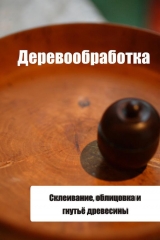
Текст книги "Склеивание, облицовка и гнутьё древесины"
Автор книги: Илья Мельников
Жанр:
Хобби и ремесла
сообщить о нарушении
Текущая страница: 1 (всего у книги 2 страниц) [доступный отрывок для чтения: 1 страниц]
Илья Мельников
Склеивание, облицовка и гнутье древесины
СКЛЕИВАНИЕ ДРЕВЕСИНЫ И ДРЕВЕСНЫХ МАТЕРИАЛОВ
Склеиванием называют соединение древесины и древесных материалов с помощью клеев и клеевых пленок. Это основной вид соединений на деревообрабатывающих производствах. Сущность склеивания состоит в следующем: нанесенный на поверхность древесины клей проникает в межклеточные и внутриклеточные пространства, застывает или затвердевает там и таким образом как бы сшивает склеиваемые поверхности. При этом между склеенными поверхностями образуется тонкий слой клея – от 0,08 до 0,15 мм.
Как при малой, так и большой толщине клеевого слоя прочность соединения ухудшается. При меньшей толщине склеивание будет "голодным", при большей – в клеевом слое в результате усадки клея при отверждении возникают внутренние напряжения.
Склеивание применяют для получения деталей больших размеров из брусков массивной древесины; для скрепления шиповых соединений; изготовления столярных плит и мебельных щитов; для облицовывания деталей и щитов.
Массивную древесину склеивают по длине, ширине и толщине. Торцы склеиваемых заготовок имеют скосы или шипы, а кромки могут быть обработаны на гладкую фугу, иметь шпунт или гребень, соединяться на вставную рейку.

Рис. Соединения брусков по длине:
а – впритык, б – в паз и гребень, в – на ус, г, д – клиновидное, е – в четверть, ж – на рейку

Рис. Способы соединения щитов:
а – на гладкую фугу, б – в четверть, в – на рейку, г – в паз и гребень, д – в паз и треугольный гребень, е – «ласточкин хвост»

Рис. Соединение досок по кромке и по длине:
а – по кромке на рейку, б – в четверть по кромке, в – в прямоугольный паз и гребень по кромке, г – в трапецпаз и гребень по кромке, д – на гладкую фугу (по кромке), е – по длине на ус, ж – по кромке в прямоугольный паз и гребень, з – на зубчатый шип
При склеивании древесных листовых материалов возможны различные варианты сочетаний материалов в склеиваемом блоке. Склеивают между собой одинаковые листовые материалы одной толщины; различные листовые материалы разной толщины (древесноволокнистая плита и шпон и т. д.); листовые и илитные материалы (столярная плита и шпон, древесностружечная плита и бумажнослоистый пластик и т. д,).
Требования к склеиваемым заготовкам и материалам. Перед склеиванием заготовки и материалы должны быть обработаны и подготовлены в соответствии с техническими требованиями и технологическими режимами. На склеиваемых поверхностях не должно быть масляных пятен, других загрязнений, стружки, пыли. Влажность древесины должна быть 8е2 %. Покоробленность заготовок не должна быть более 2 мм на 1 м длины. Подготовленные к склеиванию заготовки хранят в течение одной смены, так как при более длительном хранении они могут покоробиться, что снизит плотность прилегания склеиваемых поверхностей.
Шероховатость поверхностей, образующих наружный шов, должна быть не более 60 мкм, а поверхностей, образующих внутренний (невидимый) шов, – не более 200 мкм. Шиповые соединения деталей должны быть обработаны с соблюдением допусков и посадок, очищены от бахромы, стружки и пыли.
Способы склеивания. Практикуется два способа склеивания: холодный и горячий. Склеивание холодным способом (без нагрева склеиваемых материалов) требует длительной выдержки для схватывания клея и выравнивания влажности. Несмотря на хорошее качество склеивания, этот способ применяют редко, так как он не обеспечивает высокой производительности оборудования и требует больших производственных площадей.
При горячем способе процесс склеивания ускоряется за счет нагрева детали или клеевого шва. Теплота подводится различными способами. Кондуктивный (контактный) нагрев детали осуществляется так. Теплота подводится при нагревании склеиваемой поверхности детали контактными (электрическими или паровыми) нагревателями, имеющими постоянную температуру поверхности.

Рис. Схема подвода теплоты к клеевому шву:
а – контактный нагрев детали, б – склеивание с нагретой деталью, в – сквозной нагрев, г – прогрев в поле ТВЧ, 1 и 4 – склеиваемые детали, 2 – контактный нагреватель, 3 – клеевой шов, 5 – электрод, 6 – генератор ТВЧ
Другой способ – склеивание с нагретой деталью, т. е. с помощью аккумулированной теплоты. Нагревают одну деталь, а на другую наносят клеевой шов и подвергают детали прессованию.
Сквозной прогрев применяют при наклеивании тонкой облицовки. Теплота поступает от нагревателей во время прессования.
Подогрев в поле токов высокой частоты (ТВЧ) производят после сжатия склеиваемых поверхностей. Метод подогрева в поле ТВЧ позволяет нагревать непосредственно клеевой слой, не подвергая нагреву древесину. Для получения прочного клеевого шва необходимо настроить генератор ТВЧ на такую мощность, при которой минимальное время склеивания составляет 30-40 с.
Требования к условиям склеивания включают состояние температуры и влажности воздуха в производственном помещении, состояние склеиваемых материалов, выбор и подготовку клеев, способы нанесения клеев, способ склеивания и подвода теплоты, параметры прессования, рекомендации по выдержке склеенных деталей, применяемое оборудование, методы контроля.
Температуру и влажность воздуха в производственном помещении контролируют с целью обеспечения стабильности влажности склеиваемых материалов. Температура воздуха в помещении должна быть не ниже 18° С, а относительная влажность – не выше 65 %.
Способы нанесения клея зависят от вида склеиваемых материалов и объемов производства. На шиповые соединения клей наносят кистями, дисками или окунанием; на брусковые, плитные, листовые детали и щиты – кистями или вальцами.

Рис. Способы нанесения клея и клеящей пленки:
а – клея на одну склеиваемую поверхность, б – на обе поверхности, в – клеящей пленки, г – двустороннее механизированное, д – одностороннее механизированное, 1 и 3 – детали, 2 – клеевой слой, 4 – клеящая пленка, 5 – обрезиненные вальцы, 6 – ванна с клеем, 7 – дозирующие вальцы
При нанесении клея на одну склеиваемую поверхность клеевой слой наносится на нижнюю деталь. Клеящую пленку помещают между склеиваемыми поверхностями деталей.
Прессование осуществляется давлением на склеиваемые поверхности. Под давлением лучше соприкасаются поверхности, имеющие неровности, клей проникает в поры древесины, равномерно по всей поверхности подводится теплота.
Важное требование при прессовании – равномерность давления по всей склеиваемой поверхности. Величина давления зависит от свойств клея и склеиваемых материалов и приводится в технологической документации. Давление прессования при склеивании древесины обычно в пределах от 0,3 до 1,2 МПа. Сжатие склеиваемых поверхностей должно производиться до схватывания клея.
Прессование может быть ручным при облицовывании шпоном и сжатии шиповых соединений; с помощью простых приспособлений – клиновых и винтовых струбцин; механизированным в электромеханических, пневматических и гидравлических прессах и ваймах.
Прессы бывают много– и однопролетные. В многопролетных прессах трудно соблюдать режим облицовывания для первого и последнего щитов в комплекте загрузки, кроме того, плиты пресса прогревают щиты насквозь, поэтому после распрессовки нужна длительная выдержка щитов (до двух суток) для снятия внутренних напряжений. Эти недостатки отсутствуют у однопролетных прессов.
Выбор способа и оборудования для прессования зависит от вида и объема работ, свойств склеиваемых деталей и материалов.
Важная часть технологического процесса склеивания – выдержка деталей. Детали, поступающие на склеивание, должны пройти выдержку, для того чтобы их влажность и температура соответствовали принятым условиям склеивания. В процессе прессования выдержка под давлением необходима для схватывания клея или его полного отверждения. Продолжительность выдержки зависит от вида клея, температуры прессования, породы склеиваемой древесины.
После прессования склеенные детали выдерживают для достижения клеевым слоем достаточной прочности, охлаждения, равномерного распределения влаги в материале и стабилизации его формы. Продолжительность послепрессовой выдержки зависит от параметров прессования и температурно-влажностных условий в помещении. Методы и средства их оценки разрабатываются для каждого режима склеивания отдельно.
Основные дефекты склеивания – просачивание клея, клеевые потеки, непроклеивание, покоробленность. Они возникают при неправильной подготовке заготовок к склеиванию и нарушении режимов склеивания.
СТОЛЯРНЫЕ КЛЕИ И ИХ ПРИГОТОВЛЕНИЕ
Различают клеи животного происхождения (костный, мездровый, казеиновый, альбуминовый) и синтетические, клеящие пленки и нити.
На деревообрабатывающих предприятиях наиболее широко применяются клеи на основе мочевиноформальдегидных (карбамидных) смол, жидкие или в виде порошка, отличающиеся друг от друга содержанием свободного формальдегида, временем отверждения и жизнеспособностью. Применение конкретной марки смолы определяется условиями использования клея. (Условия приводятся в технологической документации на изготовление изделий.)
При склеивании горячим способом наибольшее применение получили карбамидные смолы, имеющие малое содержание свободного формальдегида.
Особое положение занимают смолы быстрого отверждения, применение которых позволяет реализовывать высокопроизводительные технологические процессы склеивания древесины и древесных материалов.
Клеящую пленку применяют для ребросклеивания и ремонта шпона. Она получается путем пропитки на пропиточной сушильной установке специальной бумаги смолой и последующей сушки. Ее изготовляют в виде листов различного формата.
Клеевые нити применяют при ребросклеивании шпона.
Приготовляют рабочие pacтворы клеев в специально отведенных помещениях в определенных количествах в зависимости от жизнеспособности клея.
Приготовление рабочего раствора костного и мездрового (глютиновых) клеев.
Набухшие в воде плитки клея заливают водой и варят в клееварке или котле с двойными стенками при температуре 70-80°С. Варить клей при большей температуре не рекомендуется, так как он теряет клеящие свойства. Раствор считается пригодным для использования, если при помешивании в нем не видно сгустков. В случае застывания клей можно подогреть.
Для приготовления раствора казеинового клея в посуду наливают необходимое количество воды комнатной температуры и, перевешивая, добавляют порошок клея до образования однородной сметанообразной массы. Жизнеспособность раствора казеинового клея 4-6 ч.
Синтетические клеи, основой которых являются смолы, приготовляют с использованием растворителей, наполнителей, отвердителей и других добавок. Растворителями служат вода, ацетон, спирты. В качестве наполнителей, увеличивающих вязкость клея, используют древесную муку, гипс, каолин и др. Отвердителями являются хлористый аммоний (при горячем способе склеивания), 10 %-ный раствор щавелевой кислоты или 40 %-ный раствор молочной кислоты (при холодном способе склеивания). Вязкость смоляных клеев должна быть в пределах 60-200 с по ВЗ-4. Жизнеспособность синтетических клеев небольшая – 2-6 ч и зависит от температуры клеевого раствора.
Расход клеевого раствора при склеивании древесины в зависимости от конкретных условий колеблется в пределах от 150 до 350 г/м2.
ПРОИЗВОДСТВО КЛЕЕНЫХ ЗАГОТОВОК
Клееные заготовки и детали могут быть брусковые, щитовые, криволинейные и специальные. Соединяют отдельные элементы между собой по длине, ширине и толщине. Использование клееных заготовок позволяет увеличить выход основных заготовок в деревообрабатывающем производстве на 8-12% от объема расходуемых пиломатериалов.
Склеивание или сращивание заготовок по длине производится в основном на зубчатый шип. Есть механизированные и полуавтоматические поточные линии, на которых производится нарезание зубчатых шипов, склеивание и раскрой склеенной ленты на заготовки. Например, на линии ОК502 можно склеивать отрезки длиной 250-1200, шириной 50-150 и толщиной 40-35 мм. Длина получаемых заготовок 560-2300 мм.
Линия состоит из одностороннего шипорезного станка, клеенамазываюшей головки, гусеничного пресса и торцовочного станка проходного типа, выполненного по схеме суппорта сопровождения. В зависимости от сечения склеиваемых брусков скорость подачи гусеничного пресса (и производительность линии) может изменяться бесступенчато в пределах 5-10 м/мин.
Полуавтоматическая линия ДВ202 для склеивания брусковых заготовок по длине на зубчатый шип работает следующим образом. Обработанные по сечению заготовки длиной 250-1500 мм подаются на шипорезный станок, где нарезаются зубчатые шипы с одного торца заготовки. Ленточный конвейер подает заготовки ко второму шипорезному станку для нарезки шипов на противоположном торце и на нем же с помощью профильного вальца клеенамазывающей головки наносится клей. Далее конвейером заготовки подаются к гусеничному прессу для склеивания. После пресса непрерывная лента склеенных заготовок подается в торповочный станок-автомат. Отпиленные нужной длины заготовки через перекладчик укладываются в штабель на напольный роликовый конвейер, где выдерживаются для полимеризации клея.
При скорости подачи гусениц пресса 18 м/мин и коэффициенте использования линии 0.7 сменная производительность линии составляет до 6 тыс. м заготовок.
Склеивают заготовки по ширине и толщине на гладкую фугу и на шиповое соединение. Для этого применяют струбцины, сжимы, клеильно-конвейерные прессы, щитосборочные станки и поточные линии. Отрезки, подлежащие склеиванию, должны быть строганными или калиброванными, влажность древесины не должна превышать 12 %.
ОБЛИЦОВЫВАНИЕ ДЕТАЛЕЙ ИЗ ДРЕВЕСИНЫ
Облицовывание применяется для улучшения внешнего вида деталей и изделий, повышения их прочностных свойств и основано на склеивании материалов. При облицовывании поверхности детали оклеивают листовыми или пленочными материалами.
Процесс облицовывания состоит из следующих операций: подготовки основы, подготовки облицовочных материалов, наклеивания облицовки на основу. Основой называется облицовываемая деталь, облицовкой – покрытие из листового или пленочного материала, которое приклеивают на основу.
В зависимости от формы основы различают облицовывание плоских прямолинейных и криволинейных деталей или заготовок, в зависимости от вида поверхности основы выделяют облицовывание пластей и кромок.
По виду облицовочных материалов различают облицовывание натуральным шпоном и синтетическими материалами – синтетическим шпоном, полимерными пленками, декоративным бумажно-слоистым пластиком и т. п.
Подготовительные работы. Поверхность основы должна иметь равномерную структуру без ослабленных или излишне твердых мест, впадин, клеевых, смоляных или жировых пятен. Гниль, кармашки, червоточину, сучки удаляют и заделывают вставками. Пятна клея, смолы или жира удаляют. Дефекты механической обработки (заколы, задиры, вырывы, выбоины и т. п.) заделывают местным и сплошным шпатлеванием. Шпатлевка после высыхания должна иметь незначительную усадку, а ее твердость должна быть близкой к твердости материала основы.
При облицовывании основы натуральным шпоном шероховатость поверхности основы должна быть не более 60 мкм. При облицовывании пленками поверхность основы подвергают порозаполнению. В этом случае шероховатость должна быть не более 60 мкм при облицовывании непрозрачной пленкой и не более 16 мкм при облицовывании прозрачной пленкой.
Поверхности, соответствующие этим требованиям, получают при обработке основы на рейсмусовых станках – 100 мкм, на шлифовальных станках – 60 мкм, на шлифовальных широколенточных станках – 16 мкм. Предельные отклонения по толщине основы должны быть не более е 0,2 мм.
Подготовка облицовок из натурального шпона включает в себя подбор и разметку пачек шпона, раскрой их на делянки, фугование кромок делянок, формирование облицовок. Для облицовки применяют строганый и лущеный шпон. Влажность шпона должна быть 8(2 %.
Различают правую и левую стороны шпона. Правая сторона отличается более гладкой и плотной поверхностью, левая более шероховатая, с мелкими разрывами. Лицевой стороной облицовки является правая сторона шпона.
Шпон подбирают по породе древесины, качеству, цвету текстуре, размерам листа. Для обеспечения максимального использования шпона верхний лист в пачке размечают по шаблонам цветными мелками или карандашами. Раскраивают пачки шпона на делянки по разметке сначала поперек, затем вдоль направления волокон. При раскрое листы шпона в пачке не должны смещаться один относительно другого. Не допускается перекос реза. Раскраивают шпон на круглопильных и ленточнопильных станках или гильотинных ножницах.

Рис. Схема раскроя пачки шпона:
а – на круглопильном станке, б – на гильотинных ножницах, 1 – пачка шпона, 2 – каретка, 3 – зажим, 4 – стол станка, 5 – пила, 6 – прижимная балка, 7 – нижний нож, 8 – верхний нож

Рис. Виды набора шпона:
а – в елочку, б – в крейцфугу (крестом), в – конверт, г – в шашку, д – в полуелку, е – во фриз
При раскрое на круглопильных станках пачку шпона закрепляют на каретке, каретка перемещается по пазам стола до пилы. После раскроя шпона на круглопильных и ленточнопильных станках продольные кромки не имеют требуемой шероховатости и их необходимо фуговать. Фугование исключается при раскрое пачек шпона на гильотинных ножницах с прижимной балкой. Пачку шпона укладывают на столе, зажимают балкой и обрезают.
Кромки делянок фугуют на фрезерных, фуговальных и кромкофуговальных станках.
Кромки делянок должны иметь шероховатость не более 32 мкм. Не допускаются сколы, отщепы и вырывы. Отклонение от прямолинейности кромок должно быть не более 0,33 мм на 1 м длины, а отклонение от перпендикулярности кромок и пластей – не более 0,2 мм.
Обработанные делянки должны быть уложены в пачки в той последовательности, в которой они были уложены после строгания.
Для получения требуемого рисунка на лицевой поверхности облицовываемого изделия делянки шпона собирают в наборы с соблюдением текстурного рисунка древесины и в соответствии с проектом изделия.
Из простых наборов наиболее распространены набор в рост, поперечный и косой. Поперечный и косой наборы позволяют использовать короткие отрезки шпона. Среди фигурных наборов наиболее удобны наборы в "елочку", крестом и шашечный.
Для получения готовой облицовки делянки в наборах соединяют между собой клеевой лентой, клеевой нитью или клеевым швом. Места соединения кромок должны быть плотными, без расхождений и нахлесток. На каждой пачке должен быть ярлык с указанием породы древесины, размера, даты укладки, влажности и даты ее определения.
Облицовывание. Облицовывание прямолинейных и криволинейных поверхностей деталей, пластей и кромок щитов в массовом производстве производят при неподвижном пакете в прессах различных типов.
При облицовывании холодным способом в однопролетных прессах между плитами помещают блок пакетов и через плиты осуществляют давление. Для ускорения оборота пресса пакеты формируют с дополнительными подкладными щитами, поверх которых укладывают ряд балок. Положение балок фиксируется стяжками и пакет в зажатом состоянии вынимается из пресса. Выдержка пакета производится вне пресса.
В однопролетный горячий пресс пакет подается в пространство между плитами конвейером с термостойкой лентой. В таких прессах облицовывание производится с коротким циклом времени. На базе однопролетного горячего пресса работают поточные линии, предназначенные для облицовывания пластей мебельных щитов. В состав линии входят: питатель, клеенаносящий станок, пресс и укладчик. Линию обслуживают оператор и двое рабочих.

Рис. Схемы облицовывания плоских прямолинейных заготовок:
а – однопролетный холодный пресс, б – блок пакетов, в – однопролетный горячий пресс, г – многопролетный горячий пресс, д – пресс с эластичным элементом, е – вайма для облицовывания кромок, 1 – плита пресса, 2 – пакет, 3 – балка, 4 – подкладной щит, 5 – стяжка, 7 – конвейер, 8 – камера, 9 – полость, 10 – щит, 11 – металлическая лента

Рис. Схемы облицовывания криволинейных заготовок:
а – однопролетный пресс, б – многопролетный горячий пресс, в – пресс с эластичным элементом, г – вакуумно-автоклавная установка, д – вайма с гибкой лентой, е – вайма с плитами-шаблонами, 1 – плита пресса, 2 – пакет заготовок, 3 – пресс-форма, 4 – плита-шаблон, 5 – эластичный элемент, 6 – камера, 7 – полость, 8 – шаблон, 9 – резиновый мешок, 10 – автоклав, 11 и 14 – металлическая лента, 12 – деталь, 13 – щит
Многопролетные горячие прессы увеличивают объемы и сокращают время облицовывания. Они оборудованы горячими плитами, между которыми помещаются пакеты с прокладками. Для загрузки таких прессов применяют подъемные столы, с которых пакеты загружаются в пролеты пресса, загрузочные и разгрузочные этажерки, с помощью которых одновременно загружаются и выгружаются пакеты во всех пролетах пресса.
Прессы с эластичным элементом применяют при облицовывании под небольшим давлением. В таком прессе на плите размещают пакет, поверхность которого обжимается эластичным полотном типа термостойкой резины. В полость над пакетом подается воздух (или пар), который создает давление и обогревает поверхности облицовываемого щита.
Для облицовывания прямолинейных кромок применяют ваймы. Узкие прижимные плиты создают давление на кромки щита, на которые нанесен клей и наложена облицовка. Нагреваются кромки металлической лентой, расположенной между прижимной плитой и облицовкой.
Облицовывание криволинейных заготовок производят с помощью пресс-форм.
Для облицовывания криволинейных заготовок при небольших давлениях применяют прессы с эластичным элементом. На плите под пакет кладут постоянный шаблон. Эластичный элемент прижимает пакет облицовок к шаблону, в полость подается под давлением воздух или пар.
Кромки с криволинейной поверхностью облицовывают в ваймах с гибкой металлической лентой, которую можно нагревать для ускорения приклеивания облицовки. Применяют также ваймы с жесткими плитами-шаблонами, оборудованными нагреваемыми металлическими лентами для ускорения облицовывания.
Более эффективно облицовывание поверхностей щитов в валковых прессах с непрерывным движением облицовываемых щитов. При облицовывании в одновалковом прессе облицовка к основе прижимается парой холодных или горячих валков. После пакеты укладывают блоками и выдерживают в однопролетных прессах или в зажатом состоянии до полного отверждения клея. Одновалковые прессы обычно применяют для облицовывания рулонными пленками или декоративным бумажно-слоистым пластиком.
Для облицовывания кромок с применением быстроотверждающихся клеев-расплавов используют многовалковые прессы. Валково-ленточный пресс, кроме валков, имеет металлическую ленту и ролики. Горячая лента при контакте с облицовкой щитовой детали прогревает клеевой слой, а ролики обеспечивают дополнительный прижим на время отверждения клея.

Рис. Схема облицовывания в валковых прессах:
а – одновалковом, б – многовалковом, в – валково-ленточном, 1 – щитовая деталь, 2 – валок, 3 – металлическая лента, 4 – ролик
Валковые прессы находят широкое применение при облицовывании щитовых деталей дверей и мебели методом каширования. Под кашированием понимается процесс облицовывания пластей деталей рулонными материалами путем накатывания их на поверхность основы в валковых прессах.
Дефекты облицовывания. Основными дефектами при облицовывании щитов шпоном являются: местное отставание шпона, просачивание клея, трещины в шпоне, расхождение фуг – кромок делянок, коробление, неровности на облицовке.
Причины местного отставания шпона в недостаточном количестве клея, загрязнении основы, применении горячих прокладок при формировании пакетов, разнотолщинности основы, недостаточного давления прессования.
Дефект легко обнаруживается при простукивании облицованной поверхности. Исключить его можно только при строгом соблюдении параметров технологического процесса облицовывания.
Клей просачивается по целому ряду причин: тонкий шпон, жидкий клей, избыток клея, превышение давления прессования, низкая температура горячего пресса. И этот дефект объясняется недостаточно строгим соблюдением технологии приготовления клея и режима облицовывания.
Трещины в шпоне появляются при использовании шпона с повышенной влажностью.
Расхождение фуг происходит из-за плохого стягивания делянок шпона при формировании наборов облицовок. Предупреждается появление этого дефекта постоянным контролем за качеством стягивания.
Коробление обнаруживают по зазору между облицованной поверхностью и приложенной к ней ребром линейкой. Причинами коробления являются одностороннее облицовывание, несимметричность облицовок, неравномерность остывания при выдержке, различная температура смежных плит пресса. Для предупреждения этого дефекта облицовывают обе пласти щита, обеспечивают симметричность облицовок, контролируют режимы прессования и выдержки щитов.
Неровности на облицовке возникают из-за плохой подготовки основы и применения при прессовании некачественных прокладок.