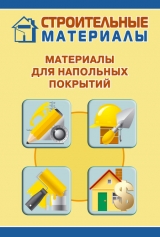
Текст книги "Материалы для напольных покрытий"
Автор книги: Илья Мельников
Жанр:
Хобби и ремесла
сообщить о нарушении
Текущая страница: 2 (всего у книги 4 страниц) [доступный отрывок для чтения: 2 страниц]
Прочность. Прочность – способность материала сопротивляться разрушению под влиянием внутренних напряжений, возникающих в результате действия на материал внешних нагрузок или других факторов. В построенном здании почти все конструкции испытывают нагрузки (вес частей здания, вес оборудования, вес мебели и др.), вследствие чего в материалах конструкций возникают напряжения, противодействующие внешним силам.
Основными показателями, характеризующими прочность материала, являются сопротивление сжатию, растяжению, изгибу. Прочность материала при сжатии и растяжении характеризуется его пределом прочности. Предел прочности, или временное сопротивление, – напряжение в материале образца, соответствующее нагрузке, при которой он разрушается.
Предел прочности различных материалов при сжатии и растяжении меняется в широких пределах – от 0,5 до 1000 МПа и более. Для многих материалов предел прочности при сжатии резко отличается от предела прочности при растяжении. Одинаково хорошо сопротивляются сжатию и растяжению такие материалы, как сталь, древесина. Плохо сопротивляются растяжению каменные материалы: природный камень, кирпич, бетон и т.п.
Примером прочности конструкции при изгибе может служить мост, доска через канаву, а также балка, на которую опираются плиты перекрытия, стропила крыши.
Твердость. Твердость – это способность материалов сопротивляться проникновению в него другого более твердого тела. Твердость не всегда соответствует прочности материала. Существуют несколько способов определения твердости. Например, твердость каменных материалов оценивают шкалой Мооса, состоящей из десяти минералов, расположенных по степени возрастания их твердости. Показатель твердости испытуемого материала находится между показателями твердости двух соседних минералов, из которых один чертит, а другой сам чертится этим материалом.
1 Тальк или мел (легко чертится ногтем).
2 Гипс или каменная соль (чертится ногтем).
3 Кальцит или ангидрит (легко чертится стальным ножом).
4 Плавиковый шпат (чертится стальным ножом под небольшим нажимом).
5 Апатит (сталь) (чертится стальным ножом под большим нажимом).
6 Полевой шпат (слегка царапает стекло, стальным ножом не чертится).
7 Кварц (легко чертит стекло, стальным ножом не чертится).
8 Топаз.
9 Корунд.
10 Алмаз.
Износ. Износ – это разрушение материала при совместном действии истирания и удара. Прочность при износе оценивается потерей в массе, выраженной в процентах. Износу подвергаются материалы дорожных покрытий, полов промышленных предприятий, аэродромов и др.
Сопротивление удару. Сопротивление удару имеет большое значение для материалов, применяемых в дорожных покрытиях и полах. Испытание материалов на удар производят на специальном приборе – копре.
Технологические свойства строительных материаловТехнологические свойства характеризуют способность материала подвергаться тому или иному виду обработки. Так, древесина хорошо обрабатывается инструментами. Технологические свойства некоторых полимерных материалов включают способность сверлиться, обтачиваться, свариваться, склеиваться. Глиняные, бетонные и иные смеси обладают пластичностью, вязкостью, которые обеспечивают заполнение определенного объема.
Вязкость. Вязкость – это сопротивление жидкости передвижению одного ее слоя относительно другого. Когда какой-либо слой жидкости приводится в движение, то соседние слои также вовлекаются в движение и оказывают ему сопротивление, величина которого зависит от температуры и вещественного состава. Вязкостные свойства важны при использовании органических вяжущих веществ, природных и синтетических полимеров, красочных составов, масел, клеев. При нагревании вязкость этих материалов снижается, при охлаждении – повышается.
Упругость. Упругость является свойством материала восстанавливать после снятия нагрузки свою первоначальную форму и размеры. Пределом упругости считается напряжение, при котором остаточные деформации впервые достигают некоторой очень малой величины.
Пластичность – способность материала деформироваться без разрыва сплошности под влиянием внешнего механического воздействия и сохранять полученную форму, когда действие внешней силы закончится. Все материалы делятся на пластичные и хрупкие. К пластичным относят сталь, медь, глиняное тесто, нагретый битум и др.
Акустические свойства строительных материаловАкустические свойства проявляются при действии звука на материал. Акустические материалы по назначению могут быть звукопоглощающие, звукоизолирующие, вибропоглощающие и виброизолирующие.
Звукопоглощающие материалы. Звукопоглощающие материалы предназначены для поглощения шумового звука. Их акустической характеристикой является величина коэффициента звукопоглощения, равная отношению количества поглощенной материалом звуковой энергии к общему количеству звуковой энергии, падающей на поверхность материала в единицу времени. Как правило, такие материалы имеют большую пористость или шероховатую, рельефную поверхность, поглощающую звук. Строительные материалы, у которых коэффициент звукопоглощения выше 0,2, называют звукопоглощающими.
Звукоизолирующие материалы. Звукоизолирующие материалы применяют для ослабления ударного звука, передающегося через строительные конструкции здания из одного помещения в другое. Звукоизоляционные материалы оценивают по двум показателям: относительной сжимаемости под нагрузкой в процентах и динамическому модулю упругости.
Вибропоглощающие и виброизолирующие материалы предназначены для предотвращения передачи вибрации от машин и механизмов к строительным конструкциям.
Ниже приводятся некоторые свойства строительных материалов.

Химические свойства строительных материалов
Химические свойства характеризуют способность материалов реагировать на внешние воздействия, ведущие к изменению химической структуры, а также воздействовать в этом отношении на другие материалы. Основные химические свойства: растворимость и стойкость к коррозии (кислотостойкость, щелочестойкость, газостойкость).
Растворимость. Растворимость – это способность материала растворяться в жидких растворителях: воде, керосине, бензине, масле и других, образовывая новые растворы. Растворимость зависит от химического состава веществ, давления и температуры. Показателем растворимости является произведение растворимости, представляющее собой предельное содержание растворенного вещества в граммах на 100 мл раствора при нормальном давлении и заданной температуре.
Стойкость к коррозии. Стойкость к коррозии является свойством материала сохранять свои качества в условиях агрессивной среды. Такой средой могут быть вода, газы, растворы солей, щелочей, кислот, органические растворители, а также биологические организмы (бактерии, водоросли и т.п.). Древесина, пластмассы, битумы и некоторые другие органические материалы при обычных температурах относительно стойки к действию кислот и щелочей средней и слабой концентрации.
Адгезия. Адгезия представляет собой соединение, сцепление твердых и жидких материалов по поверхности. Это свойство обусловлено межмолекулярным взаимодействием. Адгезионные силы сцепления очень важны при получении строительных материалов, состоящих из многих компонентов, например железобетон.
Кристаллизация. Кристаллизия представляет собой процесс образования кристаллов из паров, растворов, расплавов при электролизе и химических реакциях, который сопровождается выделением тепла.
Долговечность. Долговечность представляет собой способность материала сопротивляться комплексному действию атмосферных и других факторов в условиях эксплуатации. Старение – это процесс постепенного изменения, ухудшения свойств материалов в условиях эксплуатации.
Знание этих и других свойств позволяет сравнивать материалы между собой и определять область их применения с учетом технико-экономической целесообразности. Так, в условиях эксплуатации гидротехнических сооружений строительные материалы, изделия и конструкции, из которых они построены, подвергаются периодическому или постоянному воздействию воды и агрессивных сред, поэтому к ним предъявляются повышенные требования по водостойкости, морозостойкости, водонепроницаемости, корроизонной стойкости и др.
Многие материалы под влиянием водопоглощения ярко проявляют повышенные пластические свойства. Практика строительства показывает, что выбор технически целесообразного материала обосновывают не только его прочностные характеристики, но стойкость к воздействию внешней среды, в которой работает конструкция. Обычно эта стойкость материала во времени (долговечность) неразрывно связана с его химическими и физико-химическими свойствами. Физико-химические в свою очередь тесно связаны со структурой материала и зависят от ее изменения под влиянием внешних и внутренних факторов.
Вследствие проникновения химических реагентов из внешней среды внутренние химические реакции с образованием новых соединений могут значительным образом отразиться на структуре. Изменение структуры (микроструктуры и макроструктуры) в первый период может привести к псевдоупрочнению, а в дальнейшем – к сокращению долговечности материала. Применяемый в строительстве материал обычно подвергают технологической обработке. Cпособность поддаваться такой обработке является порой решающим показателем при выборе материала. Так, при массовой заготовке щебня для бетонных работ учитывается способность горной породы дробиться без образования плоских щебенок, поэтому при выборе материалов всегда учитывают его способность реагировать на отдельные или взятые в совокупности следующие факторы: физические, механические, внешнюю среду, температуру и ее колебания, химические реагенты, технологические операции и т.д. Эта способность материала реагировать на указанные факторы определяется его свойствами.
Оценить технические свойства и сравнить материалы между собой возможно по показателям, которые получают при испытании материалов в полевых, производственных или лабораторных условиях. Полученные знания основных технических свойств строительных материалов и изделий дают возможность рационально их использовать в строительстве. Например, по известным значениям истинной и средней плотности строительных материалов можно рассчитать, какой плотностью (или пористостью) обладают эти материалы, и составить достаточно полное представление о прочности, теплопроводности, водопоглощении и других важных характеристиках строительных материалов, чтобы в дальнейшем на этом основании решать вопрос об их применении в тех или иных сооружениях и конструкциях.
Для расчета нагрузок при определении массы сооружений для транспортных расчетов и выбора емкости складских помещений необходимо знать величину средней плотности строительных материалов. Без данных о прочности применяемых материалов невозможны расчеты прочности и устойчивости сооружений и конструкций. Прогноз их долговечности невозможен без знания таких свойств материала, как отношение к влаге, воздействию окружающей среды, смене температур и др.
Свойства материалов не остаются постоянными, а изменяются во времени в результате механических, физико-химических и биохимических воздействий среды, в которой эксплуатируется строительная конструкция или изделие. Эти изменения могут протекать и медленно (разрушение горных пород), и быстро (вымывание из бетона растворимых веществ). Следовательно, каждый материал должен обладать не только свойствами, позволяющими применять его по назначению, но и определенной стойкостью, обеспечивающей долговечную эксплуатацию изделия или конструкции.
Знание основных свойств строительных материалов необходимо также для выполнения расчетов, позволяющих оценить их качество, соответствие техническим требованиям, возможность применения в конкретных условиях эксплуатации.
Употребляемые в строительстве материалы должны удовлетворять определенным требованиям, которые устанавливаются государственными стандартами (ГОСТами). В строительстве соответствие поступающих материалов требованиям ГОСТа проверяют специальные лаборатории.
Любой вид продукции обладает определенными свойствами, представляющими интерес для потребителей. Для строительных материалов важны такие качества, как прочность, плотность, теплопроводность, морозостойкость, стойкость по отношению к действию воды, агрессивных сред и др. Качеством называется сумма свойств, определяющих пригодность материала и изделия для использования по назначению. Так, для кровельных материалов оценка их качества производится по сумме таких свойств, как водостойкость, водонепроницаемость, термостойкость, прочность на изгиб, атмосферостойкость и др.
Контроль качества строительных материалов и изделий проводят по разработанным нормам, требованиям и правилам. В зависимости от контролируемого производственного этапа различают контроль входной, технологический и приемочный.
Входной контроль включает проверку соответствия поступающих материалов и изделий установленным требованиям. Например, на предприятиях сборного железобетона проверяют качество поступающих исходных материалов: заполнителей и цемента для бетона, арматурной стали, закладных деталей, отделочных и других материалов.
Технологический контроль состоит в проверке соответствия установленным требованиям температуры, давления, времени выдерживания, тщательности перемешивания и других показателей технологического процесса.
Приемочный контроль заключается в проверке соответствия готовых изделий требованиям стандартов или технических условий.
Все материалы и изделия выпускают по государственным и межгосударственным стандартам – ГОСТ, СТ СЭВ, ИСО, СТБ, СНБ. Деятельность стандартизации существует для повышения качества продукции, безопасности ее получения и безопасности. Методы испытаний также стандартизированы. Кроме этого, в строительстве существуют «Строительные нормы» и «Технические нормативные правовые акты», представляющие собой объединенные нормативные документы по проектированию, строительству и строительным материалам.
МАТЕРИАЛЫ ДЛЯ НАПОЛЬНЫХ ПОКРЫТИЙ
Полы являются основой внутреннего убранства жилых и общественных помещений и их надежности. Поэтому напольное покрытие должно быть прочным, удобным, безопасным, долговечным и эстетичным. Полы в зависимости от расположения (на перекрытии или грунте) состоят из следующих основных конструктивных элементов:
– подстилающий слой;
– выравнивающий слой (стяжка);
– теплоизоляционный, гидроизоляционный, звукоизоляционный слой;
– прослойка;
– покрытие.
Подстилающий слой. Подстилающий слой для полов на грунте изготавливают из бетона толщиной 100…150 мм. Если в грунтовых водах имеются минеральные кислоты, применяют кислотостойкий бетон на жидком стекле. При наличии в водах растворов сульфатов используют сульфатостойкий бетон на шлакопортландцементе или сульфатостойком портландцементе. Подстилающим слоем в междуэтажных перекрытиях является несущая железобетонная плита или иной элемент перекрытия.
Выравнивающий слой. Выравнивающий слой (стяжка) служит для выравнивания подстилающего слоя, создания определенного технологического уклона или для обеспечения жесткости. Стяжки могут быть сплошными – наливными из цементно-песчаного раствора, легкого бетона, асфальтобетона, сборными. Для сборных стяжек используют бетонные плиты, твердые плиты ДВП и некоторые другие материалы. Минимальная прочность материала на изгиб должна быть не мене 2,5…3 МПа.
После выравнивающего слоя располагают материалы специального назначения: антикоррозийную гидроизоляцию, теплоизоляцию, звукоизоляцию. В качестве гидроизоляции используют рубероид на битумной мастике, изол, гидроизол, армированную пленку на синтетическом клее и др. В качестве утепляющего слоя используют сыпучие материалы (керамзит, шлак, аглопорит), а также плиты и блоки из ячеистого и легкого бетона на пористых заполнителях. Звукоизоляционный слой при устройстве пола на междуэтажном перекрытии. Здесь можно использовать песок, шлак, перлит, минераловатные плиты и маты, а также ковровые изделия и двухслойный звукоизоляционный линолеум, используемый для верхнего покрытия.
Прослойка. Назначением прослойки из цементно-песчаного раствора или раствора на жидком стекле или иных материалов под напольное покрытие является обеспечение совместной работы покрытия с нижележащими слоями. Она служит для закрепления рулонных и мелкоштучных материалов.
Покрытие. Покрытие – это верхний, лицевой элемент пола, который непосредственно подвергается эксплуатационному воздействию.
Типы и виды напольных покрытий. По типу укладки полы бывают из штучных, рулонных и плиточных материалов. Вид (название) пола определяется материалом, из которого полы сделаны:
– дощатый;
– из древесноволокнистых плит;
– паркетный – штучный, паркетная доска, щитковый, наборный (мозаичный или художественный) и массивная доска;
– ламинированное покрытие;
– линолеум;
– пробка;
– ковровое покрытие (ковролин);
– природные каменные материалы – гранит, мрамор, сланец, песчаник;
– мозаичная плитка;
– гипсокартон и др.
В зависимости от материала полы подразделяются на теплые и холодные. Теплые полы делают из материалов с небольшой сравнительной плотностью и малым коэффициентом теплоусвоения. Теплыми полами являются полы дощатые и паркетные. Как правило, их устраивают в помещениях с долговременным пребыванием людей (жилые комнаты, классы в школах, служебные помещения и др.). Кроме дощатых и паркетных полов, в жилых и общественных помещениях устраивают полы, где в качестве напольных покрытий используют линолеум, ДСП, сверхтвердую ДВП, рулонные материалы на основе химических волокон и др.
Холодные полы делают в производственных помещениях и с кратким пребыванием людей (ванные, санузлы, вестибюли, вокзалы и др.) – бетонные, цементные, из керамической плитки, плиты из природного камня и т.д.
Дощатые полы. Деревянные полы бывают дощатые, паркетные и торцовые. Дощатые полы настилают из строганых досок толщиной не менее 37 мм, шириной 120…150 мм. Материалом дощатых полов служит древесина сосны, ели, лиственницы и других пород с влажностью при укладке не более 12 %.
Полы первого этажа можно укладывать по лагам, размещенным на кирпичных столбиках через 0,8…1 м. На кирпичные столбики укладывают слой толя или другого материала и антисептированные деревянные подкладки. Лаги выверяют по уровню и не доводят на 30…50 мм до стен. Лаги изготовляют в виде пластин из распиленных пополам бревен диаметром 140 …160 мм. В местах укладки на опорах круглую часть лаги подтесывают. Дощатые полы в узких помещениях настилают по длине помещения. Их сплачивают скобами и сжимающими клиньями.
Гвоздями сначала прибивают только каждую четвертую или пятую доску, через год эксплуатации (усыхания досок) полы вновь сплачивают с прибивкой каждой доски. Вдоль стен прибивают плинтусы.
На междуэтажных перекрытиях полы настилают по лагам, которые укладывают поперек балок, ребер плит или другим опорам. По гладким поверхностям железобетонных конструкций лаги укладываются на уравнительных подкладках из досок. Доски прибивают к лагам гвоздями длиной в 2…2,5 раза больше толщины досок, утапливая шляпки в древесину. Неровности дощатых полов устраняют простружкой электрорубанком.
Зазоры между полом и стеной закрывают плинтусами или галтелями, для проветривания подполья устанавливают специальные плинтусы или вентиляционные решетки.
После прострожки полы покрывают горячей олифой, а окраску полов делают по окончании всех работ в помещении.
Полы из древесноволокнистых плит. В жилых и административных зданиях устраивают полы из древесноволокнистых сверхтвердых плит. Покрытие из сверхтвердых плит бесшумно при ходьбе, легко моется, устойчиво на истирание, не пылиться, имеет хороший внешний вид.
При устройстве полов по панелям с пустотами насыпают слой песка толщиной 50…60 мм, являющийся звукоизолятором. По засыпке делают цементно-песчаную стяжку и после высыхания ее очищают, обеспыливают и покрывают битумной грунтовкой. Через 40…48 часов, когда грунтовка подсохнет, на стяжку наносят горячую битумную мастику температурой 160 – 165 0С и укладывают твердые древесноволокнистые плиты толщиной 4 мм, после чего наклеивают сверхтвердые древесноволокнистые плиты толщиной 4…5 мм. Так как горячая мастика быстро остывает, ее наносят только под один лист плиты.
При устройстве полов на сплошных железобетонных панелях сначала наклеивают на горячей мастике слой из мягких древесноволокнистых плит толщиной 12 мм, а затем слой твердых древесноволокнистых плит толщиной 4 мм, а сверху него покрытие из сверхтвердых древесноволокнистых плит толщиной 4…5 мм. Плиты укладывают от стены, перегородки на расстоянии 5…10 мм. Стыки плит должны располагаться со швами вразбежку и не совпадать со стыками нижележащих твердых древесноволокнистых плит. Зазор в стыках не должен быть более 0,3 мм. Стыки шпатлюют водостойкими шпатлевками и после высыхания зачищают шкуркой и обеспыливают пылесосом. Все покрытие покрывают водостойкими красками или эмалями, а затем светлым лаком. Окрашивают пол за 2 раза, просушивая каждый ранее нанесенный слой.
Паркетные полы. Паркетные полы изготовляют из планок (паркета) древесины лиственных пород – дуба, ясеня, бука, граба, вяза, груши, клена, грецкого ореха, маньжурского ореха, березы, бамбука и др. Характеристика и эстетические свойства паркетны полов определяются качеством и сортом древесины. Важнейшим качеством исходного материала является твердость, которая зависит от породы, условий роста и влажности древесины. Древесина лиственных пород отличается более высокой твердостью и износостойкостью по сравнению с хвойными породами. По географической принадлежности древесина делится на местную (дуб, бук, ясень, клен, граб) и экзотическую – махагон, мербау, сайма, тик, венге, камбала, дуссие, ирокко, че, кемпас, ярра, ятоба, бамбук, зебрано, инченцо, олива, лапаччо и др.
Каждой породе древесины, помимо особенностей ее микроструктуры, степени устойчивости к внешним воздействиям, присущ свой естественный цвет. Такие породы, как клен, бук, черешня, груша, меняют оттенок цвета в зависимости от угла падения света. У бука, ясеня, березы, сосны, клена, лиственницы светлый цвет древесины. У ореха, красного и черного дерева – темный. У дуба, граба, груши, вишни, тика, оливкового дерева цвет промежуточный.
Виды паркетных полов и массивная доска. Настилка полов производится наборным паркетом или щитовым паркетом. Деревянные изделия для паркетных покрытий подразделяются на штучный паркет, паркетные доски, паркетные щиты и мозаичный паркет.
Изготовляют паркет с пазами, закрепляют вкладными шипами и гвоздями или мастикой.
Штучный паркет имеет размеры:
– толщина – 15 (18) мм;
– ширина – 30…90 мм с градацией через 5 мм;
– длина – 150…500 мм через 50 мм.
Паркетные доски изготовляют размерами:
– длина – 1200, 1800, 2400, 3000мм;
– ширина – 137, 145, 155, 200 мм;
– толщина – 15, 18, 23, 25, 27 мм.
Натуральная паркетная доска изготавливается из трех слоев древесины и отличается от штучного паркета большей подготовленностью к укладке, что позволяет осуществить настил качественного деревянного пола за несколько дней.
Паркетные щиты представляют собой изделия, состоящие из основания, на которое наклеено лицевое покрытие из паркетных планок или квадров шпона квадратами, расположенными в шахматном порядке. Пазы в кромках щитов служат для соединения их между собой с помощью шпонок или гребней.
Паркетные щиты изготовляют размерами 400 х 400 мм; 500 х 500 мм; 600 х 600 мм; 800 х 800 мм при толщине 22, 25, 28, 32, 40 мм.
Паркетные планки делают длиной 100…400 мм, шириной 20…50 мм, толщиной 4, 6, 8 мм.
Квадраты шпона изготовляют длиной и шириной 100…400 мм, толщиной не менее 4 мм.
Наборный паркет укладывают на гвоздях, на битумной мастике.
Мозаичный (наборный) паркет представляет собой карты из мелкой планки, наклеенной на бумагу. Наборный паркет представляет собой сочетание фрагментов разной формы, обычно выполненных из различных пород дерева, образующих на полу оригинальные мозаичные композиции.
Мозаичные паркетные карты приклеивают к основаниям на холодных или горячих мастиках. Настилку начинают с укладки мячного ряда из карт в центре помещения по шнуру, натянутому согласно размещению рисунка паркетного покрытия в помещении. Слой мастики под карты из планок наносят толщиной 1…1,5 мм, осаживая карты легкими ударами киянки. Через сутки после затвердения мастики швы между планками или картами заполняют ксилолитовой массой при помощи деревянного шпателя.
Щитовой паркет изготовляют массивным, листовым, щитовым на листовом материале, из паркетных досок. Щитовой паркет выпускается в готовом виде, с лаковым покрытием. Так же, как и мозаичный, щитовой паркет укладывают по твердым основаниям на битумных мастиках, лучше на резинобитумной.
Приготовление резинобитумной мастики. Для приготовления резинобитумной мастики необходимо взять битума БН 70/30 – 61 % (по массе), бензина – 26,5 %, каучука – 0,5 %, каолина – 12 %.
Приготовляется мастика в заводских условиях следующим способом: в разогретый до температуры 160…180 0С битум вводят каолин и охлаждают смесь до 90…100 0С, затем в нее вливают резиновый коллоидный раствор (каучук в бензине) и всю массу перемешивают и охлаждают до нормальной температуры. Во время работы загустевшую мастику можно разжижать, добавив немного бензина. Намазывают мастику зубчатым шпателем тонким слоем за два–три приема на площади 2…3 м кв. и последнему слою дают просохнуть 20…30 минут.
Настилка паркетных досок производится по лагам из брусков толщиной 40…60 мм на звукоизоляционных подкладках из древесноволокнистых плит через 40…50 см одна от другой. Если лаги опираются на железобетонные плиты или твердые стяжки, их изготовляют толщиной 25 мм. Паркетные доски соединяют между собой в шпунт и к лагам прикрепляют гвоздями длиной 60…70 мм. Забивают их в паз.
Окончательную отделку паркетного пола (острожка, циклевка, шлифовка) выполняют после завершения малярных работ. После настилки всего паркетного покрытия производят его циклевку и шлифование специальными машинами. Отшлифованную поверхность паркетного покрытия покрывают двумя слоями лака или натирают восковой мастикой.
Торцовые полы изготовляют из деревянных шашек высотой 60…80 мм прямоугольной или шестигранной формы из хвойных и лиственных пород древесины (за исключением пихты, березы, бука и дуба). Перед укладкой шашки антисептируют. Торцовые полы устраивают в производственных помещениях с ударными нагрузками с основаниями на грунте, иногда по железобетонным междуэтажным перекрытиям.
Укладывают шашки под шнур и правило на слой сухого песка толщиной 10…20 мм или на горячие битумные мастики слоем 2…3 мм. При укладке на горячих мастиках каждую шашку погружают в горячую мастику (кроме верхнего торца), устанавливают на место и осаживают легкими ударами киянки или молотка на деревянной прокладке. Швы между шашками должны быть не более 2 мм.
Массивная доска. Ранее массивную доску в качестве напольных покрытий, как правило, использовали при строительстве самых простых сооружений. Массивная доска представляет собой цельную доску из массива дерева. Благодаря большим размерам плашек, массивная доска позволяет максимально увидеть красоту дерева.
Паркетные полы обладают следующими преимуществами:
– низкая теплопроводность и звукопроводность;
– разнообразие древесных пород и красивая гамма цветов;
– естественность и красота материала;
– ударопрочность;
– разнообразие способов укладки: «елочка одинарная», «елочка двойная», «палуба», «квадрат полный», «квадрат неполный», укладка по диагонали и т.д.;
– возможность сочетания фрагментов разной формы и разных пород дерева, образующих на полу оригинальные мозаичные композиции (художественный паркет);
– долговечность;
– износостойкость.
Долговечность паркета зависит от его покрытия, технологии изготовления, укладки, качества материала и т.д. Лакированный паркет может прослужить 10 лет до первого ремонта. Покрытия маслом или воском нужно обновлять ежегодно. Штучный паркет может прослужить тридцать лет, если установлен с помощью мастики и лаги на полы из шпунтованной обрезной доски. Паркет на клеевой основе, который укладывается на мастику с подкладкой из ДВП, простоит 10 – 20 лет. Паркетная доска – 5 лет. Недостатками паркета являются его чувствительность к температурному режиму и влажности. Оптимальная для него температура – от 18 до 23 градусов, сырость и влажность паркет разрушают.
Ламинированное покрытие. Ламинат – это не материал. Ламинирование представляет собой нанесение на основу пластиковой пленки, имитирующей какой-либо натуральный материал. Основой может служить бумага, картон, ДСП, МДФ, стальные листы. Высококачественные ламинированные покрытия в настоящее время производят многие известные мировые компании.
Ламинат представляет собой тонкие (7 – 11мм) листы длиной 1000 – 1400 мм и шириной 190 – 200 мм, которые по краям снабжены шипами и пазами для стыковки друг с другом (как у паркета). Новейшие технологии производства и современный дизайн поверхности ламината максимально приближает его к паркету, и визуально ламинат довольно сложно отличить от натурального материала. Ламинированные панели точно передают внешний вид и фактуру не только дерева, но и камня, пробки. Они не отличаются от натуральных материалов ни цветом, ни наглядной структурой.
Ламинированные полы делятся на следующие классы износоустойчивости: 21, 22, 23, 31, 32, 33. Ламинат отличается следующими свойствами: устойчивостью к воздействию ультрафиолетового излучения, выцветанию (светостойкость); абразивной устойчивостью (сопротивление к истиранию); антистатичностью; простотой укладки; пригодностью для монтажа системы отопления в полу (как правило, водяного и только для бесклеевых систем); гигиеничностью; твердостью и прочностью; любые загрязнения (краска, жир и др.) легко удаляются с поверхности ламината водой, моющими средствами или растворителями, не влияя на декоративные качества пола; ламинат не боится острых предметов – царапины на нем заделать очень легко.
Основными недостатками ламината является его одноразовость (срок службы 5 – 8 лет, после чего его уже невозможно восстановить) и недостаточная влагостойкость. У ламинированного пола среднего качества от длительного соприкосновения с водой может немного нарушиться геометрия планок. Для ежедневного ухода рекомендуется использовать влажную ткань или пылесос. Моющие средства могут оставить белесые пятна.