвращает навинчивание контргайки. Пружинистая шайба (гровер) затягивает стык во время высыхания древесины.
Хомутами из полосовой стали толщиной 10-15 и шириной 30-100 мм укрепляют соединения строительных конструкций. Место соединения обхватывают хомутом, а затем стягивают болтом или прибивают гвоздем. В зависимости от формы соединяемых деталей применяют хомуты круглые или прямоугольные.
Уголками закрепляют угловые соединения конструкций. Их изготовляют под прямым углом, широкими и комбинированными, из стальных полос толщиной 2-10 и шириной 20-80 мм. Уголки закрепляют шурупами или болтами с одной или обеих сторон соединения. Ими крепят углы створок ворот, оконных и парниковых рам и др. В конструкциях ворот уголки объединены с петлями.
Утапливаемые кольцевидные и квадратные стальные шпонки применяют для бокового крепления двух или трех деталей. Диаметр кольцевидной шпонки 5-20 см, высота (включая выступы) – З-5 мм. В местах установки выфрезеровывают соответствующие пазы, куда вставляют шпонку, чтобы половина высоты шпонки входила в каждую деталь. Соединение со шпонкой укрепляют болтами. Соединяемые детали должны быть высушены, а шпонки плотно с натягом вставлены в пазы.
Впрессованные шпонки из стального листа толщиной 1 мм бывают кольцевидные и квадратные. Их высота 25мм с прочными острыми зубьями по обоим краям.
В местах соединения строительных конструкций выполняют отверстия под болты, затем острыми зубьями шпонку закрепляют на одной детали и накрывают второй. Вставив болты, затягивают гайки и сжимают соединение, впрессовывая шпонку в древесину. Зубья шпонок, впрессованные в древесину, обеспечивают жесткое и прочное соединение. Битумная мастика, покрывающая шпонки, защищает их от коррозии во влажной среде. Впрессовываемые шпонки употребляют в стыках крыш и других конструкций, требующих жесткости и прочности соединения.
Накладки изготовляют из полосовой стали толщиной 10 и шириной 40-60 мм, длиной 20-80 см. Их крепят гвоздями (желательно коваными) и шурупами. Концы накладок закрепляют прямыми скобами. Накладки применяют при наращивании соединений.
Глухари и крюки изготовляют из квадратной стали сечением 10х10-12х12 мм или цилиндрической стали диаметром 10-12 мм. Длина глухарей 100-120мм. Глухари бывают двух видов. Ими закрепляют оконные и дверные коробки в проемах каменных стен, если в них не заложены деревянные пробки.
Строительные скобы изготовляют из квадратной стали размером 10х10-18х18 мм или цилиндрической – диаметром 10-18мм длиной 200-500 мм. Заостренные концы скобы согнуты в одну или в разные стороны под углом 90 или 180°.
Анкерные болты используют для крепления концов балок в наружных и капитальных стенах. Их прикрепляют к концам балок с помощью болтов и скоб.
Изготовляют болты из листовой стали толщиной 10-12 мм и шириной 40-50 мм. Длина анкерного болта для закрепления конца балки в наружной стене 80-100 см.
Стальная подножка (стремя) служит для подвески промежуточной (короткой) балки к главной в местах пропуска труб. Подножку изготовляют из листовой стали толщиной 10 мм и шириной 50-70 мм. Конец короткой балки опирается на стремя, закрепленное на основной балке.
Конекторы – это квадратные стальные пластины с игольчатыми гвоздями, предназначенные для соединения узлов в несущих конструкциях.
Конекторы изготовляют в виде лент, разрезая затем по длине на нужные размеры. Их различают по номерам, толщине материала, по размерам игольчатых гвоздей, размещению и конфигурации. Ширина конекторов 25-152 мм, длина зависит от величины нагрузки. В угловых стыках конекторы впрессовывают попарно.
Конекторы впрессовывают перпендикулярно волокнам, деформируя их, но не разрушая. Деформированные волокна древесины надежно удерживают гвозди конектора, что обеспечивает прочность соединения. Игольчатые гвозди конектора располагают рядами, в шахматном порядке или кольцеобразно. Оцинкованная поверхность конекторов не подвержена коррозии. До установки конекторов деревянные соединения обрабатывают антисептиками.
Конекторы устанавливают в узлах конструкций, перекрывающих пролеты 7, 5-30 м. Высота таких ферм 1-3, 85 м.
Выбор конектора производится в зависимости от толщины используемых пиломатериалов.
За счет сопротивления волокон древесина хорошо удерживает гвозди, шурупы, болты и шпонки. Волокна древесины изгибаются и давят на поверхность забитого гвоздя, препятствуя его выдергиванию. Сопротивляемость древесины вбиванию гвоздей зависит от диаметра и длины гвоздя, плотности, твердости древесины, степени влажности, особенностей направления ее волокон и забивки гвоздя. Выдергивание гвоздей зависит от продолжительности времени нахождения их в древесине. В свилеватой древесине гвозди удерживаются крепче, чем в породах с прямыми волокнами. Только что забитый гвоздь удерживается в древесине крепче, чем по истечении времени.
Гвозди, забитые в торец (вдоль волокон), удерживаются на 25-30 % меньше, чем забитые поперек волокон. Способность древесины удерживать гвозди, забитые в радиальном или тангентальном направлении, примерно одинаковая.
Способность древесины удерживать гвозди, шурупы и другие крепления определяется силой их выдергивания. Древесина березы больше сопротивляется выдергиванию гвоздей, чем сосны, сохраняя эту способность в период эксплуатации конструкции. Во влажных условиях применяют оцинкованные гвозди.
СОЕДИНЕНИЕ НА КЛЕЯХ
Для изготовления элементов мебели, оконных и дверных блоков, брусков коробок, перегородок, строительных конструкций требуются толстомерные пиломатериалы. Для обеспечения производства толстомерными пиломатериалами тонкомерные пиломатериалы склеивают по длине, толщине и ширине. Для изготовления клееных элементов используют преимущественно пиломатериалы хвойных пород (ель, сосну) и клеи на основе синтетических смол. Марки клеев подбирают в соответствии с их свойствами. Синтетические клеи водо– и грибостойки, дают более прочное соединение. Процесс приготовления клеевого раствора и режимы склеивания проще, что удобнее при массовом производстве. Выдержка под прессом не требует длительного времени, а при подогреве может быть сокращена. Клеевой слой при склеивании почти не увлажняется, выдержка после запрессовки небольшая. Все клеевые соединения должны быть выполнены на клеях, разрешенных к применению Министерством здравоохранения.
Для производства клееных конструкций применяют резорциновый клей ФР-12, фенольный КБ-3, карбамидно-меламиновый КС-В-СК, карбамидный КФ-Ж, алкилрезорциновый ФР-100 и др. В клее ФР-12 отсутствует фенол, рабочая жизнеспособность не менее 2 ч. Клей КБ-3 водостоек, выделяет свободный фенол, содержит горючие растворители, рабочая жизнеспособность 1, 5-2 ч. Клей КС-В-СК имеет водостойкость выше карбамидных, содержит меньше фенола и горючих растворителей. Рабочая жизнеспособность более 2 ч. Клей КФ-Ж имеет ограниченную водостойкость, не содержит фенола и горючих растворителей. Клей ФР-100 не имеет свободного фенола, содержит горючие растворители, рабочая жизнеспособность более 1 ч.
Клей КФ-Ж может быть горячего и холодного отверждения. В качестве отвердителя для получения клея горячего отверждения применяют хлористый аммоний (0.5-1 мас. ч. на 100 ч. смолы), для получения клея холодного отверждения – 10 %-ный водный раствор щавелевой кислоты (10-15 мас. ч. на 100 ч. смолы). Отверждение клея при горячем способе происходит при температуре до 100 °С в течение 60-100 с.
Для склеивания конструкций, работающих в условиях повышенной влажности, используют клей КБ-3, приготовляемый на основе смолы СФЖ-3016 и керосинового контакта Петрова. Соотношение компонентов клея зависит от температуры воздуха, в котором склеивают элементы: при температуре 15-17 °С на 100 мас. ч. смолы берется 25 ч. керосинового контакта, при 18-20 °С – 20 мас. ч., а при 21-25 °С – 15 мас. ч. Этот клей водоупорен, масло-, бензо-, кислото– и биостоек. Для улучшения зазорозаполняющих свойств в него вводят наполнитель – древесную муку (до 8 % от массы смолы).
Технологический процесс изготовления клееных элементов состоит из следующих основных операций: сушки, сортировки и раскроя пиломатериалов, обработки с четырех сторон, приготовления клеев, нанесения клея на склеиваемые элементы, склеивания заготовок по длине и ширине, сборки склеиваемых заготовок, запрессовки и выдержки под давлением для отверждения клея, механической обработки склеенных элементов, защитной обработки, контроля качества склеенной продукции.
Склеиваемая древесина должна иметь одинаковую влажность и породу, так как при склеивании заготовок (деталей) из двух частей разной влажности после высыхания на более влажной стороне (заготовке) образуется вогнутость, а в клеевом шве – внутренние напряжения, поэтому разница во влажности древесины в склеиваемых элементах должна быть не более 2-4 %. Сушат пиломатериалы в сушильных камерах. Влажность пиломатериалов для склеивания не должна превышать 10е2 %. После сушки пиломатериалы в течение 3-5 сут выдерживают в помещении при температуре 18-25 °С и относительной влажности воздуха 60-70 %.
Сортируют пиломатериалы до сушки или после нее путем внешнего осмотра, оценивая качество по наличию пороков (сучки, гниль, червоточина, наклон волокон). При небольшом объеме производства пиломатериалы сортируют при поперечном раскрое. По длине и ширине пиломатериалы раскраивают на круглопильных станках или на специализированных линиях. Для поперечного раскроя применяют станки ЦПА-40, для продольного – ЦДК4-3, ЦДК5-2.
После раскроя заготовки обрабатывают на продольно-фрезерных станках. Поверхности заготовок должны быть отфугованы и профрезерованы. При соединении по длине заготовки окончательно обрабатывают после сращивания. Отфрезерованные пиломатериалы хранят не более одних суток при температуре помещения 18-20°С и влажности воздуха 50-60 %, предохраняя их от загрязнения, увлажнения или пересушивания.
Склеиваемые заготовки должны быть одинаковой толщины. Если заготовки имеют разную толщину или дефекты формы, их перед раскроем калибруют (по толщине). При сращивании по длине необходимо правильно формировать шипы. Шипы вырабатывают на шипорезных, фрезерных станках или на специализированных линиях.
Зубчатые соединения необходимо выполнять в соответствии с требованиями ГОСТа. При соединении на "ус" уклон клеевого соединения должен быть 1/10, или длина скоса должна соответствовать десяти толщинам склеиваемых заготовок.
В целях экономии древесины вместо обычных зубчатых шипов длиной 32-50 мм применяют более короткие – 5-10 мм с шагом 1, 75-3, 5 мм и затуплением 0, 2-0, 5 мм.
Небольшое количество клея приготовляют вручную, а большое – в клеемешалке типа КМ-40-10. Приготовление клея состоит из следующих операций: подготовки компонентов клея, перемешивания жидких компонентов (для устранения осадка), просеивания подсушенных порошкообразных отвердителей, взвешивания их в соответствии с составом. Составляющие компоненты клея (смола, отвердитель, наполнитель) тщательно перемешивают в течение 3-5 мин при частоте вращения лопастей 40-60 об/мин и температуре клея не более 18-20 °С.
Клей наносят на обе склеиваемые поверхности (наносить клей на одну сторону допускается лишь при большой жизнеспособности клея).
При малых объемах производства клей наносят вручную кистями, щетками или валиками, а при большом объеме – на клеенаносящих станках.
Сращивают пиломатериалы по длине на линии КДК-13. На этой линии можно сращивать пиломатериалы длиной 800-6500 мм шириной 80-200 и толщиной 16-50 мм со скоростью подачи 10-15 м/мин.
Для склеивания пакетов применяют секционный пресс КДК-10. На этом прессе можно склеивать пакеты длиной 16 500 мм, шириной 80-200 и толщиной до 865 мм. Выдержка в прессе для прямолинейных конструкций 8-10 ч. Величина торцового давления при запрессовке зубчатых соединений колеблется в пределах 1-1, 5 МПа.
Прочность склеивания древесины периодически проверяют. Для этого склеиваемые образцы деталей раскалывают по клеевому шву. Если раскол произошел по древесине, то склеивание считается прочным, а если по слою клея – то прочность склеивания низкая. Если элементы детали склеены правильно, то соединение получается прочнее самой древесины.
Большое значение при склеивании древесины имеет качество ее подготовки. Плохо склеиваются отшлифованные поверхности, покрытые пылью, жиром и др. До склеивания поверхности должны быть чисто выстроганы, плотно прифугованы и очищены от пыли, грязи, опилок.
Клей наносят на склеиваемые поверхности равномерным слоем. Остатки клея, появляющиеся на поверхности детали, при прессовании снимают влажной тряпкой, пока клей не застыл, после чего насухо протирают сухой тряпкой.
Склеивают бруски по длине на зубчатый шип на линии ОК502, состоящей из ряда последовательно расположенных агрегатов. На шипорезном станке зарезаются зубчатые шипы, на прессе на них наносится клей, отрезки соединяются и сжимаются, после чего на торцовочном станке длинные бруски торцуются на требуемую длину. Полученные отрезки через приемный стол поступают на конвейер, где укладываются в стопу и выдерживаются до полного схватывания клея. На линии можно склеивать бруски длиной 250-1200 мм, шириной 50-150 и толщиной 40-85 мм. Производительность линии до 5 м/мин.
Доски, бруски при малых объемах производства склеивают пластями или кромками в струбцинах, хомутах, ваймах. Процесс склеивания состоит из подготовки заготовок (раскрой, обработка поверхности под склеивание), склеивания их пластями, кромками, выдержки для схватывания клея, обработки после склеивания.
Технологический процесс изготовления клееных щитов включает сушку пиломатериалов, раскрой пиломатериалов по длине и ширине на круглопильных станках, фугование (продольное фрезерование) пласти и кромки на фуговальном станке, намазывание кромок клеем, склеивание реек в щиты в ваймах, технологическую выдержку, необходимую для схватывания клея, фрезерование плоскостей щита на рейсмусовом станке, обрезку щита в размер на круглопильном станке. Узкие щиты можно склеивать в струбцинах.
Рейки (детали), подлежащие склеиванию, выравнивают по длине, подбирают по толщине и собирают в пакет. Собранные в пакет детали со стороны кромки намазывают клеем, после этого детали раскладывают на ваймах так, чтобы намазанная кромка стыковалась с сухой.
При запрессовке следят за тем, чтобы щит не выпучивался и не имел перекосов. Проверяют это линейкой по диагонали и поперек щита, правильность угла проверяют угольником. После проверки детали зажимают окончательно клиньями и выдерживают до полного схватывания клея в ваймах.
На крупных предприятиях щиты дверей склеивают и облицовывают в прессах с винтовыми, пневматическими или гидравлическими зажимами, а также на линиях.
Бруски коробок (дверей) по ширине склеивают на линии ДВ504, состоящей из торцовочного и клеенамазывающих станков пресса с обогревом токами высокой частоты (ТВЧ), транспортного устройства, траверсной тележки, торцовочного станка, дробилки, напольного конвейера. Линия предназначена для подачи раскроенных реек, вырезки дефектов у реек, нанесения дозированного количества клея, формирования непрерывной ленты бруска из реек, склеивания в прессе с обогревом в зоне ТВЧ, раскроя непрерывного бруска на отрезки нужного размера, укладки их в пакеты и передачи для дальнейшей обработки (фрезерования, зарезки шипов).
Для деревянных конструкций основным видом клеевого соединения является склеивание досок, уложенных на пласти. По длине доски стыкуют впритык, с точной приторцовкой на "ус", на зубчатое клеевое соединение. Все стыки должны быть промазаны клеем.
Склеиваемые поверхности должны быть хорошо очищены, плотно прилегать друг к другу, не иметь пятен краски или масла. Выдержка после нанесения клея на поверхность древесины должна быть не более 1 ч.
Места соприкосновения деревянных элементов (коробок) с бетоном, а также торцы конструкций обрабатывают антисептическими составами.
Прочность клеевого шва должна быть не ниже прочности древесины на скалывание вдоль волокон и на растяжение поперек волокон.
Толщина брусков и досок, применяемых для склеивания, допускается до 50 мм, а в конструкциях, подверженных увлажнению, – не более 32-40 мм.