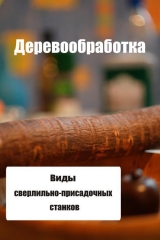
Текст книги "Виды сверлильно-присадочных станков"
Автор книги: Илья Мельников
Жанр:
Хобби и ремесла
сообщить о нарушении
Текущая страница: 1 (всего у книги 2 страниц) [доступный отрывок для чтения: 1 страниц]
Илья Мельников
Виды сверлильно-присадочных станков
Классификация станков
По назначению деревообрабатывающие станки подразделяют на три группы: универсальные, имеющие широкое распространение в различных деревообрабатывающих производствах; специализированные, предназначенные для выполнения только определенных видов работы с переналадкой станка, и специальные для определенной обработки без переналадки станка.
Деревообрабатывающие станки могут быть цикловые – с прерывистым движением детали или режущего инструмента и проходные – с непрерывным перемещением детали. У проходных станков деталь непрерывно перемещается относительно рабочих органов и при этом обрабатывается.
В зависимости от способа обработки древесины и вида технологической операции различают станки круглопильные, ленточнопильные, фуговальные, рейсмусовые, четырехсторонние, фрезерные, шипорезные, сверлильно-пазовальные, токарные, шлифовальные и др.
Для обозначения вида и станков принята буквенно-цифровая индексация. Первая буква обозначает тип станка: Л – ленточный, Ц – круглопильный, С – четырехсторонний продольно-фрезерный, фуговальный, рейсмусовый, фрезерный, Ш – шипорезный, СВ – сверлильный, Шл – шлифовальный и т. д.
Цифры после первой буквы указывают на количество рабочих органов или агрегатов станка: например С2Ф – фуговальный станок с двумя (горизонтальным и вертикальным) режущими инструментами и т. п.
Вторая и третья буквы характеризуют технологические особенности станка: ЛС – ленточнопильный столярный, ЦДК – круглопильный для продольной распиловки с конвейерной подачей, СР – рейсмусовый, ФС – фрезерный средний, СВПГ – сверлильно-пазовальный горизонтальный и т. д.
Цифры после букв индекса характеризуют главный параметр станка либо номер модели станка: СР6-9 – станок рейсмусовый, ширина стола 630 мм, девятая модель и т. д.
Основные агрегаты станков
Различаясь технологическим назначением и способом обработки детали, деревообрабатывающие станки имеют подобные конструктивные элементы и функциональные механизмы. Использование в разных станках повторяющихся нормализованных элементов и деталей называют нормализацией.
Иногда станки полностью состоят из одинаковых составных частей и отличаются один от другого только взаимным расположением рабочих органов. Такое заимствование элементов называют унификацией.
Когда станки собирают из отдельных агрегатов, которые выпускаются специализированными заводами, такие станки называют агрегатными.
Элементы станков разделяют по выполняемым функциям. Для установки и монтажа всех составных частей станка служит станина. Она устанавливается на фундамент или специальные виброизолирующие опоры. На станине располагаются корпусные детали, которые воспринимают нагрузки от рабочих органов и образуют контур станка – основания, стойки, поперечины, траверсы, кронштейны и т. д. Корпусные детали не перемещаются в ходе работы, но в ряде случаев их положение можно менять до начала обработки изделия.
Требование к станине и корпусным деталям – точность и жесткость, так как эти показатели влияют качество обработки деталей.
Агрегаты станка, обеспечивающие главное движение, называют механизмом резания. Механизм резания с выполняют в виде ножевого вала, шпинделя или пильного вала. На них крепят режущий инструмент.
Следующий агрегат – механизм подачи. Он предназначен для обеспечения подачи заготовки. Выполняется в виде конвейера, вальцов или роликов. (В цикловых станках механизмом подачи является подвижный стол или каретка.)
Расположение заготовки относительно режущего инструмента устанавливается специальными устройствами. Они включают базовые элементы станка: столы, направляющие линейки, угольники, упоры, прижимные приспособления. С помощью их достигается устойчивое положение обрабатываемой детали в проходных станках. Прижимы делают в виде клиновых ремней или лент.
На позиционных станках используются зажимы в виде колодок и пластин. Для предотвращения порчи детали рабочие элементы зажимов оснащаются съемными резиновыми накладками.
Для обеспечения настроечных перемещений служат суппорты, которые могут переставляться вручную или от механического привода. У суппорта точно обработанные поверхности, которые называют направляющими. Такие же направляющие есть на станине или корпусной детали, на них и устанавливается суппорт.
Оградительные и предохранительные устройства. Они бывают в виде колпаков, кожухов, крышек. Эти части станка предохраняют рабочего от случайного касания движущихся механизмов станка. (Ограждения блокируют с приводом станка, чтобы при их снятии станок автоматически выключался.)
Управляются станки с помощью маховиков, педалей, рукояток, кнопок и переключателей. В сложных станках органы управления выполняются в виде пульта, на котором расположены кнопки включения и выключения рабочих органов.
И последнее – вспомогательные элементы. К ним относят устройства для смазывания трущихся частей станка: масленки, шприцы, насосы для подачи масла.
Базирующие устройства служат для обеспечения качественной обработки детали – с их помощью осуществляется ориентирование, базирование и закрепление заготовки в нужном положении относительно рабочих органов станка. Ориентирование заготовки производится вручную или специальным ориентирующим устройством: винтовыми роликами, диском, отклоняющим щитком.
Базирование – ответственный этап механической обработки, так как качество его выполнения определяет точность обработанной детали. Правильная взаимная ориентировка детали и рабочих инструментов в станке определяется назначением технологических баз. Технологическая база – это совокупность базирующих поверхностей, используемых для придания заготовке заданного положения относительно режущего инструмента.
Обрабатываемые детали бывают прямолинейные с профильным поперечным сечением, в виде тела вращения или сложной пространственной формы. Базирующими поверхностями призматической заготовки являются ее пласть, кромка и торец, которые соответственно называются главная, направляющая и упорная поверхности. При базировании эти поверхности соприкасаются с опорными элементами станка. В зависимости от вида контакта заготовки с элементами различают подвижное и неподвижное базирование.
При подвижном базировании заготовка находится с опорным элементом в состоянии подвижного контакта. При неподвижном базировании заготовка в процессе обработки неподвижна относительно опорных элементов станка.
Элементы базирования деталей бывают разных конструкций. Это столы, направляющие линейки, упоры, патроны, планшайбы токарных станков.
Столыдля неподвижного базирования деталей представляют собой массивные плиты с плоской рабочей поверхностью. Стол для подвижного базирования детали должен иметь гладкую поверхность с низким коэффициентом трения. Кромка стола, примыкающая к режущему инструменту, в процессе эксплуатации обычно изнашивается и эту часть стола обычно оснащают съемной стальной накладкой. На столе монтируют направляющие линейки или угольники.
Иногда столы оснащают роликами или делают в виде роликового конвейера. Если ролики приводные, то они являются не только установочными элементами, но и служат средством для транспортировки деталей.
В зоне движения режущего инструмента на столе монтируют деревянную плиту с пазом, которая обеспечивает устойчивое положение отпиливаемых кусков материала.
Направляющие линейки станков исполняются в виде бруса с гладкой поверхностью. Концы линейки, обращенные к пиле, оснащают съемными накладками. Иногда направляющие линейки оснащают вращающимися роликами, что снижает сопротивление подачи обрабатываемого материала.
Упоры служат для точного базирования детали по длине. Они бывают утапливаемыми и откидными. Упор должен иметь достаточную жесткость, иначе при повторяющихся ударных нагрузках он может сместиться, что приведет к браку.
Правильное положение заготовки относительно стола и направляющей линейки при проходной обработке достигается боковым и верхним прижимами. Прижимы делают в виде колодки, подпружиненного башмака, или гибких пластин со скользящей рабочей поверхностью. Для уменьшения трения скольжения применяют роликовый прижим.
На станках с поперечной подачей деталей прижимное устройство выполняют в виде двух параллельных агрегатов, оснащенных бесконечными клиновыми ремнями. Ремни приводятся в движение силами трения о заготовку. Натяжение ремня можно регулировать, смещая ось шкива относительно корпуса прижима.
Наладка и настройка станков
Геометрическая точность станка, правильность наладки и настройки его оказывает существенное влияние на качество обработки деталей.
Деревообрабатывающие станки по точности выполняемых работ подразделяют на четыре класса: особой точности (О), обеспечивающие точность обработки по 10-12-му квалитетам; повышенной точности (П), обеспечивающие точность обработки по 11-12-му квалитетам (фрезерные, четырехсторонние и т. п.); средней точности (С), обеспечивающие обработку по 13-15-му квалитетам (токарные, сверлильные и т. п.); нормальной точности (Н), обеспечивающие точность обработки по 14-18-му квалитетам (ленточнопильные, круглопильные и т. п.).
Рассмотрим основные причины возникновения погрешностей при механической обработке древесины.
Геометрическая неточность станка и его износ. Не секрет, что детали станков часто изготовляют с погрешностями. В процессе сборки станка эти погрешности суммируются, таким образом точность расположения исполнительных поверхностей станка нарушается. На точность станка влияет также износ деталей в процессе эксплуатации.
Искажение формы режущей кромки резца при его заточке, погрешность при установке и закреплении режущего инструмента, а также его биение.
Зажимные и установочные элементы приспособления имеют погрешности даже при самом тщательном изготовлении. При установке заготовки в приспособление возникают погрешности базирования. В приспособлении под действием зажимных усилий и усилий резания возникают упругие деформации, которые также снижают точность обработки.
Недостаточная жесткость системы станок-приспособление-инструмент-деталь (СПИД). Жесткостью этой системы называют способность обеспечивать необходимую точность обработки при нагрузках, возникающих в процессе работы станка.
При обработке партии заготовок силы резания изменяются в зависимости от величины припуска на обработку, степени затупления инструмента и механических свойств древесины, что вызывает упругие деформации технологической системы СПИД. Деформации нарушают расположение установочных поверхностей станка и точность обработки снижается.
Ошибки при настройке станка. Ошибки возникают из-за неправильного отсчета показаний, погрешности измерения пробных деталей, неточности контрольно-измерительного инструмента. Эти ошибки и погрешности образуют результирующую погрешность механической обработки.
Наладка станка – это регулирование и согласование взаимодействия всех элементов станка, установление режимов обработки, пробный пуск и контроль обработанных деталей.
Размерной настройкой станка называют действия по обеспечению требуемой точности расположения режущего инструмента относительно установочных элементов станка (столов, упоров).
Статическая настройка с использованием встроенных в станок измерительных устройств заключается в том, что станочник перемешает рабочий орган на требуемый настроечный размер и одновременно контролирует величину перемещения по отсчетному устройству.
Статическая настройка станка по эталону (шаблону) заключается в регулировке положения инструмента до касания его лезвий рабочей поверхности шаблона. Допускаемое отклонение на настроечный размер должно быть меньше допускаемого отклонения на размер детали, подлежащей обработке. (Часто в качестве эталона используют ранее изготовленную на станке деталь.)
Эталоны применяют при настройке многошпиндельных станков и в тех случаях, когда надо одновременно учитывать несколько настроечных размеров или взаимных положений режущих инструментов, обрабатывающих деталь сложной формы.
Настройка по эталону не всегда обеспечивает необходимую точность. После обработки некоторого количества деталей необходимы дополнительное регулирование и поднастройка станка.
Статическую настройку станка с помощью универсальных измерительных приборов используют в станках, которые налаживают на один настроечный размер или в станках, не имеющих встроенного отсчетного устройства. В качестве измерительного инструмента применяют магнитные стойки, микрометры, штангенциркули. Контроль перемещения рабочего органа в момент его регулировки позволяет достичь высокой точности настройки.
Статическая настройка с помощью настроечно-измерительных приспособлений обеспечивает высокую точность. Эти приспособления конструируют для конкретного станка и изготовления конкретной детали.
Нередко настраивают станок, изготовляя пробные детали. В этом случае станок настраивают сначала с помощью встроенного измерительного устройства или других средств. Предварительную настройку выполняют с меньшей точностью, чем статическую. Обычно величина первоначального настроечного размера существенно отличается от величины среднего размера детали и выбирается такой, чтобы при обработке деталей размер их получался несколько большим, чем нужно, что исключает выпуск неисправимого брака. После предварительной грубой настройки обрабатывают пробные заготовки, детали проверяют калибром или измерительным инструментом.
Эту настройку с контролем деталей предельным калибром осуществляют тем же рабочим калибром, который используют в дальнейшем при контроле деталей всей партии. Если размер пробной детали находится в пределах допуска, настройка считается правильной.
Настройка по пробным деталям позволяет определить по результатам измерений среднее значение размера трех-пяти пробных деталей и поле рассеяния соразмеров. В результате поднастройки получают новое значение настроечного размера. Если этот размер находится в пределах допуска, обрабатывают всю партию деталей.
Этот метод расчета величины поднастройки применяют при обработке небольшой партии деталей, когда износ инструмента невелик и не может оказать существенного влияния на точность обработки.
Сверлильно-присадочные станки
Для сборки деревянных деталей используют отверстия и продолговатые пазы. В брусковых деталях их вырабатывают на сверлильно-пазовальных станках.
По ориентации волокон древесины по отношению к направлению движения подачи различают сверление поперечное и продольное. (Для каждого вида сверления есть своя конструкция режущей части сверла.) Процесс сверления характеризуется скоростью подачи сверла и частотой его вращения. При этом работает преимущественно торцовая режущая часть инструмента.

Рис. Отверстия, получаемые на станках:
а, б, в – сверлильных, г – сверлильно-пазовальных, д, е – цепнодолбежных
При выборке продолговатых пазов, кроме осевой подачи, инструмент совершает и касательное, боковое движение. В этом случае рабочими частями сверла являются не только его торцовые элементы, но и цилиндрическая часть. Работа инструмента в таком режиме затруднена, поэтому выборку глубоких пазов лучше выполнять за несколько проходов, постепенно внедряя сверло в материал и осуществляя качательные движения. Для выполнения этого сложного движения служит специальный механизм пазовального станка.
При сверлении нескольких отверстий в щитовых деталях применяют многошпиндельные сверлильные (присадочные) станки. На них сверлят отверстия одновременно на плоскости и в кромках.
Сверлильный инструмент. На сверлильно-пазовальных станках применяют концевые фрезы для выборки гнезд и сверлильный инструмент для сверления отверстий. Концевые фрезы – затылованные двузубые, сверла – спиральные с подрезателем и направляющим центром; с круговым подрезателем; цилиндрические с конической заточкой; ложечные и полые цилиндрические. Для выполнения углублений под головки шурупов и винтов применяют зенкеры.
Спиральные сверла с подрезателем и направляющим центром диаметром от 6 до 20 мм применяются для сверления отверстий поперек волокон. (Особенность этого вида сверл – наличие главных режущих кромок в плоскости, перпендикулярной оси вращения сверла.)
Сверла с круговым подрезателем применяют для сверления неглубоких отверстий, высверливания сучков, которые потом заделывают деревянными пробками.
Цилиндрические сверла с конической заточкой служат для сверления отверстий вдоль и поперек волокон. (Различаются сверла углами конической заточки.)
Ложечные сверла отличаются наличием одной режущей кромки и продольного желобка для отвода стружки. Они предназначены для сверления отверстий в торце детали вдоль волокон.
Сверла для кольцевого сверления (цилиндрические пилки) применяют для выполнения сквозных отверстий или полуокружностей у краев детали и для выпиливания пробок. Полое сверло с выталкивателем выпиленных кружков имеет диаметр от 20 до 60 мм. Получающиеся при выпиливании пробки используют для заделки сучков. Профиль зубьев цилиндрической пилки подобен профилю зубьев круглых пил с косой заточкой для поперечной распиловки древесины.
Зенкеры бывают цилиндрические (под цилиндрическую головку винта) и конические для выборки конуса под головку полупотайного винта.
Сверлильный инструмент затачивают на заточных станках и контролируют профиль режущих элементов. Сверла с подрезателем и направляющим центром затачивают с задней поверхности лезвия главных режущих кромок, с внутренней стороны подрезателей и по граням пирамиды центра. У правильно заточенного сверла форма подрезателей одинаковая, основные лезвия расположены на одном уровне, а ось центра совпадает с осью сверла.
При конической заточке спиральных сверл добиваются одинаковой длины обеих режущих кромок и равных углов наклона к оси сверла. Перемычка сверла должна быть симметрична относительно оси вращения, длина перемычки не должна превышать 1,5-2 мм.
Вертикальные сверлильно-пазовальные станки. Вертикальные сверлильно-пазовальные станки выпускают с ручной и механической подачей. Сверлильно-пазовальный вертикальный станок с ручной подачей СВП-2 на колонке имеет шпиндель с приводом через ременную передачу и стол. Шпиндель заключен в направляющую гильзу, которая перемещается вверх или вниз от педали или рукоятки. На конце шпинделя установлен патрон для крепления сверла или концевой фрезы с максимальным диаметром 40 мм.
Стол станка расположен на горизонтальных направляющих и имеет продольную подачу. Стол можно переставлять по высоте в соответствии с высотой заготовки и фиксировать в заданном положении. Стол можно поворачивать под углом или устанавливать вертикально, чтобы сверлить отверстие под углом к поверхности детали или в ее кромке. Крепят заготовки эксцентриковым прижимом.
Сверлильно-пазовальный вертикальный станок с механической подачей СВА-2 оснащен дополнительно пневматическим цилиндром для перемещения гильзы со шпинделем и пневмоприжимами.

Рис. Сверлильно-пазовальный станок СВПГ-2:
1 – педаль, 2 – механизм установки стола по высоте, 3 – гидрораспределитель, 4 – кронштейн, 5 – стол, 6 – упорный угольник, 7 – гидроприжимы, 8 – патрон
Частота вращения шпинделя у сверлильных станков обычно не изменяется, но скорость различных точек торцовых режущих кромок сверла разная. Максимальная скорость резания у точек, наиболее удаленных от оси сверла. По мере приближения к центру сверла окружная скорость главного движения уменьшается, а скорость поступательного движения подачи для всех точек одинакова, поэтому в центральной части отверстия волокна древесины не перерезаются, а сминаются и частично разрушаются.
Подачу на один оборот сверла для древесины мягких пород принимают равной 0,7-2,2 мм, твердых – 0,1-0,5 мм. Меньшие значения выбирают при сверлении глубоких отверстий малого диаметра.
При настройке сверлильных станков тип и диаметр сверла или фрезы выбирают в зависимости от характера сверления. Сверла для сверления вдоль волокон нельзя применять для выборки отверстий перпендикулярно волокнам. Угол заточки спиральных сверл должен соответствовать направлению сверления относительно волокон древесины.
При выборе диаметра сверла следует учитывать, что диаметр полученного отверстия бывает больше диаметра сверла на 0,2-0,35 мм из-за разбивки отверстия биением сверла.
Сверла крепят с помощью патронов или устанавливают в шпиндель. В патрон со стопорным винтом устанавливают сверла с цилиндрическими хвостовиками только одного диаметра. Недостаток этого патрона – он не обеспечивает точного центрирования сверла.
Более распространены трех– и двухкулачковые самоцентрирующиеся патроны. Они позволяют закреплять сверла с разными диаметрами хвостовика. Сверло в патроне крепят кулачками, сдвигая их гайкой в радиальном направлении. Зажимают сверло так, чтобы оно во время работы не проворачивалось. Вращая шпиндель вручную, убеждаются, что сверло закреплено не имеет биения. Точность установки сверла зависит от степени износа патрона.
Стол по высоте устанавливают так, чтобы в крайнем верхнем положении шпинделя расстояние от вершины сверла до рабочей поверхности стола было на 20 мм больше высоты обрабатываемой детали.
Упоры, ограничивающие ход стола, выставляют в зависимости от длины гнезда. Ход гильзы со шпинделем ограничивают упором, который устанавливают по высоте в зависимости от глубины отверстия или гнезда. Торцовые упоры, базирующие заготовку, настраивают в зависимости от условий работы.
Практикуют сверление отверстий по разметке, упорам и с применением шаблонов. При сверлении по предварительной разметке торцовые упоры не требуются. Пользуясь метками, деталь каждый раз ориентируют на столе относительно сверла. Если нужно просверлить по разметке несколько отверстий, расположенных на одинаковом расстоянии от кромки детали, используют направляющую линейку.
По упорам сверлят при обработке большой партии деталей с отверстиями одинакового диаметра. Упоры в виде пружинящих пластин закрепляют в пазах направляющей линейки. Расстояние между упорами делают равным расстоянию между отверстиями в детали. Деталь базируют торцом по очередному упору, при этом неиспользуемые упоры утапливаются деталью в паз линейки.
Шаблоны используют для сверления отверстий в щитовых деталях. Расположение отверстий в шаблоне соответствует расположению отверстий в готовой детали. Прижим располагают на стойке вблизи высверливаемого отверстия и закрепляют стопорным винтом.
На станке работает один рабочий. При включении подачи автоматически срабатывают зажимы, шпиндель подается на заготовку и производится сверление. Скорость подачи шпинделя устанавливают в зависимости от диаметра, глубины и расположения высверливаемого отверстия по отношению к волокнам древесины. В станках с механизированной подачей скорость регулируют дросселем.
Выборку паза производят так. Сначала без боковой подачи стола сверлят два отверстия по концам будущего паза. Затем промежуток между круглыми гнездами удаляют методом пазового фрезерования при боковой подаче стола. Глубокие пазы фрезеруют за два и более проходов.
Периодически проверяют параметры паза или диаметр отверстия, их положение относительно края детали. Отклонение отверстия от перпендикулярности базовой поверхности детали допускается не более 0,15 мм на длине 100 мм.
Одновременно контролируют качество обработанных поверхностей и при появлении мшистости меняют сверло на острое.
Горизонтальные сверлильно-пазовальные станки.
Горизонтальные сверлильно-пазовальные станки бывают двусторонние и с наклоняемым столом.
В сверлильно-пазовальных горизонтальных двусторонних станках от электродвигателя через ременную передачу осуществляется вращение двустороннего шпинделя, а также привод боковых колебаний шпинделя. На концах шпинделя установлены цанговые патроны с концевыми фрезами или сверлами. По бокам станины на кронштейнах расположены два рабочих стола. Столы вертикально перемещаются. Внутри каждого стола смонтирован пневмоцилиндр, выполняющий горизонтальную подачу стола.
Основными параметрами режима работы станка являются скорость осевой и боковой подачи, а также частота качаний шпинделя.
Для коротких пазов частота боковых качаний шпинделя – 300 циклов/мин, с увеличением длины паза ее уменьшают до 150 циклов/мин.
На станках используют в основном одно– и двухрезцовые концевые фрезы (при большой ширине гнезда – трехрезцовые). Ширина гнезда вследствие биения фрезы обычно больше диаметра фрезы на 0,1-0,2 мм.
Для установки фрез применяют цанговый патрон с набором сменных цанг, обеспечивающих зажим инструмента с диаметрами хвостовика 8, 10 и 12 мм.
Стол станка устанавливают по высоте в зависимости от заданного расстояния от гнезда до боковой поверхности детали. Расстояние между фрезой и поверхностью стола меняют маховичком. Для повышения точности настройки используют шаблон.
Настройка считается правильной, если при проворачивании шпинделя режущие кромки фрезы слегка касаются поверхности шаблона.
Ход стола регулируют в зависимости от глубины гнезда.
Амплитуду бокового качания шпинделя регулируют маховичком, смещая ползун относительно оси вращения шкива привода механизма качания. При сверлении отверстий ползун устанавливают в центральное положение – эксцентриситет равен нулю.
Пневматические прижимы по высоте укрепляют на столе так, чтобы между рабочей поверхностью прижима и деталью был зазор 2-4 мм.
Скорость рабочего хода стола и частоту качаний шпинделя устанавливают в зависимости от размеров вырабатываемого гнезда и твердости древесины. При малых диаметрах фрез и обработке древесины твердых пород на больших скоростях во избежание поломки инструмента не работают.
После настройки обрабатывают пробные детали.
Станок обслуживает один рабочий. Берет заготовку из штабеля и укладывает ее на стол, базируя по упору и направляющей линейке. Убедившись в правильном положении заготовки, включает подачу, при этом заготовка автоматически закрепляется и происходит фрезерование паза. В процессе работы станка станочник берет следующую заготовку и укладывает ее на второй стол.
Деталь контролируют калибром или измерительным инструментом. Детали должны удовлетворять следующим требованиям. Равномерность ширины гнезда должна соответствовать 11-13-му квалитетам. Отклонение от параллельности пласти гнезда к базовой поверхности детали допускается не более 0,15 мм на длине 100 мм. Шероховатость поверхности должна быть не более 200 мкм.
Многошпиндельные сверлильно-присадочные станки.
Для одновременного сверления нескольких отверстий в щитовой детали применяют горизонтально-вертикальные многошпиндельные сверлильно-присадочные станки.
Станок СГВП-1А предназначен для одновременного сверления отверстий в пласти и в кромках щитов. Станок представляет собой две стойки, соединенные между собой балками с прямоугольными направляющими и порталом. На направляющих установлены четыре вертикальных и два горизонтальных сверлильных агрегата, элементы базирования заготовки и конвейер. На портале установлены переставляемые прижимы. Каждый вертикальный агрегат можно переставлять по направляющим вдоль станины в соответствии с размерами щита. Горизонтальные агрегаты, кроме перемещения вдоль станины, можно регулировать и по высоте.
Для подачи заготовки в станок и удаления готового изделия служит конвейер из клиновых ремней.
Сверлильные агрегаты станка: шпиндельная насадка, траверса и суппорты установлены на направляющих станины. Шпиндельная насадка подается по круглым направляющим от пневмоцилиндров. Для точного параллельного перемещения насадки служит синхронизирующий вал.
Шпиндельная насадка состоит из корпуса, в котором размещены рабочие шпиндели и привод. От электродвигателя движение передается центральному шпинделю, от которого последовательно через зубчатые шестерни приводятся во вращение другие 20 шпинделей. Они вращаются в разные стороны, а расстояние между ними не регулируется, оно равно 32 мм.
Кроме основной насадки, к станку прилагаются дополнительные, которые имеют по пять шпинделей. Дополнительные насадки устанавливаются на корпус основной, а привод шпинделей осуществляется от одного из шпинделей основной насадки.
Основной регулируемый параметр сверления – величина осевой подачи, которую определяют по допустимой подаче на резец. Для чистового сверления облицованных щитов из древесностружечных плит подача на резец должна быть не более 0,15-0,5 мм, а при более низком требовании к качеству обработки – не более 0,5-0,8 мм.
В сверлильных присадочных станках используют стандартные цилиндрические сверла и специальные сверла с резьбовым хвостовиком. Стандартные сверла устанавливают с помощью кулачковых или специальных патронов.
Установка сверл на резьбе позволяет увеличить надежность их крепления и уменьшить расстояние между шпинделями, так как патронов в этом случае не надо. Сверла с левой резьбой ввинчивают в резьбовое отверстие шпинделя, вращающегося по часовой стрелке, а сверла с правой резьбовой – в шпиндели с вращением по часовой стрелке.
Количество сверл определяется числом отверстий, которые необходимо высверлить, сверла устанавливают только в те шпиндели, расположение которых соответствует расположению отверстий в детали.
После установки сверл настраивают горизонтальные и вертикальные сверлильные суппорты, а также базирующий механизм в зависимости от размеров щита. Регулируют положение направляющих линеек и базирующих упоров так, чтобы обеспечивалось нужное расстояние отверстий от базовых кромок щита. Величину перемещения отсчитывают по шкалам на направляющих.
Если сверла настраивают с помощью шаблона, контролируют, чтобы его базовые поверхности касались всех боковых и задних выдвижных упоров. При базировании изделий по тем же упорам расстояния до отверстий от базовых кромок будут строго выдержаны независимо от колебаний размеров изделия. Шпиндельные насадки устанавливают, перемещая их по направляющим так, чтобы сверла совпадали с отверстиями в шаблоне.
При сверлении глухих отверстий используют сверла длиной не более 80 мм, глубину сверления регулируют гайкой, навинчиваемой на втулку механизма подачи насадки.
Скорость подачи шпиндельных насадок выбирают в зависимости от глубины сверления и твердости материала щита и регулируют в пределах 0,2-1,5 м/мин.
Правильность наладки станка проверяют обработкой пробной детали.
Порядок работы на станках следующий. Станочник укладывает на конвейер заготовку и прижимает ее к боковой упорной линейке. Нажимая на педаль, включает подачу конвейера и заготовка подается в рабочую зону станка. Здесь она фиксируется двумя задними упорами, двумя досылающими пневмоцилиндрами для поджатия щита к задним упорам, и двумя досылающими цилиндрами для прижима щита к левой базовой линейке. По команде шпиндельные насадки перемешаются на заготовку. После сверления упоры поднимаются, щит выносится из рабочей зоны станка, а шпиндельные насадки возвращаются в исходное положение.