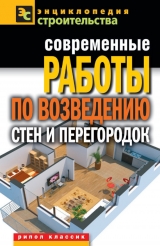
Текст книги "Современные работы по возведению стен и перегородок"
Автор книги: Галина Серикова
Жанры:
Хобби и ремесла
,сообщить о нарушении
Текущая страница: 2 (всего у книги 11 страниц) [доступный отрывок для чтения: 5 страниц]
Как правило, поставляется лес длиной 6 м, при этом максимальная длина 12,2 м (это зависит от габаритов вагона).
Сосна, заготовленная на севере Кировской области, считается северной. Древесина ее более плотная (примерно 1 т/м 3), чем у деревьев средней полосы, и цена более высокая. Но самой дорогой является ангарская сосна, которая имеет ряд отличительных признаков: она еще более плотная (тонет в воде), с темной сердцевиной и тонкими годовыми кольцами.
Второе место после сосны занимает ель, древесина которой безъядровая, мягкая, приятного белого цвета с золотистым оттенком, который она не утрачивает в течение длительного времени. Обилие твердых сучков делает обработку ели более трудной.
К хвойным породам принадлежит и лиственница, плотность древесины которой превышает этот показатель у сосны на 30 %. Значит, дома из нее могут стоять даже не десятки лет, а века! Благодаря наличию смолы лиственница не поражается вредными микроорганизмами и насекомыми, поэтому нет необходимости обрабатывать материал антисептиками. Тем не менее ее редко используют в деревянном строительстве, поскольку лиственница трудна в обработке (ее плотность 1,15 т/м 3), сохнет не менее 5–7 лет и подвержена трещинообразованию.
Дубовые стены – это всегда надежно, добротно и красиво. Дуб обладает прочной и очень твердой (поэтому обработка материала сопряжена с определенными трудностями), но склонной к растрескиванию древесиной.
Осина дает прекрасный материал, который по устойчивости сродни дубу. Она однородна, не скалывается, не сминается, не склонна к трещинообразованию и короблению. Есть сведения, согласно которым осину для стен заготавливали так: на коре прорубали несколько канавок, благодаря которым древесина не прела и при этом сохраняла необходимую влажность.
Таким образом, для строительства можно применять практически любую древесину, но при этом всетаки традиционно для бани более всего подойдут липа или осина, а для дома – сосна, ель, лиственница, кедр, пихта. Профессионалы рекомендуют несколько нижних венцов выполнять из твердой древесины, что значительно продлит срок службы постройки.
К сказанному о древесине и строительных материалах, из нее изготовленных, остается только добавить, что, какой бы материал вы ни избрали для стен своего дома, у каждого есть положительные свойства и недостатки. Позволим себе только совет: приобретайте тот материал, в котором цена и качество оптимально сочетаются.
Стены строятся не только из древесины, но и из так называемых штучных материалов, номенклатура которых огромна, поскольку они различаются целым рядом признаков, по которым их можно классифицировать:
1) по размеру:
а) кирпич;
б) камни (блоки);
2) по составу и способу изготовления:
а) керамические кирпичи и блоки;
б) силикатные кирпичи и блоки;
в) бетонные блоки;
3) по наличию пустот:
а) полнотелые;
б) пустотелые;
4) по назначению:
а) рядовые;
б) лицевые;
в) специальные (дорожный, огнеупорный).
Кирпич – традиционный искусственный материал для индивидуального строительства, который отличается прочностью и долговечностью (при наличии надежного фундамента кирпичное здание может стоять многие десятилетия).
В соответствии с составом и способом производства кирпич бывает керамический и силикатный. Технологически керамический кирпич получают посредством обжига глины, в которую введены соответствующие добавки. Данный материал пригоден не только для кладки стен и перегородок – из него возводят фундамент, применяют в печной кладке.
Размер и форма кирпича установлены ГОСТом. Согласно ему одинарный полнотелый кирпич («кирпич глиняный обыкновенный») представляет собой прямоугольный брусок длиной 250 мм, шириной 120 мм и высотой 65 мм. Такие параметры выбраны не случайно: они дают возможность осуществлять кладку, чередуя положение кирпичей по отношению к ее оси.
Каждая грань кирпича имеет определенные названия: самая маленькая – тычок, самая большая – постель, между ними (по величине) – ложок (рис. 3).

Рис. 3. Глиняный обыкновенный кирпич: 1 – постель; 2 – тычок; 3 – ложок
Помимо кирпича стандартного размера, производятся полуторный и двойной. Размеры первого: 250 x 120 x 103 мм, второго: 250 x 120 x 138 мм, причем двойной кирпич имеет другое название – «камень керамический». Благодаря такой величине процесс кладки значительно ускоряется.
Кроме того, что кирпич бывает полнотелым, производятся также пустотелый и поризованный (рис. 4). Наличие пустот снижает теплопроводность кирпича и его вес, что не только экономит материал, но и облегчает работу каменщика. Если увеличить пористость кирпича, то возрастут его теплоизоляционные качества, а также звукопоглощение.



Рис. 4. Кирпич: а – полнотелый; б – пустотелый; в – поризованный
К полнотелым относятся кирпич, не имеющий пустот, и такой материал, в котором объем пустот не превышает 13 % объема кирпича.
Полнотелым бывает исключительно одинарный кирпич, иногда – утолщенный, поскольку вес кирпича не должен превышать 4,3 кг. (Вес полнотелого красного кирпича (250 x 120 x 65 мм) составляет 3,5–3,8 кг, следовательно, 1 м 3, который содержит 480 кирпичей, весит 1700 кг.)
Кирпич и камни считаются пустотелыми при объеме пустот более 13 %, как правило, они составляют 25–45 %. Форма и размер пустот бывают различными, при этом материал должен соответствовать определенным параметрам, в частности при вертикально расположенных пустотах толщина наружных стенок должна быть не менее 12 мм; ширина щелевых пустот не должна превышать 16 мм; диаметр или сторона круглых или квадратных пустот – не более 20 мм.
По способу изготовления материал представлен двумя группами: в одной кирпич пластического формования, в другой – полусухого прессования.
В порядке информирования
При пластическом формовании исходную массу, в которой содержится примерно 20 % влаги, выдавливают на ленточных прессах (экструдерах). Первоначально кирпич выходит в виде непрерывного бруска, который разрезается на части по плоскости постели. Потом заготовки (кирпич-сырец) проходят стадии сушки и обжига. Поскольку при этом влага испаряется, масса кирпича уменьшается на 5–10 %. Так получают полнотелый кирпич. При производстве пустотелого кирпича все стадии производства сохраняются, а пустоты создают керны, которые установлены в выходной части головки пресса. Формованием пустотелого кирпича решается сразу несколько задач: во-первых, значительно улучшаются эксплуатационные качества изделия (уменьшается масса кирпича, снижается его теплопроводность, облагораживается внешний вид); во-вторых, позитивно изменяется технологичность процесса, поскольку при наличии пустот кирпич быстрее сохнет, следовательно, экономится топливо; снимается проблема внутреннего напряжения, которое возникает в материале при сушке; прогрев изделий существенно ускоряется, причем равномерно по всему объему изделия, в результате кирпич приобретает геометрическую точность, устраняется риск трещинообразования в нем, что в совокупности обеспечивает высокое качество конечной продукции. Но следует признать, что формование пустотелого кирпича-сырца сопряжено с большими трудностями, чем изготовление полнотелого изделия, поскольку к сырьевой массе предъявляются повышенные требования.
При полусухом прессовании кирпич поштучно формуется из сыпучей глиняной массы, влажность которой составляет, как минимум, 10 %. Чтобы уменьшить массу готового изделия, такой кирпич выпускается только пустотелым. Благодаря особенностям производства (небольшая влажность исходного состава, поштучное формование) кирпич отличается более правильной формой и размерами. Однако вследствие особого строения черепка морозостойкость у такого материала ниже, чем у кирпича пластического формования.
Различить кирпич, изготовленный разными способами, можно по такому признаку: у изделий полусухого прессования (рис. 5) пустоты имеют коническую форму и, как правило, не бывают сквозными.

Рис. 5. Кирпич полусухого прессования
Керамический камень имеет то же предназначение, что и кирпич, он при кладке заменяет два кирпича с учетом растворного шва между ними. В соответствии с размерами керамический камень подразделяется на:
1) обычный (250 x 120 x 138 мм);
2) укрупненный (250 x 250 x 138 мм);
3) модульный (288 x 138 x 138 мм);
4) с горизонтальными пустотами (250 x 250 x 120 мм).
Если кирпич может быть и пусто-, и полнотелым, то камень – только пустотелым. Этот материал (рис. 6) имеет разное предназначение и может использоваться для кладки:
1) наружных и внутренних несущих стен и стен каркасных построек. Из них можно класть и перегородки. Но керамические камни не допускаются для кладки фундамента, цоколя ниже слоя гидроизоляции, а также стен в помещениях повышенной влажности;
2) внутренних несущих стен и перегородок. Допускается их применение в каркасном строительстве. Ограничения те же.


Рис. 6. Блоки (камни) керамические пустотелые (размеры указаны в миллиметрах): а, б – для несущих стен; в, г, д, е – для каркасных стен; ж, з – для внутренних перегородок
Силикатный кирпич примерно на 90 % состоит из песка. Оставшиеся 10 % приходятся на известь и небольшое количество определенных добавок. Он изготавливается в автоклавах в условиях повышенного давления и при температуре 170–180 °C. По прочности не отличается от керамического, но по сравнению с ним силикатный кирпич более легкий, не столь морозо– и водостойкий, совершенно нежаростойкий, характеризуется большей теплопроводностью, поэтому и сфера его применения гораздо уже. Он применяется для кладки стен и перегородок и не используется в таких ответственных конструкциях, как фундамент, цоколь (допускается только в сухих грунтах), печь и др. Но при сухом режиме эксплуатации силикатный кирпич такой же долговечный, как и керамический.
Силикатные камни производятся только пустотелыми, имеют вертикальные пустоты (диаметр 30–32 мм), с верхней стороны они замкнутые. Применение этого материала такое же, как и у силикатного кирпича.
Бетонные камни являются распространенным строительным материалом, применяются для кладки стен, фундаментов и перегородок и в зависимости от размера представлены следующими разновидностями:
1) целым (390 x 190 x 188 мм);
2) продольными половинами (390 x 90 x 188 мм);
3) перегородчатыми (590 x 90 x 188 мм).
Подробная характеристика блоков (камней) из бетона и растворов представлена ниже.
Из рядового кирпича (блоков) строятся несущие стены. Для него характерны высокие прочностные качества и при этом недостаточная стойкость к воздействию как природно-климатических факторов, так и агрессивной окружающей среды, вследствие чего стены из этих материалов нуждаются в защитно-декоративном покрытии. Их либо оштукатуривают, либо облицовывают различными материалами.
По-другому лицевой кирпич (блоки) называют облицовочным, фасадным, отделочным. Он отличается правильной формой, наличием четких граней и однородностью окраски (за счет вводимых пигментов материалу можно придавать практически любой оттенок). Кроме того, облицовочный кирпич и блоки различаются фактурой: их поверхность бывает гладкой, волнистой, шероховатой, имитирующей натуральный или колотый камень и пр.


Рис. 7. Лицевой кирпич: а – гладкий щелевой; б – рифленый пустотелый
Лицевой кирпич (рис. 7) и камни используются для наружных работ, потому что эти материалы стойки к природно-климатическим факторам (морозам, осадкам). Они пригодны и для кладки, и для облицовки стен (наружных и внутренних). Лицевой кирпич обычно бывает пустотелым, благодаря чему качество черепка улучшается.
В настоящее время производится фасонный (фигурный, профильный) кирпич (рис. 8). Благодаря тому, что он имеет разную форму, цвет, размер и фактуру, реализуются различные архитектурные решения при устройстве дверных и оконных проемов, возведении арок, эркеров и др.
Специальные материалы (рис. 9) используются в тех случаях, когда предполагаются особые условия эксплуатации.
Например, шамотный кирпич предназначен для кладки печей, поскольку он рассчитан на высокие температуры (более 1000 °C).

Рис. 8. Фасонный кирпич


Рис. 9. Специальный кирпич: а – огнеупорный; б – клинкерный
В порядке информирования
Качество кирпича, который применяется в строительстве, подчиняется ГОСТу 7484-78 «Кирпич и камни керамические лицевые. Технические условия» и ГОСТу 530-95 «Кирпич и камни керамические. Технические условия». Качественный кирпич должен соответствовать:
1) заявленной марке по прочности, а также нормативу по водопоглощению (не менее 8 и 6 % для полно– и пустотелого соответственно);
2) марке по морозостойкости по пористости;
3) экологической норме, согласно которой удельная эффективная активность естественных радионуклидов не должна быть более 370 Бк/кг;
4) стандартным размерам. Для рядового кирпича допустимые отклонения составляют ±5, ±4, ±3 мм по длине, ширине и высоте соответственно; для облицовочного – ±4, ±3, ±2–3 мм по тем же параметрам. Грани у кирпича должны быть плоскими, ребра прямолинейными (рядовой может иметь закругления вертикальных ребер радиусом до 15 мм). Средняя часть кирпича должна быть немного темнее, чем остальная масса. Звук при ударе должен быть гулким.
Кирпич не должен содержать каких-либо включений, в частности извести (впитывая влагу, она разбухает, разрушая этим кирпич) и фрагментов камня. Стандартами предусматриваются дефекты:
1) допустимые: а) у рядового кирпича могут быть отбитые углы глубиной 10–15 мм и(или) дефекты ребер глубиной не более 10 мм, длиной 10–15 мм, но не более двух изъянов на один брусок; трещины глубиной не более 30 мм, но не более одного изъяна на ложковой и тычковой гранях; отколы поверхности глубиной 3–10 мм, но не более трех изъянов на брусок; б) это же относится и к облицовочному кирпичу, за исключением его лицевой поверхности, на которой не должно быть никаких изъянов (сколов, включений, пятен и пр.), заметных с расстояния 10 м при дневном свете;
2) недопустимые, возникающие при нарушении технологии производства: а) недожог. У кирпича цвет изменяется на горчичный, звук становится глухим, его морозо– и водостойкость снижены; б) пережог. На кирпиче образуются подпалины черного цвета, изменяется форма, его плотность и теплопроводность повышены. Если кирпич сохраняет форму, то специалисты считают, что его прочность возрастает и этот материал может применяться для кладки фундамента и там, где повышенная теплопроводность не играет решающей роли; в) высолы. Как правило, обнаруживаются не на отдельных брусках, а на стенах, которые покрываются пятнами и разводами белого цвета. Существует несколько рекомендаций, следование которым помогает избежать появления такого дефекта:
• использовать для кладки густой раствор;
• следить за тем, чтобы раствор не загрязнял лицевую сторону кирпича;
• вести работы в сухую погоду;
• обрабатывать стены специальными составами;
• при перерывах в кладке (независимо от того, на какое время) накрывать ее водонепроницаемой пленкой;
• стремиться к тому, чтобы готовые стены были бы сразу же подведены под крышу.
Помимо чисто внешних характеристик, кирпич имеет целый ряд технических, в частности прочность, морозостойкость и водопоглощение.
Прочность – это «способность материала сопротивляться внутренним напряжениям и деформациям, не разрушаясь». Показателем прочности является марка, для которой введено буквенно-цифровое обозначение, например М100. Цифра указывает, какую нагрузку, приходящуюся на 1 см 2, сможет выдержать кирпич, следовательно, в нашем примере такая нагрузка составляет 100 кг. Кирпич производится под марками от 75 до 300 (в соответствии со стандартом всего восемь марок). Для индивидуального строительства оптимальным считается материал марки М100.
Морозостойкость (Мрз) – важный показатель, который представляет собой способность кирпича противостоять периодически повторяющимся замораживанию (–18–2 °C) и оттаиванию (2–20 °C) при наличии в его порах воды. Увлажнение и замораживание, которые в наших природно-климатических условиях регулярно сменяют друг друга, в совокупности являются основным деструктивным фактором, от которого зависит долговечность большинства строительных материалов, использующихся в средней полосе России.
Этот показатель измеряется в циклах. Стандартный цикл, в процессе которого тестируется кирпич, составляет 16 ч, при этом половину этого времени материал лежит в воде, а во время оставшихся 8 ч – в морозильной камере. Испытания продолжаются до момента, когда в материале начнутся структурные изменения, т. е. он изменит массу, прочность, появятся трещины, шелушение поверхности и пр. Морозостойкость кирпича также имеет буквенно-цифровое выражение. По этой характеристике выпускаются следующие марки: F15, F25, F35, F50.
Поскольку в нашей стране регионы имеют различные природно-климатические условия, то для строительства используется кирпич разной морозостойкости. Например, в средней полосе России данный показатель составляет 35 циклов. Чем более морозостойким является кирпич, тем выше его стоимость.
Кирпич, являясь пористым материалом, может впитывать влагу. Эта его способность измеряется в процентах, т. е. в соответствии с установленными нормами данный показатель варьируется в пределах 6–16 %. Для наружных стен рекомендуется кирпич с наиболее низким водопоглощением.
Основные характеристики керамического кирпича представлены в табл. 1.
В порядке информирования
Если вы решили строить дом из кирпича, то в первую очередь потребуется приобрести данный строительный материал и доставить его на участок. И очень важно сделать это грамотно. Поэтому мы хотим дать вам несколько советов по поводу покупки кирпича.
1. Прежде всего поинтересуйтесь, есть ли у продавца сертификат, и обязательно ознакомьтесь с ним.
2. Если вы начинаете строительство двух– или трехэтажного дома, то для стен подойдет кирпич М100–125, F35–50.
3. Рядовой и облицовочный кирпич должны быть одной и той же марки (по крайней мере соседней), поскольку от этого зависит, будут ли стены иметь одинаковую прочность.
4. Предпочтителен двойной кирпич, так как выгоден, ведь при его использовании возрастет скорость кладки и сэкономится кладочный раствор, а следовательно, и деньги.
5. Если предполагается отделывать дом, то все количество облицовочного кирпича, которое потребуется для работы, закупите сразу, поскольку отдельные партии могут заметно отличаться по цвету. Кстати, цвет на качество кирпича не оказывает никакого воздействия, поэтому вы можете выбрать себе любой.
6. Если вы приобретаете и отечественный, и импортный кирпич, то сравните их параметры, поскольку в разных странах различные стандарты.
Таблица 1
Технические характеристики керамического кирпича

Поскольку кирпич отличается хорошими эксплуатационными характеристиками, в настоящее время его часто используют в индивидуальном строительстве. Но, для того чтобы дом был теплым, кирпичные стены должны иметь достаточную толщину. Если же они тонкие, например в 1 или 1,5 кирпича, то их следует отделать эффективными теплоизоляционными материалами, в роли которых выступают система вентилируемого фасада или штукатурные системы. Выполнение такой технологии потребует как финансовых, так и трудовых затрат.
Но есть и другой выход – использовать облегченные керамические блоки и кирпич. Благодаря им не только уменьшается вес ограждающих конструкций, снижается нагрузка на фундамент, но и повышаются теплоизоляционные свойства стен. Строительная индустрия предлагает новые разработки, например сверхтеплый кирпич «Термолюкс» (250 x 120 x 88 мм ± 0,5 мм), характеризующийся следующими параметрами:
1) теплопроводность – 0,2 м*°C;
2) прочность – М100–125;
3) плотность – 900–1000 кг/м 3;
4) морозостойкость – F25.
По своим свойствам ограждающая конструкция из поризованных блоков напоминает деревянную, поскольку в помещении поддерживается оптимальный температурно-влажностный режим, не нарушается воздухообмен.
В индивидуальном строительстве очень широко используются бетонные блоки (камни). Бетон относится к композиционным материалам и является результатом формования и твердения бетонного раствора, в состав которого входят вяжущие вещества, заполнители, вода и специальные добавки. Отличительные особенности бетона – долговечность, огнестойкость. В жидком состоянии бетон бывает пластичным, что позволяет выполнять из него изделия, различные по форме, в частности стеновые блоки: полно– и пустотелые, рядовые и лицевые.

Рис. 10. Поризованный керамический блок
Для снижения плотности и теплопроводности камень формуется пустотелым. Конструктивно он напоминает термос: между его торцевыми стенками расположены воздушные прослойки, разделенные перегородками в виде лабиринта, что исключает возникновение мостиков холода.
Производятся крупноформатные (250 x 380 x 219 мм) поризованные керамические блоки (рис. 10) с такими техническими параметрами:
1) теплопроводность – 0,17 Вт/*°С;
2) прочность – М75;
3) плотность – 790 кг/м 3;
4) морозостойкость – F35.
Поризованные керамические блоки от обычных кирпичей и блоков отличаются тем, что исходное сырье, из которого они изготавливаются, имеет необычную структуру. Дело в том, что в глину вводятся органические и минеральные добавки, которые при тепловой обработке сгорают, оставляя в глине поры.
Благодаря пазам и гребням на боковых поверхностях крупноформатного материала, которые выполнены с высокой точностью, стены собираются легко, как конструктор, и при этом отпадает необходимость заполнять вертикальные швы раствором, что улучшает теплотехнические характеристики стены. Для повышения теплоизоляционного эффекта кладку можно вести на легком растворе. Но, чтобы он не попадал в пустоту блоков, их поверхность прикрывается пластиковой сеткой. Дверные и оконные проемы перекрываются керамобетонными перемычками, длина которых может достигать 800–1200 мм.
Стенам из поризованной керамики придаст эстетичность облицовка керамическим или силикатным кирпичом, с которым она хорошо сочетается.
Характеристики бетона (плотность, прочность и др.) в соответствии с условиями использования могут варьироваться. Поэтому стеновые бетонные блоки классифицируются следующим образом:
1) по предназначению.
Блоки производятся для фундамента, стен, перегородок, фасада, а также в виде теплоизоляционных вкладышей для стен;
2) по плотности.
По этому признаку блоки подразделяются на:
а) особо тяжелые (более 2500 кг/м 3);
б) тяжелые (2200–2500 кг/м 3);
в) облегченные (1800–2200 кг/м 3);
г) легкие (500–1800 кг/м 3);
д) особо легкие (не более 500 кг/м 3);
3) по весу. Блоки, использующиеся для ручной кладки, имеют вес до 32 кг, с применением техники укладываются блоки весом от 500 кг;
4) по строению, т. е. на полнотелые, пустотелые (объем пустот составляет, как минимум, 15 %), многослойные (в состав входят несущий, теплоизоляционный и облицовочный слои);
5) по применению. При кладке стен используются основные блоки, а также дополнительные, применяющиеся для перевязки, облицовки и отделки оконных и дверных проемов.
Для стен производятся блоки из тяжелых и легких бетонов, а еще из пенополистиролбетона. Тяжелые бетонные блоки представлены несколькими разновидностями. К ним, в частности, относятся цементно-песчаные блоки, изготавливающиеся из смеси цемента, песка и воды. Отличительной особенностью этого материала является высокая прочность. По этому параметру различаются марки М50, М75, М100. Для частного строительства рекомендуются блоки М100, которые производятся в двух разновидностях: в виде полно– и пустотелых блоков (в последних объем пустот составляет не более 30 % объема блока). Если первые используются преимущественно для возведения фундаментов, то вторые предпочтительны для стен, поскольку благодаря пустотам имеют повышенные тепло– и звукоизоляционные свойства. При наличии пустот появляется возможность усилить стеновую конструкцию за счет вертикального армирования, после осуществления которого пустоты замоноличиваются. Фактически в этом случае бетонные блоки можно рассматривать как несъемную опалубку.
При покупке данного материала обратите внимание на имеющиеся на поверхности специфические темные разводы (иногда это характеризуют как мраморность, шагрень). При отсутствии этого визуального признака у вас должны возникнуть сомнения относительно прочностных качеств приобретаемого материала. В блоках либо нарушено соотношение цемента и песка в пользу последнего, либо имеются технологические погрешности – недостаточные усилия при прессовании. Допустимыми дефектами для бетонных блоков являются отклонения от геометрических размеров, но не более 2 мм, и мелкие сколы, но не более 2–3 мм.
К тяжелым бетонным блокам относятся и шлакоблоки, название которых говорит о том, что в их состав, помимо цемента, песка и воды, входит шлак. По своим теплоизоляционным характеристикам такие блоки эффективнее полнотелого кирпича примерно в 1,5 раза и приблизительно во столько же раз дешевле. Стены, возведенные из шлакоблока, достаточно долговечны – не менее 50 лет при условии обеспечения оптимальной влагозащиты и устройства прочного фундамента.
В порядке информирования
Для изготовления шлакоблоков применяются топливные шлаки. В отличие от доменных шлаков (керамзита) они более доступны, но по прочности немного им уступают. Наилучшими считаются шлаки, образующиеся при сжигании антрацита. Шлаки бурых углей, содержащие много примесей, для целей строительства непригодны. Промежуточное положение занимают шлаки других каменных углей, которые чаще всего и применяются для производства шлакобетона. Чтобы получить качественный строительный материал, шлаки не должны включать в свой состав никаких примесей, в частности земли, глины, несгоревших фрагментов угля. Более того, прежде чем использовать шлаки, их необходимо не менее года выдержать под открытым небом в отвалах, обеспечив отведение дождевых, снеговых и паводковых вод. Благодаря такому методу шлак освобождается от необожженных глинистых частиц, вредных солей и пр.
Прочностные и теплоизоляционные свойства шлакобетона определяются его гранулометрическим составом – соотношением крупных (5–40 мм) и мелких (0,2–5 мм) фракций шлакового заполнителя. Если преобладают первые, то получается более легкий, но менее прочный материал, при превалировании вторых – более плотный и теплопроводный. Для наружных стен оптимальна пропорция мелкого и крупного шлака от 3: 7 до 4: 6. В шлакобетоне для внутренних стен доминирует мелкая фракция, а частицы более 10 мм вообще не включаются в состав исходного сырья. Самый мелкий шлак (примерно 25 % общего объема) заменяется песком.
В качестве вяжущего при производстве шлакобетона используется цемент с добавками извести или глины, которые не только экономят цемент, но и способствуют повышению пластичности и удобоукладываемости этого строительного материала. Чтобы приготовить шлакобетон, необходимо соединить в сухом виде цемент, шлак и песок, ввести известковое или глиняное тесто и воду, тщательно перемешать. Полученный шлакобетон должен быть использован в течение 1,5–2 ч.
Стеновые блоки производятся и из легких бетонов, двумя способами: путем включения облегченного заполнителя (так получается керамзитобетон) или посредством искусственного вспенивания вяжущей составляющей (таким образом изготавливаются ячеистые бетоны – пено– и газобетон).
В состав керамзитобетона входят керамзит (вспененная и обожженная глина) – заполнитель с фракциями 5–10 мм, цемент и вода. Компоненты сначала перемешиваются, уплотняются в процессе вибропрессования и подвергаются тепловой обработке. Керамзитобетон совмещает в себе положительные стороны целого ряда строительных материалов: прочность и морозостойкость цементно-песчаных блоков, легкость и низкую теплопроводность пено– и газобетонных блоков, экологичность кирпича. Кроме того, его достоинствами являются:
1) высокие теплоизоляционные свойства. По этому параметру керамзитобетон превосходит кирпич, цементно-песчаные блоки (в том числе и пустотелые). В доме, построенном из керамзитобетона, теплопотери не превышают 25 %, в то время как в кирпичном при отсутствии дополнительного утепления – 40–60 %;
2) хорошие звукоизоляционные качества;
3) низкое влагопоглощение (ср. у кирпича: 6–12 %, у цементно-песчаных блоков: до 15 %, у ячеистых бетонов: до 30 %, у керамзитобетона: 3 %), причем увлажняется только поверхность керамзитобетона, так как воздушные пузырьки, имеющиеся внутри материала, этому препятствуют;
4) химическая стойкость;
5) относительно малый удельный вес: примерно 12 кг. При этом один блок заменяет семь кирпичей, но весит в два раза меньше, чем они. Данное качество дает несколько преимуществ: прежде всего не требуется усиления фундамента, поскольку нагрузка на него снижена; стены могут возводиться в несколько раз быстрее, чем из того же кирпича. Поскольку толщина стен уменьшается, то полезная площадь помещения возрастает приблизительно на 50 %;
6) огнестойкость.
Для индивидуального застройщика важно и то, что по соотношению цены и качества керамзитобетон представляется наиболее оптимальным вариантом для стен, тем более что армирование не требуется. Для дома в три этажа подойдет материал марки М75.
Несмотря на длинный перечень достоинств, у керамзитобетона есть и недостатки:
1) большая хрупкость (в большей степени это относится к пустотелым блокам). По этой причине они не рекомендуются для кладки фундамента;
2) обрабатывать керамзитобетон легче, чем цементнопесчаные блоки, но труднее, чем блоки из ячеистого бетона;
3) стены из керамзитобетона теплые, но тем не менее не дотягивают до нормативов по теплоизоляции, поэтому толщины стены в один блок будет недостаточно. Утеплять такие стены необходимо, как и облицовывать (внешне блоки не столь презентабельны, как кирпич). Для этого подойдут облицовочный кирпич, сайдинг и пр. Из новых отделочных материалов назовем лицевой керамзитобетонный камень (одновременно с керамзитобетонной основой создается и фактурный слой толщиной 5–7 мм, это является гарантией того, что он не будет отслаиваться), который может иметь как гладкую, так и имитирующую природный камень поверхность (гранит, известняк и пр.), а также различный цвет.
К легким относятся и ячеистые бетоны, которых объединяет особая ячеистая структура. В строительстве наиболее востребованными оказались пено– и газобетонные блоки.
Газобетон (газосиликатные блоки) производят из смеси извести, цемента, кварцевого песка и газообразователя, в качестве которого используется алюминиевая пудра (пусть последний компонент вас не пугает, поскольку он превращается в оксид алюминия и в готовом изделии его в восемь раз меньше, чем в кирпиче). В процессе взаимодействия с известью исходное сырье вспенивается, и выделяется водород, придающий материалу пористую структуру, после чего газобетон набирает прочность в автоклавах, в которых он находится при высокой температуре и повышенном давлении. Отсюда еще одно название газобетона – «автоклавный ячеистый бетон». Таким образом, производство газобетона – достаточно сложная технология (поэтому не встречается подделок данного материала), связанная с применением дорогого оборудования и осуществляемая под контролем всех этапов его получения. Поступающий на рынок материал всегда имеет сертификат соответствия. Газобетонные блоки бывают разного размера: 600 x 250 x 100 (200, 250, 350, 450, 500) мм.