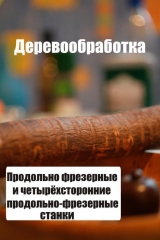
Текст книги "Продольно-фрезерные и четырехсторонние продольно-фрезерные станки"
Автор книги: Илья Мельников
Жанр:
Хобби и ремесла
сообщить о нарушении
Текущая страница: 1 (всего у книги 2 страниц) [доступный отрывок для чтения: 1 страниц]
Илья Мельников
Продольно-фрезерные и четырехсторонние продольно-фрезерные станки
Классификация станков
По назначению деревообрабатывающие станки подразделяют на три группы: универсальные, имеющие широкое распространение в различных деревообрабатывающих производствах; специализированные, предназначенные для выполнения только определенных видов работы с переналадкой станка, и специальные для определенной обработки без переналадки станка.
Деревообрабатывающие станки могут быть цикловые – с прерывистым движением детали или режущего инструмента и проходные – с непрерывным перемещением детали. У проходных станков деталь непрерывно перемещается относительно рабочих органов и при этом обрабатывается.
В зависимости от способа обработки древесины и вида технологической операции различают станки круглопильные, ленточнопильные, фуговальные, рейсмусовые, четырехсторонние, фрезерные, шипорезные, сверлильно-пазовальные, токарные, шлифовальные и др.
Для обозначения вида и станков принята буквенно-цифровая индексация. Первая буква обозначает тип станка: Л – ленточный, Ц – круглопильный, С – четырехсторонний продольно-фрезерный, фуговальный, рейсмусовый, фрезерный, Ш – шипорезный, СВ – сверлильный, Шл – шлифовальный и т. д.
Цифры после первой буквы указывают на количество рабочих органов или агрегатов станка: например С2Ф – фуговальный станок с двумя (горизонтальным и вертикальным) режущими инструментами и т. п.
Вторая и третья буквы характеризуют технологические особенности станка: ЛС – ленточнопильный столярный, ЦДК – круглопильный для продольной распиловки с конвейерной подачей, СР – рейсмусовый, ФС – фрезерный средний, СВПГ – сверлильно-пазовальный горизонтальный и т. д.
Цифры после букв индекса характеризуют главный параметр станка либо номер модели станка: СР6-9 – станок рейсмусовый, ширина стола 630 мм, девятая модель и т. д.
Основные агрегаты станков
Различаясь технологическим назначением и способом обработки детали, деревообрабатывающие станки имеют подобные конструктивные элементы и функциональные механизмы. Использование в разных станках повторяющихся нормализованных элементов и деталей называют нормализацией.
Иногда станки полностью состоят из одинаковых составных частей и отличаются один от другого только взаимным расположением рабочих органов. Такое заимствование элементов называют унификацией.
Когда станки собирают из отдельных агрегатов, которые выпускаются специализированными заводами, такие станки называют агрегатными.
Элементы станков разделяют по выполняемым функциям. Для установки и монтажа всех составных частей станка служит станина. Она устанавливается на фундамент или специальные виброизолирующие опоры. На станине располагаются корпусные детали, которые воспринимают нагрузки от рабочих органов и образуют контур станка – основания, стойки, поперечины, траверсы, кронштейны и т. д. Корпусные детали не перемещаются в ходе работы, но в ряде случаев их положение можно менять до начала обработки изделия.
Требование к станине и корпусным деталям – точность и жесткость, так как эти показатели влияют качество обработки деталей.
Агрегаты станка, обеспечивающие главное движение, называют механизмом резания. Механизм резания с выполняют в виде ножевого вала, шпинделя или пильного вала. На них крепят режущий инструмент.
Следующий агрегат – механизм подачи. Он предназначен для обеспечения подачи заготовки. Выполняется в виде конвейера, вальцов или роликов. (В цикловых станках механизмом подачи является подвижный стол или каретка.)
Расположение заготовки относительно режущего инструмента устанавливается специальными устройствами. Они включают базовые элементы станка: столы, направляющие линейки, угольники, упоры, прижимные приспособления. С помощью их достигается устойчивое положение обрабатываемой детали в проходных станках. Прижимы делают в виде клиновых ремней или лент.
На позиционных станках используются зажимы в виде колодок и пластин. Для предотвращения порчи детали рабочие элементы зажимов оснащаются съемными резиновыми накладками.
Для обеспечения настроечных перемещений служат суппорты, которые могут переставляться вручную или от механического привода. У суппорта точно обработанные поверхности, которые называют направляющими. Такие же направляющие есть на станине или корпусной детали, на них и устанавливается суппорт.
Оградительные и предохранительные устройства. Они бывают в виде колпаков, кожухов, крышек. Эти части станка предохраняют рабочего от случайного касания движущихся механизмов станка. (Ограждения блокируют с приводом станка, чтобы при их снятии станок автоматически выключался.)
Управляются станки с помощью маховиков, педалей, рукояток, кнопок и переключателей. В сложных станках органы управления выполняются в виде пульта, на котором расположены кнопки включения и выключения рабочих органов.
И последнее – вспомогательные элементы. К ним относят устройства для смазывания трущихся частей станка: масленки, шприцы, насосы для подачи масла.
Базирующие устройства служат для обеспечения качественной обработки детали – с их помощью осуществляется ориентирование, базирование и закрепление заготовки в нужном положении относительно рабочих органов станка. Ориентирование заготовки производится вручную или специальным ориентирующим устройством: винтовыми роликами, диском, отклоняющим щитком.
Базирование – ответственный этап механической обработки, так как качество его выполнения определяет точность обработанной детали. Правильная взаимная ориентировка детали и рабочих инструментов в станке определяется назначением технологических баз. Технологическая база – это совокупность базирующих поверхностей, используемых для придания заготовке заданного положения относительно режущего инструмента.
Обрабатываемые детали бывают прямолинейные с профильным поперечным сечением, в виде тела вращения или сложной пространственной формы. Базирующими поверхностями призматической заготовки являются ее пласть, кромка и торец, которые соответственно называются главная, направляющая и упорная поверхности. При базировании эти поверхности соприкасаются с опорными элементами станка. В зависимости от вида контакта заготовки с элементами различают подвижное и неподвижное базирование.
При подвижном базировании заготовка находится с опорным элементом в состоянии подвижного контакта. При неподвижном базировании заготовка в процессе обработки неподвижна относительно опорных элементов станка.
Элементы базирования деталей бывают разных конструкций. Это столы, направляющие линейки, упоры, патроны, планшайбы токарных станков.
Столыдля неподвижного базирования деталей представляют собой массивные плиты с плоской рабочей поверхностью. Стол для подвижного базирования детали должен иметь гладкую поверхность с низким коэффициентом трения. Кромка стола, примыкающая к режущему инструменту, в процессе эксплуатации обычно изнашивается и эту часть стола обычно оснащают съемной стальной накладкой. На столе монтируют направляющие линейки или угольники.
Иногда столы оснащают роликами или делают в виде роликового конвейера. Если ролики приводные, то они являются не только установочными элементами, но и служат средством для транспортировки деталей.
В зоне движения режущего инструмента на столе монтируют деревянную плиту с пазом, которая обеспечивает устойчивое положение отпиливаемых кусков материала.
Направляющие линейки станков исполняются в виде бруса с гладкой поверхностью. Концы линейки, обращенные к пиле, оснащают съемными накладками. Иногда направляющие линейки оснащают вращающимися роликами, что снижает сопротивление подачи обрабатываемого материала.
Упоры служат для точного базирования детали по длине. Они бывают утапливаемыми и откидными. Упор должен иметь достаточную жесткость, иначе при повторяющихся ударных нагрузках он может сместиться, что приведет к браку.
Правильное положение заготовки относительно стола и направляющей линейки при проходной обработке достигается боковым и верхним прижимами. Прижимы делают в виде колодки, подпружиненного башмака, или гибких пластин со скользящей рабочей поверхностью. Для уменьшения трения скольжения применяют роликовый прижим.
На станках с поперечной подачей деталей прижимное устройство выполняют в виде двух параллельных агрегатов, оснащенных бесконечными клиновыми ремнями. Ремни приводятся в движение силами трения о заготовку. Натяжение ремня можно регулировать, смещая ось шкива относительно корпуса прижима.
Наладка и настройка станков
Геометрическая точность станка, правильность наладки и настройки его оказывает существенное влияние на качество обработки деталей.
Деревообрабатывающие станки по точности выполняемых работ подразделяют на четыре класса: особой точности (О), обеспечивающие точность обработки по 10-12-му квалитетам; повышенной точности (П), обеспечивающие точность обработки по 11-12-му квалитетам (фрезерные, четырехсторонние и т. п.); средней точности (С), обеспечивающие обработку по 13-15-му квалитетам (токарные, сверлильные и т. п.); нормальной точности (Н), обеспечивающие точность обработки по 14-18-му квалитетам (ленточнопильные, круглопильные и т. п.).
Рассмотрим основные причины возникновения погрешностей при механической обработке древесины.
Геометрическая неточность станка и его износ. Не секрет, что детали станков часто изготовляют с погрешностями. В процессе сборки станка эти погрешности суммируются, таким образом точность расположения исполнительных поверхностей станка нарушается. На точность станка влияет также износ деталей в процессе эксплуатации.
Искажение формы режущей кромки резца при его заточке, погрешность при установке и закреплении режущего инструмента, а также его биение.
Зажимные и установочные элементы приспособления имеют погрешности даже при самом тщательном изготовлении. При установке заготовки в приспособление возникают погрешности базирования. В приспособлении под действием зажимных усилий и усилий резания возникают упругие деформации, которые также снижают точность обработки.
Недостаточная жесткость системы станок-приспособление-инструмент-деталь (СПИД). Жесткостью этой системы называют способность обеспечивать необходимую точность обработки при нагрузках, возникающих в процессе работы станка.
При обработке партии заготовок силы резания изменяются в зависимости от величины припуска на обработку, степени затупления инструмента и механических свойств древесины, что вызывает упругие деформации технологической системы СПИД. Деформации нарушают расположение установочных поверхностей станка и точность обработки снижается.
Ошибки при настройке станка. Ошибки возникают из-за неправильного отсчета показаний, погрешности измерения пробных деталей, неточности контрольно-измерительного инструмента. Эти ошибки и погрешности образуют результирующую погрешность механической обработки.
Наладка станка – это регулирование и согласование взаимодействия всех элементов станка, установление режимов обработки, пробный пуск и контроль обработанных деталей.
Размерной настройкой станка называют действия по обеспечению требуемой точности расположения режущего инструмента относительно установочных элементов станка (столов, упоров).
Статическая настройка с использованием встроенных в станок измерительных устройств заключается в том, что станочник перемешает рабочий орган на требуемый настроечный размер и одновременно контролирует величину перемещения по отсчетному устройству.
Статическая настройка станка по эталону (шаблону) заключается в регулировке положения инструмента до касания его лезвий рабочей поверхности шаблона. Допускаемое отклонение на настроечный размер должно быть меньше допускаемого отклонения на размер детали, подлежащей обработке. (Часто в качестве эталона используют ранее изготовленную на станке деталь.)
Эталоны применяют при настройке многошпиндельных станков и в тех случаях, когда надо одновременно учитывать несколько настроечных размеров или взаимных положений режущих инструментов, обрабатывающих деталь сложной формы.
Настройка по эталону не всегда обеспечивает необходимую точность. После обработки некоторого количества деталей необходимы дополнительное регулирование и поднастройкастанка.
Статическую настройку станка с помощью универсальных измерительных приборов используют в станках, которые налаживают на один настроечный размер или в станках, не имеющих встроенного отсчетного устройства. В качестве измерительного инструмента применяют магнитные стойки, микрометры, штангенциркули. Контроль перемещения рабочего органа в момент его регулировки позволяет достичь высокой точности настройки.
Статическая настройка с помощью настроечно-измерительных приспособлений обеспечивает высокую точность. Эти приспособления конструируют для конкретного станка и изготовления конкретной детали.
Нередко настраивают станок, изготовляя пробные детали. В этом случае станок настраивают сначала с помощью встроенного измерительного устройства или других средств. Предварительную настройку выполняют с меньшей точностью, чем статическую. Обычно величина первоначального настроечного размера существенно отличается от величины среднего размера детали и выбирается такой, чтобы при обработке деталей размер их получался несколько большим, чем нужно, что исключает выпуск неисправимого брака. После предварительной грубой настройки обрабатывают пробные заготовки, детали проверяют калибром или измерительным инструментом.
Эту настройку с контролем деталей предельным калибром осуществляют тем же рабочим калибром, который используют в дальнейшем при контроле деталей всей партии. Если размер пробной детали находится в пределах допуска, настройка считается правильной.
Настройка по пробным деталям позволяет определить по результатам измерений среднее значение размера трех-пяти пробных деталей и поле рассеяния соразмеров. В результате поднастройки получают новое значение настроечного размера. Если этот размер находится в пределах допуска, обрабатывают всю партию деталей.
Этот метод расчета величины поднастройки применяют при обработке небольшой партии деталей, когда износ инструмента невелик и не может оказать существенного влияния на точность обработки.
Четырехсторонние продольно-фрезерные станки
Четырехсторонние продольно-фрезерные станки выпускают для обработки заготовок с сечением заготовок по ширине и толщине 100Х50 мм, 160Х80 мм, 250Х125 мм; для обработки паркетных дощечек – с наибольшей шириной фрезерования 70 мм и 100 мм.

Рис. Схема четырехстороннего продольно-фрезерного станка:
1 – обрабатываемая деталь, 2 – боковые ножевые валы, 3 – верхний ножевой вал, 4 – прижимные ролики, 5 – подающие вальцы, 6 – нижний ножевой вал, 7 – гладильные ножи, 8 – нижний калевочный ножевой вал
На станине четырехстороннего продольно-фрезерного станка С26-2М размешены последовательно суппорты горизонтального нижнего шпинделя, вертикальных правого и левого шпинделей и верхнего горизонтального шпинделя. Станок может оснащаться калевочным суппортом для выборки пазов или раскроя ее на части при выходе из станка.
Режущие инструменты крепят на шпиндели, имеющие индивидуальные электродвигатели. Станок снабжен когтевой защитой, предотвращающей обратный выброс заготовки из станка. Рядом установлена планка-ограничитель подачи заготовок с недопустимым припуском.
Механизм подачи расположен впереди рабочих шпинделей и состоит из двух нижних неприводных и двух верхних приводных вальцов, верхние вальцы рифленые. Привод вальцов от электродвигателя с регулируемым шкивом через клиновой ремень (вариатор) и систему зубчатых колес. Вариатор позволяет плавно изменять скорость подачи от 7,5 до 42 м/мин.
На суппорте установлены подпружиненные ролики, прижимающие деталь к столу. Сбоку заготовка прижимается прижимом к направляющей линейке.
Устройство станков для обработки паркетных дощечек аналогично. Единственное отличие – конвейерный механизм подачи для обработки коротких заготовок. Это двухцепной приводной конвейер с подпружиненными шипами. Шипы обеспечивают надежную подачу заготовок, различающихся величиной припуска до 3 мм.
По заданным размерам детали и припускам на обработку вычисляют толщину и ширину снимаемого слоя каждым режущим инструментом. Эти данные нужны для выбора допустимой скорости подачи.
Из станков этого типа, выпускаемых сегодня, можно назвать следующую модель.
4-сторонний продольно-фрезерный станок 4ФМ-180/4 предназначен для обработки прямых и фасонных поверхностей с четырех сторон за один проход при производстве деталей для мебельных, строительно-столярных и других изделий. Используется для серийного либо массового производства погонажныж изделий, столярных изделий, картинных рам, мебели, вагонки, половой доски, деревянного упаковочного материала из древесины мягких или твердых пород.
Настройка четырехсторонних продольно-фрезерных станков – сложная и трудоемкая операция. Она заключается в установке инструментов на заданные размеры обработки, регулировке подвижных столов и направляющих линеек, а также наладке подающих и прижимных устройств.
По шаблону наладка ведется так. Переместив суппорты, подающие и прижимные элементы на расстояние, превышающее настроечный размер, шаблон устанавливают в станок – прижимают к поверхности стола и задней направляющей линейке. Сначала регулируют направляющие линейки, чтобы их рабочие поверхности были параллельны. При этом задняя линейка должна располагаться по касательной к окружности резания и выступать относительно передней линейки на толщину снимаемого слоя. Переднюю линейку выверяют с помощью прокладок, толщина которых равна толщине снимаемого слоя.
Размерную настройку режущих инструментов выполняют со стороны подачи материала в следующей последовательности: нижняя горизонтальная ножевая головка, левая и правая вертикальные ножевые головки, верхняя горизонтальная ножевая головка.
Размерная настройка для всех режущих инструментов одинакова: расфиксирование суппорта, регулировка положения режущего инструмента относительно шаблона, фиксирование суппорта. Режущую кромку ножа подводят до касания с рабочей поверхностью шаблона при провертывании ножевой головки вручную.
Можно настраивать режущие инструменты с помощью измерительных средств – шкал и лимбов.
Наладка прижимных элементов. Задние прижимные колодки у верхней ножевой головки регулируют по высоте гайками так, чтобы расстояние от стола до рабочей поверхности колодок было на 2-3 мм меньше настроечного размера. Усилие прижима регулируют, изменяя натяг пружины. Передний прижим (стружколоматель) настраивают по высоте вращением гаек. Регулировку ведут до тех пор, пока расстояние от стола до рабочей кромки стружколомателя не будет равно настроечному размеру. Силу прижима стружколомателя регулируют сжимая или ослабляя пружину.
Роликовые прижимные элементы настраивают так. Открепляют все прижимы по ходу подачи заготовки и регулируют их положение относительно стола и направляющих линеек. При настройке пользуются измерительными шкалами, прикрепленными у регулируемого устройства. Выбирают усилие прижима в зависимости от породы древесины и размеров обрабатываемого материала.
Нижние подающие вальцы устанавливают в зависимости от породы, размера и состояния обрабатываемого материала. Для твердых пород и толстых заготовок величину выступа принимают 0,2-0,3 мм, для мягких пород и тонких пиломатериалов – 0,3-0,5 мм.
Рабочую кромку переднего столика регулируют по высоте рукояткой механизма настройки. Столик должен быть опущен относительно заднего стола на величину снимаемого с нижней пласти слоя.
Затем регулируют верхние подающие вальцы по высоте, устанавливают ограничительную планку и когтевую защиту.
Усилие подачи создают прижимом верхних вальцов и нижним.
Закончив размерную настройку, осматривают подвижные части и устанавливают ограждения. Трубопроводы эксгаустерной сети присоединяют к стружкоприемникам и включают разрежение воздуха в системе отсоса стружек. Включают вращение режущих инструментов. После набора частоты вращения одним шпинделем включают следующий.
Убедившись в безотказной работе всех режущих инструментов на холостом ходу, включают подачу и обрабатывают пробные заготовки.
При правильной наладке допускаются следующие отклонения точности обработанных деталей:
– равномерность по толщине и ширине детали на всей ее длине – по 12-му квалитету;
– непрямолинейность боковых кромок – не более 0,2 мм на длине 1000 мм;
– непараллельность боковых кромок – не более 0,3 мм на длине 1000 мм;
– неперпендикулярность смежных боковых поверхностей – не более 0,15 мм на длине 100 мм.
Если станок не оснащен загрузочно-разгрузочными устройствами, его обслуживают двое рабочих. Станочник укладывает заготовку на стол, базируя ее кромкой по направляющей линейке. После захвата заготовки подающими вальцами станочник берет следующую заготовку и подает ее без межторцовых разрывов.
Второй рабочий принимает готовые детали, проверять качество обработки и складывает в штабель.
При механизированной загрузке и разгрузке станка станочник следит за работой всех элементов станка.
Нельзя подавать заготовки с большими припусками, слишком тонкие и покоробленные. При заклинивании или остановке заготовки нужно включить обратную подачу и вывести заготовку из станка. При появлении мшистости и ворсистости на обработанных поверхностях меняют затупившиеся фрезы.
4-сторонний продольно-фрезерный станок 4ФМ-180/4 предназначен для обработки прямых и фасонных поверхностей с четырех сторон за один проход при производстве деталей для мебельных, строительно-столярных и других изделий. Используется для серийного либо массового производства погонажныж изделий, столярных изделий, картинных рам, мебели, вагонки, половой доски, деревянного упаковочного материала из древесины мягких или твердых пород.